Abstract
Contents
- Introduction
- 1. Theme actuality
- 2. Research purpose and tasks and expected results
- 3. Analytical review
- 4. Research part
- 4.1 Simulation of the overhead crane construction
- 4.2 Estimation of natural frequencies
- 4.3 Transient time diagrams
- 4.4 Verification of the results on the model with distributed parameters
- Conclusion
- References
Introduction
In the modern manufacturing process transportation is indispensable step, since it is impossible to implement all the steps of production in one line. When it comes to moving big loads crane systems are applied. Depending on the design and purpose they may have a horizontal movement, hoisting and slewing mechanisms.
One of these types of systems – overhead crane. This plant is widely used in various industries, such as metallurgy.
1. Theme actuality
Overhead crane provides the horizontal movement of loads, using the mechanisms of translational motion. Depending on usage they may have only one such mechanism (for indoor use) or two that provides the movement in the perpendicular directions (universal). In this case construction length reaches several tens of meters, which causes the distribution of stiffness along its length. In such circumstances, eigen vibrations of elastic construction may reach significant values, which leads to a considerable increase of mechanical stresses in its elements [1, 2, 3]. Considering the harmonic nature of the transient processes of elastic vibrations the lifespan of the whole crane unit is reduced due to the phenomenon of metal fatigue. This calls for creating damping methods for these vibrations.
2. Research purpose and tasks and expected results
On the basis of the available parameters data of the overhead crane construction it is necessary to create its computer models that accurately reflect its dynamic properties and to develop elastic vibrations damping methods. The effect of the obtained control law for load sway damping is to be checked and the adequacy of the obtained results is to be confirmed on the experimental installation.
It’s necessary to solve the following tasks in the work to achieve the defined purpose:
- to create a computer model of the overhead crane construction, which accounts the distribution of mass and elasticity along its length;
- to create a simplified linearized model of the crane based on the analysis of obtained transient graphs;
- to synthesize the controller for construction elastic vibrations damping and to verify its effectiveness on both models;
- to complement the model with load swing effect and to check the quality of the system;
- to synthesize the observer to recover the full state vector of the system;
- to implement these algorithms on the Arduino family microcontroller and experimentally confirm the earlier results.
The object of study: computer model of the overhead crane with the distribution of mass and elasticity.
The subject of study: damping of elastic vibrations of the crane construction.
The main scientific and practical results, their effect:
- Using specialized software allows of the study of the elastic properties of mechanical constructions in the transient state as well as from the point of view of a harmonic oscillation spectrum.
- Disposing the cart in the middle point of the crane and its motionless fixing it is possible to describe the dynamics of the crane movement quite accurately with equations of motion for a two-mass electromechanical system, having previously replaced the distributed parameters with lumped ones.
- If it is possible to measure or identify physical quantities corresponding to the state variables of a two-mass electromechanical system, the elastic vibrations of crane construction can be effectively damped by synthesizing state-feedback controller.
3. Analytical review
Elasticity of the construction as well as its mass are distributed, and the nature of this distribution depends on the crane unit construction, position of the cart with payload, mass of the payload and so on. So, the analysis of the elastic properties of the mechanical construction with traditional methods is ineffective, since the replacement of distributed parameters with lumped requires an accurate calculation of the natural frequencies of vibration.
For the convenience of such research, there are a lot of software packages that describe the transient processes in systems with distributed parameters using partial differential equations (PDEs). The functioning basis of such packages is the finite elements method, which involves partitioning the entire system into define-form finite elements [8] and solving of PDEs at the nodal points. With the help of these packages it is convenient to analyze the adequacy of used approaches to replace distributed parameters with lumped ones, and properties of systems that will make the basis for the synthesis of the control system.
Traditionally, the analysis of the elastic vibrations in mechanical systems is carried out by presenting the entire construction as the set of masses with elastic connections between them, i.e. representation of an entire construction in the form of multimass system [3]. Thus the most significant oscillation frequencies are selected and, depending on their number, the order of the system is selected. If a system has only one significant natural frequency, its dynamic properties with a fair degree of accuracy may be reproduced with two-mass system. There are a lot of elastic oscillations damping methods for it, but the most interesting is using of state-feedback control. In this case, the dynamic properties of a closed loop system are determined by the location of its poles, which depends on the feedback coefficients of the system state variables. If it is possible to measure or identify these variables, the desired character of transients, which in this case includes damping of the elastic construction vibrations, can be obtained by selecting the location of the poles.
4. Research part
The creation of a computer model of the overhead crane elastic construction, simplification of its mathematical description, design of state-feedback control system and analysis of the effectiveness of the elastic vibrations damping are considered.
4.1 Simulation of the overhead crane construction
Analysis of elastic vibrations of systems with distributed parameters, like overhead crane construction, is convenient carried out in specialized software packages that simulate the behavior of such systems by solving PDEs. Comsol Multiphysics package allows the analysis of steady-state and transient responces, the calculation of natural frequencies and Bode diagrams.
A simplified model of the bridge structure in this package is shown in Fig. 1. The input parameters for it are geometric configuration of the bridge and trolley structure and mechanical properties of the material they are made of: density, Young’s modulus and Poisson's ratio.
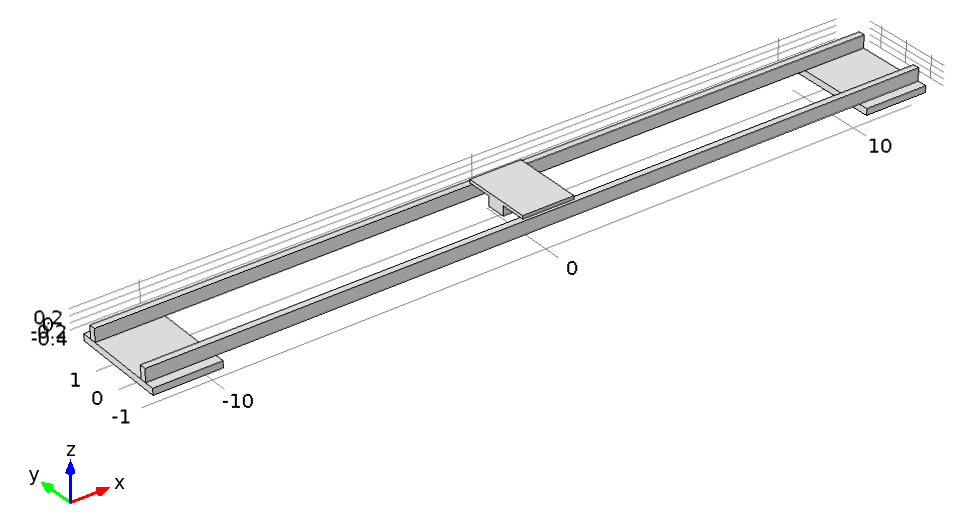
Figure 1 – Crane construction model
So, the bridge consists of two solid metal rectangular rails with reduced density and Young’s modulus. Standard data of construction steel were taken as the basis, but the density was reduced so that the structure mass coincides with the real data set. The Young’s modulus was reduced in proportion to the mass, so that natural frequency remained unchanged.
Let us assume that trolley is fixed in the center point of the bridge. This simplification allows doing all the necessary research with a sufficient degree of accuracy without the additional cost of computing time.
4.2 Estimation of natural frequencies
To determine the natural frequencies of an overhead crane construction necessary restrictions are imposed on the movement that will be present in the simulation of system dynamics. In this case, we do not allow the movement of construction along X and Z axes (see Fig. 1).
Fig. 2-5 shows the first four modes of natural vibrations of the structure. It is known [1, 2, 3] that these frequencies are typically of a few Hertz, which was confirmed by simulation.
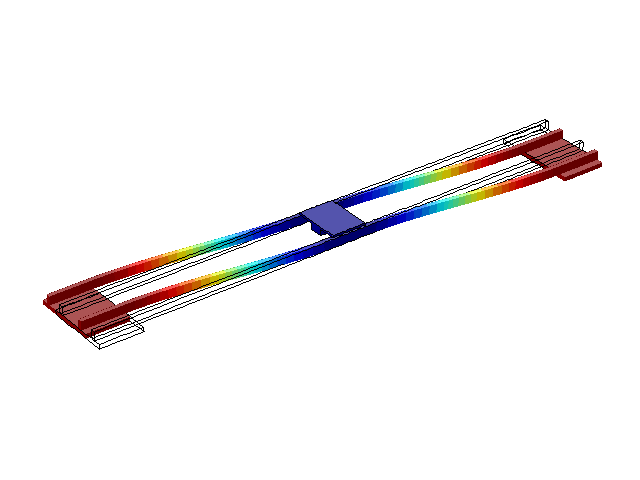
Ðèñóíîê 2 – The natural mode of vibrations of the bridge by frequency f=0,61 Ãö
(animation: 24 frames, endless repeating, 273 kilobytes)
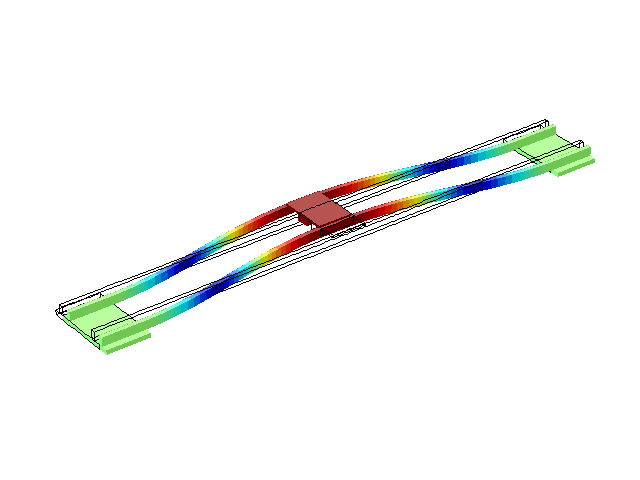
Ðèñóíîê 3 – The natural mode of vibrations of the bridge by frequency f=1,18 Ãö
(animation: 24 frames, endless repeating, 279 kilobytes)
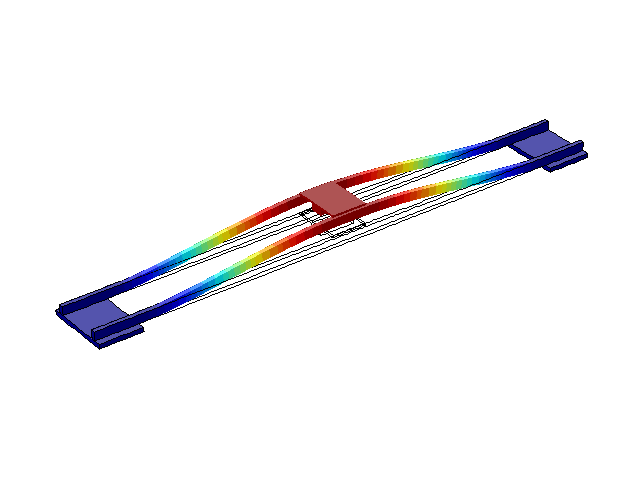
Ðèñóíîê 4 – The natural mode of vibrations of the bridge by frequency f=1,76 Ãö
(animation: 24 frames, endless repeating, 275 kilobytes)
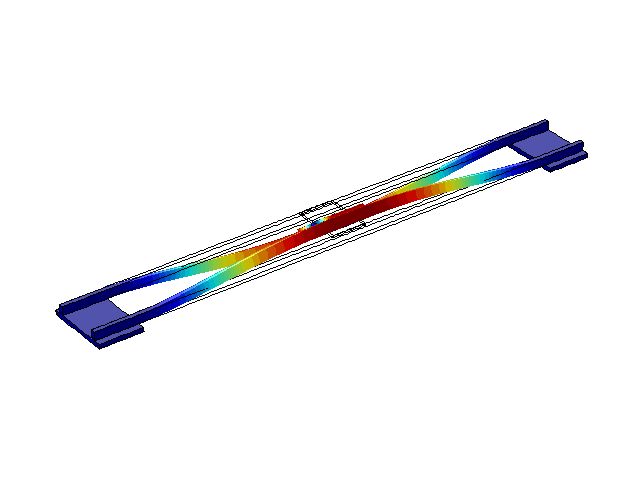
Ðèñóíîê 5 – The natural mode of vibrations of the bridge by frequency f=3,31 Ãö
(animation: 24 frames, endless repeating, 289 kilobytes)
4.3 Transient time diagrams
Transient time diagrams of bridge movement were received under simplification that the drive torque produces a force that is uniformly distributed over the plane of the end boundaries of the model [7].
The force applied to the bridge corresponds to the acceleration to 0.5 m/s in 1 s and equivalent deceleration after 7 s of steady velocity. The simulation results showed that if the trolley is located at the central point of the bridge, the velocity and displacement at its end points are equal.
Velocity time diagrams at end points of the bridge v1 and trolley v2, as well as the maximum bridge deformation in its movement direction Δs2, which is measured at its central point, are shown in Fig. 6. The graphs show that in both end points there are non-damped vibrations, the amplitude of the velocity vibrations reaches 0.1 m/s.
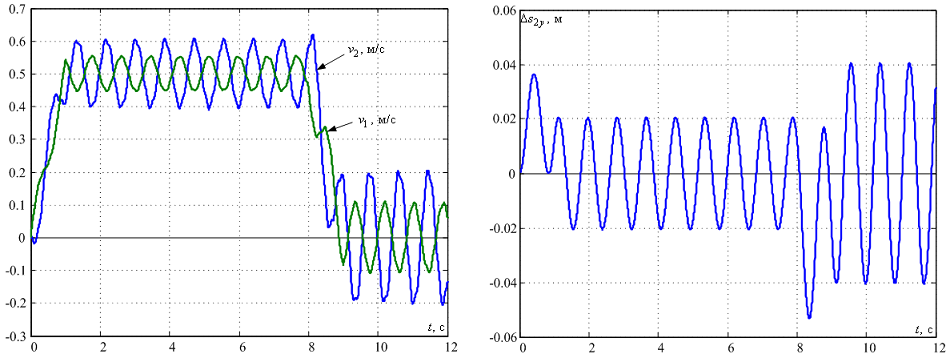
Figure 6 – Transient motion of the elastic structure of an overhead crane
Obviously, a significant effect on transient has only one harmonic component, which corresponds to a natural vibration frequency of f=1.18 Hz, as shown in Fig. 3. Velocity time diagram indicates that the vibration spectrum contains at least one further harmonic component, but its amplitude is much smaller than the core, and therefore its influence can be neglected. Therefore, the process of elastic vibrations with a reasonable degree of accuracy can be described by a conservative element with the transfer function:
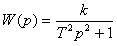
This description corresponds to the behavior of multi-mass electromechanical system, which we take as the basis for creating a simplified mathematical model.
The kinematic model of three-mass system and its mathematical description was derived and simplified to two-mass system, for which state feed-back controller was designed in order to suppress its elastic vibrations. From this model a force time diagram was obtained.
4.4 Verification of the results on the model with distributed parameters
To the bridge model in software package Comsol a linear force, obtained from a system with state-feedback control, is applied. The simulation results are shown in Fig. 7.
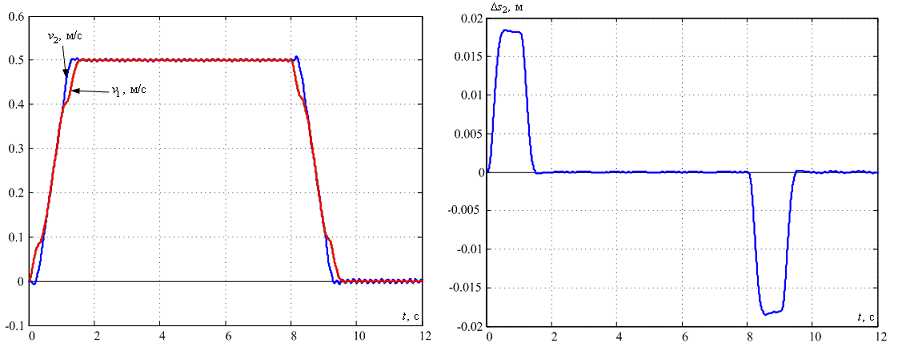
Figure 7 – Time diagrams in distributed parameter model when applying the force from the system with the state-feedback control
It is clear that the low-frequency elastic vibrations are completely suppressed. This leaves vibrations of higher frequencies that are not included in the linear model. Nevertheless, simulation results coincide with those obtained from a linear model, which confirms its adequacy.
Further research carried out in Comsol, have shown that locking trolley at other points of the bridge the nature of elastic vibrations varies considerably: there are additional frequencies that vary over a wide range. This makes it impossible to use the synthesized state-feedback control with a wide range of required trolley movement. To design an adaptive control system a linear model of the bridge based on three-mass kinematic circuit, in which change of trolley position is taken into account by changing in the coefficients of elasticity and mass distribution, can be used.
In this case, design of several state-feedback controllers for different trolley positions is a perspective with a smooth transition between them using the Sugeno type fuzzy controller appears promising [5].
Conclusion
A computer model of crane construction in the software package Comsol Multiphysics, which takes into account the distribution of mass and elasticity along its length and allows investigating its elastic vibrations, was received. Based on the time diagrams a simplified linearized model that allows the synthesis of controllers for vibrations damping of elastic structures was created.
The most significant conclusions and recommendations are as follows:
- Analysis of the elastic properties of mechanical structures is conveniently carried out in specialized software, which uses the finite element method.
- Only one harmonic component of elastic vibrations has a significant impact on bridge movement.
- Under assumption that the trolley is fixed in the central point of the bridge, the bridge structure dynamic properties can be represented as two-mass electromechanical system.
- The use of state-feedback controller can effectively suppress the elastic vibrations of the bridge structure, if there is a possibility to get information about all the available state variables at any given time.
Note. When writing this text the work was still in progress, so the essay contains results available at the time of the exam on the subject Internet-technology
. The deadline for master’s thesis and date of defense – January 2014.
References
- Áóä³êîâ Ë.ß. Áàãàòîïàðàìåòðè÷íèé àíàë³ç äèíàì³êè âàíòàæîï³äéîìíèõ êðàí³â ìîñòîâîãî òèïó: Ìîíîãðàô³ÿ. – Ëóãàíñüê, âèä-âî ÑÍÓ ³ì. Â.Äàëÿ, âèä. 2-å, 2003. – 210 ñ.
- Ìàêóðèí À.Â., Ìîðîçîâ Ä.È. Äèíàìèêà ïðîäîëüíîãî ïåðåìåùåíèÿ ìîñòîâîãî êðàíà ñ ó÷åòîì óïðóãîñòè ýëåìåíòîâ êîíñòðóêöèè // Åëåêòðîòåõí³÷í³ òà êîìï’þòåðí³ ñèñòåìè. – 2011. – ¹3(79). – Ñ. 167-169.
- A. Buch. Optimale Bewegungssteuerung von schwingungsfahigen mechatronischen Systemen mit zwei Freiheitsgraden am Beispiel eines Krans mit Pendelnder Last und elastischer Mechanik – Magdeburg, 1999. – 250 S.
- B. Jerman. An enhanced mathematical model for investigating the dynamic loading of a slewing crane [Ýëåêòðîííûé ðåñóðñ]: / B. Jerman. – Ýëåêòðîí. òåêñò. äàí. – Slovenia: 2006. – Ðåæèì äîñòóïà: http://pic.sagepub.com/content/220/4/421
- C.Y. Chang. The switching algorithm for the control of overhead crane [Ýëåêòðîííûé ðåñóðñ]: / C.Y. Chang. – Ýëåêòðîí. òåêñò. äàí. – China: 2006. – Ðåæèì äîñòóïà: http://link.springer.com/article/10.1007%2Fs00521-006-0036-z
- E. Reynders. Reference-based combined deterministic-stochastic subspace identification for experimental and operational modal analysis [Ýëåêòðîííûé ðåñóðñ]: / E. Reynders, G. De Roeck. – Ýëåêòðîí. òåêñò. äàí. – Belgium: 2008. – Ðåæèì äîñòóïà: http://www.sciencedirect.com/science/article/pii/S0888327007001823
- F.L. Chernousko. Control of elastic systems by bounded distributed forces [Ýëåêòðîííûé ðåñóðñ]: / F.L. Chernousko. – Ýëåêòðîí. òåêñò. äàí. – Russia: 1996. – Ðåæèì äîñòóïà: http://www.sciencedirect.com/science/article/pii/009630039600001X
- K.A.F. Moustafa. Modelling and control of overhead cranes with flexible variable-length cable by finite element method [Ýëåêòðîííûé ðåñóðñ]: / K.A.F. Moustafa, E.H. Gad, A.M.A. El-Moneer, M.I.S. Ismail. – Ýëåêòðîí. òåêñò. äàí. – Egypt: 2005. – Ðåæèì äîñòóïà: http://tim.sagepub.com/content/27/1/1.abstract
- N. Uchiyama. Robust control of rotary crane by partial-state feedback with integrator [Ýëåêòðîííûé ðåñóðñ]: / N. Uchiyama. – Ýëåêòðîí. òåêñò. äàí. – Japan: 2009. – Ðåæèì äîñòóïà: http://www.sciencedirect.com/science/article/pii/S0957415809001500
- 10. Y. Sakawa. Nonlinear model and linear robust control of overhead traveling cranes [Ýëåêòðîííûé ðåñóðñ]: / Y. Sakawa, H. Sano. – Ýëåêòðîí. òåêñò. äàí. – Japan: 1997. – Ðåæèì äîñòóïà: http://www.sciencedirect.com/science/article/pii/S0362546X97860415