Abstract
Content
- Introduction
- 1. Theme urgency
- 2. Goal and tasks of the research
- 3. An approach to the unification of synthesis of Moore FSM on FPGA
- 3.1 Analysis of semi-coking gas
- Conclusion
- References
Introduction
Today, the share of oil and gas in the total use of primary energy balance of Ukraine is about 50 %. The priority energy source is natural gas, whose share in the energy mix in recent years is 38–41 %. Ukraine is a country with a deficit of its own natural carbohydrate resources to meet the gas demand through its own production by 35 % (2010) in oil – by 12–15 %. In 1991, gas consumption was 118.1 billion cubic meters, and the country ranked third place in the world in terms of gas consumption, second only to the United States and Russia. The use of natural gas to Ukraine in 2010 amounted to 57.6 billion cubic meters.
At the present level of prices for gas or coal gasification is a thermal processing for Ukraine the most cost–effective solution.
1 Theme urgency
Semi–coke gas produced by thermal processing, similar to the composition of natural gas and has valuable products but not used in industry.
Published data on the composition of semi–coking gas does not pass characteristics of the process of thermal degradation of sulfur coals, what are the Donbass coal.
In this work is studied sulfur coals Donbass grade D of different genetic types on how to reset, semi–coke in a gas contains a number of carbons valuable products hydrogen, methane, including hydrogen sulfide. The combustion of sulfur and coking coal emit harmful gases – this is because the concentration of this product is so small that it does not allow it to collect and qualified to use it.
2 Goal and tasks of the research
Purpose – to optimize product Semicoking malometamirfizovannyh sulfur coals, the use of semi–coking gas and the possibilities of its future use as fuel, raw materials for the chemical industry and an additional source for hydrogen sulfide. To accomplish this goal, the study conducted derivatografic coal, on the basis of which it is clear that the carbonization temperature of 550 °C does not correspond to a maximum temperature of decomposition of the main types of coal. This is due to the fact that the guests on the carbonization yield of products is targeted not at all grades of coal. In order to improve the method of conducting semi–coking with the maximum temperature obtained for the Derivation of coal.
3 PRACTICAL WORK
In the pyrolysis of fossil coal at temperatures not higher than 550 °C without the formation of air following products: involatile residue (char), gum, water (moisture Pyrogenetic coal and water) and the semi–coke gas. Depending on the heating conditions, along with the primary processes of thermal degradation may occur secondary reactions, which affect the composition of the pyrolysis products. To reduce these unwanted processes must accurately determine the temperature corresponding to the maximum speed of the thermal decomposition of organic matter coal. The optimum temperature for the production of primary products was determined by semi–coking Derivatograph (Тmax).
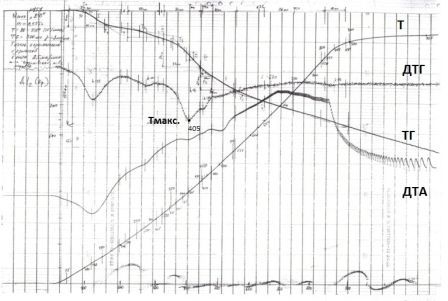
Figure 1 – Derivation
The definition of output of semi–coking and semi–coke getting gas were carried out in a retort Fisher at the final heating temperature of 520 °C according to GOST 3168–66 at Tmax = 405 °C for the study of coal (Fig. 2). The object of these studies used low–quality coal mines Trudovskaya grade D, K8 reservoir with a sulfur content of 5,85 %, particle size < 3 mm.
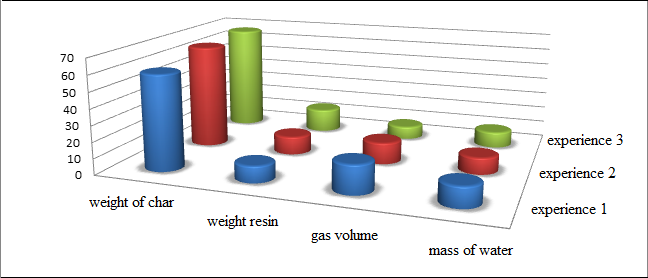
Figure 2 – Product yield carbonization
3.1 Analysis of semi–coking gas
For the analysis of the gas installation using UIH (All–Union Institute of heating) (Figure . 3). Determination of sample gas components such as: Cn Hm, O2 and CO,the amount of acid gas was carried out by their respective selective absorption of the absorption solution. H2, CnH2n+2 fractionated and analyzed by combustion over copper oxide at different temperatures. In this case, the percentage of the components was determined by measuring the reduction in the analyzed gas samples at successively conducted operations absorption or burning.
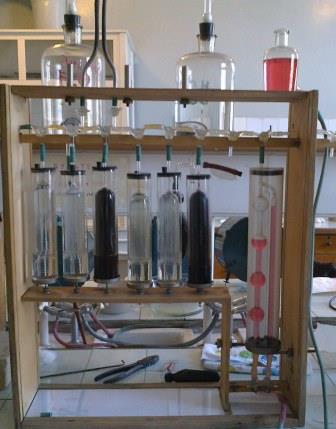
Figure 3 – UIH gas analyzer
As seen in Figure 4, resulting in the semi–coke gas identified following components: carbon dioxide, unsaturated hydrocarbons, oxygen, carbon monoxide, hydrogen, methane and its homologs, nitrogen and hydrogen sulfide.
With increasing heating temperature of the final semi–coke gas increases, its composition varies. Conducting pyrolysis Tmax = 405 °C leads to an increase in gas quantity the most valuable components – Hydrogen and unsaturated hydrocarbons – 3.2 and 3.9 times, respectively. Furthermore, this gas can serve as raw material for producing hydrogen sulphideas the concentration of the latter increases to 28 %.
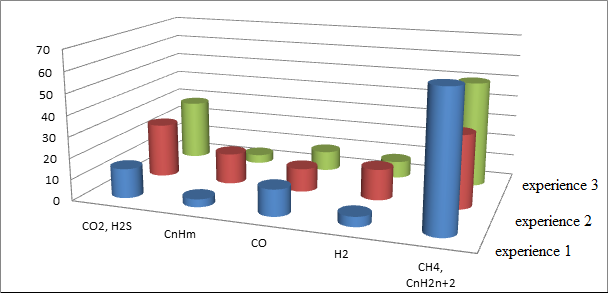
Figure 4 – The composition of semi–coking gas
Conclusion
Higher concentrations of carbon monoxide and hydrogen in the primary gas, while reducing the concentration of CO in them as compared to standard carbonization gas indicates that occur secondary processes according to the reaction
CO + H2O → CO2 + H2
Based on the data, we can conclude that the main drawback of the method according to GOST carbonization is the fixed temperature of pyrolysisAccording derivatography that does not conform to the maximum temperature of the decomposition rate of the least stable component of WMD (Tmax). Consequently, the method can not be extended to the whole range of coal metamorphism. In addition, the results show that the standard semi–cokingdoes not allow the primary degradation products of coal, as the temperature of the process for the coal nizkometamerfizovannyh overstated. From a practical point of view holding carbonization at the optimal temperature set by derivatograms can increase the yield of liquid and gaseous products, which can serve as feedstock for the chemical industry and energy.
In writing this essay master's work is not yet complete. Final completion:December 2013. Full text of the work and materials on the topic can be obtained from the author or his manager after that date.
References
- Мировые запасы природного газа,автор статьи – Александр Долгих 2010г. [электронный ресурс]. – Режим доступа: http://dolgikh.com/index/0-39
- Большая советская энциклопедия: В 30 т. – М.: «Советская энциклопедия», 1969–1978.[электронный ресурс].–Режим доступа:http://slovari.yandex.ru/~книги/БСЭ/Полукоксовый%20газ/
- Химические вещества из угля. Под редакцией И.В. Калечица – М.:Химия, 1980, 616с.[электронный ресурс].–Режим доступа:http://www.twirpx.com/file/144764/
- Кафтанов С.В. (ред.) Общая химическая технология топлива,Учебное пособие для вузов. – Москва–Ленинград, ГХИ НКТП СССР, 1941. – 770 с.[электронный ресурс].–Режим доступа:http://www.twirpx.com/file/942348/
- Газоанализатор ВТИ–2, инструкция по эксплуатации, Москва – 1965.[электронный ресурс].–Режим доступа:http://www.ngpedia.ru/cgi-bin/getimg.exe?usid=205&num=0
- Н.И.Царев, В.И.Царев, И.Б.Катраков. Практическая газовая хроматография: Учебно–методическое пособие для студентов химического факультета по спецкурсу «Газохроматографические методы анализа». — Барнаул: Изд–во Алт. ун–та, 2000. − 156 с.[электронный ресурс].–Режим доступа:http://www.chem.asu.ru/org/crom/chrom.pdf
- Стаскевич Н. Л. – Справочник по сжиженным углеводородным газам, 1986г., 543 стр.
- Методические указания к лабораторному практикуму «Исследование технологических показателей твердых горючих ископаемых», Донецк ДПИ - 1985.