Abstract
Соntent
- 1. Relevance
- 2. The purpose and objectives of the study
- 3. The alleged novelty
- 4. Perceived usefulness is
- 5. Analysis of possibilities to handle curved surfaces
- 5.1 Machining characteristics of curved surfaces
- 5.2 Optimization of cutting conditions for machining curved surfaces
- 6. Determination of the effect of blade angles in terms of cinematic tool on roughness of curved surfacesa
- References
1. Relevance
Among the various types of surfaces of machine parts are curved surface machining where very difficult.
To ensure the accuracy and quality of the surface layer of the parts, working surface which is limited with a shaped profile, is a complex technological task. Processing shaped surfaces requires complex relative motion kinematics of workpiece and tool and is characterized by variable values of technological factors determining processing conditions.
In connection with the above, the subject of the work devoted to turning performance of curved surfaces of machine parts by choosing rational parameters of cutting process is very relevant and of great practical interest.
2. The purpose and objectives of the study
The aim of the study is to increase productivity and decrease cost of curved surfaces grinding machine parts through the justification of rational parameters of machining.
The main research objectives:
- Analysis of the processing capability of the curved surfaces of machine parts;
- Research of regularities of formation characteristics of surface layer turning curved surfaces, taking into account the variability of geometrical parameters of tools;
- Study on the regularities of change in temperature and cutting force in turning curved surfaces, taking into account the variability of parameters section of the cut;
- Optimization of modes of grinding curved surfaces, taking into account the variability of parameters of the cutting process on the criteria for maximum performance and minimum cost;
- Feasibility of application of lubricating technology environments (SOTS) for high performance processing;
- Software development of theoretical calculations of parameters of the surface layer, the temperature optimum modes of cutting and grinding of curved surfaces;
- Machining process design
rolling casters
to improve performance and reduce cost.
3. The alleged novelty
- In the development of theoretical models of determining heat flow and temperature while turning curved surfaces, taking into account the variability of parameters of the cutting process.
- In establishing analytical dependencies of optimal performance and cost cutting from while turning handle curved surfaces.
4. Perceived usefulness is:
- In creating the reasoned recommendations on selection of optimum cutting data and rational scope of SOTS for various conditions turning machining curved surfaces.
- The design of technological process for machining parts
rolling casters
to improve performance and reduce cost.
5. Analysis of possibilities to handle curved surfaces
In various branches of mechanical engineering is necessary to produce parts whose surface is limited by the complex with a shaped profile. These details include forming rolls for rolling mills and electric welding tube (fig. 1), feeding and gauge the correct cutting Mills; various runners wheeled, tracked, lifting-transport machines, punches and dies dies and moulds, cams, rotors and stators of blowers, blades of gas turbines, guides, equipment, etc.
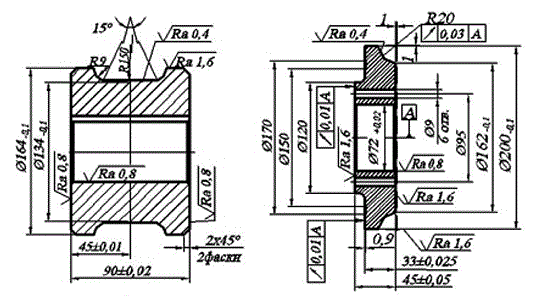
Fig.1 – Examples of parts having a shaped profile
Shaped surface of machine parts are divided into: [1, 2]:
- Algebraic surface, that is described by mathematical equations (bar, nelinejcatye, screw);
- Tabular numeric coordinates of individual points (the pen blade profiles, etc.);
- Design surface due to necessity;
- Transitional surface (radial jumps from the tail section of turbine blade had working, etc.).
In high-volume and mass production facilities for handling external and internal surfaces of the fittings on the generic and aggregate machinery, semiautomatic, machines, transfer lines, flexible CNC modules used: [1, 2].
- Prismatic and round shaped cutters for workpieces with different shape forming; shaped cutters;
- Broaches for shaped bodies of rotation and holes; (in the three cases above form cutting edges tools with a shaped profile coincides with blanks);
- How to copy with the direct and indirect effects of copying roller and copier.
In the first case, the contact is done through load, hydraulic pressure or compression, and the second through a hydraulic, pneumatic or electronic controls.
The most widely used gidrokopirovanie, including 3-d copying and copying motion in scale by combining the copiers with lever mechanisms – ladder pantographs.
In some cases, the role of the copier are:
- Builders in the form of separate mechanisms or devices based on complex electric circuits;
- Incorrect method of kinematic chains, connecting the rotation of the workpiece and the cutting tool from the workpiece or tool handling subsidiary.
In a single, small batch and serial production workpieces with shaped surfaces should be on machine tools with numerical program control. Sound economic choice of the type of automated equipment – machines with CNC machines, CNC and cam machines can be produced by using the graphs presented in Fig. 2 [1, 2]. Installation schemes of blanks with shaped surfaces on CNC Lathes are governed by GOST 3.1107.
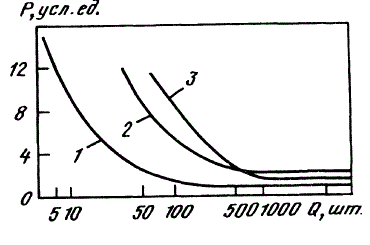
Fig.2 – Dependency unit cost of production of the size of the party and the type of equipment: 1 CNC machine –; 2 – CPU machine; 3 – cam machine
Implementation process of shaped workpieces on lathe, milling and multi-task machining is performed in the following sequence [3]:
- A technological process;
- Calculated on the basis of the cash management program-technological charts and records program;
- A monitoring daemon on koordinatografe and make the necessary corrections;
- The trial is held machining CNC machined parts;
- Control of machined parts, corrected in the calculation and the technologically process;
- Batch processing is carried out.
5.1 Machining characteristics of curved surfaces
Machining curved surfaces very difficult. First of all, their processing is characterized by variable input parameters of the cutting process: variable contoured profile radius and axial surface variability of an allowance and physico-mechanical properties of the workpiece material, etc.
In addition, processing of curved surfaces is characterized by variability of kinematic parameters of cutting process: geometrical parameters of the tool and blade section of the stratum, and as a consequence-forces, temperatures, cutting parameters of machined surface. [3].
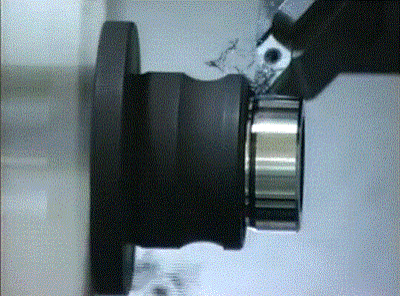
Fig. 1.1 Process of Turning of a Curvilinear Surface
(animation: 6 frames, 7 cycles of repeating)
When processing complex shaped surfaces to increase tool life and the quality of processing machines must be equipped with automatic control systems. [3].
Automatic control system must ensure the permanence of the cutting speed, feed, pie and cutting temperature in any zone treated contoured surfaces. It does this by automatically adjusting the speed of the workpiece or tool, regardless of the reasons that may cause a change of temperature or cutting.
These systems enhance the stability of physical optimization criteria and process reliability in general, providing high performance and quality of treatment.
Currently, the focus of research of machining characteristics of curved surfaces is given to the accuracy of the processing[4-10]. Information about the patterns form a surface layer of curved surfaces of machine parts is virtually non-existent, that requires research in this direction.
To many detail with shaped surfaces, e.g. rollers to rolling, increased demands on durability and wear resistance at high temperatures, which are used to manufacture stainless steel, heat-resistant and high-strength steels and alloys with a very low machinability.
One of the promising ways to improve the effectiveness and efficiency of machining tool is the use of SOTS.
A significant contribution to the development of the science of physical and chemical processes occurring in the contact zones of processed and instrumental material, commonly known as Tribology cutting when using the MOATS have made Russian and foreign scientists Г.В. Виноградов, М.Б. Гордон, И.В. Гребіщіков, Г.И. Єпіфанов,М.И. Клушин, В.Н. Латышев, П.А. Ребиндер, Г. Мерчант, В.Я. Кізельштейн, Ф.П. Боуден, Д. Тейлор и др..[10-16].
In some works, there are suggestions that the MOTES can provide not only positive but also negative effects on the cutting process. There are conflicting reports on the effect of water, oxygen, air and vacuum on the cutting process is not clear, the composition and properties of protective films on contact, yet detailed descriptions of the mechanism of chemical reactions occur when cutting [17].
The purpose of SOTS – less wear of cutting tools, improving the quality of the processed surface and increased productivity – [18].
Effective SOTS have great influence on the quality of surface roughness, the depth and degree of naklepanogo layer. Basically, SOTS reduces the surface roughness on 0.5-1 class, as well as reduce the depth and extent of slander of superficial layers of detail. For example, oxygen and SOTS in the sense that they have oxygen, improves the surface quality by reducing or eliminating build-up on cutters [19-21].
Application of metal cutting processing SOTS enables you to increase hardware performance, precision and fineness of processing, reduce marriage, improve working conditions and, in some cases, reduce the number of technological operations [22]
For metalworking processes SOTS are chosen according to the type of operations and their technological features, characteristic of processed materials, etc recommendations for choosing SOTS for various conditions of metal cutting processes are given in [22-27]. Select the SOTS recommendations on transport and storage, preparation of working solutions, monitoring and adjusting the quality, utilization, safety at work with the SOTS.
Method of calculating the cooling properties of SOTS presented in [28]. Are the equations which enable you to determine the effect of physico-chemical properties of SOTS on the heat transfer coefficient, which increases with increasing thermal conductivity and velocity of the fluid motion and decreases with increasing surface area cooled, thermal diffusivity and liquid dynamic viscosity. Heat transfer coefficient depends also on temperature boundary layer[28].
Nowadays there is a list of articles on the calculation of heat flow and temperature cutting with SOTS and intensification of cutting process[29-32]; improve processing performance of hard-machinable materials using SOTS [33-35].
Despite the large amount of information about the use of SOTS, scientific and reference literature there is little information on the quantitative evaluation of cutting ability of reducing temperature and increasing productivity of machine parts processing by SOTS. existing methods of calculation of heat flow and temperature in the cutting zone, taking into account the action does not take into account the particularities of processing LARGE of curved surfaces with variable parameters of the cutting process. For these types of surfaces is of interest the further development of the method of determination of the forces and temperatures in the cutting zone by using various SOTS.
5.2 Optimization of cutting conditions for machining curved surfaces
Analysis of possibilities to improve efficiency and reduce the cost of processing is very important the correct choice of the cutting conditions. The greatest challenge of modern mechanical engineering is achieving higher performance processing for a given level of quality of surface layer of detail that can be achieved by grounding the optimal level of processing options.
In the field of cutting tools, there are quite a number of works dedicated to the optimization of its parameters and operating conditions in terms of the various performance criteria. Most attention in the literature on determining rational cutting conditions.
With regard to the processing of metals by cutting the target functions should be submitted, depending on the values that you want to automate. Depending on whether all used variables depending on the criteria of linear or non-linear there is at least one, speak of a linear or nonlinear optimization [42, 43]. Depending on the type of calculation of technological and economic constraints and the form of the objective function using different methods to optimize cutting data [44]. Great attention is given to the refinement of the technological and economic-organizational dependencies [45, 46].
Of paramount importance was the choice of the optimization criterion. Most effective for solving practical problems would have been such a criterion that takes into account all the issues that interest the production. The absence of such a universal criterion is the cause of the diversity of technical and economic indexes, which are used as optimization criterion.
We propose[44] to apply multiple criteria, such as minimum cost and maximum performance or maximum profit.
In published works on optimization of modes is not general criterion, taking into account all existing in practice. The easiest way to solve the problem of multicriterion optimization is the main selection criterion of efficiency and other classified criteria restrictions. In this case, the task goes odnokriterial?noi optimization, in practice there are many effective and successful methods. [41, 42].
For practical use is the ability to perform analytical calculations of optimum cutting conditions that simply provides the geometric method of programming. Method of optimizing cutting conditions with the use of IHL provided in [47]., gives an analytic solution for the identification of the optimal cutting conditions in turning on the criterion of minimum cost.
Modern trends in optimization of cutting conditions aimed at solving multiobjective tasks ensuring the simultaneous improvement of processing parameters on different criteria. A multicriterion optimization is to use multiplicative convolution of criteria for different optimization criteria lead to a single criterion, providing the best combination of each [48].
Of interest is the further development of IHL using multiplicative criteria based on the variability of the process parameters of cut when machining curved surfaces.
6. Determination of the effect of blade angles in terms of cinematic tool on roughness of curved surfaces
Ensuring a certain level of quality of machine parts during machining is the important task of manufacturing engineering, researches of effects on roughness of machined surfaces of the geometric parameters of the cutting tool is quite relevant.
It is now widely known to the General regularities of formation of surface roughness in machining based on conditions that are the basis of the forecast level of roughness in the design phase of technological processes and control parameters of roughness at the stage of manufacture of machine parts.
During the processing of curved surfaces is a complex change of kinematic geometry blades of tool and cutting parameter of surface layer that is associated with the curvature of the surface, which greatly complicates the analysis of the influence of these parameters on the degree of roughness. Research in this area is very limited.
To work is to set the regularities of formation of curved surfaces of rotation bodies roughness during turning the corner in terms of kinematic variables blade tool.
During processing, the average deviation of profile cutters is defined by the following common equations [51].:

where r-corner radius cutter; s – submission; φ – lead angle cutter; φ1 – auxiliary angle cutter; R zi – calculated roughness height profile:
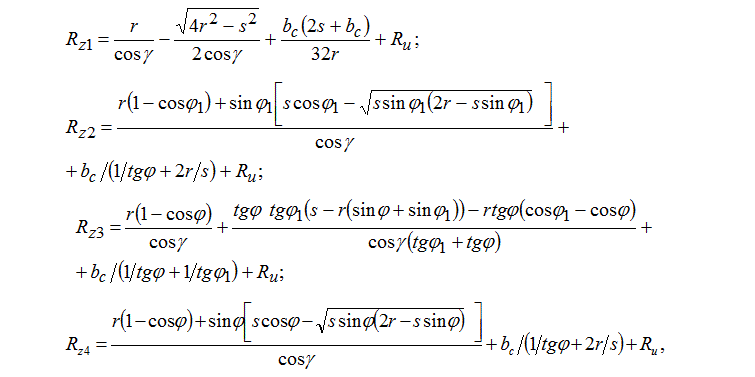
where γ – the cutting angle of the cutter; Rи – height of the roughness profile at the top of the cutter; bс – the amount to displace the plastic:
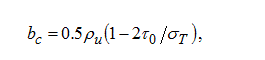
where ρи – cutting edge radius tool; σТ, τ0 – yield strength and power of the processed material.
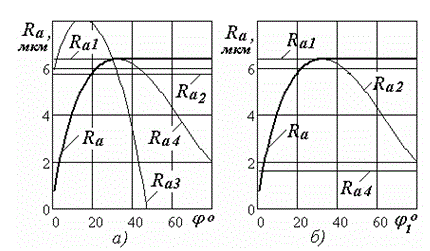
Fig. 2.1. Graphic dependences of the parameters of surface roughness RA of the angles in terms of the blade tool: the main φ – а) and support φ1 – б)
In Figure 2.1 prevedeny dependency charts of surface roughness parameter Ra from the angles of blades for the following conditions: – the cutter corner radius r = 0, 5 mm; filing of s = 0, 2 mm/Rev; lead angle; φ = 90° an additional angle φ 1 = 30°.
Charts show that for given conditions, a significant influence on the surface roughness Ra corners to have a range of up to 30 ° change when increasing both core and supplementary angles in terms of roughness is growing. The further change of angles in terms does not affect the roughness, which is determined by the roughness of the Rа1 and they are not independent. The main effect of the plan, with constant support corner is determined in accordance Rа4, the roughness Rа2, that depends on the support angle remains constant. Influence of the support the plan with the main corner shall be determined in accordance Rа2, It remains a constant roughness Rа2, that depends on the main corner in the plan.
During the processing of curved surfaces of kinematical angle as the major and minor changes simultaneously (fig. 2.2).
Example of defining kinematic main and auxiliary angles to is convex to the surface with a constant radius of curvature (forming the surface of rotation-circle, the center of the coordinate system is the center of curvature, that is the center of the circle).
Position the blade at the top of the curved surface is determined by the instantaneous rotation angle, which is calculated as follows:

where ζ=х/ρ – dimensionless coordinate.
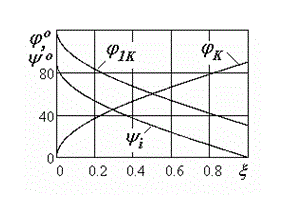
Fig. 2.2. Graphics change blade angles in terms of cinematic tools during processing of curved surface
Kinematic chief φК and an additional φ1К angles are relative to the direction of traffic flow DS instantaneous rotation angle ψi:

Instant diagrams of rotation angles ψi and kinematic main φК and subsidiary φ1К the angles are shown in the fig. 2.3.
Patterns of forming the roughness of the surface is curved, unlike the previously examined (fig. 2.1) are simultaneously changing the kinematics of the main and auxiliary angles in the plan.
Diagrams of roughness parameters Rаi Depending on the location of the top edge on the curved surface machined with the simultaneous changes in terms of cinematic angles are shown in the fig. 2.4.
Charts show that for specified conditions on influences of surface roughness of Ra curvilinear range change the angle to 30°, and coordinates to 0,1 (fig.3) has the lead angle ψ: with his increasing roughness is growing (in terms of angle of main bearing ψ determined by the roughness of Ra4). Due to the fact that the support angle ψ1 throughout the length of the curved surface exceeds 30° (fig. 2.3), his influence on the surface roughness is absent (the influence of the support the plan ψ1 determined by the roughness of Ra3). Further change in the main corner ψ>30° also has no effect on the roughness. It remains constant, and is determined by the roughness of the Ra1, in terms of the angles is not affected.
Thus, on the basis of established patterns of changes in terms of cinematic angles the blade turning tool during some influence of curved surfaces of the main and auxiliary angles of blade tool on machined surface roughness. As a result of the executed researches for the given radius at the top of the blade and innings have quantitative relation of roughness with angles in the tool's blade, which constitute the basis for the development of roughness during processing of curved surfaces.
References
- Гжиров Р. И. Программирование обработки на станках с ЧПУ / Р.И. Гжиров, П.П. Серебреницкий. – Л.: Машиностроение, 1990. – 489 с.
- Дерябин А. Л. Программирование технологических процессов для станков с ЧПУ / А.Л. Дерябин. – М.: Машиностроение, 1984. – 51 с.
- Шарин Ю.С. Технологическое обеспечение станков с ЧПУ М.: Машиностроение, 1986. – 176с.
- Лещенко А.И. Анализ точности обработки фасонных поверхностей в зависимости от погрешности настройки инструментов на программ-ную операцию вісник приазовського державного технічного університету 2008 р. Вип. № 18 с. 129-133.
- Марецкая В.В. Моделирование технологических процессов механической обработки с использованием программного комплекса «Моделирование В Технических Устройствах» («МВТУ») // Известия вузов. Машиностроение. – 2004. – № 4. – с. 39-52.
- Марецкая В.В. Исследование отклонений профиля рабочей поверхности валка, вызванных упругими отжатиями элементов технологической системы // Справочник. Инженерный журнал. – 2006. – № 12. – с. 50–54.
- Марецкая В.В. К вопросу автоматизации направленного формирования показателей качества деталей // Вестник компьютерных и информационных технологий. – 2008. – № 3. – с. 29–34.
- Камсюк М.С., Грановский Э.Г. Определение отклонений, обусловленных отжатиями технологической системы при контурном фрезеровании // Известия вузов. Машиностроение. – 1981. – №5 – с. 139–143.
- Грановский Э.Г., Камсюк М.С. Точность обработки сложноконтурных поверхностей деталей // Основные направления развития технологии машиностроения: Труды МВТУ. – 1981. – № 348. – с.110–127.
- Технологическая наследственность в машиностроительном производстве / под ред. А.М. Дальского. – М.: Изд-во МАИ, 2000. – 364 с.
- Виноградов Ю.М. Применение химическиактивных веществ для повышения эффективности СОЖ при резании металлов / Ю.М.Виноградов. – М.: Изд. МДНТН, сб. №1, 1966, с. 1-13
- Зорев Н.Н. Обработка резанием тугоплавких сплавов / Н.Н. Зорев, З.М.Фетисова. – М.: Машиностроение, 1966, с. 64-69
- Мерчант М.Ю., В сб. Международная конференция по смазке и износу / М.Ю. Мерчант. – М.: ИЛ., 1956. с. 95-105
- Матвеевский Р.М. Температурная стойкость граничных смазочных слоев и твердых смазочных покрытий при трении металлов и сплавов / Р.М.Матвеевский. – М.: Наука, 1971. – 213 с.
- Носовский И.Г. Исследование изнашивания металлов в различных газовых средах / И.Г.Носовский. – Редиздат Аэрофлота, 1956. – 120 с.
- Чубаров А.Д. Деформирование и роль температурного фактора в процессе резания титановых сплавов / А.Д. Чубаров, Н.Н. Новиков. - М.: Вестник машиностроения, 1959, №9. – с. 40-43
- Латышев В.Н. Повышение эффективности СОЖ / В.Н Латышев – М.: Машиностроение, 1975. – 88 с.
- Смазочно-охлаждающие технологические средства для обработки металлов резанием: Справочник / Под ред. С.Г. Энтелиса, Э.М. Берлинера. – М.: Машиностроение, 1986. – 352 с., ил.
- Боуден Ф.П. Трение и смазка твердых тел / Ф.П. Боуден, Д.А. Тейбор. - М.: Машиностроение, 1968, 493 с.
- Кривоухов В.А. Обрабатываемость резанием жаропрочных и титановых сплавов / В.А. Кривоухов. - М.: Машгиз, 1961. - 270 с.
- Латышев В.Н. Влияние газовой среды и смазочного материала на температуру поверхностей трения / В.Н. Латышев. - Изд. АН СССР: Маши-ностроение 1971, №4. – с. 109-111
- Топлива, смазочные материалы, технические жидкости. Ассортимент и применение: Справ. Изд./ К.М. Бадыштова, Я.А. Бердштадт, Ш.К. Богданов и др.; Под ред. В.М. Школьникова. – М.: Химия, 1989. – 432с.
- Худобин Л.В. Техника примения смазочно-охлаждающих средств в металлообработке / Л.В. Худобин, Е.Г. Бердичевский. – М.: Машинострое-ние, 1977. – 189 с. с ил.
- Справочник по обработке металлов резанием / Ф.Н. Абрамов, В,В. Коваленко, В.Е. Любимов и др. - К.: Техника, 1983. – 239 с.. ил. – Биб-лиогр.: с. 235-237.
- Прогрессивные режущие инструменты и режимы резания металлов. Справочное издание / В.И. Баранчиков, А.В. Жариков, Н.Д. Юдина и др. М.: Машиностроение, 1990.
- Базовый ассортимент смазочно-охлаждающих технологических сред для обработки металлов резанием // Тематический обзор. – Централь-ный научно-исследовательский институт информации и технико-экономических исследований нефтеперерабатывающей и нефтехимической промышленности. 1986 г.
- Топлива, смазочные материалы, технические жидкости. Ассортимент и применение: Справочник / И.Г. Анисимов, К.М. Бадыштова, С.А. Бнатов и др.; Под ред. В.М, Школьникова. Изд. 2-е перераб. И доп. – М.: Из-дательский центр «Техинформ», 1999. – 596 с.: ил.
- Расчет тепловых потоков и температур резания при точении с использованием смазочно-охлаждающих жидкостей. / Т.Г. Ивченко (ДонНТУ, г. Донецк, Украина) Надійність інструменту та оптимізація технологічних систем. Збірник наукових праць. – Краматорськ, ДДМА. вип.26, 2010. – c. 90-96.
- Теоретичні основи керування температурою різання з використанням охолоджуючих середовищ / Т.Г. Івченко (ДонНТУ, м. Донецьк, Україна) Надійність інструменту та оптимізація технологічних систем. Збірник наукових праць. Вип.18. – Краматорськ: ДДМА, 2006. – c. 39-45.
- Вплив способу подачі охолоджуючого середовища на температуру різання / Т.Г. Івченко, В.Г. Нечепаєв, О.М. Гнитько (ДонНТУ, м. Донецьк, Україна) Надійність інструменту та оптимізація технологічних систем. Збірник наукових праць. Вип.16 . – Краматорськ: ДДМА, 2005. – c. 34-38
- Интенсификация процесса резания сборными режущими инструментами с использованием охлаждающих технологических сред / Александр Михайлов, Татьяна Ивченко, Ольга Дубоделова (ДонНТУ, г. Донецк, Украи-на) Tehnologii Modern, Calitate, Restructurare. Vol. 1. – Chisinau: Universitates Tecnica a Moldovei, 2005. c. 289-295
- Влияние функциональных технологических свойств смазочно-охлаждающих технологических сред на выбор оптимальных режимов реза-ния / Вадим Богуславский, Татьяна Ивченко Пер. с англ. Ирина Зайцева In-fluence of functional properties of technological cutting fluid on a choice of opti-mum cutting regimes [электронный ресурс]. – Режим доступа: http://www.modtech.ro/vol3no22011/2_FINAL_Bogouslavskiy_Vadim.pdf.
- Повышение производительности обработки труднообрабатываемых материалов с применением смазочно-охлаждающих жидкостей / В.А. Богуславский, Т.Г. Ивченко, Зантур Сахби (ДонНТУ, г. Донецк, Украина) Наукові праці Донецького національного технічного університету. Серія: Машинобудування і машинознавство. Випуск 7(166). – Донецьк: ДонНТУ, 2010. – c. 9-16.
- Vadim Bogouslavskiy, Tatiana Ivchenko. Optimisation of cutting regimes at application of technological cutting fluid // ModTech International Conference 25-27th May 2011, Vadul lui Voda: Chisinau, 2011. P. 669-672. (Index to Scientific & Technical Proceedings of Thomson Scientific - Institute for Scientific In-formation (ISI).
- Клушин М.И. Определение стойкости режущих инструментов, обеспечивающих получение максимально возможной прибыли и производи-тельности общественного труда / М.И. Клушин, Г.Г. Аносов. – Вестник ма-шиностроения, №6, 1970. – с.74-76.
- Макаров А.Д. Оптимизация процессов резания / А.Д. Макаров – М.: Машиностроение, 1976. – 278 с.
- Старков В.К. Обработка резанием. Управление стабильностью и качеством в автоматизированном производстве / В.К. Старков. – М.: Маши-ностроение, 1989. – 296 с.
- Старков В.К. Технологические методы повышения надежности обработки на станках с ЧПУ / В.К. Старков. – М.: Машиностроение, 1984. – 120 с.
- Старков В.К. Оптимизация процесса резания по энергетическим критериям / В.К. Старков, М.В. Киселев // Вестник машиностроения. – М.: 1989, №4. – с. 41-45.
- Якобс Г. Оптимизация резания. Параметризация способов обработки резанием с использованием технологической оптимизации / Г. Якобс, Э.Якобс, Д. Кохан // Пер. с нем. – М.: Машиностроение, 1981. – 279 с.
- Гильман А.М. Оптимизация режимов обработки на металлорежущих станках / А.М. Гильман. – М.: Машиностроение, 1972. – 188 с.
- Евтушенко Ю.Г. Методы решения экстремальных задач и их применение в системах оптимизации / Ю.Г. Евтушенко. – М.: Наука, 1982. – 432 с.
- Кроль О.С. Оптимизация и управление процессом резания. Учеб. Пособие. / О. С.Кроль, Г.Л. Хмелевский. – К.: УМК ВО, 1991. – 140 с.
- Карпусь В. Е. Системные критерии механообрабатывающих технологических систем / В.Е. Карпусь С.В. Луцкий. // Резание и инструмент в технологических системах. – Харьков: ХГПУ, 2000, Вып.57. – с.105-109
- Реклейтис Г. Оптимизация в технике: В 2-х кн. Кн. 2. / Г. Реклейтис, А.Рейвиндран, К. Рэгсдел. // Пер. с англ. – М.: Мир, 1986, - 320 с.
- Ивченко Т. Г. Использование метода геометрического программирования для расчета оптимальных режимов резания при точении / Т.Г.Ивченко Научный вестник ДГМА. – Краматорск: ДГМА, 2011. – №2 (8 Е). с.110-116.
- Король K.O., Ивченко Т.Г. Многокритериальная оптимизация режимов резания на основе мультипликативной свертки критериев ИНЖЕНЕР: студенческий научно-технический журнал / Донецк: ДонНТУ, 2012, № 13. - с.124-128.
- Суслов А.Г. Качество поверхностного слоя деталей машин / А.Г. Суслов. - М.: Машиностроение, 2000. - 320с.
- Качество машин: Справочник. В 2 т. Т.1 / А.Г. Суслов, Э.Д. Браун, Н.А. Виткевич и др. - М.: Машиностроение, 1995. - 256с.
- Грановский Г.И., Грановский В.Г., Резание металлов: Учебник для вузов / Г.И. Грановский, В.Г. Грановский. - М.: Высш. шк.,1985. - 304с.
Remark! When I wrote this abstract, master's work is not yet completed. The definitive variant will be ready by December, 2013. Full text of work and materials on the subject can be obtained from the author or his adviser after that date.