Исследование параметров стружки при плоском алмазном шлифовании
Автор:Азарова Н.В., Матюха П.Г., Цокур В.П.
Источник: Наукові праці Донецького національного технічного університету.
Введение
Сведения о размерах единичных срезов, образующихся при шлифовании, необходимы для расчетов нагрузки на единичном зерне, параметров шероховатости обработанной поверхности, температур в зоне обработки, в связи с чем исследуемый вопрос является весьма актуальным для теории шлифования. В силу особенностей рабочей поверхности круга (РПК), заключающихся в отличии геометрических параметров отдельных зерен, их размеров и ориентации, с обрабатываемой поверхности удаляются срезы самых различных конфигураций и размеров. Соответственно при шлифовании образуются и различные виды стружек. В основе их классификации используется форма стружек (ленточная, запятообразная, сегментообразная, промежуточная [1]; волнистая и сферическая [2]), а также особенность их образования (сливная, скалывания, с оплавом, оплавленная, со спеком и спекшаяся [3]). Вместе с тем данные о сопоставлении параметров срезов и стружек в литературе отсутствуют.
Целью работы является оценка сопоставимости параметров среза и параметров стружки, образующейся при алмазном шлифовании.
Основное содержание работы
Поскольку размеры стружек в результате пластических деформаций, происходящих в процессе резания, отличаются от размеров срезов на коэффициент продольной усадки стружки, при сопоставлении статистических характеристик размеров срезов и стружек будем учитывать значение коэффициента усадки
Исследованию подвергали стружки, полученные при плоском шлифовании образца из стали Р6М5Ф3 периферией круга 1А1 250*16*75*5 АС6 160/125-4-М2-01 на модернизированном станке модели 3Д711АФ11. Перед экспериментом шлифовальный круг подвергали электроэрозионной правке, а затем прирабатывали в течение 30 минут. Правящий электрод представлял собой брусок из меди М1, обеспечивающий длину контакта с РПК 30 мм. Режимы правки: скорость круга 30 м/с, вертикальная подача (0,005…0,007) мм/ход, что обеспечивало силу тока (7…8) А, поперечная подача – ручная.
Режимы шлифования: скорость круга 30 м/с, скорость детали 6 м/мин, поперечная подача 2,5 мм/ход, глубина шлифования 0,015 мм. Охлаждающей жидкостью являлся 0,3 %-ный водный раствор кальцинированной соды. Обрабатываемый образец размерами 60*40 мм был установлен на магнитной плите стола.
Динамика процесса шлифования характеризовалась частотой радиальных колебаний 37 Гц с амплитудой 0,9 мкм. Колебания с более высокой частотой в силу низкой амплитуды (менее 0,5 мкм), значительно меньшей параметров шероховатости обработанной поверхности, не учитывали.
Сбор стружки осуществляли в специально изготовленную ёмкость, которую устанавливали на магнитную плиту вплотную к шлифуемому образцу. Собранную стружку извлекали из емкости, просушивали, размагничивали и укладывали на поверхность подложки. Подложку с исследуемыми стружками устанавливали на предметном столике 1 микротвердомера ПМТ-3 (рис. 1, а, б).
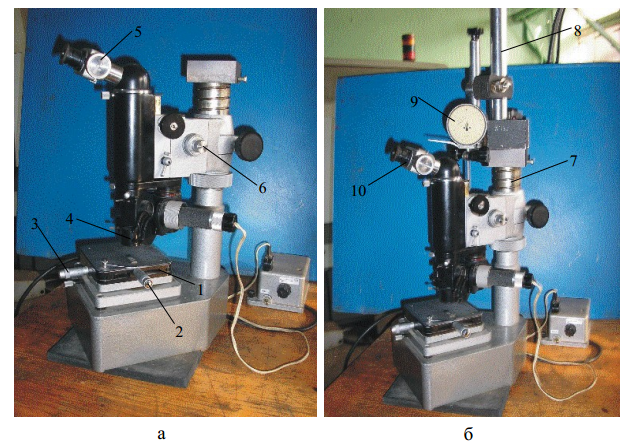
Цена деления лимбов на винтах продольного 2 и поперечного 3 перемещений предметного столика составляла 0,01 мм. Информация о координатах расположения подложки со стружками на предметном столике позволяла, при необходимости, повторно найти стружки для исследования и фотографирования.
Измерение толщины, ширины и длины стружек проводили с помощью оптического устройства микротвердомера ПМТ-3 при увеличении 520 раз, которое обеспечивается объективом 4 (F = 6,2; A = 0,65).
Ширину стружек измеряли с помощью микрометрического винта перемещения тубуса 6 с ценой деления 0,002 мм (рис. 1, а). Для повышения точности измерений на стойке 7 микротвердомера ПМТ-3 закрепляли площадку, на которую устанавливали магнитную стойку 8 с микрометром 9 с ценой деления 0,001 мм (рис.1, б)
Для измерения длины прямолинейных коротких стружек использовали лимбы микрометрических винтов координатного перемещения предметного столика с ценой деления 0,01 мм. Для измерения длины криволинейных стружек в окуляр микроскопа 10 устанавливали сетку (размер клетки 0,5*0,5 мм), закрывающую 50% поля окуляра(рис. 2). При аттестации прибора с увеличением в 520 раз параметры ячейки составили 0,015*0,015 мм.
Измерение параметров стружек осуществляли следующим образом
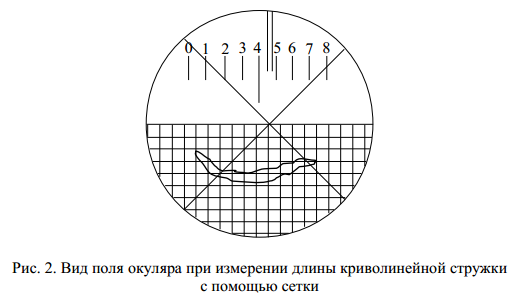
При измерении толщины стружки находили контуры стружки справа и слева в том же сечении, в котором измеряли и ширину, и по разности показаний лимба окулярного микрометра определяли толщину стружки.
При измерении ширины стружки фокусировку оптической системы производили вначале на подложку, а затем на наивысшую точку стружки в данном сечении. Раз- ность двух отсчетов, снятых с лимба винта микрометрического движения тубуса при фокусировке на подложку и наивысшую точку сечения стружки, принимали за ширину стружки.
Длину криволинейных стружек измеряли путем перемещения их в поле окуляра с сеткой и по количеству ячеек, занимаемых изображением стружки, определяли ее длину. Погрешность измерения длины стружки не превышала половины цены деления сетки, что составляло 5-10 % от длины стружек.
Исследовали выборку из 300 стружек, которую впоследствии подвергали статистическому анализу с целью определения законов распределения исследуемых параметров.
Как показали исследования, по форме образовавшиеся стружки можно отнести к ленточным, запятообразным, сегментообразным и дробленым (рис. 3, а, б, в, г).
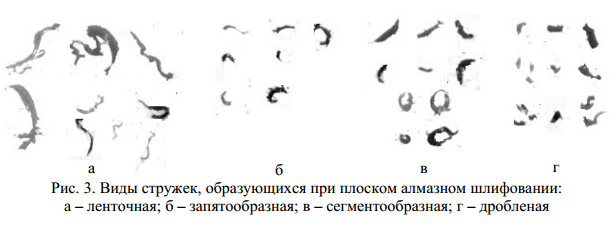
Запятообразные стружки имеют вид запятой с утолщением на одном конце. Они образуются запятообразными срезами, а также промежуточными. Сегментообразные стружки имеют утолщение посередине и образуются сегментообразными срезами. Ленточные стружки также образуются сегментообразными срезами. Дробленые по длине стружки имеют приблизительно одинаковую ширину по всей длине. Они могут быть образованы запятообразными, сегментообразными и промежуточными срезами.
Результаты, полученные при измерении стружки, обработаны методами математической статистики. Построены гистограммы распределений толщины и длины стружки (рис. 4). Анализ гистограмм распределений геометрических параметров стружки показывает, что имеет место относительно большой диапазон изменения исследуемых параметров, преобладание мелких стружек.
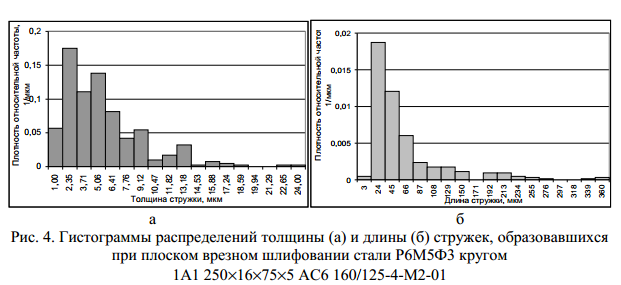
Средние значения исследуемых параметров стружки, определенные экспериментально, составили: длина 52,59±3,42 мкм, ширина 11,89±0,49 мкм, толщина 4,93±0,21 мкм.
Приведенные данные показывают значительное расхождение сопоставляемых рассчитанных по срезам и экспериментально полученных длин стружек (практически в 12 раз), что объясняется, по нашему мнению, дроблением стружек по длине.
В расчётах выходных показателей процесса шлифования основное влияние оказывает толщина среза, которая, как показывает сравнение, попадает в 95%-ный доверительный интервал, что говорит об отсутствии влияния сравниваемых способов определения параметров стружки на их величину
Таким образом, параметры единичного среза, определенные с помощью математической модели шлифования, можно использовать для расчета сил резания, параметров шероховатости обработанной поверхности
Выводы
- Средняя толщина стружек, определенная экспериментально, составляет 4,93±0,21 мкм, что сопоставимо со средней толщиной стружек, равной 4,88±2,85 мкм, которая рассчитана по толщине среза на базе математической модели шлифования.
- Параметры срезов, определенные с помощью математической модели, можно использовать для расчетов параметров шероховатости обработанной поверхности, сил резания и т.п
Список использованной литературы
1. Маслов Е.Н. Теория шлифования материалов. – М.: Машиностроение, 1974. – 316 с.
2. Huges F.H. Talking diamond grinding. Pat 5. Tooling, 1978, Feb.3-21.
3. Лурье Г.Б., Комиссаржевская В.Н. Устройство шлифовальных станков. – М.: Высшая школа, 1983. – 215 с
4. Азарова Н.В. Математическая модель плоского врезного шлифования с вибрациями // Вестник двигателестроения. – Запорожье: ОАО «МоторСич», 2005. – № 1. – С. 119-123.
5. Байкалов А.К., Волкова Т.М., Вал Е.И. Геометрические параметры стружки при шлифовании и притирке ЭВМ // Синтетические алмазы. – 1972. – № 4. – С. 17-19.