Оптимальный уровень автоматизации сборки выбранного модуля в качестве компонента консультативной системы
Автор: B. Reifur, Вроцлавский технологический университет
Источник: Archives of civil and mechanical enginerring, 2007.
Аннотация
При проектировании сборочных процессов особенно трудно определить оптимальный уровень автоматизации, т. е. соотношение долей ручных и автоматических операций в сборке. Этот фактор существенно влияет на производительность, так как она определяет трудоемкость сборки изделия, количество сборщиков, тип и стоимость оборудования. Представленная модульная система открывает возможность проявления значительной гибкости в анализе и оценка продукта на пригодность для автоматической сборки, выбор оборудования и создание новых маршрутов сборки в зависимости от меняющихся потребностей промышленного продукции. По связям конструкции и технологических особенностей с производительностью и экономической эффективностью производства модуль позволяет получить более простой и объективный метод определения уровня автоматизации.
1 Уровень автоматизации сборки
В последнее десятилетие увеличение доли автоматизации производства оказалось правильной стратегией для предприятий, чтобы остаться конкурентоспособными в высокоразвитых странах. В результате возросло число компания, использующих передовые автоматизированные системы сборки изделий. В то же время растет и число мнений, что неограниченная автоматизация влечет за собой чрезмерно дорогостоящие инженерные преобразования.
Ввиду этого множество компаний направляют свои интересы на поиск решений уменьшения уровня автоматизации до оптимального уровня. Ожидаемые экономические выгоды быстро переросли в непредвиденные расходы: потери внутри линии, потери в связи с остановкой конвейера, необходимость использования большого количество технического и обслуживающего персонала, высокая стоимость перехода на новую конструкцию изделий и большие запасы запчастей, необходимые для удовлетворения спроса.
Все большее число научно-исследовательских центров делают оценки продуктивности изделий, которые будут собраны в автоматическом цикле, и пригодности компонентов изделия для подобного технологического решения организации производства. Автоматизированные системы стали широко применяться без оценки продуктивности выпускаемых изделий и затрат на технические работы.
В связи с изменением спроса на мелкую серию новых продуктов инженеры-конструктора и инженеры-технологи предприятий должны находиться в контакте со специализированными консультативными системами, чтобы получать помощь в оценке пригодности продукта для автоматической сборки и экономической целесообразности подобного решения.
Поиск оптимального уровня автоматизации сборки становится возможен благодаря процессу анализа и системы отбора (описана в SOP 04), разработанной автором статьи [5] и в настоящее время дополненной модулем оценки подготовленности продукта к автоматической сборке и выбора оптимального уровня автоматизации, включая оценку типа и стоимости оборудования.
Чтобы автоматические сборочные системы использовались максимально эффективно, технологический процесс сборки изделия и его узлов должен быть правильно разработан. Поэтому особое внимание уделяется именно конструкторской и технологической подготовке изделия для автоматизированной сборки. Это требует постоянного анализа и оценки результатов с целью получения более технологичной конструкции. С этой целью показатели производительности деталей, сборочных единиц и изделия в целом обычно определяются из пригодности к условиям автоматической сборки, после чего сравниваются между собой, и производится их суммирование. Это необходимо для постоянной проверки производительности выпуска рассматриваемой продукции, хотя по многим причинам вопросы производительности сборки не анализируются должным образом на стадии проектирования и даже позже.
Проектные решения изделия и его компонентов, сборка которых планируется к автоматизации, должны предопределять не только простоту осуществления сборочного процесса, но и простоту конструкции сборочной оснастки и инструментов. Производительность сборки также тесно связана с надежностью и стабильной работой сборочного оборудования. В целях обеспечения надлежащей производительности выпуска продукции [1, 2] к конструкции отдельных деталей следует использовать особый подход.
Для объектов автоматической сборки должно быть характерно:
- удобство автоматической ориентации и подачи;
- удобство базирования и транспортировки в зону сборки;
- оптимизация конструкции под автоматическую сварку и контроль шва;
- минимальное количество деталей в собираемом узле;
- простота конструкции;
- соблюдение принципов модульности.
В автоматической системе сборки собираемые объекты должны быть определенным образом доставлены в область, где происходит непосредственное соединение. Поэтому важное значение имеет поведение компонентов при ориентировании и манипулировании, поскольку оно оказывает влияние на способ осуществления сборки, который должен быть заранее предопределен. Проектируя сборочный процесс, следует принимать во внимание условия взаимной ориентации присоединяемых деталей (базовой и пристраиваемой), то есть – приведение к надлежащему контакту заданных поверхностей и фиксации соединения, так называемую иммобилизацию двух компонентов по отношению друг к другу.
Оценивая конструкцию и производительность сборки, разрабатываются компьютерные алгоритмы, согласно которым автоматически выставляется экспертная оценка пригодности изделия к автоматической сборке. Алгоритм оценки изделия исходит с точки зрения критерия производительности, что позволяет конструкторам и технологам выбрать наиболее выгодные решения и избежать случайных ошибок. Анализируя подробное описание процесса сборки, программа выполняет углубленный анализ сопряженных деталей, оценивает пригодность соединения для автоматической сборки и дает экспертное заключение о проекте, с указанием непригодных элементов.
2 Системы оценки технологичности деталей и узлов автоматической сборки
Предложенный модуль оценки технологичности конструкции и ее пригодности для условий автоматической сборки был построен с использованием накопленной базы знаний системы, искусственных нейросетей и специально разработанного программного обеспечения. Модуль базируется на ГУРУ.
Разработанная система позволяет анализировать конструкцию и соединения с помощью программы, интерфейс которой показан на рис. 1. Для оценки воспроизводимости конструкции система задает пользователю ряд вопросов. Вопросы отображаются в последовательных окнах диалога, где пользователь должен ответить «Да» или «Нет» на заданный вопрос. Если функция оказывается несовместимой с общими правилами производительности автоматической сборки изделий, отображается сообщение (рис. 1b). Если система не обнаруживает ошибки в структуре, отображается сообщение «Конструкция верна с точки зрения производительности» (рис. 1c).
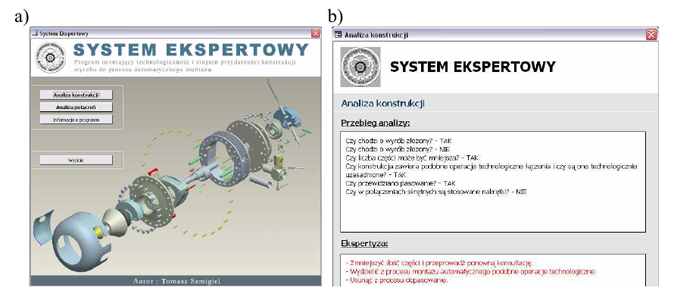
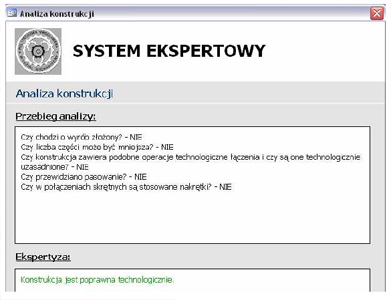
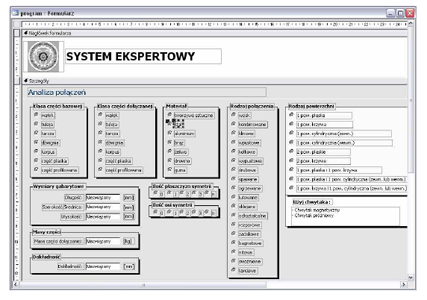
Рисунок 1
С началом анализа соединений (рис 1d) требуется ввести основные функции сборки, такие как: базовая деталь, класс, ориентируемость (количество осей и плоскостей симметрии), габаритные размеры (длина, ширина, диаметр, высота), материал, тип соединения, требуемая точность, масса деталей и тип поверхностей.
После введения данных система приступает к их анализу, используя знания базы, дает экспертное заключение, оценивая, подлежат ли соединения автоматической сборке, а также дает рекомендации в виде подробного отчета или сообщения (в зависимости от выбранного варианта) (рис. 2).
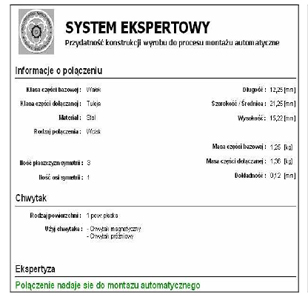
Рисунок 2
Если соединение не удовлетворяет требованиям по технологичности, программа дает подробные объяснения, почему конструкция не подходит для условий автоматической сборки, и предлагает рекомендации по модернизации (рис. 3).
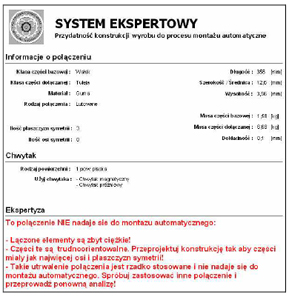
Рисунок 3
3 Уровень автоматизации выбранного модуля
При проектировании сборочных процессов особенно трудно определить оптимальный уровень автоматизации, то есть соотношение долей ручных и автоматических операций в сборке. Этот фактор существенно влияет на производительность, именно он определяет трудоемкость сборки изделия, количество слесарей-сборщиков, тип и стоимость оборудования. Неправильно выбранная степень автоматизации влечет за собой дополнительные затраты, низкую производительность и отсутствие гибкости и зачастую – потребности в новых инвестициях, направленных на снижение этой степени.
Существующие методы определения оптимального уровня автоматизации сборки достаточно неэффективны, поскольку базируются на субъективной оценке уровня автоматизации через несколько вариантов, расчете их экономической эффективности и выборе решения, который наилучшим образом соответствует исходным предположениям. Такие методы весьма трудоемки, а их результаты – неудовлетворительны. Позже это приводит к проблемам с производительностью и дальнейшими расходами.
Принцип, касающийся конструкции и технологических особенности производительности и экономической эффективности, позволяет объективно определить уровень автоматизации и оправдать конфигурацию сборки оборудования [4]. В качестве численной характеристики уровня автоматизации сборки целесообразно применять относительное значение Х:

где tP – трудоемкость ручной сборки изделия;
tJ – трудоемкость j-ого варианта сборки.
В соответствие с вышеуказанным, в зависимости от необходимых параметров все сборочные процессы находятся в интервале от 0 до 1, где Х=0 соответствуют ручной сборке и увеличивается с уровнем автоматизации. Например, расчетный уровень автоматизации сборки (для различных видов изделий) [6] Х равен нулю для ручной сборки, до 0,25 – для механизированной, близок к 1 – для полуавтоматической сборки и равен 1 – для автоматической.
Учитывая конструкцию изделия, условия производства, вид оборудования, общий уровень автоматизации производства, проводится функционально-стоимостной анализ, в котором указанные параметры рассматриваются в отношении друг к другу. Основным критерием, связывающим параметры между собой, будет функция вида:

где ZJ – переменный показатель снижения расходов;
M – количество операций сборочного процесса;
j – порядковый номер варианта;
i – операционный номер варианта;
δ = 1,5 – соотношение оплаты и расходов;
β – суммарные расходы, пропорциональные прямой оплате труда;
S – тариф слесаря-сборщика;
N – годовая производственная программа выпуска изделий;
En – нормативный коэффициент эффективности капиталовложений (1,15..1,25);
AIJ – стоимость оснастки на i-ой операции;
aIJ – количество оснастки, работающей параллельно на i-той операции.
Минимальный уровень автоматизации Xmin соответствует минимуму функции и рассчитывается из следующего соотношения [6]:

где p1, q1, p2, q2 – поправочные коэффициенты регрессии;
tP – трудоемкость ручной сборки.
Пример выбора оптимального уровня автоматизации для любой производственной программы конкретного изделия показан на рис.4.
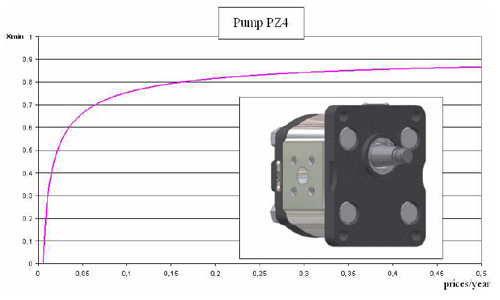
Рисунок 4
4 Заключение.
Разработанная система является эффективным инструментом программного обеспечения для конструкторов и проектировщиков, позволяя работать в аппаратно-программной среде, специально предназначенной для решения комплексных конструкторских и технологических задач и проблем, в том числе – анализа сборочных узлов и организации процессов сборки.
Благодаря этой системе можно принимать обоснованные решения о пригодности рассматриваемых соединений для автоматической сборки и получить экспертное заключение, прямо указывающее непригодные места в конструкции изделия. В результате время, которое конструктор будет тратить на ряд трудоемких рутинных интеллектуальных задач, значительно уменьшается.
Основные преимущества системы включают:
- сокращение времени разработки;
- быстрый доступ к результатам работы;
- гибкость для случаев, когда исходные данные меняются на разных стадиях проектирования;
- снижение затрат на проектирование технологии.
Представленные консультативные системы в сочетании с анализом области сборочных работ и конструкции изделия и модулей для выбора оснастки, транспортных систем, питателей и т.д., приносит заметные выгоды, вытекающие из сокращения реализации процесса проектирования и технологической подготовки производства.
Список использованной литературы
- Zurek J., Briese W.: Algorithmization of producibility evaluation for automatically assembled machine parts and units (in Polish), Technologia i Automatyzacja MontaZu, 1999, No. 4.
- Lunarski J.: Producibility of automatically assembled machine structures (in Polish), Wyd. OBR TEKOMA, Warsaw, 1991.
- Reifur B.: Costs of automatic orientation equipment as expert system module (in Polish), Technologia i Automatyzacja MontaZu, 2002, No. 4.
- Zha X.F., Du H.J.: Knowledge-based approach and system for assembly oriented design. Part I. The approach, Engineering Applications of Artificial Intelligence I, 1 Febr. 2001.
- Reifur B.: SOP, Cracow, 2004.
- Zenkin A.S., Labutina W.O., Kozello N.L.: Wyznaczanie optymalnego poziomu automatyzacji procesуw technologicznych montaSu wyrobуw, Technologia i automatyzacja montazu, 2003, No. 2.