Методика оценки технологичности конструкции изделия для условий автоматической сборки
Автор: А.Г. Холодкова, к.т.н.
Источник: Ежемесячный научно-технический и производственный журнал «Сборка в машиностроении, приборостроении» 11-2008 (100)
Аннотация
Рассмотрена методика количественной оценки возможности применения автоматической сборки изделия, которая позволяет рассчитать коэффициент автоматизации сборочного процесса.
Жизненный цикл изделия в значительной степени зависит от технологичности его конструкции при изготовлении и эксплуатации. Конструкция изделия, в первую очередь, должна быть подготовлена к конкретным условиям: технологии, оборудованию, техническому оснащению и организации процесса.
Автоматическая сборка предъявляет ряд особых требований к конструкции собираемого изделия и его элементов. Недостаточно полное и четкое выполнение этих требований приводит к снижению качества собираемых изделий, неоправданным затратам труда, средств, материалов, времени и зачастую делает невозможным автоматизацию сборочных процессов.
Автоматическая сборка – процесс образования соединений изделий и его составных частей, осуществляемый при помощи автоматического сборочного оборудования и состоящий из следующих этапов:
- загрузка и предварительная ориентация деталей;
- транспортирование деталей в зону сборки;
- базирование и окончательная (взаимная) ориентация;
- выполнение соединения;
- удаление подсобранного изделия или сборочной единицы со сборочной позиции.
В каждом конкретном случае число и содержание выполняемых операций и переходов сборочного процесса обусловлено конструкцией собираемых деталей и изделия или сборочной единицы.
Существенное влияние на надежность и качество сборочного автоматического процесса оказывают функциональные элементы деталей и сборочных единиц, участвующих в сборочном процессе и взаимодействующих с ориентирующими, транспортными и исполнительными сборочными механизмами автоматического сборочного оборудования.
В соответствии с ГОСТами России 14.201–83, 14.205–83 оценку технологичности конструкции проводят по двум критериям: качественным и количественным [1].
При качественной оценке (хорошо – плохо; допустимо – недопустимо) проектируемого изделия определяют соответствие конструкции требованиям автоматической сборки:
- минимальное число деталей;
- наличие сборочных единиц;
- обеспечение точности замыкающих звеньев размерных цепей методом полной взаимозаменяемости;
- наличие надежных установочных баз и баз для ориентации деталей;
- удобство подвода автоматического сборочного инструмента;
- уровень унификации элементов собираемых деталей;
- характер и размеры сопряжений;
- количество направлений сборочных движений при выполнении соединений;
- наличие центрирующих элементов на сопрягаемых поверхностях (фасок, поясков, расточек и т.п.).
В ряде отраслей на предприятиях, проектирующих изделия под автоматическую сборку, создают специальные альбомы, руководящие документы, в которых приведены технологические решения конструкций деталей и соединений, обеспечивающих безотказную автоматическую сборку.
Для обеспечения ориентации деталь должна быть симметричной (иметь максимум плоскостей симметрии). Если деталь в целом симметрична, но имеет некоторые асимметрично расположенные конструктивные элементы (выступы, проточки, отверстия и т.п.), то полную симметрию обеспечивают введением дополнительных "ложных" элементов.
У асимметричных деталей асимметрия должна быть ярко выражена, причем всегда предпочтительнее асимметричность по наружной поверхности детали. Детали, которые необходимо ориентировать по внутреннему асимметричному контуру, должны иметь на наружной поверхности отличительный элемент, расположенный в соответствии с внутренним контуром. Помимо этих требований асимметричные детали надо проектировать таким образом, чтобы центр тяжести не совпадал с условным геометрическим центром и был как можно дальше удален от последнего.
Для удобства ориентации в некоторых случаях следует вводить дополнительные конструктивные элементы, не требуемые служебным назначением детали (пазы, выступы, фланцы и т.п.). Шпильки должны иметь резьбу одного шага и направления, длины резьбовой части должны быть одинаковой величины. Если резьбы на концах шпильки имеют разные шаги, то желательно, чтобы длины резьбовых частей отличались друг от друга.
Детали не должны сцепляться и заклиниваться друг с другом при автоматических ориентации и подаче в зону сборки в загрузочных и подающих устройствах. Детали, напоминающие по своей конфигурации колпачки и стаканы, должны иметь на дне выступы, которые препятствуют их случайному западанию. В деталях, имеющих пазы и выступы, размеры выступов должны быть больше размеров пазов, а внутренние и внешние криволинейные поверхности должны иметь разные радиусы кривизны.
Диаметр внутреннего отверстия в деталях должен быть меньше диаметра выступающей части.
Во избежание заклинивания деталей типа пружинных шайб ширина замка не должна превышать их толщины. В противном случае замок у таких деталей выполняют в виде косого или ступенчатого паза. Также у полых деталей, имеющих сквозной паз, ширина последнего должна превышать толщину стенки.
Для удобства транспортирования детали ее опорная поверхность (установочная база) должна иметь достаточную площадь. Если это торец головки ступенчатой цилиндрической детали, то ее диаметр должен быть больше, чем остальные диаметры, переходный радиус должен быть минимальным.
Во избежание сцепления спиральных пружин необходимо выполнить ряд условий: шаг навивки пружин должен быть меньше толщины проволоки или пружина должна иметь плотную навивку у торцов и в средней части, пружины должны быть изготовлены с заправленными шлифованными торцами, конечные витки пружин сжатия должны располагаться параллельно друг другу. В противном случае пружины нужно подавать на сборочную позицию в ориентированном положении в кассетах.
Желательно под автоматическую сборку проектировать изделия, состоящие из минимального числа деталей. Это достигают изменением конфигурации деталей и применением других видов соединений. На рис 1 приведены конструкции одноцелевого назначения. Число деталей во втором варианте (см. рис. 1, б) было существенно уменьшено, что позволило сократить трудоемкость и себестоимость автоматического сборочного процесса, снизить капитальные затраты и размер занимаемых производственных площадей.
Новая конструкция имеет не только на одну деталь меньше, но и обеспечивает удобство сборки на автоматической сборочной позиции, так как присоединяемый подузел устанавливают вертикально сверху вниз. В базовом варианте присоединяемый узел устанавливали снизу, что требовало кантования собираемого изделия.
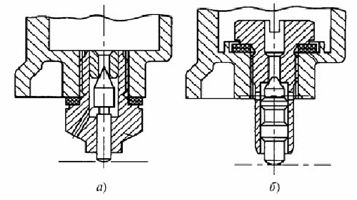
Рис. 1. Упрощение конструкции за счет сокращения числа деталей:
а – нетехнологичная конструкция; б – технологичная конструкция

Рис. 2. Объединение нескольких деталей в конструкции:
а – исходная сборная конструкция; б – конструкция, полученная литьем
Существенное сокращение деталей в конструкции изделия дает применение крепежных комплектов, в которых стопорящие детали объединены с резьбовой деталью. Накатка резьбы на винтах после установки шайб существенно упрощает конструкцию исполнительного механизма на сборочной позиции: отпадает необходимость предварительной подсборки винта с пружинной шайбой.
Современные технологические методы (прецизионное литье, порошковая металлургия, штамповка и т.д.) позволяют объединить несколько деталей (рис. 2, а) в одну более сложную (рис. 2, б).
Уменьшения количества деталей достигают применением анаэробных адгезивов, с успехом заменяющих стопорящие детали у резьбовых соединений, шпонки для передачи крутящего момента, герметизирующие прокладки. Эффективно применение крепежных элементов – заклепок, изготовленных заодно с базовой деталью вытяжкой, выдавливанием и т.п.
В последние годы широкую известность приобрела методика проектирования изделий DFMA (Design for Manufacture and Assembly), которая базируется на 3 методах, оценивающих технологичность изделия при проектировании с помощью 3 модулей:
Альтернативные проекты разрабатываемого изделия, сгенерированные во время анализов DFA и DFM, сравнивают между собой, а также с данными конкурентоспособных изделий при помощи модуля DFC. Мерой эффективности процесса сборки и степени сложности конструкции является модуль DFA:
где NM – теоретически минимальное число деталей, обеспечивающих правильное функционирование собранного изделия; TM – суммарное прогнозируемое время сборки; число 3 означает идеальное время сборки, равное 3с на одно соединение.
Величина этого показателя для данного конкретного изделия может уменьшиться только в результате ликвидации ненужных деталей или операций при сборке: пригонке, регулировке и т.п. Этот показатель представляет собой качественную оценку конструкции изделия с точки зрения эффективности сборочного процесса.
В настоящее время в этой методике добавлены модули разборки и рециклинга, касающиеся более поздних фаз жизненного цикла изделия. Однако модуль разборки также важен и при изготовлении изделия, когда в конструкции применяют сборочные единицы – комплекты, требующие разборки перед общей сборкой (шатун в сборе с крышкой, разъемные опоры коленчатого вала и т.п.). Удобство разборки необходимо учитывать в процессах испытания и обкатки механизмов.
При проектировании группы изделий различных типоразмеров для гибкого роботизированного производства одним из важнейших требований является унификация вида сопряжений, базовых и присоединяемых деталей, механизмов и схватов, что позволяет существенно снизить время на переналадку оборудования при переходе на сборку изделия другого типоразмера.
Для количественной оценки свойств конструкции, характеризующей ее технологичность в целом или раздельно по производственным признакам, Госстандартом России разработана единая система показателей, обязательная для анализа конструкции в процессе проектирования при выборе оптимального варианта.
Технологичность конструкции изделия в изготовлении (производственная технологичность) определяют следующие основные показатели: трудоемкость Т, ч; себестоимость С, руб. Дополнительными показателями являются коэффициенты, оценивающие: уровень стандартизации (Кст) и унификации (Кун); повторяемости (Кпов) изделий; наличие сборочных единиц (Ксб); методы, обеспечивающие точность замыкающего звена (Квз); уровень механизации и автоматизации сборки (Кмех; Кавт) и т.д. Пределы большинства относительных частных показателей одинаковы:
0 ≤ K ≤ 1
Комплексный показатель технологичности конструкции изделия удобно выражать среднеарифметической величиной с учетом экономической эквивалентности Кэ.эi ("весового" вклада) принятых показателей Кi:

где К – комплексный показатель технологичности; Кi – частный показатель технологичности; Кэ.эi – коэффициент экономической эквивалентности i-го частного показателя.
Значения комплексного показателя коэффициентов экономической эквивалентности находятся в тех же пределах, что и частных показателей.
Потребность в объективной оценке уровня автоматизации сборки проектируемого изделия привела к созданию отраслевых методик расчета коэффициентов технологичности, как комплексных, так и частных, при помощи которых можно рассчитать коэффициент автоматизации и оценить влияние конструкции на трудоемкость, себестоимость и производительность автоматического сборочного процесса.
Методика комплексной многоуровневой оценки технологичности конструкции изделия для условий автоматической сборки, разработанная совместно коллективами ПНО "Автопромсборка" (г. Минск) и МГТУ им. Н.Э. Баумана, была апробирована как в автомобильной, так и в приборостроительной промышленности в 80–90 гг. XX века [2].
Согласно этой методике выделены группы функциональных элементов и сборочных единиц, влияющих на выполнение каждого этапа автоматического сборочного процесса, и оценены:
- возможность использования различных ориентирующих и подающих устройств при наличии у собираемых деталей надежных баз ориентации, устойчивости, отсутствии сцепляемости, симметричности расположения их поверхностей, а также сложности и стоимости ориентирующих и транспортных устройств. На этом уровне оценка технологичности конструкции собираемых деталей выражена комплексным показателем Кт.д;
- возможность безотказного выполнения соединения с заданным качеством различными исполнительными механизмами и устройствами с учетом их сложности и стоимостных затрат. На этом уровне оценка технологичности конструкции соединения описана комплексным показателем Кт.с. Если показатели технологичности двух деталей Кт.дi и их соединения Кт.сi больше или равны нормативным значениям, при которых автоматические процессы ориентации деталей, их подачи в зону сборки и выполнения соединения проходят безотказно с обеспечением требуемого качества сборки, то такое соединение можно выполнять автоматически;
- структура и состав сборочного оборудования с учетом надежности его работы, капитальных затрат и продолжительности цикла сборки. На этом уровне технологичность конструкции изделия оценивают комплексным показателем Кт.и.
Графически методика многоуровневой оценки технологичности конструкции изделия для автоматической сборки представлена на рис. 3.
Частные показатели технологичности Ктi рассчитывались на основе данных многолетних теоретических, экспериментальных и производственных исследований процессов автоматической сборки различных соединений, а также размеров капиталовложений на создание или приобретение сборочного автоматического оборудования. Коэффициенты Кэ.эi определяли с учетом влияния каждого частного показателя Ктi на производительность и себестоимость автоматического сборочного процесса по результатам экспериментальных и производственно-статических исследований и на основании экспертных оценок. Для этого использовали опыт квалифицированных специалистов (экспертов) в области автоматической сборки. На основании опыта и имеющейся информации каждый из экспертов предсказывал величину Кэ.эi в виде максимального и минимального значений в пределах 0…1. Далее на основе полученных данных вычисляли следующие величины.
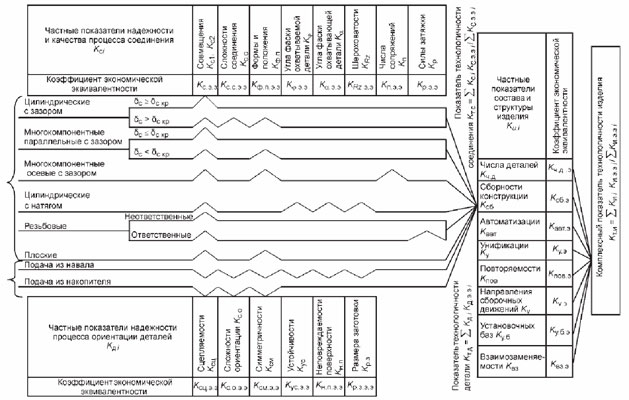
Рис. 3. Многоуровневая оценка технологичности конструкции изделия для автоматической сборки
По оценкам каждого i-го эксперта средние значения Мi(x) и дисперсию Si(x):

Среднее значение оценок экспертов:

Среднеквадратичная ошибка оценок экспертов:

где N - количество экспертов.
Проверку согласованности мнений экспертов проводили при помощи коэффициента вариации по формуле:

Так как в сумме значения всех коэффициентов Кэ.эi должны быть равны 1, то каждый из коэффициентов Кэ.эi может быть очень мал. Для удобства расчетов часто пользуют другие способы определения Кэ.эi [2]: коэффициент Кэ.эi, имеющий максимальное значение, принимают равным единице, и остальные коэффициенты находят по формулам
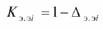

Если комплексные показатели технологичности соединения Кт.сi и образующих его деталей Кт.дi будут больше или равны нормативным (минимально допустимым) значениям этих показателей, данное соединение пригодно для автоматического выполнения. Если Кт.сi и Кт.дi будут меньше нормативных значений этих показателей, то конструкции элементов изделия нуждаются в доработке, в противном случае уровень автоматизации сборки снизится.
После определения показателей Кт.сi и Кт.дi для всех соединений и деталей рассматриваемого узла или изделия можно рассчитать коэффициент автоматизации сборки:

где Nс.авт – число соединений, выполнение которых можно осуществить автоматически на всех этапах сборочного процесса; Nс – общее число соединений в изделии.
В работе [2] были определены значения коэффициентов экономической эквивалентности рассмотренных ранее дополнительных частных показателей технологичности Кт.иi.
Определение частных показателей технологичности изделия позволяет рассчитать комплексный показатель технологичности изделия, оценивающий уровень его пригодности к автоматической сборке, по формуле

Причем при Кч.д, равном 0,9…1 (при числе деталей не больше 8), коэффициент сборности не учитывают. Было принято, что при значениях комплексного показателя Кт.и меньше 0,6 конструкцию изделия можно считать технологичной для автоматической сборки. При меньших значениях Кт.и конструкция изделия нуждается в доработке.
Вывод.
Разработанная программа расчета Kт.и, т.е. оценки технологичности конструкции для автоматической сборки по рассмотренной методике является подсистемой в структурной схеме основных этапов проектирования ТП автоматической сборки с применением ЭВМ в рамках автоматической системы технологической подготовки производства (АСТПП).
Список использованной литературы
- Амиров Ю.Д. Технологичность конструкции и качество сборки изделия // Сборка в машиностроении, приборостроении. 2003. № 6, 7. С. 3–9.
- Методика и нормативы оценки технологичности конструкции деталей и сборочных единиц автомобилей при автоматической сборке: руководящий документ. Минск. 1985. 405 с.