Механизм зарастания погружных стаканов при непрерывной разливке стали
Авторы: Аксельрод Л.М., Паршин В.М., Мазуров Е.Ф.
Источник: Журнал «Сталь». – 2011. – 2007. – №4. – С. 30-33.
Аннотация
УДК 621.746.047
Аксельрод Л.М., Паршин В.М., Мазуров Е.Ф. Механизм зарастания погружных стаканов при непрерывной разливке стали. Рассмотрен механизм формирования отложений на внутренней поверхности погружных стаканов при непрерывной разливке и приведены результаты исследования их микроструктуры.
Качество непрерывнолитой заготовки и стабильность разливки – взаимосвязанные параметры процесса. Отложения неметаллических включений на стенках канала сталеразливочного тракта (стакан-дозатор и погружаемый стакан, включая сталевыпускные отверстия) вынуждают уменьшать скорость непрерывной разливки вплоть до ее полного прекращения. Неметаллические включения могут привести к значительным дефектам металла. Формирующиеся в канале отложения ухудшают условия разливки, оказывая косвенное влияние и на количество плен: уменьшение проходного сечения металлопровода приводит к неравномерности потока и колебаниям уровня металла в кристаллизаторе, что способствует попаданию покровного шлака из кристаллизатора в металл [1] и, как следствие, к нарушению равномерности процесса формирования структуры слитка.
В результате процесс затягивания становится причиной снижения производительности и качества металла. Для замедления процесса затягивания необходимы: защита струи металла от вторичного окисления на всем протяжении металлургического тракта, включая выпуск металла из сталеразливочного ковша; снижение активности кислорода и содержания неметаллических оксидных включений в стали перед разливкой за счет вакуумирования металла и обработки его восстановительными шлаками; модифицирование неметаллических включений глинозема вводом в металл кальция; создание условий для удаления включений в промежуточном ковше в результате применения турбостопов, перегородок, порогов, вдувания аргона в металл в промежуточном ковше; эти меры эффективны в сочетании с применением шлакообразующих смесей; использование в конструкции металлопроводов огнеупоров, взаимодействующих с глиноземными неметаллическими включениями, например содержащих цирконат кальция, с образованием предположительно легкоплавких соединений, смываемых затем потоком металла, либо применение несмачиваемых материалов, формирующих газовую прослойку на контакте огнеупор – неметаллические включения.
Это, конечно, не все известные меры; например, не затронуты вопросы гидродинамики истечения металла, геометрии сталевыпускных каналов, что в ряде случаев может играть существенную роль.
В металле к началу разливки после его глубокого раскисления алюминием содержится значительное количество неметаллических включений. Так, в 325-т ковше сталь, раскисленная алюминием (0,0015 % [Al] или 15 ррm), содержит до 3 – 4 л плотного оксида алюминия, значительная доля которого, вероятно осядет на стенках сталевыпускного тракта промежуточного ковша [2], вызывая уменьшение внутреннего диаметра канала. При разливке стали методом «плавка на плавку» количество сорбированных на поверхности стакана неметаллических частиц возрастает и в итоге приводит к его зарастанию. При этом возрастает роль включений второго и третьего рода, которые в определенных условиях способны сформировать значительную долю отложений в канале металлопровода.
Исследованы отложения в погружаемых стаканах при непрерывной разливке металла трех цехов: металл в ковше раскисляли алюминием и обрабатывали в одном случае известково-глиноземистым шлаком с продувкой аргоном, в другом – твердой шлакообразующей смесью (CaO – CaF2) с продувкой аргоном, в третьем металл в ковше раскисляли алюминием и вакуумировали (RH). Концентрация алюминия находилась в пределах 0,02 – 0,45 %. Содержание магния в металле обычно составляло 0,0004 – 0,0050 %. Перед разливкой содержание кальция, например, в стали 09Г2ФБ было в пределах 0,0010 – 0,0045 %. При 0,02 – 0,06 % [Аl] содержание Са в стали 09Г2ФБ составляло 0,001 – 0,002 %.
Типичная картина отложений, которая обычно фиксируется на внутренних поверхностях погружаемых стаканов, представлена на рис. 1. Видно, что отложения на стенках погружаемых стаканов имеют зональную структуру. Фазовый состав отложений на стенках погружаемых корундографитовых стаканов (по данным петрографического и рентгенофазового анализа) при разливке сталей Ст3 и 17ГС приведен ниже. В динамной стали, содержащей 0,45 % [Al] основная фаза отложений представлена глиноземом, в том числе и в рыхлой зоне. Присутствие в стали 10Г2БТ титана в количестве до 0,08 % проявилось в наличии гексаалюминатов кальция (СаО·6Al2О3), содержащих Ti2О3.
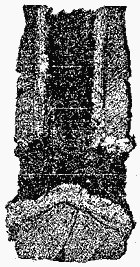
Рисунок 1. Характер отложений на внутренней поверхности погружаемого стакана
Фазовый состав отложений на стенках погружаемых корундографитовых стаканов:
– рыхлый слой: СаО·6Al2О3; СаО·2Al2О3; 2СаО·Al2О3; FeО·Al2О3; MgО·Al2О3;
– промежуточный слой: Al2О3 (вторичный); СаО·6Al2О3; СаО·2Al2О3; металл;
– плотный слой: СаО·Al2О3; Al2О3 (вторичный); металл.
Следует также отметить, что в отложениях наблюдается значительное количество корольков металла размерами 0,001 – 4 мм, матрицей которых служит оксидная составляющая.
В ряде случаев металл представляет собой матрицу, в которой размещены неметаллические включения в виде глиноземсодержащих глобул сложного состава. При этом металл занимает 30 – 95 % объема слоя. Этот вариант типичен для условий разливки стали с температурой в промежуточном ковше на уровне нижнего предела разливаемости. Макро- и микроструктура отложений на стенках каналов погружаемых стаканов представлена соответственно на рис. 1 и 2 при разливке стали следующего состава, %: 0,13 – 0,14 С; 0,63 – 0,64 Мn; 0,21 – 0,25 Si; 0,018 – 0,025 S; 0,014 – 0,018 Р; 0,03 – 0,04 Сr; 0,03 – 0,06 Ni; 0,03 Cu; 0,02 – 0,04 А1; 0,002 Ti. Температура начала и конца разливки 1555 – 1570 и 1540 – 1555 °С соответственно. Химический и фазовый состав отложений, приведенных на рис. 2, следующий, %: 1 – железо металлическое (98,66 Fe; 0,88 Мn; 0,46 О); 2 – частично окисленное железо (90,6 Fe; 1,46 Мn; 7,97 О); 3 – корунд (70,7 Al; 29,30 O); 4 – сложная марганцовистая шпинель (72,84 A12O3; 16,82 МnО; 7,21 MgO; 2,45 FeO; 0,68 TiO2); 5 – cложный марганцевый алюмосиликат (27,95 А12O3; 27,61 SiO2; 27,70 МnО; 4,12 Na2O; 3,77 ТiO2; 3, СаО; 2,29 К2O; 2,69 ZrO2; 1,0 MgO). При этом железо и корунд превалируют, а сложный марганцевый алюмосиликат и частично окисленное железо присутствуют в небольшом количестве.
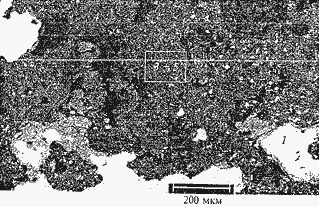
Рисунок 2. Микроструктура отложений на стенке канала погружаемого стакана после службы, РЭМ, ×105:
1 – железо металлическое; 2 – железо, частично окисленное; 3 – корунд; 4 – шпинель марганцовистая; 5 – сложный марганцевый алюмосиликат
Более типичные отложения на стенках погружаемых стаканов [3] включают скопление пластинчатого корунда, гекса- и диалюминатов кальция и шпинели сложного состава с вкраплениями корольков железа.
Природа неметаллических включений в отложениях при содержании [А1] ≥ 0,03 % в сочетании с обработкой высокоизвестковым раскисленным шлаком либо ТШС (CaO + CaF2) соответствует составу алюминатов кальция и магния с присутствием частиц глинозема. Исследование состава неметаллических включений в раскисленной алюминием электростали после обработки «белым» шлаком показывает [4, 5], что включения состоят преимущественно из алюминатов кальция и магнезиальной шпинели. При этом наибольшее количество алюминатов кальция представленo частицами СаО·6Al2О3 и СаО·2Al2О3. Включения, соответствующие фазе 12СаО·7Al2О3, встречается крайне редко и в малом количестве. Большая шасть алюминатов кальция содержит, как правило, кристаллы выделенной магнезиальной шпинели.
Рассмотрим условия формирования неметаллических включений второго и третьего рода в раскисленной алюминием стали и механизм их отложения на стенках погружных каналов.
В условиях разливки металла на входе в стакан-дозатор промежуточного ковша температура металла равна t = tL + (35 – 40) °С. В кристаллизатор сталь поступает при температуре, близкой к температуре ликвидуса (1475 – 1545 °С). Можно предположить, что на огнеупорной холодной стенке стакана происходит уменьшение температуры до двухфазной области и ниже вплоть до температуры солидуса.
При движении жидкого металла по металлопроводу струя металла отклоняется от вертикали и начинает касаться стенки погружаемого стакана, например из-за несоосности расположения стопора-моноблока относительно разливочного отверстия стакана и вертикальных перемещений при регулировании уровня металла в кристаллизаторе. Корундографитовые стаканы (25 – 30 % С), особенно холодные, имеют повышенную теплопроводность. Отметим, что теплопроводность графита при комнатной температуре втрое выше, чем при 1000 °С, и вчетверо, чем при 1500 °С.
В результате теплообмена холодной стенки огнеупора и стали на поверхности стакана формируется настыль. При этом, чем выше теплопроводность стенки, тем вероятнее образование металлической настыли.
В разливаемой стали в растворенном виде имеются кислород и сильные элементы-раскислители, такие как А1, Са, Mg. Таким образом, в стали должны образовываться сложные продукты раскисления. Для анализа и решения проблемы неметаллических включений полезно, на наш взгляд, использовать рассчитанные Г.Г. Михайловым поверхности растворимости компонентов в жидком металле (ПРКМ), которые позволяют установить комплекс оксидных фаз, образующихся при взаимодействии металлического расплава системы Fе – С – О – А1 – Са – Mg с растворенным кислородом.
На рис. 3 и 4 представлены ПРКМ в системах Fе – С – О – А1 – Са и Fе – С – О – А1 – Са – Mg при 1500 и 1550 °С и 101 кПа. Жирными линиями здесь заданы концентрационные области жидкого металла, равновесного с одной из оксидных фаз – продуктов раскисления стали, природа которых указана в круглых скобках. Тонкими линиями нанесены изокислородные сечения.
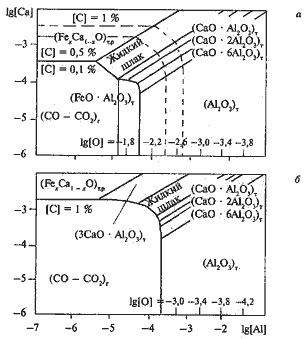
Рисунок 3. ПРКМ системы Fе – С – О – А1 – Са при 1550 (а) и 1500 °С (б), p = 101 кПа
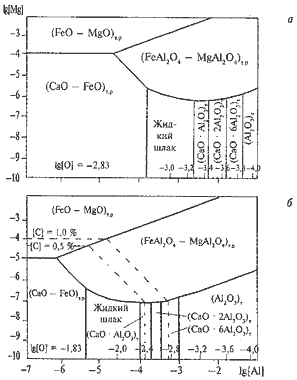
Рисунок 4. ПРКМ системы Fе – С – О – А1 – Са – Mg при °С, р = 101 кПа, 5·10-3 % [Ca] (a) и 5·10-4 % [Ca] (б)
В соответствии с содержаниями [А1], [Са], [Мg] и ПРКМ для систем, приведенных на рис. 4 и 5, равновесные неметаллические включения должны содержать алюминаты кальция состава СаО·6Al2О3; СаО·2Al2О3; СаО·Al2О3; шпинели системы FеО·А12О3 – MgО·А12О3 (герцинит-алюмомагниевая шпинель).
При высоком содержании алюминия в стали равновесной фазой во включениях оксидов будет корунд (А12O3). При небольших содержаниях алюминия (≤ 0,01 %), Са и Мg (< 10-6 – 10-7 %) равновесный состав неметаллических включений представлен оксидами сложного состава, дополнительно содержащими SiO2, МnО, FеО. При содержании [А1] ≥ 0,03 % и относительно низких концентрациях [Мg] и [Са], согласно ПРКМ системы Fе – С – О – А1 – Са – Мg, выделяющиеся включения будет соответствовать корунду. При температуре разливки состав отложений зависит от содержания Са, Мg, А1, находящихся в расплаве.
Если рафинирование стали перед разливкой было недостаточно, то отложения могут иметь смешанный состав – от алюминатов кальция (и шпинелей) до глинозема.
Обычно в конвертерной стали, раскисленной алюминием, содержится мало магния и кальция, поэтому при разливке погружаемые стаканы зарастают пре-имущественно отложениями глинозема.
При вакуумировании и обработке рафинировочным шлаком в ковше-печи сталь эффективно очищается от включений. По данным работы [6], активность кислорода в стали уменьшается до 10 – 15 ppm.
На рис. 1 и 2 приведены разрез погружаемого стакана и состав отложений при разливке металла после вакуумирования и обработки восстановительным шлаком на агрегате ковш-печь, т. е. при достаточно низкой активности кислорода в стали. ПРКМ системы Fe – С – О – А1 – Са – Mg показывают, что при температурах раскисления и разливки равновесными оксидами являются включения глинозема (А12О3); при разливке стали с высоким содержанием алюминия (0,45 % в динамной стали) отложения соответствуют составу глинозема.
При снижении температуры стали область формирования глинозема расширяется (см. рис. 3). Уменьшается относительное содержание растворенных в стали кальция и магния (отрицательная величина удельной свободной энергии образования СаО и МgO больше, чем А12O3). Поэтому с понижением температуры расплава при движении по металлопроводу, например от 1550 °С до температур двухфазной области, содержание растворенного кальция (и магния) в металле становится меньше (10-6 – 10-7 %). В этом случае во время контакта со стенкой стакана основным типом вновь возникающих включений в соответствии с ПРКМ систем Fe – С – О – А1 – Са и Fe – С – О – А1 – Са – Mg будут включения глинозема (А12O3).
Константа равновесия КAl составляет ∼ 10-9 [7]. При уменьшении температуры стали в процессе разливки в месте контакта металла со стенкой холодного стакана КAl понижается до 10-14. Вновь возникающие в стали включения глинозема из-за существенного снижения КAl по механизму зарождения и роста должны быть мелкими и могут быть отнесены к типу вторичных и третичных.
Рассмотрим энергетически наименее благоприятный случай – возможность гомогенного зарождения включений глинозема в объеме струи металла (такая возможность не отрицается, например, В.И. Явойским [8]). Радиус гомогенно зарождающегося включения глинозема с ростом вследствие диффузии можно оценить по уравнению [7]:

где N = 5·107 см-3 – число частиц;
СО = (7; 14; 21)· 10-5 г/см3 – исходная концентрация кислорода в стали;
Сgl – равновесная концентрация (активность кислорода с поверхностью частицы глинозема при аА12O3 = 1 г/см3; при 0,02 и 0,05 % [Al] – 15,4·10-5 и 2,8·10-5 г/см3 соответственно;
Ср – 1,9 г/см3 – концентрация кислорода в оксиде; lgKА12O3 = -64000/T+20,48.
Радиус зарождающихся включений составив 0,48 – 0,78 мкм.
Длительность роста частицы глинозема в результате чистой диффузии до 90% конечного объема составит [7]:

где D = 6·10-5 см2/с – коэффициент диффузии кислорода в жидком железе;
r – радиус частицы, мкм.
Расчет подтверждает возможность возникновения и быстрого роста мелких включений А12О3 при фактической активности кислорода в стали. Длительность роста частицы глиноземистого включения составит 0,34 с.
В работе [9] показана возможность ускоренного перемещения мелких частиц в концентрационном поле в сторону увеличения содержания кислорода. Поскольку на поверхности струи металла концентрация кислорода всегда выше (в том числе за счет атмосферного кислорода), возникающий градиент поверхностного натяжения вдоль границы раздела частица – раствор вызывает механическое движение мелких частиц к стенке стакана. Поэтому в процессе разливки возникающие мелкие включения глинозема (или алюминатов) могут быстро (ускоренно) перемещаться на поверхность металл – огнеупор, «прилипать» к стенке стаканов и спекаться.
Оценочные расчеты по формулам (1) и (2) хорошо согласуются с экспериментальными данными, что свидетельствует об описанном механизме зарастания стакана.
Однако не всегда включения, возникшие в результате смещения равновесия алюминий – кислород в сторону образования А12О3, отложатся на поверхности стакана, так как степень омывания его поверхности струей металла непостоянна как в течение плавки, так и на разных плавках. Условия, особенно температурные на поверхности контакта струи стали со стаканом будут изменяться как в течение конкретной плавки, так и при разливке серии плавок. С другой стороны, несмотря на принимаемые меры по удалению неметаллических включений на стадии подготовки металла, в нем всегда остается определенное количество частиц первого рода, которые служат центрами образования крупных включений за счет налипания на них гомогенно зарождающихся включений, причем в основном небольшого размера. Этот процесс будет способствовать зарастанию канала.
Поэтому всегда степень зарастания стаканов при разливке стали одной марки и на разных ручьях даже в одинаковых условиях будет различаться.
Удельная межфазная энергия на границе огнеупор – включение всегда меньше, чем на границе металл – включение, состоящее из алюминатов кальция или глинозема. Уменьшение поверхностной энергии –ΔF = σМ-ВΔS способствует переходу включений с поверхности металла на поверхность стенки стакана. Вновь появившиеся включения удерживаются на поверхности огнеупора или других уже отложившихся частицах вследствие адгезии и высокотемпературного спекания.
Таким образом, для уменьшения скорости зарастания стаканов необходимо обеспечить как минимальное снижении температуры стали, так и существенное подавление вторичного окисления и сокращение удельной поверхности контакта металла со стаканом.
Для реализации условий, обеспечивающих стабильную непрерывную разливку стали, необходимы:
– организация высокотемпературного (≥ 1000 – 1200 °С) подогрева разливочного и погружного стаканов перед началом разливки в сочетании с их эффективной теплоизоляцией снаружи;
– использование материалов с низкой теплопроводностью, например, бикерамических стаканов с безграфитовым слоем на внутренней поверхности;
– вдувание в канал подогретого инертного газа через стык огнеупоров, составляющих металлопровод, либо через стенку огнеупора.
Библиографический список
1. Jungreithmeier A., Pessenberger E., Burgstaller K. Production of UL CIF Steel Gradies at Voest-Alpine Stahl GmbH // Iron and Steel Technology. 2004. Vol. 1. N 4. P. 41 – 48.
2. Damen W. F. M., Kendall M., Visser N. N. A real clog free nozzle? How the self cleaning nozzle does it? // 5th European Continuous Casting Conference. June 20 – 22.2005. Nice (France). P. 454 – 460.
3. Аксельрод JI. М., Барановский М. P., Мельникова Г. Г. Затягивание графитсодержащих погружаемых стаканов при разливке стали на MHJI3 // Огнеупоры. 1991. № 12. С. 29 – 34.
4. Каблуковский А Ф., Салаутин В. А., Мазуров Е. Ф., Гнучев С. М. Электроплавка стали в крупных печах. – М.: Металлургия, 1979. – 216 с.
5. Kohn A., Wаnin М. // Revue metallurgie. 1969. Vol. 66. N 5. P. 325 – 339.
6. Кузьменко A. Г., Мазуров Е. Ф., Фролов Ю. Ф. Технологические аспекты повышения эффективности внепечной обработки электросталеплавильного комплекса // Сталь. 2006. № 4. С. 33 – 38.
7. Rohde L. E., Choudhury A., Wahlester M. // Archiv Eisenhuttenwesen. 1971. N 3. S. 25 – 32.
8. Явойский В. И. Теория процессов производства стали. – М.: Металлургия, 1963. – 820 с.
9. Минаев Ю. А., Уточкин Ю. И., Григорян В. А. Влияние концентрационных полей на поведение продуктов раскисления стали // Известия АН СССР. Металлы. 1971. № 6. С. 15 – 17.