Abstract
The content of the abstract
- Introduction
- 1. Theme urgency
- 2. Goal and tasks of the research
- 3. Results of the study
- Conclusion
- References
Introduction
Among the stationary electro-mechanical equipment at the mine units are most responsible hoisting systems, which are used for lifting of minerals on the surface of the earth, lowering and lifting people, providing mine the necessary materials and equipment.
Currently, the level of automation of mine hoist systems remains low, resulting in decreased quality control parameters and the efficiency of operation of protection against harmful modes of operation, reduced their reliability and the efficiency of the process as a whole.
Due to the special importance of technological mine hoist installations in mine production, the large size of damage from accidents, as well as a high level of safety requirements for the lifting of persons and control the use of such facilities is permissible only automated systems for compulsory participation rights. With the improvement of systems of automation of mine hoist installations scope of functions performed by a man steadily decreased, and now it remained for the functions that are difficult to automate or more reliably performed by a person in a standard, especially in the emergency situation, as well as a common control of the situation and take emergency measures [1].
1. Theme urgency
Increase of technical and economic indicators of the elevator installation are largely determined by the efficiency of the system of automatic control [2]. Currently, higher reliability and durability, reduced power consumption, increased productivity, and control of all process parameters that affect the working condition of the elevator installation is carried out by means of modern automation. The most rational from the point of view of control is to develop an automated system that collects information from all places of technological area, to carry out their direct processing and transmission. The use of digital sensors and microprocessor technology for the processing and transfer of information allows precise control of a sufficient number of parameters mine hoist machines transmit data to the remote controller and the top level of the automation system, save the sensors over a long period and to analyze the nature of their changes over time.
2. Goal and tasks of the research
The aim is to improve the reliability of the control system of the elevator installation separation through its governance structure and the use of the active reserve components, as well as the organization of the reception, processing, storage and transmission of information about the process on the remote controller.
To achieve this goal should be solved the following problems:
- Analysis of the recovery process, as the object of automation;
- A critical review of the prior art associated with lifting facilities;
- Rationale and development of automation systems hoist installation;
3. Results of the study
Figure 1 shows a block diagram of a system according composed developed algorithm and a control method.
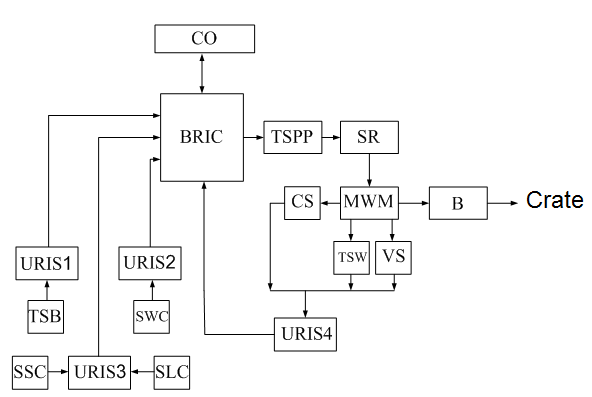
Figure 1 – Block diagram of the automated system of the object
The figure shows the following notation: CO – Computer Operator; BRIC – Block receive information and issue commands; TSPP – The system of pulse–phase control; SR – Synchronous rectifier; MWM – Motor winding machine; B – Drum; VS – The voltage sensor; TSW – Temperature sensor windings; CS – current sensor; TSB – Temperature sensor bearing unit; SSC – speed sensor crates; SLC – Sensor location crates; SWC – Sensor weight of the cargo; URIS 1, 2,3,4 – unit receiving information from the sensors.
The principle of this system is the following: the computer room, as well as at the top, at the bottom of the barrel and copra are set corresponding blocks URIS 1, 2, 3, 4, which in turn have been receiving information from sensors technological process control. Each signal from the sensor to transmit over long distances without loss, is assigned to the appropriate address, by which the unit receiving the information and issue commands will conduct a survey of each block and the data is transferred over the protocol. These signals are received in digital form at the receiving unit of information and issuing commands. Further, all information supplied computer operator at the control panel, where is the monitoring of the process, where the operator collecting the data, can control the motor winding machine in accordance with the specified parameters and operating modes. In each block as a device matching for analog operational amplifiers are used, and is used for discrete isolation. Receiving unit information and issuing commands includes in its composition two microcontrollers (primary and secondary) which are interconnected switching device. In case of failure of the main microcontroller switching device includes a microcontroller backup job. For greater efficiency, chart climb is divided into eight sections and failover backup system microcontroller starts with the point at which the main stop.
Conclusion
The study analyzed the process lifting as an automation object, set goals and objectives of the study. Made a critical review of the known technical solutions to automate the process of recovery. Produced substantiation and development of the automation system of the elevator installation: was developed automation block diagram of the object and the algorithm of each block.
This master's work is not completed yet. Final completion: December 2013. The full text of the work and materials on the topic can be obtained from the author or his head after this date.
References
- Система управления и комплексной защиты шахтной подъёмной установки / [Кащич А., Марищенко А., Божок Н. и др.] // Cистемная интеграция, добывающая промышленность. – 2005. – №2. – С.26–34.
- Руководство по ревизии, наладке и испытанию шахтных подъемных установок: нормативное производственно–практическое издание/В.Р. Бежок, В.Г. Калинин, В.Д. Коноплянов, Е.М. Курченко; Под общей редакцией В.А. Корсуна. – Донецк, 2009. – 672 с.
- Дроздова, Л.Г. Стационарные машины: Учеб. пособие. – Владивосток: Изд-во ДВГТУ, 2007. – 157 с.
- Гаврилов П.Д., Гимельштейн Л.Я., Медведев А.Е. Автоматизация производственных процессов: Учебник для ВУЗов.– М.: Недра, 1985. – 216с.
- Правицкий Н.К. – Рудничные подъемные установки. –Харьков, 1956, 301 с.
- Аппарат защиты и контроля движения [Электронный ресурс]. – Режим доступа: http://www.ooo–yuep.com/ru/azkd
- ABB AB – Mine Hoist Systems [Электронный ресурс]. – Режим доступа: http://www.mining–technology.com/contractors/.
- Каталог продукции компании FHF [Электронный ресурс]. – Режим доступа: http://www.fhf–bt.org/.
- Стороженко М. А. Аппаратура управления и контроля рудничными подъёмными установками / М.А. Стороженко, А.Ф. Кирей. – М.: «Недра», 1980.
- Евстифеев А.В. Микроконтроллеры AVR семейств Tiny и Mega фирмы ATMEL. – 5-е изд., стер. – М.: Издательский дом «Додэка–XXI», 2008. – 560с.