Abstract
Content
Introduction1. Theme urgency
2. The goal and tasks of the research
3. Brief description of the object and contol system.
Conclusion
List of references
Introduction
Today, there are many implementations of so-called balancing robot. In essence, a balancing robot is a stabilization system of inverted pendulum. A balancing robot is usually a platform on two wheels. Principles of construction of these systems are similar, but applied stabilization algorithms and electronic components in the real models are significantly different. It is important in the synthesis of the control system to get an accurate mathematical model of the control object and all the components which are included in the system. This can be done on the basis of the laws of physics, mechanics, etc. Sometimes, however, is not enough knowledge about the object or the object parameters may be changed within certain limits. Then experimental methods, which essentially boils down to a statistical analysis of process data are applied.
1. Theme urgency
The stabilization of unstable physical objects is one of the most frequent problems of control theory which engineers of this area face. Therefore there is a need for a rich experience in solving similar problems for future engineers. It is important to get not only theoretical knowledge and skills for working with mathematical models, but practical skills and experience of working with real physical objects, which physical nature can not be fully described by the model.
One of the most common systems of dynamic balance is the automatic control system of a robot in the form of an inverted pendulum. It has already widespread in automation and robotics due to its simplicity and high agility and flexibility. Using advanced micro-electromechanical systems (MEMS sensors) for this sort of systems provides even greater miniaturization and availability of such systems, thus expanding the scope of their application. Smooth stabilization requires a very precise determination of the deviation angle and the calculation of the control action, taking into account the dynamic characteristics of DC motors, that cause balancing robot to be in a state of balance. Engine’s parameters may differ even running in the different directions of shaft rotation. Therefore, there is a need to identify a model of the motor in various modes to further integration of the model in the control algorithms.
2. The goal and tasks of the research
The main goal of the master's work is to design and build automatic control system which maintains the dynamic balance of the balancing robot, that is developed in the form of an inverted pendulum.
The main tasks of the research:
- Analysis of existing systems and stabilization of dynamic balance.
- Analysis of the available identification methods of models of that kind.
- Development of a mathematical model of the object.
- Development of functional and structural diagrams of the object.
- Modeling of dynamic processes in the object.
- Analysis of the existing methods for determining the deviation angle of the construction and data processing from sensors.
- The research of identification methods of the object’s position.
- Synthesis identification algorithm of the parameters of the balancing robot (motor parameters, deviation angle, position).
- Refinement of mathematical model and programming algorithms for data processing from sensors.
- Development of the bench model of the balancing robot.
3. Brief description of the object and contol system
The design of the balancing robot is quite simple and for this reason it has a number of useful properties. The simplified design of the balancing robot is represented in figure 3.1. Using of two wheels reduces dimensions and increases reliability, and separate management of each of them (by means of DC-motors) does a platform very maneuverable, in particular a platform can turn while moving or perform a turn on a place. But the main shortcoming is that the platform is unstable and after switching off the DC-motors the platform will lose balance and fall. However to make a platform steady the system of automatic control is called. Having created the closed contour, constantly measuring the deviation angle of the platform, there is an opportunity to develop quite frequent control actions which will correct the state of platform.
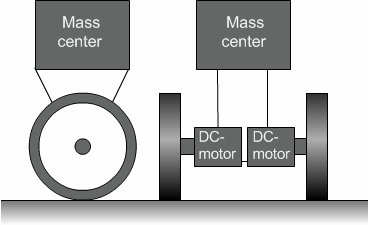
Figure 3.1 — Simplified design of the balancing robot
The idea of balance maintenance is pretty simple. The design has the only point of balance when the mass center of the load is directly over a rotation axis. If the center of gravity of a design deviates aside, gravity is partially transmitted through resistance to the earth, and other its component creates the moment of rotation of a design which seeks to overthrow a design sideways. To compensate this force, the system has to begin movement with acceleration towards falling. F is the force which creates acceleration and it is displayed on force operating towards a support, and force which creates the return moment of rotation of a design.
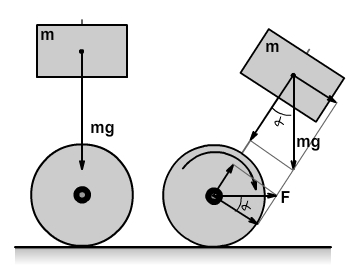
Figure 3.2 — Physical model of object
The condition for balance maintenance is as follows:

Taking into consideration only small deviations from an balance state (α → 0), it is possible to obtain simpler condition for balance using linearization:
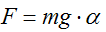
Thus process of balance maintenance of such system can be split into two main components: definition of a deviation angle of a design from balance state and management of wheels rotation depending on deviation size, for creation of force which compensates falling.
The animation below demonstrates the essence of the balance maintenance.
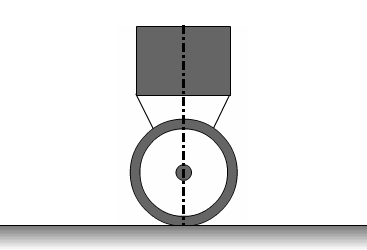
Figure 3.3 — The essence of the balance maintenance.
Using MEMS which represents combination of the accelerometer and a gyroscope for determination of deviation angle of the balancing robot will be the most correct. Task of regulation and calculations the control actions are assigned to the microcontroller, and control law is realized programmatically. Control of DC-motors is implemented using the pulse-width modulation (PWM).
System output is deviation angle of a pendulum from a normal to surface which is measured by the accelerometer and a gyroscope. Signals from MEMS are passed through system of complementary filters which is represented in figure 3.4. The difference of master control (0 degrees) and the current deviation angle comes to a regulator entrance (in our case to the microcontroller) that calculates control action stabilization of balancing robot.
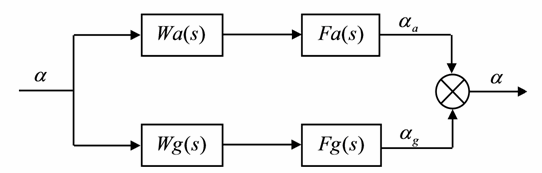
Figure 3.4 — System of complementary filters
where Wa(s) — transfer function of the accelerometer; Wg(s) — transfer function of the gyroscope; Fa(s) — transfer function of the accelerometer filter; Fg(s) — transfer function of the gyro filter; — deviation angle that is measured.
The purpose of complementary filters is support the equality of entrance and output signals. But at low frequencies of change of a deviation angle the system prefers accelerometer indications. The reason it that when the design is in a condition close to a state of rest, it is accelerometer data that is most true, and at high frequencies – indications of a gyroscope which isn't sensitive to sharp movements of a design are more exact. Each sensor dominates
at a signal frequency at which influence of its shortcomings is minimum. This approach provides rather high precision of measurements at relative simplicity of realization. There are also alternative methods of data processing from sensors, for example using the Kalman filter.
Conclusion
1. For the most exact calculation of control actions and, therefore, smooth stabilization of a design it is necessary to consider engine model, i.e. its transfer functions during the work in different modes.
2. For processing of signals from sensors there is an opportunity to use complementary filters or Kalman filter. Further it is necessary to compare these algorithms and choose the most effective.
3. For identification of position of a robot the built-in encoders will be used.
This master's work is not completed yet. Final completion: December 2013. The full text of the work and materials on the topic can be obtained from the author or his head after this date.
List of references
- Симою М.П. Определение коэффициентов передаточных функций линеаризованных звеньев систем регулирования. Автоматика и телемеханика, 1957г., №6. С. 514-527
- Льюнг Л. Идентификация систем. Теория для пользователя: М.: Наука, 1991г., 432 с.
- Ерофеев А.А. Теория автоматического управления: Учебник для вузов. – 2-е изд., перераб. и доп. – СПб.: Политехника, 2001. – 302 с.: ил. С. 34
- Эйкхофф П. Основы идентификации систем управления. Оценивание параметров и состояния.–М.: Мир, 1975г., 687 с.
- Голиков В.В. Дипломний проект "Спроектувати систему автоматичного управління балансуючого робота з використанням МЕМ датчиків руху. Спроектувати програмну частину"
- Подлесный Н.И. Элементы систем автоматического управления и контроля / Подлесный Н. И., Рубанов В. Г. — К.: Высшая шк., 1991. — 330 с.
- Башарин А. В. Примеры расчетов автоматизированного электропривода / Башарин А. В., Голубев Ф. Н., Кепперман В. Г. — М.: Энергия, 1964. — 274 с.
- Корнилов Ю. Г. Теоретические основы автоматического регулирования / Корнилов Ю. Г. — К.: Техника, 1965. — 462 с.
- Зайцев Г. Ф. Основы автоматического управления / Зайцев Г. Ф., Костюк З. И., Чинаев П. И. / Изд. 2-е. — К.: Техника, 1977. — 472 с.
- Фритч В. Применение микропроцессоров в системах управления / Фритч В. — М.: Мир, 1984. — 464 с.
- Фридмен М. Проектирование систем с микрокомпьютерами / Фридмен М., Ивенс Л. — М.: Мир, 1986. — 405 с.