Технические науки
Автоматизированные системы управления на производстве.
В.Г. Курносов, д.т.н., В.И. Силаев, д.т.н., В.В. Синенко, к.т.н,
А.А. Винарик, инженер
ОАО «Автоматгормаш им. В.А. Антипова»
Основные направления развития работ по созданию автоматизированных систем оперативно-диспетчерского управления горным предприятием
Высокий, всевозрастающий уровень нагрузки на добычные забои, повышенные требования к скорости проведения подготовительных выработок, оснащенность современными автоматизированными техническими средствами горно-шахтного оборудования, обеспечение шахт системами приборной оценки безопасного ведения горных работ, предполагает создание автоматизированных систем сбора информации о ходе технологических процессов, представления ее в наиболее понятном виде, формализации и выдачи набора оптимальных решений для более четкой организации работ по выполнению производственных задач, повышения надежности и безопасности их ведения.
Системы управления горным производством даже на современных угледобывающих предприятиях реализуются в основном за счет создания информационных средств. Анализ показывает, что в таких системах из общего времени работы диспетчерской службы 25 % тратиться на обслуживание вышестоящих уровней, а задачи оперативного управления составляют 2-3 % от времени работы диспетчера. Кроме того, возрастает количество планово-экономических, учетно-статистических задач. Диспетчер ведет первичный учет работы всех технологических звеньев, заполняет целый ряд различных отчетных документов.
Затраты диспетчера на эти работы и получение информации в телефонном режиме составляет более 50 % его рабочего времени. Функции оперативного контроля и управления распределяются между информаторами с различных точек технологических процессов. Такая децентрализация доставки информации часто приводит к ошибкам, искажает объективность информации. Обилие информационных потоков, иерархичность их представления, требует перебора различных вариантов решения задач, их оптимизации в различных производственных ситуациях. Отсутствие однозначных объективных критериев методов их оценки, ряда субъективных факторов, зависящих от уровня осведомленности и возможности переработки информации человеком, определяет создание системы автоматизированного управления производством, эргатической (человеко-машинной) системы, с определением человека как звена в системе управления. И если на нижнем уровне его роль сводиться к выбору устовок в локальных системах, то на более высоком уровне организации управления решаются более сложные интеллектуальные задачи и роль человека функционально должна быть более широка, и принятие решения должно быть более оптимальным, тем более на высоких ступенях иерархии управления, так как от этого зависит эффект работы всего предприятия. То есть необходимо обеспечить надежность его работы в системе, минимизировать напряженность выполнения им функций. Такое разнообразие выполняемых диспетчером функций, иногда неоднозначность оценки факторов, не точная их формализация, случайность возникновения ситуаций предопределяет комплексный подход к решению задач оперативного управления производством, что невозможно без создания автоматизированной системы управления, которая бы минимизировала отрицательное влияние «человеческого фактора» на всех уровнях управления.
Анализ показывает, что такую сложную задачу необходимо решать,
разбив
на ряд последовательных задач, на ряд узлов на каждом уровне, чтобы
обеспечить максимально-необходимую пропускную способность каждого
уровня.
Поэтому, наиболее оптимальной, на наш взгляд, является структура
построения на многоуровневой, иерархически соподчиненной топологии.
Анализ указанных факторов подтверждает, что система должна быть многоуровневая. Для совершенствования системы необходима разработка оптимизационно - имитационных схем и моделей.
Как показывает практика, принятие решений в иерархической системе происходит поэтапно, что позволяет разбивать общую задачу на последовательность задач, меньшей размерности. Одной из важных задач является определение узлов на каждом уровне, чтобы обеспечить максимальную пропускную способность каждого уровня.
Определяющим критерием построения системы управления является выбор
структуры.
При нормальной работе объекта диспетчер просматривает важнейшую
информацию о процессе с целью выявления некритичных нарушений, которые
не приводят к срабатыванию аварийной сигнализации.
Если диспетчер оповещен о нарушении, он концентрирует внимание на
соответствующей проблеме. Это инициирует процедуру защит, вызов правил
диагностики для выявления причин отклонения от регламентированных
норм.
Основные требования при выборе структуры могут быть обозначены
следующими:
- возможность проводить многоэтапный процесс выбора распределенной
информационной сети;
- возможность перераспределять функции по каждому уровню;
- возможность конструирования системы поиска решений на каждом этапе.
Создаваемые системы должны решать
основные задачи:
- анализ нарушений в работе технологических объектов;
- включать элементы «советчика» диспетчера;
- обеспечивать возможность формирования управляющего воздействия на
объект и обеспечивать управление в автоматическом режиме.
Одним из требований к созданию системы является разработка совершенной
программы, позволяющей планировать прогноз событий, фиксацию скорости
изменения величин, давать возможность углубляться в процесс и
детализировать нарушение его хода.
Задачи синтеза структуры можно
разделить на несколько основных:
- синтез структуры при заданных функциях и алгоритмах функционирования
системы;
- синтез функций, алгоритмов функционирования заданной многоуровневой
информационной сети;
- синтез структуры распределенной информационной сети, включая
оптимизацию функционирования системы;
- распределение функций по узлам и выбор их состава.
При создании системы управления особую роль необходимо уделять элементам и устройствам визуализации, в том числе и хода процессов, с учетом их дешифрации и представления в удобном виде. Система должна включать создание оптимизационно-имитационных схем, указывать направление выбора стратегий поиска наиболее адекватных решений.
Одним из вариантов оптимизации решений возможно использование
экспертных оценок.
Важной задачей является автоматизация и формализация принятия решений,
требуется включение в контур АСОДУ (автоматизированной системы
оперативно-диспетчерского управления) экспертных систем, базирующихся
на знании и опыте экспертов, позволяющих выдавать советы, особенно при
возникновении нештатных ситуаций. Такие системы позволят решать задачи
по прогнозированию, диагностированию хода производства, что дает
возможность принимать более качественные решения по выбору управляющих
воздействий в реальном масштабе времени.
Пропускные способности человека, как звена управления, ограничены,
поэтому возникает необходимость строить структуру системы как
многоуровневую, установив иерархическую соподчиненность.
Принятие решений наиболее перспективно может быть основано на принципах
поэтапного хода процесса, с разбивкой процесса на задачи меньшей
размерности.
Это позволит использовать по максимуму пропускную способность
каждого
уровня.
Важным направлением эффективного решения задач оптимизации является
имитационное моделирование на таких этапах: анализ работоспособности,
анализ режимов, прогнозирование, усовершенствование, проектирование.
Важными компонентами структуры вывода информации является
«планировщик событий». Это дает возможность
работать системе в режиме напоминания диспетчеру, что на данном этапе
необходимо выполнить такую-то процедуру, это позволяет сократить
количество запросов и избежать перегрузок на оператора.
При разработке уровней управления, их пропускной способности,
необходимо учитывать возможности оператора, его функциональную
надежность с учетом вероятностной оценки риска, как звена эргатической
системы управления, для ее качественной оценки.
Таковы основные направления развития автоматизированных систем
оперативно-диспетчерского управления шахтой.
Таким образом, основной целью работ по созданию системы АСОДУ
является
создание современных средств автоматизированного управления,
диспетчеризации и мониторинга основных технологических процессов
горного производства, контроля параметров безопасного ведения горных
работ.
При этом необходимо решить следующие основные задачи:
- провести анализ специфики горного производства и разработать
структуру АСОДУ;
- разработать концепцию построения интегрированной системы обработки и
передачи информации;
- разработать принципы и методы имитационной системы моделирования
сетевых систем для определения различных вариантов АСОДУ, с оценкой их
информационных характеристик;
- разработать методы распределения информационно-вычислительных задач
управления и выбора средств их выполнения.
- разработать концепцию построения экспертной системы, методики отбора
вариантов оптимальных управленческих решений;
- провести исследования и разработать передаточную функцию звена
– человека в системе АСОДУ и определить параметры
устойчивости системы с определением ограничений.
Начиная с 70-х годов прошлого столетия на предприятиях угольной
промышленности широко внедряются средства автоматизации,
автоматизированные системы управления технологическими процессами
АСУТП, системы оперативно-диспетчерского управления СОДУ. Но их
разработки не носили системного характера, средства автоматизации
зачастую были локальными, построенными на устаревшей элементной базе,
использующие ограниченный объем информации, алгоритмы функционирования
были несовершенными. И как показал опыт эксплуатации, автоматизация
отдельных объектов и подразделений даже при достижении на них
достаточно высокой эффективности в большинстые случаев незначительно
сказывается на показателях деятельности шахты. Для достижения
оптимальных результатов необходиама разработка принципиально новой
концепции создания системы управления, охватывающей всю шахту.
Такая концепция была разработана институтом «Автоматгормаш им.
В.А. Антипова». Она предусматривает комплексную автоматизацию
шахт на базе современных информационных технологий, многофакторный
контроль хода технологических процессов, состояния оборудования,
горного массива, внутришахтной аэрологической среды и прогноз их
развития.
В концепции безопасность рассматривается не как самостоятельный,
отдельный от технологии горных работ вид деятельности, а как звено
качественной, надежно функционирующей цепочки всей шахты, в которой
опасным является весь производственный процесс на протяжении всего
времени его протекания и каждое отклонение его от штатного хода должно
немедленно устраняться.
Разнообразие структурных особенностей и производственного потенциала
шахт обуславливает необходимость открытой иерархической структуры,
модульного построения системы, а высокая динамичность, случайный
характер изменений и неопределенность горно-геологических условий и
внешней среды – ее адаптацию и необходимость прогнозирования
развития ситуаций.
Концепция реализуется в рамках создаваемой институтом модульно-адаптивной прогностической системы управления шахтой. В максимальном варианте система состоит из 22 отдельных функционально автономных, но информационно связанных модулей, одним из которых является модуль оперативно-диспетчерской службы. Система АСОДУ (автоматизированная система оперативно-диспетчерского управления) предназначена для оперативного управления шахтой на основе информации о параметрах безопасности и прогнозе появления аварийных ситуаций, ходе технологических процессов, состоянии горно-шахтного оборудования и внутришахтной среды. Эта информация отображается на экране коллективного пользования, мониторах диспетчера, руководителей шахты и руководителей технических служб и используется для принятия диспетчером и руководством шахты оптимальных управленческих решений. Структура системы АСОДУ представлена на рисунке 1.
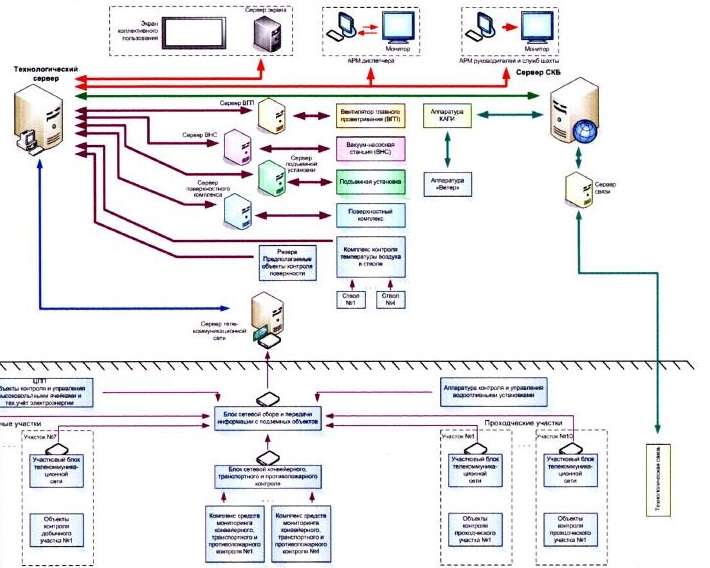
Рисунок 1 – Структура системы АСОДУ
Система АСОДУ состоит из 3-х
основных иерархических уровней:
- нижний – локальные устройства и аппараты управления;
- средний – устройства управления технологическими процессами;
- верхний – управление шахтой или объектами в целом.
Все подсистемы объединены в вычислительную сеть с формированием общей
базы данных.
Подобный подход обеспечивает оперативно-диспетчерский и
производственно-технологический персонал полной и достоверной
информацией о режимах работы технологических объектов шахты.
Контроль технологических процессов и управление всеми установками
сосредоточены в пунктах управления.
Система обеспечивает:
- измерение и оперативный контроль технологических параметров;
- регистрацию отклонений параметров от установленных границ;
- отображение состояния объектов на АРМ;
- диагностику и самодиагностику комплекса технических средств системы;
- архивацию параметров;
- печать журнала событий;
- печать архивных данных в виде таблиц и в виде трендов;
- просмотр архива в оперативном режиме реального времени в виде таблиц,
либо в виде трендов.
В системе предусмотрены функциональные, аппаратные, программные и
другие средства обеспечения живучести системы и надежности ее
функционирования при возможных отказах оборудования и ошибочных
действиях персонала. Аппаратные средства выполнены по блочно-модульному
принципу построения. Функциональная надежность обеспечена системной
организацией структуры и взаимодействием программно-технических
средств, наличием систем диагностики, простотой обслуживания и замены.
Система предназначена для непрерывной круглосуточной работы и сохраняет
работоспособность основных функций при выходе из строя отдельных
элементов и позволяет производить оперативный ремонт или замену их без
остановки.
Система выполняет следующие основные
функции:
- непрерывный циклический сбор, сохранение и преобразование в единый
формат информации от дискретных, аналоговых и контактных датчиков,
которые подключены к соответствующим входам устройства сопряжения с
объектом (УСО);
- непрерывный обмен информацией с системой комплексной безопасности и с
шахтными автоматизированными компьютерными системами;
- ручной ввод данных в сервер при недостоверности информации от
имеющихся шахтных информационных систем и датчиков для объективной
оценки ситуации;
- передачи информации в локальную сеть шахты по запросу с АРМ
пользователей;
- создание базы данных в выводом по запросу архивной информации на
внешние носители (CD-диски, флеш-память) для прогнозирования развития
аварий, расследования причин появления предаварийных и аварийных
ситуаций и их устранения;
- отображение информации о технологических параметрах, показателях
безопасности, командах управления;
- сохранение информации в базе данных сервера на протяжении не менее 90
дней.
- предусмотрена возможность корректировки конфигурации нижнего и
среднего уровней системы;
- сбор, математическая обработка и хранение данных в базе данных
сервера;
- связь системы посредством терминальных устройств ввода/вывода (АРМов)
и человеко-машинного интерфейса с эксплуатационным и административным
персоналом заказчика;
- система ведет учет времени работы оборудования добычного и
проходческого участков, транспорта, стационарного оборудования и
оборудования поверхностного комплекса;
- время простоя должно регистрироваться с указанием диспетчером причины
любого зарегистрированного простоя;
- время фактического периода работы и его завершения, время начала
простоя, его завершения и повторного начала работы регистрируются и
сохраняются в автоматическом режиме;
- автоматическое ведение системного журнала событий по следующим
параметрам:
- вход/выход из системы пользователей (оперативного персонала);
- пропадание/восстановление каналов связи;
- неисправности оборудования;
- выход контролируемых параметров за технологические границы;
- выход контролируемых параметров за аварийные границы;
- квитирование сигналов тревоги оператором;
- формирование по запросам пользователей отчетно-статистической
информации (выдача согласованных с заказчиком отчетных форм, в
соответствии с правами доступа).
На экране коллективного пользования отображается:
в базовом режиме – информация общешахтного характера с
возможностью ее детализации, план горных работ или его фрагмент с
условным обозначением необходимого или используемого оборудования,
транспорта, вентиляции, энергоснабжения и т.п.;
по запросу диспетчера:
- аэрогазовая обстановка в горных выработках с цветной индикацией
состояния атмосферы на объектах;
- схема конвейерного транспорта с конвейерами, бункерами, подъемными
установками;
- информация о работе компрессоров, водоотливов, вентиляторов главного
проветривания, очистных и проходческих забоев;
- схемы энергоснабжения с индикацией состояния объектов
(включен/отключен/авария).
Важными особенностями АСОДУ является наличие функций многофакторного
контроля состояния контролируемых объектов и процессов и
прогнозирование развития ситуаций.
Действительно, состояние сложного объекта или процесса, например,
внутришахтной атмосферы, углепородного массива, горной машины
невозможно оценить, используя только один показатель. Необходим
комплексный многофакторный контроль ряда наиболее информативных
параметров и их анализ с учетом возможной взаимозависимости.
Но при этом приходиться считаться с существенными ограничениями, связанными, во-первых, со стесненностью пространства в горных выработках и габаритами оборудования, во-вторых, с невозможностью измерения необходимых параметров, например, сопротивляемости угля резанию в процессе выемки угля. К тому же избыток информации может отрицательно влиять на ее адекватное восприятие персоналом, особенно в экстремальных ситуациях. Поэтому необходимо оптимизировать ее объем с учетом указанных ограничений и пропускной способности операторов автоматизированных объектов.
Недоступные для измерения параметры оцениваются по косвенным,
связанным
с ними, показателям. Так, сопротивляемость угля резанию – по
величине потребляемой двигателями резания комбайна мощности при данной
скорости подачи.
Получение данных об объекте контроля при появлении отказа или аварии
является запоздалым. Необходимо предотвращать эти явления. Поэтому в
некоторых системах автоматизации имеется функция
«предаварийное состояние». Но этого тоже
недостаточно, т.к. желательно иметь информацию о возможности
эксплуатации объекта в этом состоянии и в каком режиме объект можно
эксплуатировать. Радикально проблема решается при прогнозировании
развития ситуации.
Аппроксимация задачи производится в
два этапа:
- задание структуры ;
- оценка параметров.
Выбор структуры функций упрощается, если известна физика процесса. При
отсутствии такой информации функцию задают, как правило, Необходимо
найти такие значения , при которых значения хорошо приближаются к
показателям в точках наблюдения.
Результаты выполненных исследований являются теоретической основой
создания системы мониторинга и прогнозирования природных и
технологических опасностей, связанных с деятельностью шахт.
Система предназначена для автоматизированного выполнения комплекса функций повышения уровня безопасности и снижения количества аварий на шахтах, что предполагает:
- отбор, введение, обработку и представление информации о параметрах
и
режимах работы, выявление и индикацию недопустимых отклонений от
установленных значений основных технологических параметров и параметров
безопасности;
- распознавание развития аварийных (нештатных) ситуаций на начальных
стадиях с помощью технических и организационных мероприятий и
своевременное доведение информации до руководителей с целью принятия
решений по прекращению развития аварий;
- обработку информации о состоянии элементов, узлов, окружающей среды,
горного массива и других составных звеньев технологического цикла
шахты, моделирование и прогноз оптимальных руководящих решений;
-оснащение шахт созданными техническими и программными средствами
диагностики, автоматизации сбора и обработки информации;
- многоуровневое управление технологическим процессом работы шахты,
которое должно осуществляться и координироваться руководителем смены и
диспетчерскими службами по направлениям.
Учитывая наличие на многих шахтах диспетчерских пунктов устаревших
конструкций, для их радикальной модернизации на современной базе
разработан комплекс технических средств автоматизации диспетчерских
пунктов шахт, который поставляется шахтам по их индивидуальным заказам
с адаптацией программного обеспечения к конкретным условиям каждой
шахты.
Экономический эффект от использования
автоматизированного
диспетчерского пункта образуется за счет:
- оптимизации работы технологической системы шахты путем принятия
управленческих решений на основе своевременной достоверной информации,
рационального использования оборудования, существующего парка
аппаратно-технических и программных средств и улучшения
функционирования системы связи;
- повышения уровня безопасности угольного предприятия за счет получения
объективной информации о состоянии технологического оборудования, ходе
производственных процессов, параметрах безопасности, исключения влияния
«человеческого фактора»;
- уменьшения убытков от аварий и затрат на ликвидацию их последствий
путем предупреждения нарушений технологического цикла, принятия
предупредительных мер по предотвращению аварийных ситуаций, повышения
уровня оперативности и объемов информации, представляемой руководителям
шахты и горноспасательной службы о техногенных и экологических факторах.
Литература:
1. Курносов В.Г., Силаев В.И. Научные основы автоматизации в угольной
промышленности: опыт и перспективы развития: монография. –
Донецк: Изд-во «Вебер» (Донецкое отделение), 2009. –
422 с.
2. Котлярский А.И., Ревякин В.И., Жмакин Е.А., Гайдабура В.А. Система
мониторинга работы добычного участка// Уголь – 2009 - №5 –
с.20-23.
3. Комплекс технічних засобів автоматизації диспетчерського пункту
шахти. Патент України на винахід №43808. Автори: Курносов В.Г., Вінарік
А.А., Сіненко В.в. та ін. – Бюл.№16, 2009.
4. Автоматизована система протиаварійного захисту шахти. Патент України
на винахід №65121. Автори: Курносов В.Г., Сіненко В.В., Красік Я.Л. та
інші. Бюлю №8 11.06.2007.
5. Автоматизована система комплексної безпеки шахт. Патент на корисну
модель №37488. Бюл. 22 25.11.2008.