Реферат по теме выпускной работы
Содержание
- Введение
- 1. Анализ методов удаления окалины
- 1.1 Травление в растворе серной кислоты
- 1.2 Травление в растворе соляной кислоты
- 1.3 Травление в растворе азотной кислоты
- 2. Проведение испытаний на растяжение
- 2.1 Испытывание образцов полученных по технологической схеме без применения окалиноломателя
- 2.2 Испытывание образцов полученных по технологической схеме с применением окалиноломателя
- 2.3 Испытывание образцов полученных по технологической схеме предусматривающей обжатие листа в холодном состоянии
- Выводы
- Список источников
Введение
На трубном заводе «Славсант» (г. Антрацит) для производства электросварных труб в качестве заготовки используется рулонный горячекатанный тонколистовой прокат. В процессе формовки трубных заготовок вкатываемая валками в металл окалина ухудшает качество готовой продукции, условия труда и состояние инструмента. Предложено выполнить удаление окалины путем упруго-пластического изгиба штрипса. В ходе выполнения работы были проведены испытания механических свойств исходных образцов штрипса и образцов штрипса, полученного после удаления окалины путем знакопеременного упруго-пластического изгиба и после обжатия. Важно было убедиться, что прочностные и пластические свойства металла изменятся в допустимых для стабильной работы трубоэлектросварочного агрегата (ТЭСА) пределах.
1. Анализ методов удаления окалины
1.1 Травление в растворе серной кислоты
Серная кислота — сильная двухосновная кислота. Для травления используют техническую кислоту. В соответствии с ГОСТ 2184-77 техническую серную кислоту выпускают трех марок: контактную, башенную и регенерированную. Наиболее высокую концентрацию моногидрата Н2SO4 имеет контактная серная кислота, которая подразделяется на техническую, содержащую 92,5% Н2SO4, технически улучшенную (92,5—94,0%) Н2SO4, и кислоту олеум, не содержащую воды.
Особенности травления металла в растворе серной кислоты следующие. Поскольку окалина имеет множество трещин, пустот и пор, взаимодействие кислоты с её компонентами и чистой поверхностью металла начинается практически одновременно. Легче всего взаимо-действует с кислотой закись железа, а магнетит и гематит растворяются плохо. Процесс химического травления зависит в первую очередь от толщины и структуры окалины. Оптимальные условия травления создаются тогда, когда окалина содержит максимальное количество вюстита, а гематит отсутствует. По мере растворения слоя вюстита прочность сцепления окалины с основным металлом уменьшается. Под влиянием выделяющегося молекулярного водорода окалина механически отделяется от основы и оседает в виде шлама на дно ванны. Травление окалины, не содержащей вюстита, протекает очень медленно, что вызывает повышенный угар металла и образование на его поверхности раковин и пор. При этом создаются предпосылки для интенсивного проникновения водорода в сталь и, следовательно, увеличивается водородная хрупкость.
С повышением концентрации раствора серной кислоты скорость травления увеличивается, достигает максимума при её содержании в растворе 25%, а затем уменьшается таким образом, что при 50% концентрации серной кислоты время травления весьма велико. При больших концентрациях серной кислоты железо практически нерастворимо, что позволяет использовать при транспортировке и хранении концентрированной серной кислоты стальную тару. Обычно концентрация травильного раствора не превышает 20%, так как дальнейшее её увеличение приводит к дополнительным потерям металла. При травлении металла в растворе серной кислоты образуется сульфат железа FеSO4, количество которого постоянно возрастает с увеличением длительности использования ванны. С повышением концентрации сульфата железа его растворимость уменьшается и он начинает выкристаллизовываться в растворе в виде железного купороса FеSO4 • 7Н2О, осаждаясь на поверхности металла. Присутствие большого количества сульфата железа в растворе замедляет длительность травления, а выделение купороса на поверхности стали при-водит к местному недотраву. По мере накопления в ванне сернокислых солей железа состав необходимо периодически корректировать.
Атомарный водород проникает в металл и вызывает так называемую водородную хрупкость стали, определяя появление ряда характерных дефектов. Насыщение стали водородом незначительно изменяет прочностные характеристики стали, несколько увеличивая пределы прочности и текучести. Гораздо сильнее изменяются вязкие свойства С увеличением продолжительности травления в 15% -м растворе серной кислоты при температуре 70 °С резко снижаются относительное удлинение, относительное сужение площади поперечного сечения. Это означает, что по мере насыщения металла водородом повышается склонность к хрупкому разрушению.
Для предупреждения водородной хрупкости и частичного восстановления вязких свойств стали протравленный металл подвергают длительному вылеживанию или сушке при температуре 100—200°С, в процессе которой водород улетучивается. Однако происходит только частичное восстановление вязких характеристик. Таким образом, реакция взаимодействия раствора кислоты с металлом нежелательна, поскольку приводит к водородной хрупкости и вызывает необратимые потери металла. Процессу травления металла в растворе серной кислоты присущи многие существенные недостатки экономического, технологического и экологического характера, из-за которых в последнее время наметилась устойчивая тенденция к переходу на травление металла в солянокислых растворах.
1.2 Травление в растворе соляной кислоты
Соляная кислота — сильная одноосновная кислота, представляющая собой раствор хлористого водорода в воде. Основной способ получения соляной кислоты — синтез из хлора и водорода. При травлении металла используется кислота соляная синтетическая техническая (группа В) с содержанием хлористою водорода 31% но ГОСТ 857-69.
При увеличении концентрации соляной кислоты в отличие от серной скорость травления непрерывно и быстро возрастает. Наиболее выгодной концентрацией следует считать 15—20%. Травильный раствор соляной кислоты используют до содержания 1—5% свободной кислоты, при этом содержание растворенного железа должно быть не более 100 г/л.
Преимущество соляной кислоты по сравнению с серной — достаточно быстрая скорость травления уже при комнатной температуре. Скорость травления в растворе соляной кислоты больше зависит от концентрации, а в растворе серной кислоты — от температуры. При повышении температуры скорость травления в растворе соляной кислоты возрастает. Нагрев травильного раствора выше 50°С недопустим из-за интенсивного испарения вредных газов в основном виде хлористого водорода. Количество выделяющегося водорода при травлении в растворе соляной кислоты гораздо меньше, чем в растворе серной. Поэтому насыщение водородом при травлении в соляной кислоте также меньше. Например, одинаковая водородная хрупкость стали получается при травлении в 20% НСl и 5% H2SO4. Степень наводораживания металла при травлении в растворе соляной кислоты в 3—8 раз меньше, чем в растворах серной. Снижение водородной хрупкости — одно из основных преимуществ применения соляной кислоты.
Затраты на нейтрализацию отработанных солянокислых растворов меньше на 25%, а сам процесс протекает гораздо эффективнее, чем при нейтрализации сернокислых отходов. Возможна практически полная регенерация выработанных растворов соляной кислоты с созданием экологически чистого полностью замкнутого цикла. В табл. 23 приведены режимы травления металла в растворе соляной кислоты. Недостаток данной технологии — нагрев травильного раствора до 60°C, определяющий повышенную летучесть и ухудшение санитарных условий в травильном отделении. Недостатки соляной кислоты – использование специализированной тары при транспортировке и хранении, низкая рабочая концентрация при травлении, обуславливающая её большой расход и необходимость установки дополнительных емкостей для хранения.
1.3 Травление в растворе азотной кислоты
Азотная кислота — сильная одноосновная кислота, содержание которой как в жидкости, так и в парах составляет 68,4%. Современные промышленные способы получения основаны на окислении аммиака кислородом воздуха. Разбавленная азотная кислота выпускается 55, 47, 45%; концентрированная — 98 и 97%.
Однако выделяющийся при этом водород восстанавливает азотную кислоту до азотистой. При дальнейшем восстановлении азотистая кислота распадается на оксиды азота и воду В результате этого при растворении стали в азотной кислою водород не является конечным продуктом газовой среды и наводораживание металла отсутствует.
Выделяющиеся газы при травлении вредно действуют на дыхательные органы.
2. Проведение испытаний на растяжение
2.1 Испытывание образцов полученных по технологической схеме без применения окалиноломателя
Были проведены испытания на растяжения четырёх образцов стали 08кп согласно ГОСТ 11701-804. Испытывались плоские образцы (рисунок 2.1)
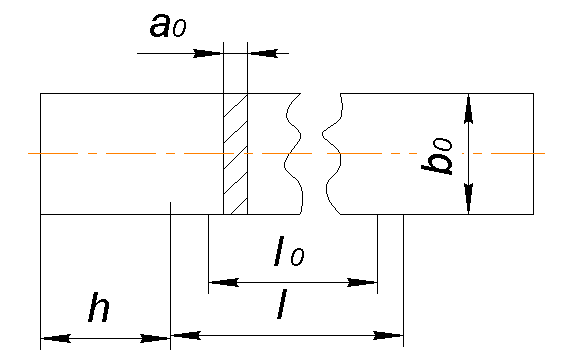
Рисунок 2.1 – Форма образцов
Испытания производились на разрывной машине Р-10 (рис. 2.2).
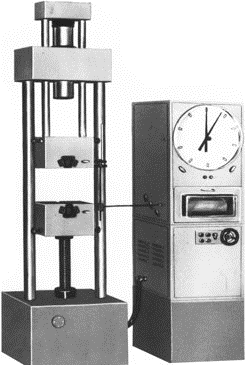
Рисунок 2.2 – Разрывная машина Р-10
Масса машины – 1260кг, максимальная нагрузка – 100 кН, силоизмеритель маятниковый, габариты (ДхШхВ) - 1300х700х2500 мм, питание – 380В. Подготовленные образцы закреплялись в захватах машины и к ним прикладывалось тянущее усилие. В момент заметного скачка усилия его значение фиксировалось (Pт). Рассчитывалось значение предела текучести
Далее фиксировалось значение усилия которое предшествует разрыву образца (Pв). Рассчитывалось значение предела прочности.
Был проведен статистический анализ полученных данных и вычислена относительная ошибка эксперимента по каждому значению.
Реузльтаты испытаний представленны на рисунке 2.3.
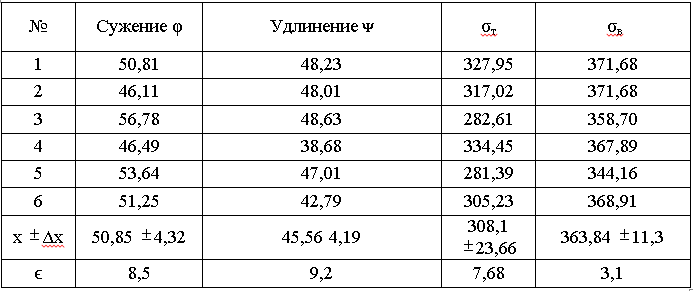
Рисунок 2.3 – Результаты испытаний на растяжение образцов из стали марки 08кп
2.2 Испытывание образцов полученных по технологической схеме с применением окалиноломателя
Испытания проводились аналогичным образом. Результаты - на рисуке 2.4.
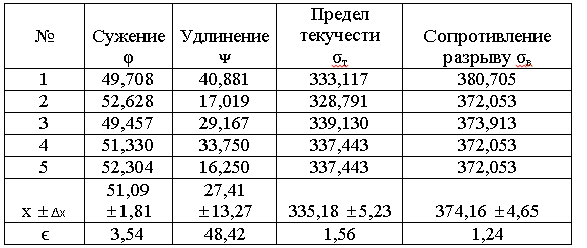
Рисунок 2.4 – Результаты исследований на растяжение образцов из стали марки 08кп после знакопеременного упруго-пластического изгиба в окалиноломателе
2.3 Испытывание образцов полученных по технологической схеме предусматривающей обжатие листа в холодном состоянии
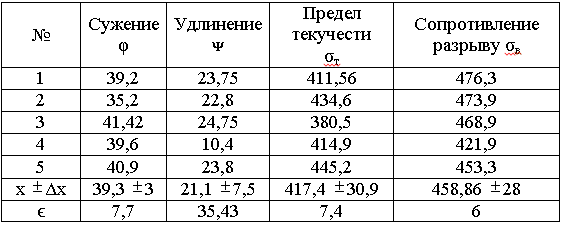
Рисунок 2.5 – Результаты исследований на растяжения образцов из стали марки 08кп после обжатия в холодном состоянии
Выводы: в результате испытаний выявлено, что после применения окалиноломателя изменение пластических и механических свойств незначительно, а после применения обжатия наблюдается падение пластических свойств, и рост механических.
Выводы
Предложенного схема удаления окалины методом знакопеременного упруго-пластического изгиба имеет практический интерес на предприятии, в ближайшее время планируется ее промышленное внедрение. Эти нововведения улучшат условия труда, качество готовой трубы. В первой части данной научно-исследовательской работы были выполнены следующие мероприятия:
- Был проведен анализ существующих методов удаления окалины, и сделан вывод, что вместо методов травления целесообразно будет использовать метод знакопеременного упруго-пластического изгиба.
- Были проведении исследования на растяжение образцов исходной заготовки, образцов, которые были подвергнуты знакопеременному упруго-пластическому изгибу, и образцов, которые были обжаты. В результате опытов выяснилось, что после знакопеременного упруго-пластического изгиба механические и пластические свойства образцов заметно не изменяются, что свидетельствует о том, что применение такого метода удаления окалины не ухудшит энергосиловые условия работы формовочного стана.
При написании данного реферата магистерская работа еще не завершена. Окончательное завершение: декабрь 2013 года. Полный текст работы и материалы по теме могут быть получены у автора или его руководителя после указанной даты.
Список источников
- Матвеев Ю.В., Ваткин Ю.А., Кричевский Ю.М. Сварные трубы. - М.: Металлургия, 1972. - 184с.
- В.М.Друян, Ю.Г.Гуляев, С.О.Чукмасов. Теорія та технологія трубного виробництва.- Дніпропетровськ: РВА “ДніпроVAL”, - 2000,- С.587.
- Технология сталепроволочного производства. Учебник для ву-зов./Ю.И.Коковихин и др.- К., 1995, - 608с.
- Виноградов А.Г. Трубное производство. - М.: Металлургия, 1981. - 344с.
- Суфьянов, Д. В. Теоретическое исследование процесса прохождения горячекатанной полосы через изгибно-растяжной окалиноломатель / Д.В. Су-фьянов, Н.Н. Огарокв, С.В. Денисов // Производство проката – 2012. - № 10. С.31-34.