Abstract
Content
1. The theoretical part
Rolling redistribution, being in the final integrated steel-making industry is a special place. It provides products rolled many of our customers at home and abroad. Hundreds of mill, mill steel plants of the country supplying the engineering industry, transport, construction and other organizations to hire thousands of sizes.
Objectives of continuous improvement of rolling production, productivity increases rolling mills, expanding the assortment, increase in the number of alloy steel and special steels, the supply of steel products on the theoretical mass, and with a quality require constant improvement of quality rolls.
The rolls of rolling mills are the working tool during the production and rolling of the basic operations - deformation (compression) of metal and give it the desired shape. In the process of deformation of the metal, rotating rolls perceived pressure during rolling, as well as a number of other pressures and impacts associated with it.
The quality of rolls very high requirements because they define the normal operation of the mill, its performance and the quality of manufactured products.
The main problem in the manufacture of rolls is the choice of optimal regimes of heat treatment. The choice depends on the mode of the rolls. Application of annealing after forging caused by the necessity of recrystallization structure wrought metal lower level of hardness and residual stress, preventing formation of hairline cracks. To obtain the fine structure and the carbide dissolution grid often used after thermal annealing rolls improvement.
Heat treatment of the rolls are quite complex and time-consuming, involve a large number of operations, different times of exposure and as a result, the whole process has a different duration. Feature of the heat treatment of large sections of workpieces is the occurrence of significant stress - thermal, structural and mechanical.
In today's industry there are a number of tasks that need to predict the structure of the steel after heat treatment. The study of structural transformations is mainly carried out by isothermal and thermokinetic diagrams. However, they are of limited use, as are valid only for the specific chemical composition of the steel. Also thermokinetic diagrams can not provide reliable information on the structure of the steel, if the cooling is different from cooling modes in the experiments. For this reason thermokinetic diagram used for quantitative evaluation of stability of the austenite under continuous cooling.
2. The purpose and objectives of the study
The purpose of this master's work is the development of laboratory methods for on the basis of the results of mathematical modeling, physical modeling of structure to carry out the roll of steel 70Х3ГНМФ 981mm diameter and 1866 mm long with samples of small cross section.
3. The practical part
Using the ANSYS program was built graph showing a change rate of the cooling roll over its cross section, after heating to the hardening temperature corresponding to 850 ° C.

Picture 1 - Cooling roll of steel 70Х3ГНМФ
According to the method proposed by Kazantsev in the reference manual for the calculation and design "Industrial Furnace" curves were characterized by different cooling rate model samples section of 20mm by changing the temperature of the environment. Discovered that cooling at 400 ° C, most closely characterizes the roll surface cooling and cooling at 500 ° C gives an idea of how the cooling will occur at a distance 80mm from the surface of the roll. These curves were plotted on the original schedule.
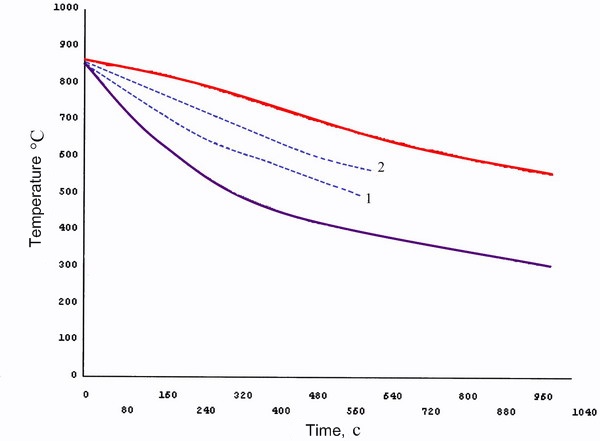
Picture 2 - Cooling roll steel 70Х3ГНМФ superimposed cooling curves of the samples (1-cooling at 400 ° C, 2 - cooling at 500 ° C)
Heat treatment was performed on samples of a given steel section 20 mm, which was in the samples were heated to 850 ° C with subsequent transfer to the furnace heated to 400 ° C and 500 ° C and there is exposure 30min. The final cooling is carried out in air.
After the heat treatment was measured and the hardness of the samples studied for their microstructure. The hardness of the sample after holding at 400 ° C was 53HRC, and after holding at 500 ° C - 54 HRC.
In the future we plan to conduct a more thorough analysis of the data and validation of the results.
Literature
- Гун Г. С. Обработка прокатных валков / Гун Г. С., Соколов В. Е., Огарков Н. Н. – Москва: Металлургия, 1983. - 112с.
- Требования к валкам широкополосных станов горячей прокатки / [утв. Сахаров О. Г.]. – Краматорск: Новокраматорский машиностроительный завод, 2000. – 17с.
- Гедеон М. В. Термическая обработка валков холодной прокатки / Гедеон М. В., Соболь Г. П., Паисов И. В. - Москва: Металлургия, 1973. - 344с.
- Медовар Л. Б. Современные валки прокатных станов. Требования, материалы и способы производства / Л. Б. Медовар, А. К. Цыкуленко, В. Е. Шевченко // Общие вопросы металлургии. – 2001. – с. 38.
- Мерзляков В. И. Обработка и ремонт прокатных валков / Мерзляков В. И. – Москва: Металлургия, 1957. – 235с.
- Горбатюк С. М. Повышение стойкости прокатных валков. / Горбатюк С. М., Седых Л. В. // Металлург. – 2010. - № 5. – с. 53-54.
- Малыхина О.Ю. Влияние основной термообработки на структуру и свойства кованой стали 150ХНМ. / Малыхина О.Ю., Титова Т.И., Шульган Н.А., Солнцев Ю.П. // Деформация и разрушение материалов. – 2006. - № 8. – с. 26-29.
- Валки листовых станов холодной прокатки / [Новиков В. Н., Белосевич В. К., Гамазков С. М., Смирнов Г. В.]. – М. : Металлургия, 1970. – 336 с.