Abstract
Maintenance
- Introduction
- 1. Relevance of the topic
- 2. Direct start
- 3. Start by switching the stator winding in star-triangle scheme
- 4. Rheostat start
- 5. Autotransformer start
- 6. Switching pairs of poles
- 7. Start with using soft starters
- 8. Frequency start
- 9. Inertial impeller
- Conclusions
- References
Introduction
First design of three-phase asynchronous motor was designed, created and tested by Russian engineer M. O. Dolivo-Dobrovolsky in 1889-1891 years. The design of asynchronous motor, proposed Dolivo-Dobrovolsky, was very successful and is the main design of these engines to date. In our time asynchronous motors (AD) are widely used in different branches of industry, households and agriculture. They are used in a variety of mechanisms: the drive of metal cutting machines, elevators, conveyors, pumps and fans. Low-powered engines are used in the automation devices and home appliances.
Wide application of induction motors due to their advantages in comparison with other engines: high reliability, easu of repair, a small number of structural elements, the ability to work directly from AC power, simplicity of service.
However, the simple design leads to difficulties when starting the motor. At the moment of start-up n=0, slide S=1. Since the current in the windings of rotor and stator depend on the slide and grow when it is increased, the starting current motor 5 ÷ 10 times its rated current.
1. The relevance of the topic
To solve the problems appearing when uncontrolled start-up of the asynchronous motor used different methods, which in varying degrees, provide for the acceleration of the asynchronous motor with a given value of the current is considerably lower than that of the direct (uncontrolled) the start [1].
This allows you to prevent premature failure of asynchronous motor and driven mechanisms, to increase the resource of switching equipment, to ensure the possibility of electric drive control with use of modern automation means.
Application of modern controlled lets start to reduce active power consumed, significantly reduce reactive power consumption, lower noise levels, to reduce vibration motor.
Ability to hold to choose correctly the trigger method asynchronous motor is included in the set of skills, which should possess the motorer-electrician. Therefore, at the Department of Electromehanical system of automation and electrical drive
in the laboratory of electric drive control systems designed stand for investigation of the schemes of the start asynchronous motor.
2. Direct start
In most cases, induction motors are connected direct to the mains supply (figure 1) . In the stator of motor circuit close contacts of the electromagnetic starter, winding are connected to the line voltage mains supply, there is a rotating electromagnetic field, and the drive starts to work. Low-power of asynchronous electric drives with a capacity of not more than 3 kW negative impact on the mains supply with direct connection is not critical. Of course, having a place throw current cannot be neglected, but even household AC power usually have some provision for capacity to withstand the torque overload.
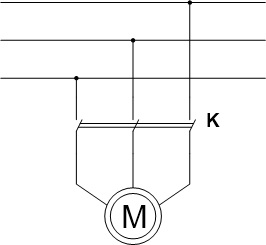
Figure 1 – Direct start asynchronous motor
As for the drive motor, in the absence of significant voltage drop it always starts without consequences. Motors of this type small and average capacity are typically designed so that when the actual connection of the stator winding to the mains supply emerging starting currents did not create excessive electrodynamic forces and excess temperature, dangerous from the point of view of mechanical and thermal strength of the machine main components. Therefore, the direct connection in the mains supply is often used asynchronous drives as small pump and fan installations, circular saws, metal-working machines [3].
In asynchronous motors ratio L/R is relatively low (particularly in small motors), so the transition process at the time of connection characterized by a very fast attenuation free current. This allows you to ignore a free current and consider only the steady-state value of the current transition process.
Acceleration is determined by the difference between the curves x M and MCT and the moment of inertia of the rotor mechanism is driven. If at the initial moment of start of MP < MCT , the motor speed will not be able.
Despite these shortcomings, starting the motor via a direct connection of the stator winding to the mains supply are widely used due to the simplicity and good technical and economic properties of motor squirrel-cage rotor - low cost and relatively high energy densities.
3. Start by switching the stator winding in star-triangle scheme
If the motor tens of kW or more, a direct connection to the mains is simply unacceptable. In this case, the inrush current should be limited, as they create unnecessary the load on the mains supply and can cause significant voltage drop, the most evident when insufficiently powerful electric networks or when powered from an independent source.
For reducing the starting current is applied, the control circuit of the electric motor is star-triangle (Fig. 2)when where it is launched from a low starting current (connection diagram star) and over time switch to normal mode (connection diagram of triangle).
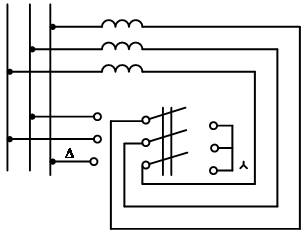
Figure 2 – Start the asynchronous motor switching stator winding star-triangle
Voltage supplied to phase stator winding, reduced 1.73 times, resulting in a reduction of phase currents 1.73 times and line currents of 3 times. At the end of the start and acceleration of the motor to the nominal frequency of stator rotation winding switch back to normal scheme.
First, when you start the motor connects in star
, and the time and the amount of current is thirds of nominal. After the specified interval, the actuator is switched off and then on again, but already under the scheme triangle
.
Start to be effective if during acceleration on a "star" of the motor will be able to develop the torque, which is required to set the speed, which is sufficient to switch on the "triangle". If this happens at a speed much slower nominal current at such a start will not be substantially different from current direct start, therefore, the use of the device makes no sense.
Addition to large variations in the current and torque, at the torque of transition motor to work on a "triangle" there are other complex transition processes. The amplitude depends on the amplitude and phase of the voltage that is generated by the motor when shifting [7].
In the worst case, the voltage can be the same as in the mains supply, but to be out of phase. Then the current will exceed the rated twice as far, according to the formula above, in four.
4. Rheostat start
This method can be applied if there is no need to develop a great starting point. Circuit stator winding for the period of start incremental active (resistors) resistance (Fig. 3). It should be noted that the resistance created by some low voltage proportional to the starting current, resulting in the stator winding is filed under voltage. This reduces the voltage drop on the specified resistance and increases automatically applied to the motor voltage. After speeding-up extension resistors closed short contactor K1.
This method start to reduce applied to the stator voltage uses liquid or metallic resistors. With proper choice of resistors such devices provide a good reduction of time and the starting current of the motor.
Exact choice of resistors should be made at the design stage, consider parameters of the motor, its modes of operation and expected load. However, such information is not always available, and when the resistors choose inaccurate, and the quality and reliability of the actuator remains low.
Feature of this scheme is that the resistance of the resistors is changing in the process of their heating. Because danger of overheating, starters with resistors are not used to work with high inertia machines and mechanisms.
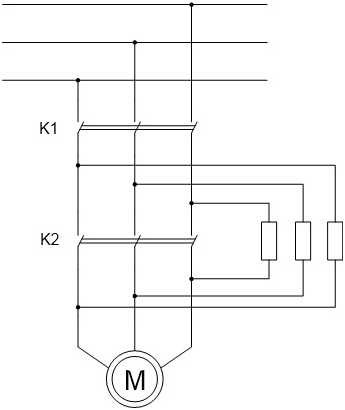
Figure 3 – Rheostat start asynchronous motor
5. Autotransformer start
With this method start the motor connects to the mains supply through the step-down transformer (Fig. 4), which can have several degrees, switchable during start corresponding equipment.
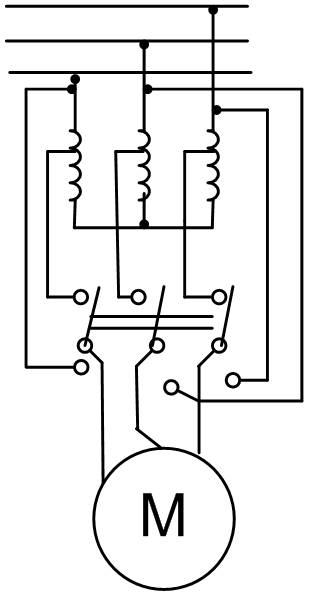
Figure 4 – Autotransformer start asynchronous motor
If this scheme is starting to reduce applied to a motor voltage is used autotransformer. For speed regulation of the inrush current and torque are special outlets. Full speed of rotation of the motor shaft is achieved until the transition to nominal voltage and surge current are thus minimised. At the same time, due to the staggered nature of regulation to achieve high precision is impossible.
Starter with autotransformer, unlike start method star/triangle is characterized by a closed transition processes. This means that the hard transients torque curves and power during acceleration of the motor is missing.
Because of the falling value voltage on the autotransformer, decreases time at any speed of the motor. With high inertia load drive starting time may exceed permissible (safe) limits and, if variable, the behavior of the system becomes optimal.
Start using autotransformer usually used when starting frequency up to 3.Times for more frequent launches asynchronous motors you want to use autotransformers considerably large size and cost, which leads to irrational use of this method.
6. Switching pairs of poles
If this starting asynchronous motor speed change is not smooth and irregular, requires a rather complicated switching device, especially when the number of speeds higher than two. When switching from one speed to another breaks the chain of stator, with the inevitable shocks of current and torque, power factor at lower speeds lower than at higher because of increased magnetic flux leakage.
Reducing torque motors with switching number of poles. When you change speed of such motors from high to low can take appropriate measures to reduce torque, because its value when switching pairs of poles greater than the starting torque. This can be achieved not only through the throttle and RTD schemes but also inexpensive way 2-phase switching (Figure 5). With this switch the motor for a certain period of time (adjustable via relays) works only between two phases of the stator windings for low speed. Because of this symmetrical (in normal mode) rotating field is distorted, and the motor creates less torque.
Best way is the use electronic devices of smooth switching number of poles WPU, electronic circuit which disables the 3rd phase when switching poles and reattach it to the desired time.
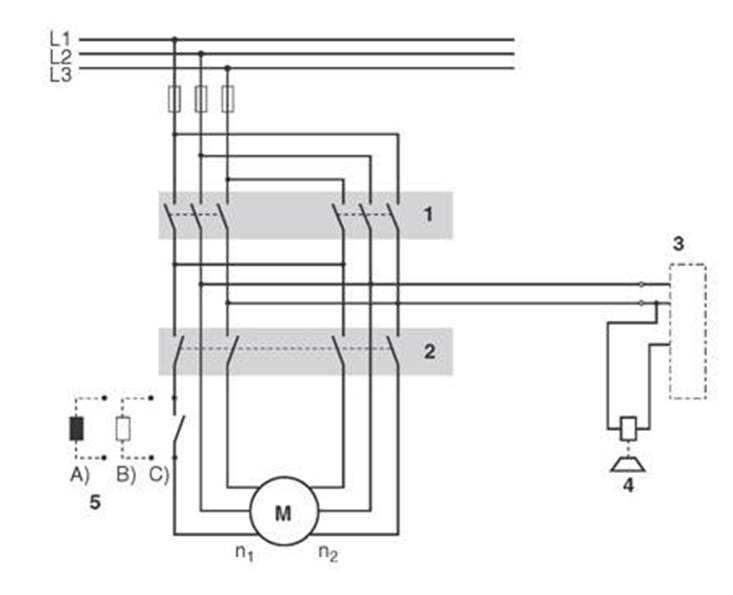
Figure 5 – Application of the device for smooth switching to the number of poles for start-up AD
To reduce the cast time when switching couples poles are used electronic devices of smooth switching number of poles type WPU.
Motor with a larger number of speeds (4 - 8), which requires increasing size and less profitable (low efficiency, significant size, the high price).
Two-speed asynchronous motors manufactured with two independent three-phase windings of the stator with different number of poles pairs, which allows speed to control rotor speed connection one of windings of three-phase mains supply. The transition from low speed to high should be made after the time delay for demagnetization of the motor, to avoid large surge of current due in opposite phase between the mains supply and the motor. Power connection diagram of two-speed motor to soft starters in figure 6, and the management on risunke.
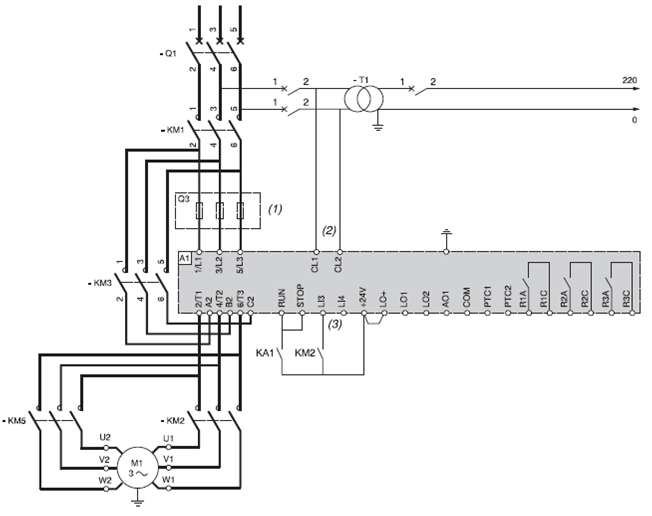
Figure 6 – Power part a
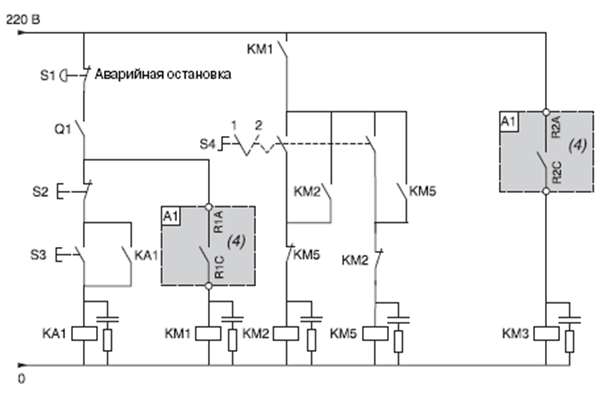
Figure 7 – The control module
In this scheme it is possible to use the motor with two independent windings. These motors two speeds and they are designed so that each winding communicates internally with different number of poles and depending on what the winding is connected to the mains supply, the motor will rotate at different speeds.
Motor with one winding connection with Dahlander shown in figure 8 and 9. These two-speed motors are designed with conventional three-phase winding, but connected inside so that according to that which external switching produced, in the motor will be switching from one to the other number of poles, but the ratio will always be 2 : 1; thus, the motor will be two different speeds, one to two times the other [11].
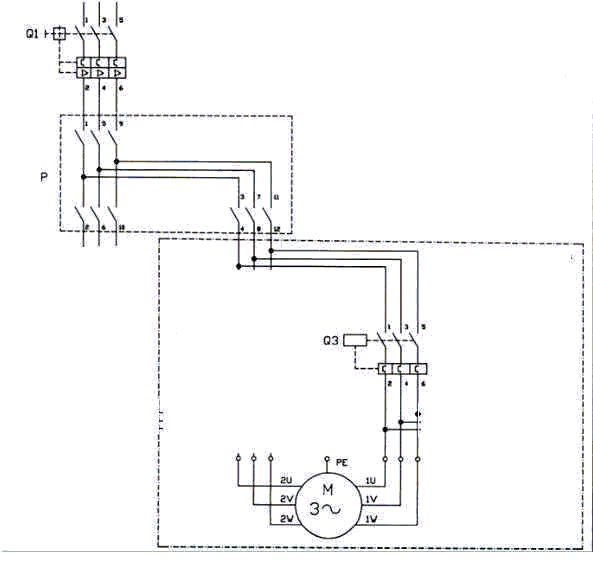
Figure 8 – Power part
(animation: 6 frames, 7 cycles, 151 KB).
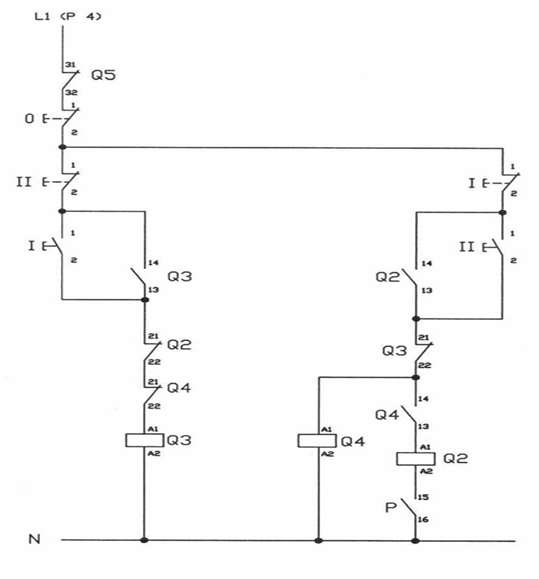
Figure 9 – Managing part a
There are also motors with winding delander and other independent coil (with this type of motor is achieved three different speeds, two winding connection delander and the third with independent winding) and motors with two windings Alanlara (with this type of motor implements the four speeds, two on each winding).
7. Start with using soft starters
Scheme of work with using soft starters can be one of four types:
- Regulators starting torque control one-phase three-phase asynchronous motor. Although this type of control and is able to control the smooth start, it does not provide the decline of the starting current, when using regulators starting torque, current to motor windings is approximately equal to the current, which is obtained by direct start.They cannot provide start of the high inertial mechanisms (due to the risk of overheating of the motor), as well as frequent starts/stops of the actuator.
- Voltage regulators without feedback can work only on strictly set by the user program. Feedback from the motor is missing, so they can't change the motor speed, adjusting it to the changing load. Otherwise they meet all the requirements that apply to the soft starter, and able to manage all phases of the motor. It is perhaps the most popular devices of smooth start. Diagram of motor start is determined by preliminary tasks starting voltage and time required to start. Many devices of this type can provide also limit the inrush current is achieved by reducing the voltage at startup. Of course, such regulation is also capable of controlling a slow mechanism, executing a smooth and continuous stooping regulators can to lower voltage in three phases, but the current is obtained unbalanced.
- Voltage regulators with feedback signal is a modernized version of the devices described above. They can read the current value of a current and voltage regulation so that the current does not exceed the user-defined framework. Also, the data obtained are used for a variety of protections (from the imbalance of the phases overload etc).This device of smooth start asynchronous motors can be grouped with other similar devices in a single system of motor control.
- Regulators current feedback signal. This is the most modern devices of smooth start. The work scheme is based on the regulation of force of a current and voltage not, as the previous model. This provides better steering precision, more simple programming and quick setup - after all most of the options here is detected automatically, without any manual input.
At the torque of start of the current flowing through the motor equal to the current case, the jammed rotor. The motor at this time accelerates, and the point in a torque becomes higher face value, after which comes to the nominal value. The nature of changes in the current and torque depends on the design and model of each particular motor.
Device for motor soft start is an electronic device that reduce the strain and inrush current by phase control. Electronic device contains the adjustment unit, where are set various operational and security settings, and the power block with a counter-parallel to the thyristors. With its help inrush current limit, as a rule, the size, in 2-3 times the rated current. Availability significant moment of inertia in the launching process can lead to the increase of heat generation in the electric motor, and thus reduce its service life [17].
At a smooth start of the motor, thyristor power block provides a feed of current non-sinusoidal form and creates a higher harmonics. Due to the very short time of acceleration/deceleration from a practical point of view (and in the norms of higher harmonics) it has no lasting negative impact on the supply chain. However, can interfere in the work of controllers. To exclude the effects of interference advisable to install interference filters at the input device of smooth start.
As shown, the device of smooth start, it is recommended to install, together with the bypass contactor to the motor during operation worked in a mode of direct connection to the supply mains. This ensures minimum wear and loss of power in the device of smooth start.
Most important element in the power part of soft starters is a classic triac (two counter-parallel thyristor with the control input)to be included in series between supply guide and motor winding. The thyristor is unlocked, provided the application of direct voltage anode-cathode and simultaneous submission of unlocking potential or his pulse on the control electrode. Locked thyristor only by the decrease in the circuit "anode-cathode-load" to a value close to zero. As part of soft starters thyristor plays the role of fast semiconductor contactor, include stress, and turn off the current [5].

Figure 10 – Connection asynchronous motor Wye
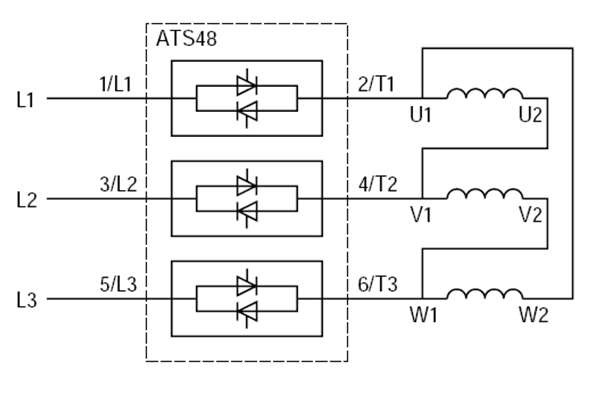
Figure 11 – Connection asynchronous motor scheme triangle
Temporary moment of locking in the transition through zero current thyristor, through which feeds winding overclocking of the motor, always lags behind the transition phase voltage sinusoid through zero due to the inductive component of soft starters contain triacs, include in one, two or all three phases and, in case of connection windings triangle, you can include triacs not in phase power, and gap winding Fig. 3 . In this case, the current through triac reduced 1.73 times and allows you to choose less powerful and cheaper soft starters, but doubles the number of necessary cables (with a valid current in the same 1.73 times below).
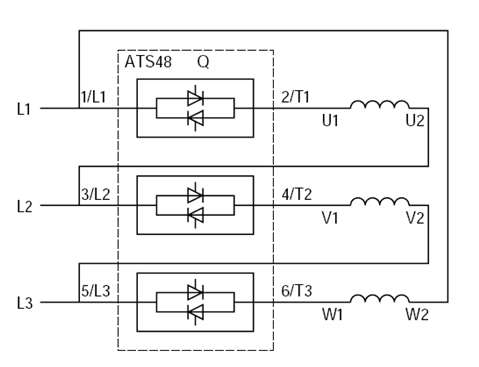
Figure 12 – the Connection of the motor winding triangle with the consistent connection of soft starters
Use of various schemes of connection to soft starters ( for example Altistart_48_ATS48D17Q ) causes the spread motor power: 3 kW at 230 V (connection supply line of the motor) to work in difficult conditions (rated current 12A) figure 8. or 15 kW at 400 V (connected in series to each winding motor (nominal current 29A) figure 9.
Scheme of work of the soft starters can be one of four types:
- stop coast;
- is not used, the function of the cascading start;
- there is no pre-heating.
the Main functions of soft starters:
- forwarding prepared configuration
- render communication parameters
- save destination configuration
- preparation and storage of the data on the hard disk
- comparison and edit the settings with the help of computer equipment
- to compare the current device configuration from a previously saved configuration
- manage installed equipment
- to structure the equipment levels (electric equipment, machines, shop)
- to store messages service
- to facilitate connection to an Ethernet mains supply by storing IP addresses
- submit classified by function device settings in illustrated diagrams or simple tables
- define a custom parameter names
- create a custom menu (selection of individual parameters)
- create a dashboard control with graphical elements (motors potentiometers, measuring instruments)
- to sort options
- to display texts in five languages (French, English, German, Spanish, Italian)
- output of the thermal condition of the motor
- output current of the motor: displays from 0 to 999 A
- output of time work
- output active power
- output torque of the motor
- output active power consumed
- output messages: starting device without a team start and no meals
- output messages: starting device without a command start-up and power
- output stages acceleration and deceleration
- output messages: work in steady mode
- this message: the braking process
- output messages: starting device in the current limitation
- this message: the time has not expired
- fix the last fault fixed device
- output phase sequence: direct or inverse
8. Frequency start
Most effective for asynchronous drive is start using a frequency converter. Changing frequency and magnitude of the supply voltage, converter enables asynchronous motor to start and run at optimal performance in any drive. It is absolutely excluded current surges and torque reaches a maximum of possible values [6].
9. Inertial impeller
For some drives (not requiring control acceleration) reduction of acceleration when starting and deceleration during braking (smooth acceleration and deceleration) is achieved by installing cast iron impeller motor (flywheel), creating additional moment of inertia. When this should be taken into account number of starts of the actuator within the hour, as when a large number of inclusions, the motor will overheat and fail.
Conclusions
Ability to carry out correctly to choose a method of start of two-speed asynchronous motor is included in the set of skills that must possess an engineer-electromechanic. Therefore, in the department of "Electromehanical system of automation and electrical drive" (EAPU) in the laboratory of electric drive control systems designed stand for research device of smooth start-based devices Altistart_48_ATS48D17Q (17A, 170-460V) Schneider Electric, Manager of the motor start ARV/2U3 power of 1.5 kW/2.2 kW (380 V, 50 Hz, 1410/2760 rpm, 3,8A/4,6A).
Developed stand is planned to use in educational process on preparation of bachelors in a direction Electromechanics
in the long term can be extended and expanded. As the nearest perspective we consider the implementation of a system logical control AD on the basis of programmable logic controller OVEN 100-24, and the development means computer registration of voltages, currents and speeds investigated asynchronous motor.
So for example through pilot plant can be set at what low voltages will start the drive belt conveyor, which is almost always forced to run in the loaded condition.
When writing this abstract master's work is not completed. Final completion: December 2014. Full text of the work and materials on the topic can be obtained from the author or his head after the specified date.
References
- Полилов Е.В., Батрак А.М., Руднев Е.С., Скорик С.П., Горелов П.В. Исследовательский стенд для апробации алгоритмов Управления сложными электромеханическими системами // Електротехн. та комп'ют. системи. - 2011. - Вип. 3. - С. 481-487. - Библиогр.: 14 назв. - рус.
- Толочко О.И., Розкаряка П.И., Горобец Н.М. К вопросу об изменении типовых структур цифровых систем управления комплектными электроприводами // Наукові праці Донецького національного технічного університету. Серія: “Електротехніка і енергетика”, випуск 10 (180). - Донецьк: ДВНЗ «ДонНТУ», 2011. – C. 188-193
- Шуйский В.П. Расчет электрических машин. Пер. с немец. –I.: Энергия, 1968, 731с.
- Толочко О.И., Коцегуб П.Х., Розкаряка П.И Реализация алгоритмов цифрового управления позиционным электроприводом постоянного тока // Вісник Кременчуцького державного політехнічного університету імені Михайла Остроградського. Вип.3(44):Ч.1 . 2007 . 178 с. : іл. - С. 18-20.
- Чиликин М.Г., Сандлер А.С. Общий курс электропривода: Учебн. для вузов. М.: Энергоиздат, 1981. – 576 с.
- Алексеев К.Б., Палагута К.А. Микроконтроллерное управление электроприводом // Учебное пособие. - М.: МГИУ, 2008. - 298 с.
- Чекавский Г.С. Конспект лекция по СУЭП, ДонНТУ, каф. ЭАПУ, 2012 г.
- Усольцев А.А. Общая электротехника // Учебное пособие. СПб.: СПбГУ ИТМО, 2009. - 301 с.
- Мощинский Ю.А., Беспалов В.Я., Кирякин А.А. Определение параметров схемы замещения асинхронной машины по каталожным данным // Ж.:
Электричество
в №4/98. 1998, c. 38–42. - Постников И.М. Обобщенная теория и переходные процессы электрических машин: Учебн. для вузов, 2–е изд., перераб. и дополн. М.: Высш.школа, 1975. – 319 с.
- Беспалов В.Я., Копылов И.П. Переходные процессы в асинхронных двигателях при несинусоидальном напряжении. Электричество,гё 8, 1971.
- Беспалов В.Я., Исследование асинхронных двигателей при несинусоидальном напряжении. Автореферат канд. дисс. М.: 1968.
- Браславский И.Я., Ишматов З.Ш., Поляков В.Н. Энергосберигающий асинхронный электропривод: Учеб. Пособие для студ. высш. учеб. Заведений /; под ред. И.Я. Браславского, – М.: Издательский центр
Академия
, 2004. – 256 с. - Мельников H.A. Реактивная мощность в электрических сетях.–М.; Энергия, 1975. 128с.
- Шевченко И.С., Морозов Д.И Электромеханические процессы в асинхронном электроприводе: Учеб. Пособие / – Алчевск: ДонДТУ, 2009, – 349 с.
- Бородина И.В., Вейнтер A.M., Серый И.М., Янко–Тринцкий A.A. Автоматический регулируемый по скорости электропривод с асинхрони–зированным синхронным двигателем. Электричество, 1975, № 7,с. 41–46.
- Пересада С.М., Ковбаса С.Н. Цифровые системы управления электроприводом [электронный ресурс] – Режим доступа:http://www.el-drives.com
- Пересада С.М., Ковбаса С.Н. Станция быстрого моделирования алгоритмов управления электроприводом [электронный ресурс] - Режим доступа:www.el-drives.com
- Веников В.А. Переходные электромеханические процессы в электрических системах. Учебн. для электроэнерг,специальн. вузов,3.е изд., перераб. и доп. М.: Высш.школа, 1978. – "415 с.
- Винаков А.Ф., Бабийчук О.Б. Однофазный реверсивный электропривод с квазичастотным управлением // Электротехника и электрооборудование. 1995.–Вып.47.– С.49–53.
- Петров Г.Н. Электрические машины. Учебн. для электроэнерг.вузов и факульт. в 3–х ч. Изд. 2–е перераб. ч.2. Асинхронные и синхронные машины. M.JI.: Госэнергоиздат, 1963, 416 с.