Abstract
The Contents
- Introduction
- 1. Theme actuality
- 2. The main aims and research problems
- 3. Analysis of the previous researches
- 4. Material and results of research
- 4.1 Short-circuited windings protection of a rotor under a thermal overload
- Conclusions
- References
Introduction
Usually at electric power plants induction motors with a short-circuited rotor and direct start-up are the main drives for mostly all mechanisms of auxiliary needs. These can be aspirators, exhauster, grinding machines, line pumps, oil pumps, condensate transfer pumps and others. Induction motors has a huge number of advantages:
- possibility of short-term mechanical overloads;
- simplicity of a design;
- simplicity of start-up and ease of its automation;
- higher power factor and efficiency, than at electric motors with a wound induction rotor.
Despite induction motors advantages damageability statistic averages to 25-35% a year from the total amount, being in operation [1,2].
Modern standards of the majority countries including Ukraine bring more and more great demands to technical exploitation of electrical installations. Requirement for continuous monitoring of expensive equipment`s work increases necessity for using of high-quality, reliable and combined protection of electric motors [4].
1. Theme actuality
Usually at electric power plants induction motors with a short-circuited rotor and direct start-up are the main drives for mostly all mechanisms of auxiliary needs. These can be aspirators, exhauster, grinding machines, line pumps, oil pumps, condensate transfer pumps and others. Damageability statistic averages to 25-35% a year from the total amount, being in operation. The purpose of improvement of relay protection and automatic equipment of motors is to minimize damageability[1,2].
The main reason of motor`s damageability is imperfection of existing relay protection and automatic devices which mostly protect electric motors very bed due abnormal modes caused by thermal overheat. Therefore development of more sophisticated protection based on microprocessor control systems is important. Also using of simulation in the MatLAB provides an opportunity to easily deploy algorithm in relay protection microprocessing terminal.
2. The main aims and research problems
This master's thesis is devoted to mathematical modeling of induction motor`s relay protection for electric power plants auxiliary. Actually have already realized in the MathCAD program thermal protection improvement for a short-circuited rotor of induction motor which is based on real-time current mode parameters control (instantaneous values of phase currents, phase voltages, zero sequence currents and heating temperature of a stator winding).
Main objectives of research:
- To develop mathematical model of induction motor in the programs MathCAD, MatLAB, then also to analyze various operating modes with heating temperature control of a rotor`s short-circuited winding of the induction motor.
- Implementation of advanced algorithms thermal protection.
- Confirmation of relay protection algorithms computation total correctness which is based on mathematical model.
3. Analysis of the previous researches
Recently much attention is paid to a development of the electronic modeling devices intended for protection of motors, working in a mode with frequent start-up and stops, with start-up and braking. Modeling devices allow to provide heating control of separate motor`s elements which at difficult working cycles heat up differently. The electronic model is thermal analogue of the motor. Such protection relay is more difficult, than the thermal relay on bimetallic elements. Range of use is limited to special electric drives. However in process of its improvement is possible to expect spread of functional area [4].
4. Material and results of research
Considerably on the motors durability is mostly influenced the state of the windings isolation aging which may be due to emergency modes. which are provided by the operating exceeding permissible temperatures. As it was spoken earlier, there is a lack of winding heating temperature measurement for a rotor caused by problem with difficulty installation of the temperature sensor. Computation of rotor temperature realizing in real time based on rotor active resistance determination and its comparison with known value of a cold state.
Calculation of temperature of a rotor is carried out in real time on the basis of determination of active resistance of a rotor and its comparison with known value of a cold state.
Calculations is based on using of electric motor equivalent circuit with two rotor contours (for the accounting of a skin-effect) and a contour of losses in stator steel (fig. 1)..[7].
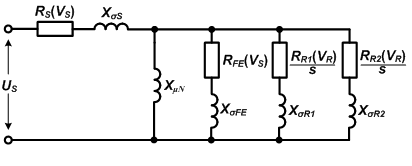
Figure 1 – Induction motor equivalent circuit with KZR with two-cages rotor and a contour of steel losses
Also was simulated starting-up mode of induction motor.
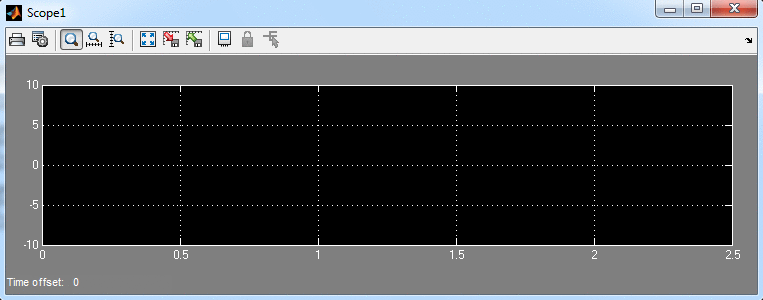
Figure 2 - Induction motor Start-up with KZR
(Анимация: 7 кадров, 4 цикла повторения, 160 килобайт)
4.1 Protection of a short-circuited rotor against a thermal overload
Adjustment process of the developed protection includes preparative operations. They are:
- realization of no-load operation and short circuit experiments, giving on a stator windings various frequency three-phase voltage at the fixed motor`s rotor, measurement of initial temperature of a cold state [8];
- definition of following resistances according to experiments data: stator windings, losses in steel, mutual induction (Xµ), resistance of two cages rotor.
For realization of thermal protection algorithm requires parameters knowledge of an induction motor equivalent circuit (fig. 1), at a known cold or initial state temperature.
The operations made in real time for one working step:
- measurement of phase currents (ia, ib, ic) and voltages(ua, ub, uc);
- calculation of sliding S based on measurement with using rotor position sensor (PS) of angle position ? for a rotor;
- measurement of heating temperature of a stator winding using PS;
- Filtration of the measured phase currents and voltages in the block of a digital filtration;
- Resulting active resistance vector calculation of a rotor sliding R_R^initial(S) which depends on the current value S.
- Determination of phase values of induction motor`s input active and inductive entrance active and inductive resistances.
- Calculation of induction motor input impedance:
- Adjustment of induction motor stator winding active resistance:
- Resistance and conductance calculation of a rotor and magnetization branch:
- Conductance calculation of a rotor:
- Induction motor`s rotor active resistance calculation for a hot state:
- Calculation of the current value of induction motor`s rotor heating temperature:
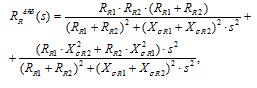
As an example of thermal protection work it was made for the electric motor of the АВ series, 630 kW and stator voltage 6 kV. Catalog data of this induction motor are presented in table 1.
Table 1 – Catalog data for induction motor АВ series 630 kW/6 kV.
Pnom,kW | Unom,kV | Inom,kА |
630 | 6 | 92 |
η | Snom | cosφ nom |
0,92 | 0,01 | 0,87 |
TS/Tnom | Tmax/Tnom | IS/Inom |
1,5 | 2,5 | 5 |
The result of parameters calculation of an equivalent circuit for the induction electric motor with two cages rotor and a losses in steel branch is presented in the table 2 [6].
Table 2 – Parameters of the double-circuit equivalent circuits with a contour losses in steel of a stator induction motor АВ series, 630 kW / 6 kV.
Rs,о.е. | Xσs,о.е. | Iном,кА |
0,01 | 0,091 | 2,73 |
RFE,о.е. | XσFE ,о.е. | RR1,о.е. |
0,012 | 0,153 | 0,012 |
XσR1 ,о.е. | RR2,о.е. | XσR2 ,о.е. |
0,153 | 0,165 | 0,112 |
Results of set mode simulating are shown in fig. 3. Dependences of stator phase A current and heating temperature a winding of a rotor on time.
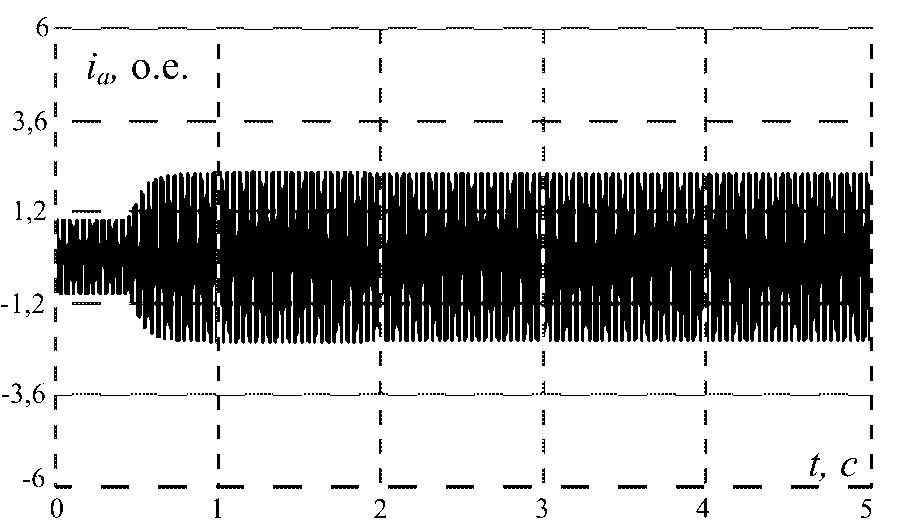
Figure 3 - - Dependences of stator phase A current on time
Conclusions
Improvement of protection algorithms against thermal stator windings overloads and short-circuited rotor overloads of the induction motor based on indirect determination of rotor winding heating temperature was carried out.
Computing of heating temperature is made at rate of real time by using rotor active resistance calculations and its comparison with known value in a cold state. The considered algorithm is realized in the form of mathematical model in MathCad and MatLAB.
At the moment the master's thesis is not yet complete. Dead line: January, 2015. The full thesis and all research materials can be received at the author or his chief after the specified date.
References
1. Корогодский В.И. Релейная защита электродвигателей напряжением выше 1 кВ / С.Л. Кужеков, Л.Б. Паперно – М.: Энергоатомиздат, 1987. – 248 с.
2. Сивокобыленко В.Ф. Микропроцессорная защита от тепловой перегрузки асинхронного электродвигателя / В.Ф. Сивокобыленко, С.Н. Ткаченко // Науково-прикладний журнал “Технічна електродинаміка”. Тематичний випуск “Проблеми сучасної енергетики”. Інститут електродинаміки, Національна академія наук України. – Частина 1. – Київ, 2008. – С. 47 – 52.
3. Копылов И. П. и Клоков Б. К.. Справочник по электрическим машинам:— М.: Энергоатомиздат, 1988.—456 с: ил.
4. Мусин А. М. Аварийные режимы асинхронных электродвигателей и способы их защиты. — М.: Колос, 1979.— 112 с, ил.— (Б-чка сел. электрика).
5. Устройства для защиты асинхронных двигателей [Электронный ресурс] – Режим доступа к статье:http://dvigatel.info/news/view/8.html
6. ГОСТ 7217-87. Межгосударственный стандарт. Машины электрические вращающиеся. Двигатели асинхронные. Методы испытаний. 2003. – 38 с.
7. Зимин Е. Н. Защита асинхронных двигателей до 500 В. Изд. 2-е, переработ, и доп. М.— Л.,изд-во “Энергия”, 1967. 88 с. с черт. (Б-ка электромонтера. Вып. 209)
8. Архипцев Ю. Ф. Асинхронные электродвигатели. – М.: “Энергия”, 1975. – 96 с.