Реферат за темою випускної роботи
Зміст
- Вступ
- 1. Актуальність теми магістерської роботи
- 2. Мета і задачі дослідження
- 3. Результати літературного огляду та патентного пошуку
- 3.1 Результати літературного огляду
- 3.2 Результати патентного пошуку
- 4. Відомі конструктивні схеми зарубіжних розробників і вибір конструктивного рішення
- 5. Розробка та виготовлення фізичної моделі жолобу і видача рекомендацій при проведенні досліджень
- Висновки
- Перелік посилань
Вступ
На сьогоднішній день виплавка сталі в дугових електросталеплавильних печах через високу конкуренцію різних підприємств і країн отримує все нові методи удосконалення. Ці методи знижують витрати на виробництво сталі за допомогою зменшення часу плавки, використання різної шихти.
Одним з таких методів є заливка рідкого чавуну в ванну дугової печі. Заливка чавуну може здійснюватися зверху через відведену кришку ДСП або через спеціальне заливальне вікно в корпусі печі. Заливка рідкого чавуну через вікно печі здійснюється через спеціальний жолоб, по якому чавун потрапляє у ванну дугового печі, тим самим зменшуючи час на завантаження шихти і зменшуючи швидкість розмивання футєровки ДСП.
1. Актуальність теми магістерської роботи
Застосування в завалку електропечі рідкого чавуну проводиться за допомогою досліджуваного жолоба. Заливка рідкого чавуну в електропіч енергетично вигідно через виділення додаткової хімічної енергії, а й введення в ванну фізичного тепла. Температура рідкого чавуну перед заливкою в піч становить 1150-1350? С, при цьому його теплосодержание досягає 223-272 кВт * год / т, що забезпечує при заміні 1% брухту рідким чавуном близько 2,23-2,72 кВт * год / т додаткової енергії. Хімічні реакції окислення кремнію і марганцю при вмісті 1% рідкого чавуну в шихті додатково вносять близько 1,40 кВт * год / т. Зміст вуглецю в чавуні забезпечує надходження тепла від його окислення в кількості 0,5 кВт * год / кг. Крім того, слід враховувати енергію розчинення вуглецю, яка складає близько 0,6 кВт * год / кг. Тому сумарний внесок 1% рідкого чавуну в тепловий баланс плавки становить приблизно 4,3 кВт * год / т.
Однак, за деякими даними, незважаючи на зниження витрати енергії і скорочення тривалості плавки, при роботі на рідкому чавуні, собівартість готової сталі зростає приблизно в 1,3-1,5 рази. Варто відзначити, що в умовах дефіциту сталевого брухту і наявності надлишкової кількості передільного чавуну на металургійному комбінаті такий технологічний варіант може бути економічно доцільний навіть для виробництва сталі масового сортаменту. Разом з тим, існує оптимальне з точки зору собівартості готового напівпродукту співвідношення чавун-лом. Існують розрахункові дані, за якими для певних конкретних умов виробництва (маса плавки 165 т) економічно оптимальну кількість рідкого чавуну в шихті становить окло 30%[1].
2. Мета і задачі дослідження
Метою даного дослідження є розробка та обгрунтування раціональних параметрів пересувного жолоба для заливки чавуну в дугову електропіч
Для досягнення поставленої мети необхідно вирішити такі завдання:
- На основі порівняльного аналізу існуючих технічних рішень розробити вдосконалений жолоб для заливки чавуну.
- Розробити методику розрахунку кінематичних і енергосилових параметрів жолоба.
- Провести перевірку правильності прийнятих технічних рішень та отриманих розрахункових залежностей на фізичному аналогу жолоба.
- Видати рекомендації для промислового використання запропонованої розробки.
- Виконати оцінку техніко-економічної ефективності розроблених технічних рішень.
3. Результати літературного огляду та патентного пошуку
3.1 Результати літературного огляду
Загальносвітовий тоннаж сталі, яка виробляється в ДСП, тільки за останні 12 років зріс в 1,5 рази. Сьогодні у світі, за різними оцінками, функціонує близько 1200-1350 ДСП різної місткості. На даний момент 11 країн випускає більше 10 млн.т електросталі на рік кожна, а на сукупну частку цих держав припадає майже 70% всього виплавленого продукту. Однак, на відміну від ситуації, що склалася в конвертерному виробництві, в секторі електросталі відсутня домінування однієї країни, практично повністю визначальною приріст обсягів виробництва. Тут в групу провідних світових металургійних країн, крім «традиційних» США, Японії, Італії та Німеччини, увійшли також Індія, Туреччина, Іспанія і Мексика. Сучасні темпи приросту виплавки сталі в ДСП слід розглядати як свідчення високої конкурентоспроможності електросталеплавильного виробництва, що обумовлено науково-технічним прогресом в частині стратегії функціонування і форматів побудови відповідних виробництв.За останні три десятиліття тривалість плавки в ДСП скоротилася з 180 хв до 40-45 хв при зменшенні питомих витрат електроенергії з 630 кВт • год до 340-350 кВт • год на тонну виплавленої сталі. Годинна продуктивність печі стає основною її характеристикою і для печей вместімостью100-200 т і досягає 180-200 т / год, а потужність пічного трансформатора іноді перевищує 1 МВА / т. Розвитку процесу виплавки сталі в ДСП значною мірою посприяла концепція металургійного міні-заводу, що отримала швидке поширення з середини 1980-х років. Вдосконалення і трансформація агрегатів, що входять до складу такого сталеливарного модуля, привели до зміни технологічних функцій дугової сталеплавильної печі [2].
У зв'язку з тим, що основним способом виплавки сталі є киснєво-конвертерний, що споживає меншу кількість брухту порівняно з мартенівським, виникли передумови для більш швидкого розвитку електросталеплавильного виробництва, що працює на твердій шихті. Друга важлива причина розвитку виплавки сталі в електропечах-все зростаюча потреба в легованих сталях і чистому металі з металізованої окатишів. Розвиток електросталеплавильного способу виробництва сталі буде йти паралельно з киснево-конвертерни. На металургійних підприємствах з великим обсягом виробництва низьколегованої та трансформаторної сталей в основному застосовують дугові трифазні електропечі місткістю 50, 100 і 200 т. На спеціалізованих заводах з виробництва високоякісної та спеціальної сталей застосовують дугові електропечі місткістю 3-100 т, індукційні електропечі звичайних конструкцій і вакуумні.
Високоякісні злитки (по структурі і поверхні) отримують в вакуумних електропечах з витрачаємим електродом і в печах електрошлакового переплаву. Останнім часом для отримання сталей для атомної і ракетної техніки застосовують електронно-променеві плазмові печі. Феросплави виплавляють в дугових електропечах на спеціалізованих заводах.
Виплавка сталі в дугових електропечах заснована на тому, що електрична енергія перетворюється в теплову внаслідок електричного розряду, протікає в газовому середовищі або у вакуумі. В електричному розряді зосереджуються висока концентрація енергії і величезні потужності в невеликих обсягах металу, в результаті чого виходять високі температури і швидке розплавлення металу.
В даний час частина твердого брухту замінюють на рідкий чавун. Заливка рідкого чавуну здійснюється за допомогою знімного чи стаціонарного жолоба. Тривалість заливки чавуну визначається організаційними можливостями і зазвичай становить 15-30 хв. Чавун необхідно заливати повільно, інакше можливі бурхливе окислення вуглецю чавуну і викиди металу і шлаку з печі. Плавлення як самостійний період плавки починається після заливки рідкого чавуну. Основним завданням цього періоду є розплавлення металу і нагрівання його вище температури плавлення (лінії ликвидус) на 40-60 ° С, а також попереднє рафінування металу[3].
3.2 Результати патентного пошуку
У результаті патентного пошуку були знайдені патенти, які мають відношення до розробки прогресивних способів виплавки сталі в дугових печах.
Патент RU 2302471 C1
Винахід відноситься до чорної металургії, зокрема до способів отримання сталі в дугових електросталеплавильних печах. Спосіб включає подачу в піч металобрухту та рідкого чавуну, розплавлення, окислювальний період, випуск плавки із залишенням шлаку і частини металу в печі. Перед випуском в піч присаджують вапно в кількості 1-5% від маси завалювання. Заливку чавуну при температурі 1250-1360 ° С у кількості 40-70% від маси завалювання проводять на залишившийся в печі шлак і частину металу. Після заливки чавуну проводять завалку вапна в кількості 1-3% і металобрухту в кількості 30-60% від маси завалювання. Окислення проводять киснем з витратою 8000-12000 м3 / год до вмісту вуглецю не менше 0,10%. У ківш при випуску присаджуют кремній і марганцевмісні феросплави з розрахунку введення кремнію 0,10-0,25% і марганцю 0,40-0,50% і вапно з розрахунку 3-20 кг / т рідкої сталі. Подальше доведення стали по температурі і хімічним складом проводять на агрегаті ківш-піч. Винахід дозволяє підвищити якість сталі, скоротити тривалість плавки.
Заливка рідкого чавуну (40-70 тонн) проводилася з чавуновозного ковша за допомогою мостового крана при відкритому своду печі на залишок пічного шлаку і металу. Далі завантажували 1000-3000 кг вапна і баддею здійснювали завалку 30-60 тонн металобрухту. Робота проводилася без подальших подвалок металобрухту в піч. Окислення вуглецю проводили продувкою сталі в печі газоподібним киснем через систему газокисневих пальників з витратою 8000-12000 м3 / т. Під час окислення вуглецю температура в печі не перевищувала 1700 ° С, причому температура заливаємого чавуну змінювалася в межах 1250-1360 ° С. При досягненні необхідного змісту вуглецю, фосфору і температури проводили випуск плавки з відсічкою пічного шлаку. Перед випуском плавки в піч зверху по труботечкам завантажувалася вапно в кількості 1000-5000 кг, після чого виробляли випуск із залишенням в печі всього шлаку і 10-15 тонн металу. При виплавці сталі за заливаэмим способом скорочується тривалість плавки з 70-80 хв до 59-68 хв, електроенергії з 300-420 кВт • год / т до 290-320 кВт • год / т, електродів з 3,50-3,60 кг / т до 2,00-2,90 кг / т, зменшений вміст хрому і нікелю до 0,03%, міді до 0,04%, забрудненість сталі неметалевими включеннями (середній бал забрудненості не перевищує 0,7)[4].
Патент RU 2258084 C1
Винахід відноситься до чорної металургії, зокрема до способів виплавки сталі в дугових електросталеплавильних печах. Спосіб виплавки сталі включає завалку металобрухту та вапна. Після проплавлення металобрухту при витраті електроенергії 180-300 кВт • год / т металобрухту заливають зверху рідкий чавун при температурі 1280-1400 ° С у кількості 30-60% від маси завалювання, що містить, мас.%: (2,0-3,5 ) С, менше 0,01 Si, менше 0,015 Р, менше 0,025 S. Окислюють вуглець газоподібним киснем при температурі в печі не більше 1700 ° С. При випуску стали відсікають пічний шлак і залишають 10-15% від загальної маси рідкого металу в печі. Подають в ківш під час випуску шлакоутворюючих сумішей, що складається з вапна і плавикового шпату в співвідношенні (0,8-1,2): (0,2-0,5) з витратою 10-17 кг / т сталі, і присаживают феросплави. Спосіб дозволяє знизити витрату електроенергії і електродів при виплавці сталі, скоротити тривалість плавки, підвищити якість сталі, зменшити витрату розкислювачів і легуючих.
Для цього запропоновано спосіб виплавки сталі в дуговій електропечі, що включає завалку металобрухту та вапна, розплавлення металобрухту, заливку рідкого чавуну, окислення вуглецю газоподібним киснем, дефосфорацию, наступний випуск сталі в ківш і присадку в ківш під час випуску шлакоутворюючої суміші, що складається з вапна і плавикового шпату, причому заливають рідкий чавун у кількості 30-60% від маси завалювання, при вмісті в ньому, мас.%: вуглецю 2,0-3,5, менше 0,01 кремнію, менше 0,015 фосфору, менш 0,025 сірки, причому чавун заливають при температурі 1280-1400 ° С зверху в піч після проплавлення металобрухту при витраті електроенергії 180-300 кВт • год / т металобрухту, температуру в печі при окисленні вуглецю підтримують не більше 1700 ° С, випуск сталі в ківш проводять з отсічкою пічного шлаку із залишенням 10-15% від загальної маси рідкого металу в печі, подають в ківш під час випуску сталі шлакоутворюючих суміш при співвідношенні в ній вапна і плавикового шпату (0,8-1,2): (0,2-0,5) з витратою 10-17 кг / т сталі і присаджують феросплави[5].
Патент RU 2197535 C2
Винахід відноситься до способів отримання сталі в дугових електросталеплавильних печах. Спосіб включає завалку в піч металобрухту, заливку рідкого чавуну, розплавлення металошихти, дефосфорацию сталі шляхом присадок порцій залізної руди або агломерату в суміші з вапном, розкислення сталі і шлаку в печі, випуск сталі в ківш під пічним шлаком, присадку в ківш десульфурірующая суміші, що складається з вапна, плавикового шпату і порошку алюмінію. До складу завалювання вводять агломерат або залізну руду в кількості 30-60 кг / т сталі. Після проплавления металошихти при витраті електроенергії 220-320 кВтг / т металобрухту в піч заливають рідкий чавун при температурі не нижче 1200oС зі швидкістю заливки 6-12 т / хв, проводять окислення газоподібним киснем з витратою 1500-3000 м3 / ч. Співвідношення присаживают залізної руди або агломерату в суміші з вапном підтримують відповідно (1-2): (2,5-3,5) при їх витраті 70-110 кг / т сталі. Після чого спускають шлак через поріг робочого вікна. Співвідношення вапна, плавикового шпату і порошку алюмінію в введеної в ківш десульфуріруючої суміші підтримують відповідно (1,1-1,5): (0,3-0,5): (0,05-0,1) при витраті суміші - 14-18 кг / т сталі. Спосіб дозволяє знизити витрату електроенергії та електродів при виплавці сталі, скоротити тривалість плавки, підвищити якість сталі.
Відомі також способи заливання рідкого чавуну через жолоб фірми Пауль Вюрт
, а також в піч зверху. Однак у першому випадку потрібно дороге
переобладнання печі, причому вузьким
місцем при заливці чавуну є жолоб (як стаціонарний, так і знімний) внаслідок брикання
залишками шлаку і чавуну при заливці.
При цьому заливка чавуну повинна здійснюватися з певною підвищеною температурою, тому що незначне падіння температури може викликати замерзання заливаємого в піч
чавуну в заливальному жолобі і виході останнього з ладу з усіма аварійними наслідками. Заливка чавуну через жолоб пов'язана також з розмивом футєровки жолоба і забрудненням
стали неметалевими включеннями екзогенного характеру. Крім того, значні витрати на утримання жолоба в робочому стані.
Заливка чавуну через звід може бути організована при значно нижчій температурі, однак при температурі чавуну менш 1200oС можливо спелеутворення, в результаті якого дрібні частки графіту, осідаючи на короткій мережі дугового електросталеплавильної печі, можуть викликати коротке замикання. Невідпрацьована технологія заливки чавуну в піч зверху може викликати викиди чавуну, шлаку і сталі з печі, переливи, підвищений знос футєровки, незначний ступінь дефосфорации і десульфурації.
Бажаними технічними результатами винаходу є: зниження витрати електродів при виплавці сталі, скорочення тривалості плавки, підвищення якості сталі.
Для цього до складу завалювання вводять агломерат або залізну руду в кількості 30-60 кг / т сталі, після проплавлення металошихти при витраті електроенергії 220-320 кВтг / т металобрухту в піч заливають рідкий чавун при температурі не нижче 1200oС зі швидкістю заливки 6-12 т / хв, проводять окислення газоподібним киснем з витратою 1500-3000 м3 / ч, співвідношення присадження залізної руди або агломерату в суміші з вапном підтримують відповідно (1-2): (2,5-3,5) при їх витраті 70-110 кг / т сталі, після чого спускають шлак через поріг робочого вікна, а співвідношення вапна, плавикового шпату і порошку алюмінію в введеної в ківш десульфурірующая суміші підтримують відповідно (1,1-1,5): (0,3-0,5): (0,05-0,1) при витраті суміші - 14-18 кг / т сталі[6].
4. Відомі конструктивні схеми зарубіжних розробників і вибір конструктивного рішення
На малюнках 1 і 2 показані конструкції жолоба німецьких фірм RHI і SIEMENS VAI. Жолоб для заливання рідкого чавуну конструкції RHI поміщається на пересувний візок за допомогою мостового крана, а жолоб SIEMENS VAI закріплений на пересувному візку і не вимагає кантування, що є перевагою в порівнянні з жолобом RHI.
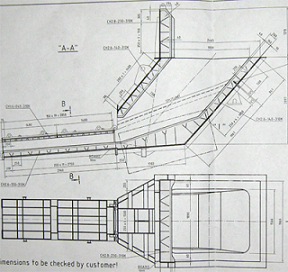
Малюнок 1 – Жолоб для заливання рідкого чавуну конструкції RHI
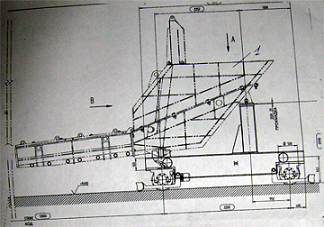
Малюнок 2 – Жолоб для заливання рідкого чавуну конструкції SIEMENS VAI
Також існує конструкція жолоба для розливання чавуну конструкції НКМЗ.
Жолоб для заливання рідкого чавуну конструкції RHI поміщається на пересувний візок за допомогою мостового крана, а жолоб SIEMENS VAI і НКМЗ закріплені на пересувному візку і не вимагають кантування, що є перевагою в порівнянні з жолобом RHI.
5. Розробка та виготовлення фізичної моделі жолобу і видача рекомендацій при проведенні досліджень
При розробці фізичної моделі за основу була взята конструкція жолоба для заливки чавуну фірми SIEMENS VAI. На даний момент сконструйована модель пересувного жолоба (мал. 3.), на який буде закріплена модель жолоба. На візку закріплений привід, що складається з електродвигуна і вручну зібраного п'ятиступінчастого редуктора.
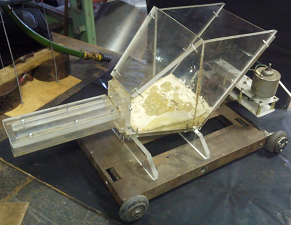
Малюнок 3 – Фізична модель пересувного жолоба
При розробці моделі жолоба був обраний масштаб 1:10. Вибираючи масштаб моделі, слід також враховувати значний вплив сил поверхневого натягу рідини на протікання процесу в моделі агрегату при занадто малих перетинах її каналів і отворів. Діаметр отворів на моделі при використанні різних моделюючих рідин повинен бути наступний: для води - не менш 12 мм, гліцерину - 10, гасу і масла - не менше 8 мм. Оскільки рідку сталь при проведенні досліду замінить вода, то діаметр випускного отвіра жолоба при вибраному масштабі відповідає умові більше 12 мм.
Матеріалом для виготовлення моделі послужить органічне скло, що володіє прозорістю і легко піддається різним видам механічної обробки, що дозволяє точно скопіювати практично будь-яку конфігурацію контурів натурного зразка досліджуваного агрегату і проводити візуальні спостереження за протікаючими в моделі гідрогазодинамічних процесами.
Для проведення досліджень процесу протікання рідкого чавуну в жолобі необхідно буде провести візуалізацію рідинного потоку. Візуалізація - це створення умов, що сприяють появі контрастною картини траекторій руху потоків моделюючої рідини за рахунок введення в неї фарбувальних рідких речовин або дрібнодисперсних твердих частинок, що мають високий коефіцієнт відбиття. Краплі кольорової рідини або ж частинки, уносимі оптично прозорими потоками, в точності відтворюють їх рух і при належній освітленності дозволяють отримати чітку картину розподілу потоків в робочому обсязі моделюючого агрегату.
Візуалізація течій вважається важливим фактором у дослідницькій роботі і, в першу чергу, у фізичному моделюванні гідродинамічних процесів, так як не тільки дозволяє зробити певні висновки щодо якісної сторони досліджуваних явищ, а й відноситься до одного з необхідних умов реалізації оптичного методу контролю часу перемішування рідини і фотометодом вимірювання швидкості рідинних потоків. Для фіксування результатів дослідження буде проведена фотозйомка. У складних умовах спеціальних видів фотозйомки гідродинамічних процесів часто потрібно розробка спеціальних пристосувань, що дозволяють реалізувати поставлене завдання в кожному конкретному випадку з найбільшою ефективністю[7].
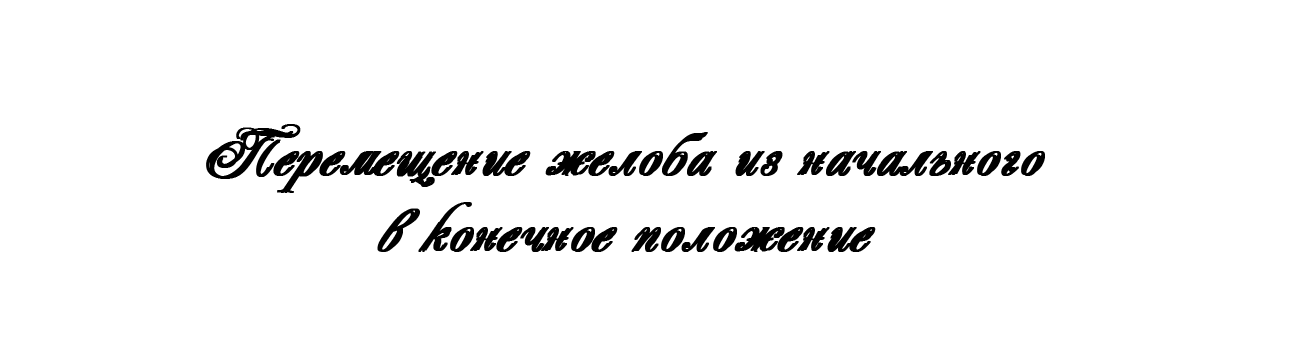
Малюнок 4 – Переміщення жолоба з початкового в кінцеве положення
(анімація: 8 кадрів, 6 циклів повторення, 165 кілобайт)
Висновки
Таким чином, розробки, спрямовані на удосконалення плавки металу в електропечах є перспективними за рахунок зниження витрат на твердий металевий лом, енергоресурси і зниження собівартості металу за допомогою заливки в піч рідкого чавуну.
Запропонований варіант жолоба є більш універсальним за рахунок конструктивних особливостей і усуненням проблем з розмиттям футєровки рідким чавуном. Дослідження дозволяють збільшити термін служби жолоба до проведення чергового ремонту.
При написанні даного реферату магістерська робота ще не завершена. Остаточне завершення: грудень 2014 року. Повний текст роботи і матеріали по темі можуть бути отримані у автора або його керівника після зазначеної дати.
Перелік посилань
- Информационный портал
Steel times
– Жидкий чугун для плавки стали в современной дуговой печи (ДСП). Режим доступа: http://steeltimes.ru/books/steelmaking/minizavod/244/244.php - Электрометаллургический прогресс/ Кукин С.В./ Металл – 2007. – № 5. – С. 15.
- Информационный портал
Specural Com
– Заливка жидкого чугуна в мартеновскую печь и плавление. Режим доступа: http://specural.com/articles/category/5/message/63/ - Патент RU 2302471 C1 Россия, C21C5/52, C21C7/06. Способ выплавки стали в дуговой электропечи / Ю.Д. Девяткин, Е.П. Кузнецов, Н.А. Козырев и др.; ОАО
Новокузнецкий металлургический комбинат
. №2006114524/02; заявлено 27.04.2006; опубл. 10.07.2007. Режим доступа: http://bd.patent.su/2302000-2302999/pat/servl/servlet65cc.html - Патент RU 2258084 C1 Россия, C21C5/52, C21C7/06. Способ выплавки стали в дуговой электропечи / Л.А. Годик, А.И. Катунин, Н.А. Козырев и др.; ОАО
Новокузнецкий металлургический комбинат
. №2003136330/02; заявлено 15.12.2003; опубл. 10.08.2005. Режим доступа: http://bd.patent.su/2258000-2258999/pat/servl/servletab79.html - Патент RU 2197535 C2 Россия, C21C5/52, C21C7/06. Способ получения стали в дуговой электросталеплавильной печи /А.И. Катунин, Л.А. Годик, Н.А. Козырев и др.; ОАО
Кузнецкий металлургический комбинат
. №2000107730/02; заявлено 29.03.2000; опубл. 27.01.2003. Режим доступа: http://bd.patent.su/2197000-2197999/pat/servl/servlet9794.html - Еронько С.П., Быковских С,В. Физическое моделирование процессов внепечной обработки и розливки стали. – К.: Техника, 1998. – 136 с.