Реферат за темою випускної роботи
Зміст
- Вступ
- 1. Актуальність теми, мета і задачі
- 2. Аналіз способів, що забезпечують задані високі якість і точність обробки поверхонь
- 2.1 Тонке точіння
- 2.2 Шліфування
- 2.3 Метод пластичної деформації
- 2.4 Висновки
- 3. Вибір найбільш раціонального способу обробки для здобуття якісних точних поверхонь по існуючим критеріям оцінки
- 3.1 Критерій «максимум продуктивності»
- 3.2 Критерій «мінімум собівартості»
- 3.3 Висновки
- Список джерел
Вступ
Розвиток машинобудування на сучасному етапі неможливий без постійного підвищення продуктивності праці і поліпшення якості виробів, що випускаються. Для вирішення цього завдання розробляються і упроваджуються різні методи обробки. У моїй роботі розглядатимуться тонке точіння, шліфування та метод пластичної деформації при обробці точних поверхонь деталі типу «Вал», виконаної з сталі 40Х.
1. Актуальність теми, мета та задачі
В даний час вимоги до якості поверхонь значно підвищились, які пов'язані з особливими вимогами експлуатації виробу. Це викликано значним кроком вперед усіх технологій обробки – з'явилися високоточні верстати і удосконалились інструменти, розробляються і упроваджуються нові методи обробки (до таких методів обробки можна віднести метод поверхневої пластичної деформації в гнучких гранульованих робочих середовищах).
Метою даної роботи є вивчення варіантів обробки точних поверхонь деталі типу «Вал».
Основним завданням є розгляд методів обробки точних поверхонь деталі «Вал» шляхом вживання тонкого точіння, шліфування і пластичної деформації і, надалі, вибір найбільш вигідного методу обробки.
2. Аналіз способів, що забезпечують задані високі якість і точність обробки поверхонь
2.1 Тонке точіння
Цей метод точіння широко застосовують в авіаційній, тракторній і автомобільній промисловостях при обробці циліндричних і конічних поверхонь (зовнішніх і внутрішніх), а також торцевих поверхонь, уступів і ін. Тонке розточування, особливо кольорових металів, по точності і чистоті поверхні перевершує розгортання і не поступається шліфуванню [3].
З причини малого перетину стружки, що знімається, невеликих сил різання і незначного нагріву заготівки виключається здобуття значного деформованого шару на обробленій поверхні. Із–за невеликих пружних деформацій технологічної системи забезпечується точність обробки по 6–8–у квалітетам, для кольорових металів і сплавів – навіть по 5–6–у квалітетам. Шорсткість обробленої поверхні заготівки зі сталі та чавуну Rа 2,5...0,63 мкм, з кольорових сплавів – Rа 0,32...0,16 мкм [5].
В якості різального інструмента для тонкого точіння застосовують:
- Різці з пластинками твердого сплаву марок ВК2 і ВК3М для тонкого обточування та розточування чавуну; Т30К4 і Т60К6 для тонкого точіння та розточування сталі, легких сплавів і кольорових металів.
- Алмазні різці – для тонкого точіння та розточування легких сплавів, кольорових металів і неметалічних матеріалів.
Величина кутів заточки різців, які оснащені пластинками твердого сплаву, які застосовуються при тонкому точінні, приведена в таблиці 2.1.
Таблица 2.1. –Кути заточки різців, які оснащені пластинами твердого сплаву, які застосовуються при тонкому точінні
Алмазні різці значно довговічніші за твердосплавні різці. Вони дозволяють працювати сотні годин без переточування і переналадки і тим самим обробляти велику кількість однакових деталей з дотриманням точності розмірів.
Алмазні різці виготовляють двох видів:
- з напайними алмазами (рис. 2.1);
- з механічним кріпленням алмазу в державці (рис. 2.2).
Для різців використовують кристали алмазів вагою 0,2–0,6 каратів (1 карат дорівнює 0,2 г).
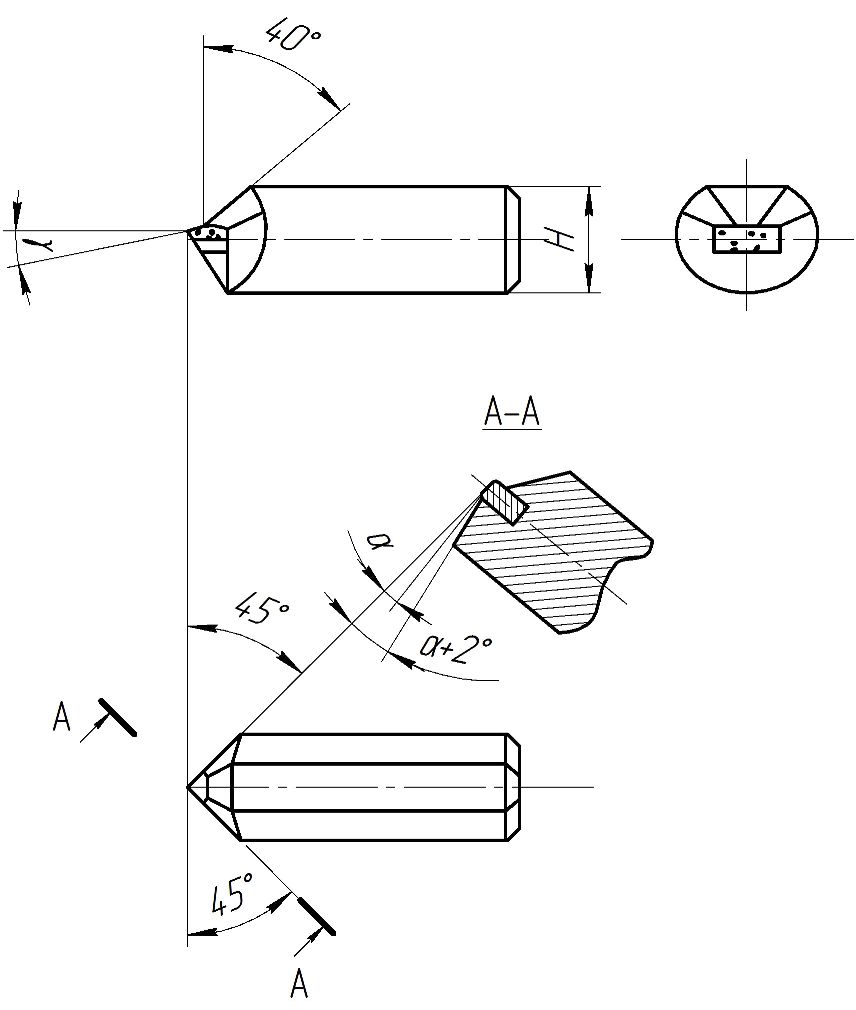
Рисунок 2.1 – Токарний різець з напайним алмазом.
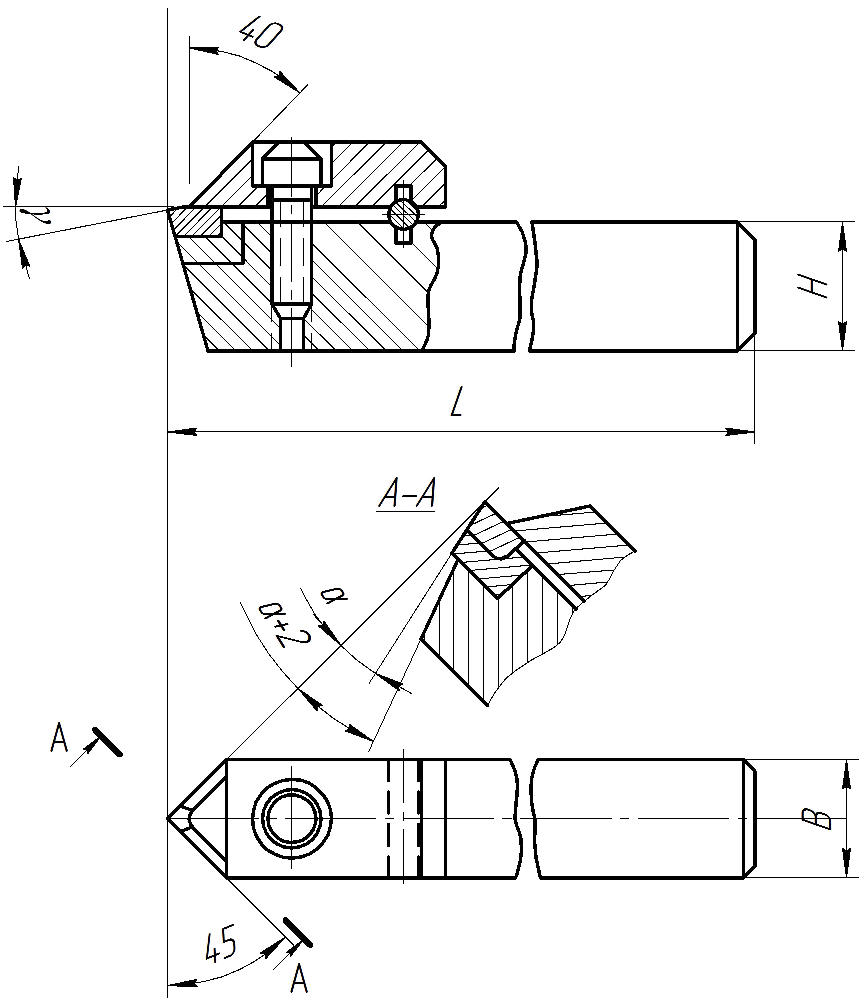
Рисунок 2.2 – Алмазний різець з механічним кріпленням алмазу.
2.2 Токарний різець з напаєнним алмазом.
Шліфування – один з видів обробки металів різанням. При шліфуванні припуск на обробку знімається абразивними інструментами – шліфувальними кругами. Шліфувальний круг являє собою пористе тіло, що складається з великої кількості дрібних зерен. Ці зерна з'єднані між собою особливою речовиною , яке називається зв'язкою. Тверді матеріали, з яких утворені зерна шліфувального круга , називаються абразивними матеріалами. Процес шліфування полягає в тому , що шліфувальний круг знімає з деталі тонкий шар металу ( стружку ) гострими гранями своїх абразивних зерен [7].
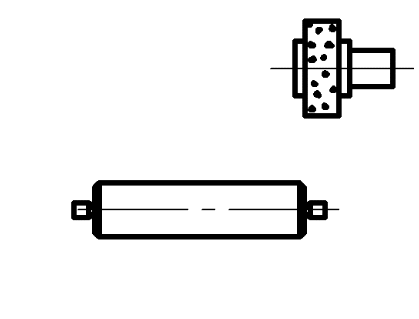
Рисунок 2.3 – Схема круглого зовнішнього шліфування.
Застосовуються операції чорнового, попереднього, остаточного та тонкого шліфування.
Чорнове шліфування передбачає обробку без попередньої токарної операції зі зніманням збільшеного припуску від 1 мм і більш на діаметр. Цю операцію доцільно виконувати на режимах силового та швидкісного шліфування при vкр=50-60 м/с. У відмінності від токарної обробки чорнове шліфування забезпечує більш високі точність обробки по 8–9–му квалітету і більш низький параметр шорсткості Ra=2,5–5,0 мкм, який не потребує наступного попереднього шліфування. Його застосування доцільно за наявності точних заготовок або заготовок, які мають погану оброблюваність лезовим інструментом.
Попереднє шліфування звичайно виконують після токарної обробки з підвищеною швидкістю різання vкр=40–60 м/с. Попереднє шліфування здійснюють до термообробки для створення базових поверхонь або у якості проміжної операції для підготовки поверхні до остаточної обробки. На операціях попереднього шліфування досягається точність за 6–9–м квалітетом та параметр шорсткості поверхні Ra=1,2–2,5 мкм.
Остаточне шліфування дозволяє отримати точність обробки за 5–6–м квалітетами і параметр шорсткості поверхні Ra=0,2–1,2 мкм. Найбільш часто застосовують швидкість різання vкр=35–40 м/с.
Тонке шліфування застосовують головним чином для отримання параметра шорсткості Ra=0,025–0,1 мкм. Воно потребує дуже доброї попередньої підготовки, так як припуск, який знімається при тонкому шліфуванні не перевищує 0,05–0,1 мм на діаметр. Застосування тонкого шліфування можливе при наявності прецизійного верстата і спеціальних кругів, воно економічно доцільно лиш в умовах одиничного та дрібносерійного виробництва. В масовому виробництві низькі параметри шорсткості поверхні більш продуктивно і надійно отримують на суперфінішніх і полірувальних верстатах [2].
2.3 Метод пластичної деформації
Поверхнево–пластична деформація (ППД) – один з найбільш простих і ефективних технологічних шляхів підвищення працездатності та надійності виробів машинобудування. В результаті ППД підвищується твердість та міцність поверхневого слою, у якому формується сприятлива залишкова напруга, зменшується параметр шорсткості Rа, збільшуються радіуси закруглення вершин нерівностей, відносна опорна довжина профілю і т.п. [1].
Пластична деформація поверхневого шару , що виникає під дією зусиль деформуючого тіла, змінює його фізико–механічні властивості і структуру. Ступінь пластичної деформації і її наслідки залежать від характеру деформації, її режиму, вихідного стану матеріалу, макро- і мікроструктури, шорсткості поверхні, форми, розмірів деталі та ряду інших чинників.
Вивчення природи і закономірностей фазових і структурних перетворень, що відбуваються в матеріалі деталі під дією ППД, є необхідною передумовою для створення нових та оптимізації існуючих технологічних процесів і обладнання. Знання цих закономірностей дозволяє розширити їх технологічні можливості і розкрити внутрішні резерви [6].
Формування поверхневого слою з заданими властивостями повинно забезпечуватись технологією зміцнення. Найбільш широко застосовують способи обкатування і розкочування шариковими та роликовими обкатниками зовнішніх та внутрішніх циліндричних, плоских та фасонних поверхонь. Циліндричні зовнішні, внутрішні, фасонні поверхні обробляються, як правило, на токарних, револьверних, свердлильних і інших верстатах; плоскі поверхні – на стругальних, фрезерних верстатах. Приклади обкатування і розкочування поверхонь роликами приведені на рис. 2.3. Звичайно цими способами обробляють достатньо жорсткі деталі зі сталі, чавуна і кольорових сплавів. На рисунку 2.3, а показана схема обробки циліндричних зовнішніх та внутрішніх поверхонь.
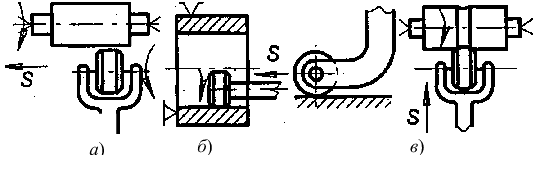
Рисунок 2.4 – Схеми обробки роликом:а – зовнішні та внутрішні циліндричні поверхні; б – плоскі поверхні; в – фасонні поверхні.
Якість оброблюваної поверхні при обкатуванні роликами та шариками в значній мірі залежить від режимів деформування: сили обкатування (або тиск на ролик і шарик), подачі, швидкості, числа робочих ходів і застосування змащувально-охолоджуючих рідин. До обкатування та розкочування заготовки обробляють точінням, шліфуванням та іншими способами, які забезпечують точність, по 7 – 9-му квалітету. Припуск на обробку звичайно рекомендується обирати рівними 0,005...0,02 мм.
Пластична поверхнева деформація може бути оздоблюючо-зміцнюючою операцією (покращує шорсткість поверхні та зміцнює поверхневий шар), оздоблюючо-зміцнюючою та калібруючою операцією (окрім сказаного вище, підвищує точність обробки); оздоблюючо-калібруючою операцією (зміцнення не відбувається).
Поряд з викладеними вище способами широко застосовують відцентрове (інерційне) зміцнення. При цьому використовується відцентрова сила кульок (роликів), що вільно сидять в радіальних отворах швидкообертаємого диска. Схема відцентрової обробки поверхні кульками показана на рис. 2.3. Шарики 2 при обертанні диска 3 зміщуються в радіальному напрямку наносячи багаточисельні удари по заготовці 1 і пластично деформуючі поверхню. Для отримання поверхонь з мінімальним параметром шорсткості та зміцненим шаром невеликої глибини застосовують алмазне вигладжування. Процес аналогічний обкатуванню, але інструментом слугує кристал алмаза, який знаходиться в спеціальній державці.
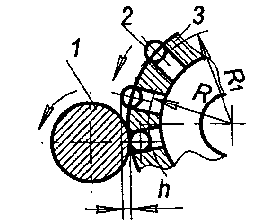
Рисунок 2.5 – Схема відцентрової обкатки.
До методів пластичного деформування, які зміцнюють поверхні деталей, відносяться: обробка дробом, гидровіброударна обробка; електромагнітне, ультразвукове зміцнення та ін.[1].
2.4 Висновки
Вище були розглянуті способи обробки, які забезпечують високі якість та точність обробляємих поверхонь. Складність явищ, супроводжуючих процеси розмірно–чистової обробки лезовим або деформуючим інструментом і різноманіття чинників, що впливають на утворення нерівностей, обумовлюють відхилення їх форм і розмірів від геометрично правильних.
3. Вибір найбільш раціонального способу обробки для здобуття якісних точних поверхонь по існуючим критеріям оцінки
Будь-який технологічний процес має бути економічним. При проектуванні технологічного процесу можуть бути встановлені такі режими різання, які дозволять отримати дуже високу продуктивність праці. При цьому стійкість інструменту буде низькою, що викличе велику витрату інструменту. Для забезпечення високої ефективності виробництва необхідно технологічні чинники процесу різання розглянути з економічної точки зору.
3.1 Критерій «максимум продуктивності»
Для забезпечення максимальної продуктивності штучний час обробки повинен бути мінімальним [4].
Для операції точіння, яке виконується за один прохід, штучний час визначається.

де TL – сумарний час простою,який приходить на одну деталь;
Т – стійкість інструменту;
s – подача;
1/n, 1/n1 – показники ступені при швидкості та подачі;
t – глубина різання;
v – швидкість різання;
l – довжина проходу інструменту;
D – діаметр заготівки;
λ=1/πD
A=K·b-1/n2
Вимогою максимальної продуктивності можливо записати наступним чином:
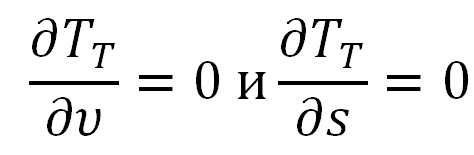
або
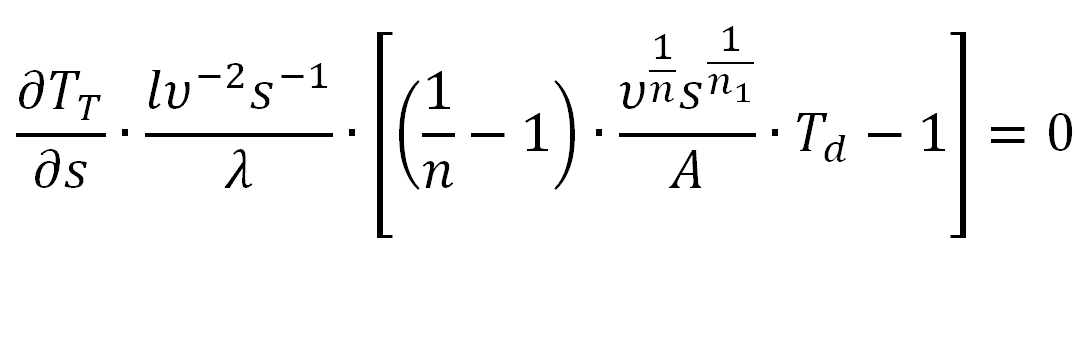


Тобто

Рівняння 1 і 2 не можуть бути справедливі одночасно і, тобто, мінімум штучного часу або максимум продуктивності не є єдиним. (рис. 3.1).
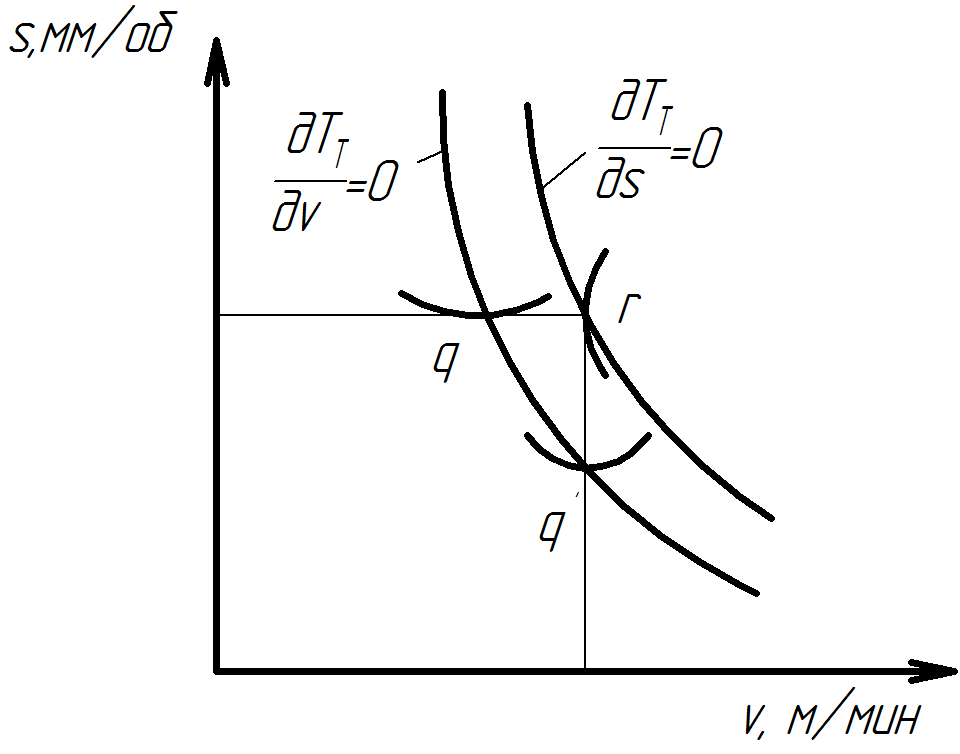
Рисунок 3.1 – Залежність подачі s від швидкості різання v для випадку максимуму продуктивності і відсутності обмежень.
Найбільша продуктивність буде досягнута при максимально допустимій подачі і відповідної швидкості різання, визначеної з рівняння 3.2.
3.2 Критерій «мінімум собівартості»
Собівартість обробки деталі складається з декількох статей. Для простоти розглянемо обробку одним інструментом.
1 Непродуктивні витрати З, що доводяться на одну деталь, включають вартість закріплення і зняття однієї деталі, вартість простою устаткування. Непродуктивні витрати підраховуються по формулі
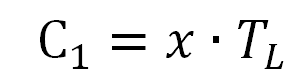
де х – вартість 1 хв;
TL – сумарний час простою, на одну деталь.
2 Вартість машинного часу обробки C2 визначається як перемноження вартості 1 хв. машинного часу х на машинний час обробки Tc

3 Вартість часу на зміну інструменту C3 визначається як відношення вартості 1 мін на час зміни інструменту, що доводяться на одну деталь
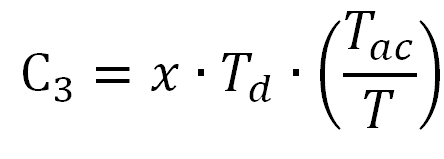
де Td – час зміни інструмента;
Tac – дійсний час обробки однієї деталі;
Т – стійкість інструмента.
4 Вартість інструменту, віднесена до однієї деталі C4, дорівнює вартості інструменту, що доводиться на ріжуче лезо у, помножене на число ріжучих лез, використовуваних при обробки даної деталі

5 Вартість інструменту, що доводиться на одне лезо, залежить від вигляду інструменту. Для напайного інструменту ця величина дорівнює:

У собівартість можуть бути включені і інші витрати, такі, як витрати на рідину, що охолоджує, на розробку інструменту, на оброблюваний матеріал, хоча перераховані витрати, окрім витрат на оброблюваний матеріал, можуть бути включені в накладні витрати. Таким чином, собівартість деталі дорівнює

де C5 – вартість матеріалу.
Виключив вартість матеріалу, маємо
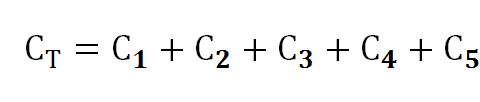
Розглядаючи рівняння 1, бачимо, що собівартість деталі може бути понижена шляхом скорочення часу закріплення і зняття деталі, часу простою і часу зміни інструменту. Для цього можуть бути використані як технічні, так і організаційні методи. Вдосконалення матеріалу інструменту і заточування підвищує стійкість інструменту, зменшує кількість змін інструменту і вартість заточування, що доводиться на одну деталь, тим самим знижуючи собівартість деталі. Знос ріжучого інструменту може бути також понижений шляхом зміни властивостей оброблюваного матеріалу. Вплив швидкості різання на собівартість деталі представлений на ріс.3.2.1,а. Зміна штучного часу (або продуктивність) залежно від швидкості різання показана на мал. 3.2.1,б [4].

Рис.3.2 – Залежність собівартості (С) та штучного часу TT обробки деталі від швидкості різання v: 1 – витрати на обробку C2, 2 – витрати на інструмент та його зміну (C3+C4), 3 – загальні витрати (собівартість) С, 4 – час на зміну інструмента (Td·Tac/Tc), 5 – повний (штучний) час, 6 – машинний час.
3.3 Висновки
При виборі найбільш економічного способу обробки, використовувались 2 критерія оцінки: «мінімум собівартості» і «максимум продуктивності». Вибір критерію залежить від заданих вимог на виробництві. На даний момент на виробництві переважно намагаються забезпечити необхідну продуктивність при мінімумі собівартості.
Список джерел
- Технология машиностроения: курс лекций / А.Г. Ткачёв, И.Н. Шубин. – Тамбов: Изд-во Тамб. гос. техн.ун-та, 2009. – 164 с. – 100 экз. – ISBN 978-5-8265-0857-2.
- Наерман М.С. Справочник молодого шлифовщика. – М.: Высш. шк., 1985. – 207 с., ил. – (Профтехобразование).
- Тонкое точение. [Электронный ресурс]. – Режим доступа:http://machinetools.aggress.ru/
- Армарего И. Дж. А., Браун Р.Х. Обработка металлов резанием. Пер. с англ. В.А. Пастунова. М., «Машиностроение», 1977. 325с.
- Точение.[Электронный ресурс]. – Режим доступа:http://dlja-mashinostroitelja...
- Бойко Н.И. Ресурсосберегающие технологии повышения качества поверхностных слоев деталей машин: Учебное пособие для вузов ж.-д. транспорта.- М.: Маршрут, 2006. – 198 с.
- Шлифование металлов. [Электронный ресурс]. – Режим доступа:http://www.markmet.ru...