Abstract
Contents
- Introduction
- 1. Mathematical description of aerogasdynamic processes
- 2. Development of algorithms for safe supervisory control ventilation excavation sites
- Conclusions
- List of sources
Introduction
Ventilation systems of a large modern mines are fairly complex sets of mountain structures and systems ensuring safe and productive work of miners. Without its effectiveness is impossible to realize the basic process of coal mining. Therefore, the ventilation system can be attributed to an important technological process of coal mines, which aims to ensure viability and comfortable working conditions for miners and the elimination of dangerous concentrations of methane in the mine atmosphere.
Task of automated ventilation control includes a number of interrelated subtasks to identify the needs in the gas flow rate factor in the area of optimal air and refinement airflow at mining sites. Thus on a methanic segment under the desired quality control processes primarily understood ensuring safe conditions – to limit the concentration of methane in the regulatory process at a safe level. Due to the fact that, in accordance with safety regulations redistribution of airflow accompanied to stop mining, the most important quality control algorithms is the minimization of time working out the required air flow rates and, consequently, decrease downtime sites.
1. Mathematical description of aerogasdynamic processes
Gasdynamic processes in the ventilation network excavation sites collieries are determined by the aggregate flow rates of gas from the satellite (Figure 1.1) , developed from the breast formation (Figure 1.2) and their interaction with the air flow in a porous medium workings and goaf [1,2]. In general, each of these elements and vent area network represent a system with distributed parameters, and unsteady gas transients in the network are described by complicated equations of motion of methane–air mixture in the partial derivatives [2]. Mathematical model of methane–air mixture motion area is the most accurate and plays a decisive role for research and establish the physical essence of non–stationary processes for gas. However, in management tasks can be used in a simple model because the cutoff frequency of methane in the lava(Figure 1.2) and recovery – satellites(Figure 1.1), which represent the main perturbations of gas in the area is extremely low and does not exceed ωmgm≈0.001s-1[3].
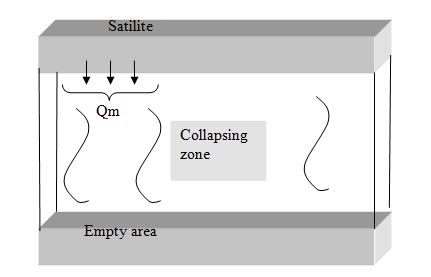
Fig. 1.1. Generalized scheme of gas movement from a satellite in goaf target formation
Qmsp – flow rate of methane destroyed part of the satellite through the zone caving goaf in lava
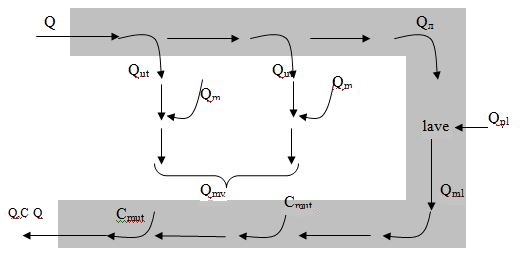
Fig. 1.2. Generalized scheme of motion–gas mixture into the workings and goaf excavation site
Q – air flow rate in the area;
C – methane concentration in the outgoing jet area;
Qut – flow rate of air leakage through the goaf;
Ql – airflow in the longwall;
Qpl – flow rate of methane in the lava from breast mined seam;
QSMEs – methane production rate of the satellite;
Cmut – concentration of methane in air leakage through the goaf;
QmV – total production rate of methane from goaf;
Qth – total flow rate of methane in the outgoing stream area.
Adjustable coordinate plot in the control loop of gas is methane concentration in the most dangerous gas mine workings area defined by safety regulations. In developing the reservoir, for example, a direct course, so is the control parameter methane concentration in the outgoing jet area (Figure 1.2). In developing the gas–dynamic model of such sites except gassing of breast slaughter and satellites should be considered in the gas content of the air leaks developed space (Figure 1.2). Therefore, in general, complete mathematical description of the site as a control object with lumped parameters should include a system of differential equations dynamic processes in mines and in the drains of the goaf.
Thus, the main problem in constructing a mathematical model of the ventilation network area as a control object on Gas is the development of the equations of gas dynamics in transient workings and goaf ventilation network site.
For a limited frequency range of external perturbations on gas can be considered [1], that the concentration of methane in all During excavation area is homogeneous, and the inertia of the gas–dynamic processes is determined mainly by the agitation speed Air and gas throughout the volume of excavation.
To describe and analyze the dynamics of management processes for use in production areas developed an approximate mathematical model [4] gassing processes of developed space and changes in the concentration of methane in the casting area:
where: Gs – setpoint flow rate of air at the site; Gin – disturbance in the air, U – air flow rate changes at the site adopted in the regulatory system as a control variable; Qm – methane production rate in the area; G – relative change in the air flow at the site; q – relative change in the flow rate of methane in the area; T – time of a single air exchange in the area; Q0, Q0m– nominal values, respectively, and discharge air flow methane; C – methane concentration in the outgoing stream area. It is obvious that q(t)≥-1.
2. Development of algorithms for safe supervisory control ventilation excavation sites
The overall objective monitoring and automated control winding sections includes a number of interrelated problems to determine the state of the ventilation system, the regulation modes of main ventilation fans, redistribution of air between the main roadways and optimization by security regimes airing mining plots [5,6,7]. When regulating stations for gas factor is assumed that the controller based on the current gas evolution determines the optimal mode of ventilation area for gas and forms corresponding to this mode, the reference (setpoint) flow and methane concentration at the inlet actuator unit (IB) of the regulator air flow which, under the control and supervision Manager fulfills the specified settlement (nominal) mode of ventilation plot. By virtue of the low–frequency spectrum of perturbations in the gas in the translation section in the desired state of perturbation gas remain quasi–stationary state and the desired design area remains unchanged in the process of dispatching management. Naturally, in order to minimize the time working out the normal mode of transfer of the section in airing new calculated state advisable to carry out the best(optimal) for speed way, and if necessary on a plot of ventilation resource restriction methane concentration at safe levels. A fragment of a possible structure of regulated areas in the shaft ventilation network shown in Figure 2.1.
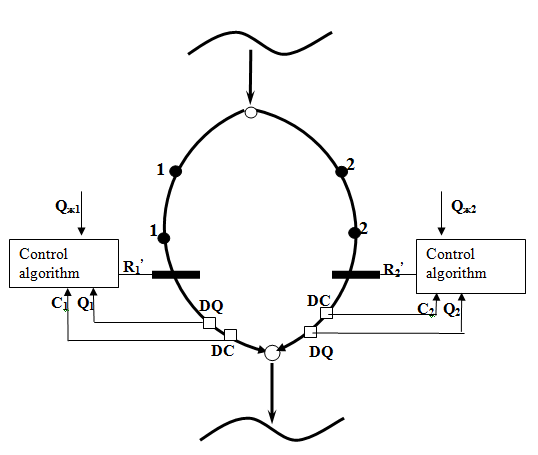
Fig.2.1. Block diagram of the controlled portions of the test fragment SHVS: Dq – air flow sensor; BO – methane concentration sensor; Qx1, Qx2 – desired air flow rate on the sites; R1', R2' – adjustable resistance area
Develop effective mining working areas on the desired flow rate of air devoted a considerable amount of work [8]. However, due to non–minimal – phase nature of the transient gas in areas (presence of "bursts" methane concentration) and substantial inertia dynamic processes to solve the safe and efficient maneuvering flow rate of air in order to establish the required level of concentration of methane in the mining sites is still far from complete.
Development of new approaches to the establishment of the desired flow rate on mining sites metanoobilnyh implemented for circuit conditions supervisory control winding sections(Fig. 2.2).
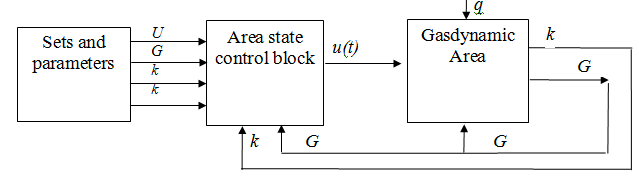
Fig.2.2. Generalized structure contour dispatching portion of gas
Conclusion
Key findings are as follows.
- Phase plane method, a new logical law in performance of the quasi–discrete control Ventilate the area when developing the desired end–state area with limited concentration of methane in the settlement an acceptable level, characterized in that the control unit influences the formation uses sliding modes.
- Shown that under certain non–standard modes of ventilation transfer area to the desired state is not feasible without exceeding the optimum concentration of methane estimated safe level.
- Methods of mathematical modeling processes at aerogazodinamicheskih dispatching safe management areas in a controlled model of a mine ventilation network with distributed parameters and the use of tools developed software support processes supervisory control airflow confirmed efficiency of the algorithm.
Further developments related to the implementation of the algorithm in a real system management control ventilation excavation sites collieries.
In writing this abstract master's work is not yet complete. Final completion: winter 2014–2015. The full text of the work and materials on the topic can be obtained from the author or his head after that date.
List of sources
- Касимов О.И. Физическая сущность и некоторые закономерности переходных газодинамических процессов на выемочных участках шахт Донбасса / О.И. Касимов, И.Н. Попов. – В кн.: Аэродинамические процессы на выемочных участках угольных шахт. – Киев: ИТТ АН УССР, 1965. – С.3–8.
- Фельдман Л.П. Уравнения неустановившегося движения метано–воздушной смеси в выработках и выработанном пространстве участка. / Л.П. Фельдман. – В кн.: Разработка месторождений полезных ископаемых. – Киев: Техника, 1971, вып.22. – С.95–105.
- Петров Н.Н. Методы синтеза систем автоматического регулирования вентиляторов главного проветривания./ Н.Н. Петров, П.Н. Ермолаев, П.Т.Пономарев. В кн. «Автоматическое управление в горном деле». Сб. научных трудов. – Новосибирск ИГД СО АН СССР, 1971. – С. 23–49.
- Чередникова О. Ю. Синтез и исследование алгоритмов оптимального по быстродействию управления. – Донецк. 2013, ст.
- Назаренко В.И. Разработка и исследование системы диспетчерского управления проветриванием шахт методами математического моделирования.: Дис. канд. техн. наук. / Назаренко Виктор Иванович. – Донецк, 1974. – 222с.
- Автоматизированная система контроля и прогнозирования состояния рудничной атмосферы угольных шахт./ Лапко В.В. и др. Наукові праці Донецького державного технічного університету. Серія: Проблеми моделювання та автоматизації проектування динамічних систем, випуск 10: – Донецьк, ДонДТУ, 1999. – С. 253 – 258.
- Аппаратно–программный комплекс автоматизации контроля состояния рудничной атмосферы / [Святный В.А., Лапко В.В., Достлев Ю.С., Краснокутский В.А., Иванов А.Ю.] // Донбасс–2020: Наука и техника – производству: матер. науч.–практ. конф., 5–6 янв. 2002г..–Донецк: ДонНТУ, 2002. – С.163–173.
- Абрамов Ф.А. Моделирование динамических процессов рудничной аэрологии / Абрамов Ф.А., Фельдман Л.П., Святный В.А. – К.: Наук. думка, 1981. – 284 с.
- Воронов А.А. Основы теории автоматического управления. Часть 2. Специальные линейные и нелинейные системы автоматического регулирования одной величины. / А.А. Воронов. – М.: Энергия, 1966. – 325с.
- Черных И.В. Simulink: Инструмент моделирования динамических систем [Electronic resource] – Access: http://www.matlab.exponenta.ru, free.