Abstract
Сontent
- Introduction
- 1. Theme urgency
- 2. Goal and tasks of the research
- 3. Brief overview Masters work
- 3. 1 Summary of the mine
- 3. 2 Analysis mine degassing network
- 3. 3 Disturbance Analysis technology of works
- 4 Analysis of the prospects for the development of the mine degassing system
- Conclusion
- References
Introduction
Increase in coal production and the rate of complications associated with mining mining – geological and mining conditions, the mining of coal seams associated with the increase of gas and gas–dynamic phenomena (GDYA) in mines. In this connection special importance is the problem of reducing the use of gas hazardous workings developed degassing of coal seams during mining operations.
1. Theme urgency
With the development of coal deposits of methane inextricably linked. During mining operations, released accumulated in the Massif methane explosion hazard in underground mines.The main sources of methane in the working areas are moonlighting coal seams and rock, which methane from the average of 75.0%–89.0% of the total flow rate on the plots. Therefore, these sources must be degassed in the first queue.
To ensure gas safety for working areas and increasing the load on the working face by GOR mine accepted standard and combined degassing, which provide satellite degassing reservoir, host rocks and goaf moving stopes.
2. Goal and tasks of the research
The purpose of this study is to increase the coefficient of degassing to ensure safe conditions of working, increasing the captured methane–air mixture. Also consider the organization in the long term development of degassing, an information field which is the analysis of the required parameters underground degasification excavation sites. The analysis and consideration, allows you to organize a comprehensive system degassing mine. A brief analysis of the program degassing wells from the surface.
Main tasks of the research:
- Analysis methods of minimization amount of states in completely and incompletely specified Moore FSM.
- Systematic analysis of operational systems and their impact on the safety of the mine.
- Checking degassing efficiency factor.
- Improving the quality of captured methane–air mixture.
- Research and development activities to improve mine degasification system taking into account the revised inventory.
- Analysis of prospects for the development of the mine degassing system.
Research object: mine "Pokrovsky" the system degassing.
Research subject: improving the degassing system and improve safety.
As part of master's thesis will receive the actual scientific results in the following areas:
- Development of recommendations for improvement of drainage system for the reduction of accidents.
- Achieving the highest economic effect of the use of methane.
3. Brief overview Masters work
During the reporting period (4 months) in 2014 produced 3 million 137 thousand tons of coal. Mining development program for 2015 is provided to achieve production at 9 million 194 thousand tons.
Over the past period in 2014 was commissioned 3 stope:
-
2th northern lava block 10
-
6th southern lava block 10
-
5th South lava block 10
3. 1 Summary of the mine
Mine Pokrovsky
(Fig. 1). fulfills the coalbed methane–d4 with 15–25 m3/t.s.b.m., the top and the soil layers which lie 5 satellites and powerful (up to 20–40 m) layers of gas–bearing sandstones. Methane sandstones is 3–4 m3 per tonne. Furthermore, methane is present in other breeds: siltstone, mudstone, and even in water in a dissolved state.
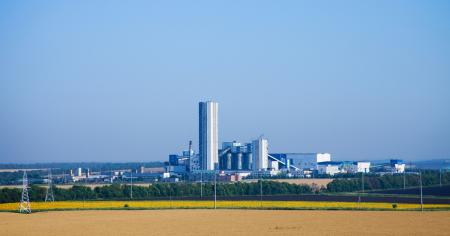
Fig. 1 – mine Pokrovsky
Number of captured methane–air mixture in 2013 amounted 197mln.m3 methane–air mixture or 32.1 million m3 in terms of 100% CH4, are disposed in 2013 in the boiler room of the mine 9.7 million m3 of pure
methane.( Fig. 2 ).
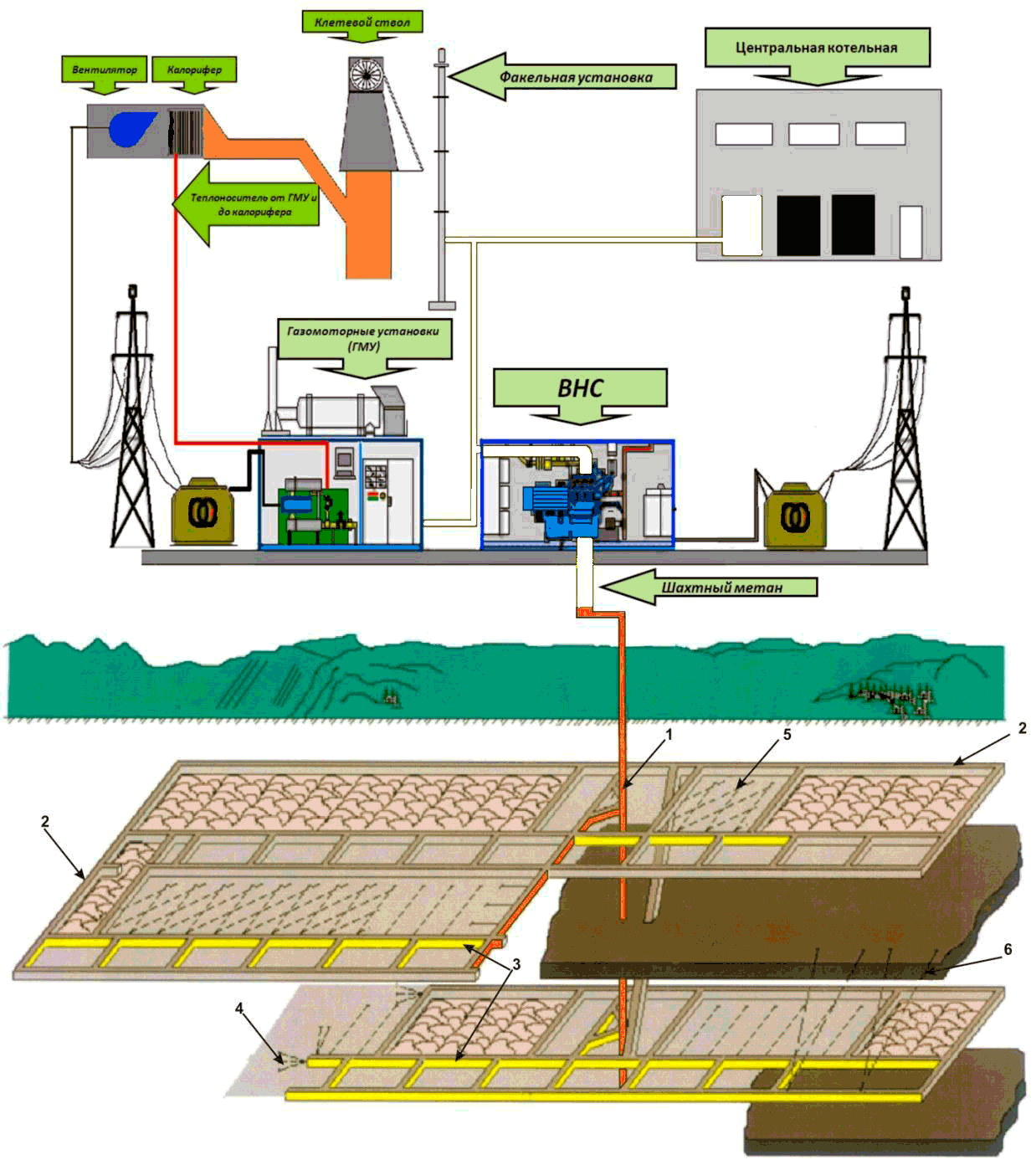
Fig. 2 – Methane recovery scheme
3. 2 Analysis mine degassing network
Mine degasification scheme is a network of pipelines located in the mines, which is roughly divided into three branches – a branch of the horizon 593 m, 708 m and horizon 815 m.
Branch horizons 593 m and 708 m outcrop main industrial area and connected to the VNS number 1, and the branch to the surface horizon 815 m industrial site AMS–2 and is connected to the VNS number 2.
Length branches 593–7500 m, presented decontamination Pipelines 426 mm 325 mm and district.
Length branches 708–10300 m, presented decontamination Pipelines 426 mm 426mm and district.
Length branches 815–9000 m, presented decontamination Pipelines 530 mm 426 mm and district.
At the moment, the average volume of captured methane facilities underground degasification 350–400 m3/min methane–air mixture or 80–95m3/min100% CH4.
Currently, there are two work surface vacuum pump stations VNS number 1 (the main industrial site) and VNS number 2 equipped with vacuum compressors VVK2–150.
The drilling of degasification wells are held at all mining sites mines, used for drilling drills GBH 1/89/12 production Deilmann–Haniel mining systems GmbH
.
Degasification wells for drilling rock bits used CCE 120.4 mm Warze
114.2 mm, reinforced diamond–tipped and chisel istirayusche–cutting type A 112 mm. Wells are drilled Kustov method (two–three wells in the bush). The distance between the bushes is 10–20m. [6].
3. 3 Disturbance Analysis technology of works
Fifth southern lava unit 10 – the concentration of methane in the gas mixture at the output 18% of the wells drilled drilling machine GBH1/89/12 stock 100 rods, chisel 114 mm. Drilling rig in a satisfactory condition, that allows you to drill at least 30–35 m per shift, the backlog of lava bush degasification wells is 50 m wells are drilled according to the passport parameters with the distance between the bushes 10 m sealing wells 2–3 m, so the work wells ephemeral.
The second southern lava unit 10 – the concentration of methane in the gas mixture at the output 18%, drilling drilling rig GBH1/89/12 made available 100 rods, chisel 114 mm. Drilling rig in a satisfactory condition, that allows you to drill at least 30–35 m per shift, the backlog of lava bush degasification wells is 50 m wells are drilled according to the passport parameters with the distance between the bushes 10 m length and diameter of wells according to the passport, and the rotation angle and recovery wells is not always observed due to the presence of anchors and gain pickup. Sealing wells 2–3 m, so the work is ephemeral wells.
First southern lava unit 10 – the concentration of methane in the gas mixture at the output 30% of the wells drilled drilling machine GBH1/89/12 available 80 rods, chisel 114 mm. Drilling rig in a satisfactory condition, that allows you to drill at least 30–35 m per shift. Wells are drilled according to the passport parameters with the distance between the bushes 10 m length and diameter of wells according to the passport. Sealing wells 2–3 m, so the work is ephemeral wells.
First northern lava unit 10 – the concentration of methane in the gas mixture at the output 30% of the wells drilled drilling machine GBH1/89/12 available 80 rods, chisel 114 mm. Drilling rig in a satisfactory condition, that allows you to drill at least 30–35 m per shift, the backlog of lava bush degasification wells is 30 m wells are drilled according to the passport parameters with the distance between the bushes 10 m sealing wells 2–3 m, so the work wells ephemeral. Wells are drilled at increased inflow of degasification wells and wells installed dehumidifiers in time [7].
4. Analysis of the prospects for the development of the mine degassing system
In the analysis of methane at the mine working areas heavily set strict dependence of methane, which is 10% methane m3/min 100 for every 1, 000 tons of daily production. Currently means of ventilation kaptiruetsya largest share of methane – is lack of degassing efficiency, which in co–current circuits ventilation shall capped 60–70% of the total methane. Given the limited capacity of the ventilation system of treatment due to the workings section excavation complexes and regulated PB air velocity, the maximum possible supply of fresh air to ventilate the excavation site can be from 3000 to 3500 m3/min. According to the amount of air may be diluted to a safe concentration of 1 m3/min 30–35% pure methane (converted to 4000 tons / day of raw coal ). Whereby at excavation sites happen exceeded the maximum allowable concentration of methane and significantly overstated the rate of air flow in sewage workings.
Application ramjet ventilation schemes virtually eliminates the presence of dangerous concentrations of methane–air mixture at the junction of lava from the roadway, but in airway outside the lava at a distance of 30–40 meters form local accumulations of methane in contact rigid security strip and roof (Fig. 4). In order to increase the load factor on the gas and creating safe working conditions in coal loads up to 8000–15000 tons / day is necessary to use a combined degassing scheme, which provides degassing reservoir – satellites, host rocks, further developed space stope and moving part of the ventilation nadbermovoy generation. For these purposes, to develop with the outgoing air stream routed 2 degassing pipe that besides kaptirovaniya methane degasification wells drilled for stope line (line number 1 – degassing) provides additional degassing goaf and nadbermovoy part of the ventilation generation (line number 2 – goaf ) to reduce methane emissions in the background outgoing jet excavation site.
With an increase in the percentage of methane in the captured agents degassing methane–air mixture at 1% – the amount of recoverable gas increased by 2.4 m3/min 100% CH4.
Analysis of surface decontamination
Degassing goafs stopes moving through wells drilled from the surface [4].This method is applied as an additional degassing degassing method developed space together with degassing of the underground workings. Since 2005, the mine produced construction of wells from the surface to reduce outgassing at excavation sites ( Fig. 5). Gassing of such wells begins when approaching stope. Maximum flow rate is observed in their undermining and ranges from 5 to 10 m3/min. In the active period of operation of such wells are allocated from 800 to 1500 thousand m3metana. Methane content in the gas mixture is 90–98%. Established experimentally that the degassing efficiency in production areas can be further increased to 20%, which entails an increase in the load on the gas factor. This measure in conjunction with degassing through wells drilled from workings eliminates restrictions on the gas factor loadings on the face output.
Indings
Methane refers to gas, which, according to experts, create a greenhouse effect, keeping the heat in the Earth's atmosphere. The degree to which a particular greenhouse gas keeps the heat of the thermal effect is measured relative to carbon dioxide. It is believed that the ability to trap heat in the atmosphere over a hundred years, methane is 21 times superior to carbon dioxide. Methane and other greenhouse gases are emitted into the atmosphere as a result of both natural processes and human activities such as coal mining. [5]
Based on the findings will be developed a set of measures on the use of methane in the industry and the national economy.
Thus, in the work solved an important social problem to improve the efficiency of degassing sources that allow:
- Improve the environmental situation in the Donetsk region in general, due to the reduction of greenhouse gas methane.
- Reduce the consumption of thermal power plants of Ukraine natural gas and coal to generate electricity.
- To improve the safety of mining operations, reduce accidents and injuries in the workplace.
- Increase coal production by reducing downtime associated with dangerous concentrations of methane.
- Obtain additional financial resources through the implementation of emission reduction units.
- To improve the social situation of workers in the enterprise.
- Raise the rating as businesses with high quality production.
In writing this essay master's work is not yet complete. Final completion : December 2014. Full text of the work and materials on the topic can be obtained from the author or his manager after that date.
References
- Дегазация выработанных пространств (Обзор). – М. 1976, 56 с.
- Руководство по дегазации угольных шахт. – М. : Недра. 1975, 189 с.
- Дегазация угольных пластов и вмещающих пород при проведении горных выработок. Временное руководство и типовой проект. – М. : ГОСГОРТЕХИЗДАТ. 1962 г., С. 38 – 40.
- Дегазация угольных шахт. Требования к способам и схемам дегазации СОУ 10. 00174088 – 2004.
- Инструкция по расчету количества воздуха необходимого для проветривания действующих угольных шахт. – М. : Недра, 1975 г.
- Ушаков К. З., Бурчаков А. С., Пучков Л. А., Медведев И. И. Аэрология горных предприятий: Учебник для ВУЗов, – М. : Недра, 1987. – 421 с.
- Порцевский А. К. Безопасность жизнедеятельности при горных и горноразведочных работах. Часть 1. – М. 2005, 80 с.