1. Введение
Все процессы жизнеобеспечения человечества в современном мире напрямую зависят от стабильности и качества потребляемой электроэнергии. В этой связи, энергетические компании сталкиваются с задачей обеспечения стабильного и бесперебойного процесса генерации электроэнергии. Чтобы решить эту проблему необходимо проводить мониторинг технического состояния оборудования электростанций в режиме реального времени. Однако, только основные механизмы энергии, которые производят электрическую энергию, - турбины – оборудованы контролем и блок -системами. В то же время для работы одной турбины необходимо использовать десятки поддерживающего динамического оборудования, таких как различные виды мельниц, дутьевых вентиляторов, вытяжных вентиляторов, насосов, градирен. Многие вспомогательные агрегаты работают без резерва, и их внезапный отказ приводит к снижению объема и качества вырабатываемой электроэнергии до полной остановки турбины. Оснащение оборудования собственных нужд электростанций системами автоматической диагностики и мониторинга технического состояния является реальным способом обеспечить безопасную и надежную работу электростанций [1] и стабильности жизнедеятельности человечества.
2. Системы мониторинга технического состояния и автоматической диагностики
Теперь известно большое количество систем мониторинга состояния, диагностики и параметров динамического оборудования электростанций.
Видный представитель таких систем является система [2], некоторые из практических результатов которой используемые на тепловой электростанции, будут обсуждаться в этой статье. Тестовые объекты, в первую очередь - сеть датчиков, установленных непосредственно на вспомогательном оборудовании тепловых электростанций. Эти датчики выполняют преобразование измеряемых параметров различных физических величин (вибрация, температура, ток, давление и т.д.) в электрические сигналы. Электрический сигнал от датчика через кабельные линий связи входит программируемые интерфейсные модули для предварительной обработки и далее - для обработки диагностической станции. Визуализация результатов измерений в режиме реального времени представлен на мониторе со значениями измеряемого параметра и цветными иконками (зеленый - "ТЕРПИМО", желтый - "НЕОБХОДИМЫЕ ДЕЙСТВИЯ", красный - "НЕВЫНОСИМАЯ"), соответствующие текущему техническому состоянию диагностируемого оборудования. Одновременно выдаются в автоматическом режиме диагностические инструкции (экспертные).
2.1. Мониторинг состояния - Режим "Монитор"
На экране "Монитор" схематически представлены: оборудование работает в виде интуитивно понятно любому человеку, основные параметры должны быть измерены в соответствии с ГОСТ Р 53565-2009 [3], представлены в верхней левой части экрана, но самое главное - рекомендации автоматической экспертной системы, в верхнем правом углу экрана "Монитор", будут осуществляться в целях обеспечения безопасной эксплуатации оборудования. Когда техническое состояние системы переходит в состояние "Невыносимой" работы, система предупреждает персонал через устную коммуникацию, чтобы выполнить срочные меры по обеспечению безопасной эксплуатации оборудования. Технологии должны соответствовать рекомендациям системы, в соответствии с действующими правилами персонала, в автоматическом режиме контролировать скорость и качество изменения состояния узлов и их компонентов.
2.2. Мониторинг состояния - Режим "Тренд"
Все параметры, измеренные с помощью системы, хранятся в базах данных для различных интервалов времени от 12 часов до 9 лет. Представлены четыре дня тенденции ускорения передней несущей части двигателя показывает, что только в течение двух дней техническое состояние рабочего устройства находится в категорию "терпимо", то есть дефект в подшипнике увеличивается (рисунок 1, раздел 2) и техническое состояние машины переходит в категорию "Невыносимая". Система автоматически информирует сотрудников о необходимости выполнить вывод из эксплуатации блока в течение 5 часов деятельности с последующим ремонтом (рис 1, раздел 3).
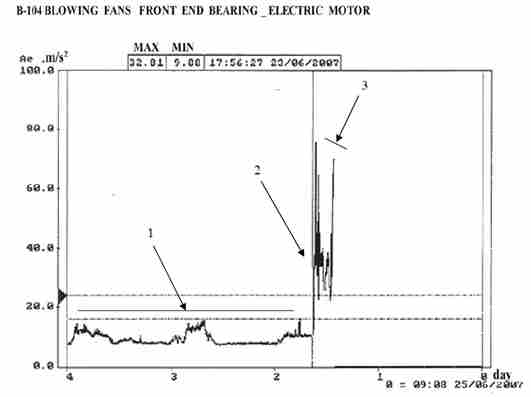
Рис. 1. Тенденция с ускорением до 4 дней передний конец подшипника электродвигателя.
3. Примеры диагностики оборудования
Система обеспечивает надежную диагностику дефектов в подшипниках, режимов нарушения технологического процесса (нарушение кавитации, гидроударов и т.д.), нарушения центровки валов и балансировки вращающихся частей, ослабления крепления, электромагнитное и другие дефекты [4].
3.1. Нарушение режима работы оборудования
Следует отметить, что периодически технологический персонал должен работать со вспомогательным оборудованием в других параметрах, чем приведенные в паспорте, чтобы обеспечить работу энергоблока, что, несомненно, будет влиять на состояние механического устройства и его технические ресурсы. При управлении насосом ПЭ-500-180-3 на тепловой электростанции сотрудник изменил технологический режим ее работы, в результате чего это привело к увеличению давления насоса примерно на 15%, а занижение нагрузки на 40%, что привело техническое состояние насоса в категорию "Невыносимая" - действующие значения были: виброускорение (AE) - 33,88 м / с2, скорость вибрации (VE) - 13.22 мм / с, вибрации смещения (Se) - 23.10 мкм (таблица 1).
Таблица 1. Измеренные параметры вибрации насоса.
Тип подшипника | Направление | Ae, м / с2 | Ve, мм / с | Se, мкм |
Хвост подшипника | X - горизонтальное | 33.88 | 13.22 | 23.10 |
Y- вертикальное | 19.72 | 7.43 | 12.82 | |
Z - осевое | 17.30 | 6.16 | 4.07 | |
Передняя часть подшипника | X - горизонтальное | 7,91 | 3,72 | 5,76 |
Y- вертикальное | 12.16 | 4.59 | 5.71 | |
Z - осевое | 13,68 | 3,27 | 4,66 |
В амплитудном спектре виброускорения (рисунок 2) и скорости вибрации (рисунок 3) доминирующей является частота вращения рабочего колеса насоса 349,2 Гц (22.83 м / с2, 10.39 мм / с).
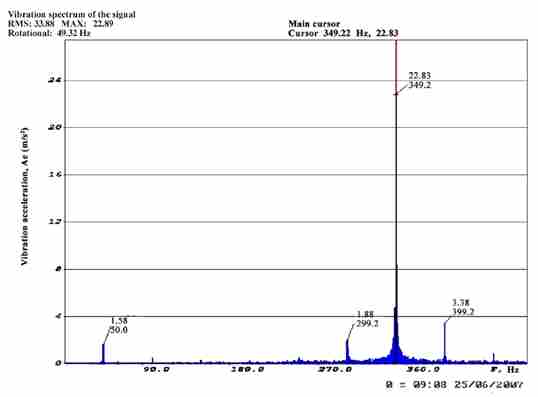
Рис. 2. Амплитудный спектр виброускорения от 0 Гц до 450 Гц.
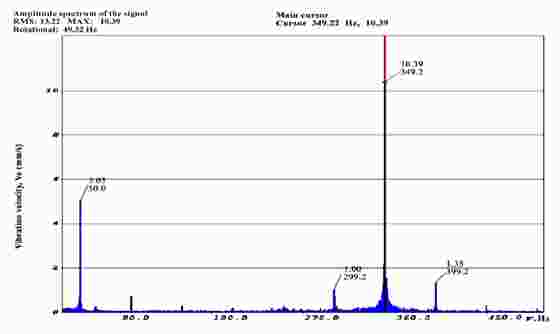
Рис. 3. Амплитудный спектр виброскорости от 0 Гц до 450 Гц.
В амплитудном спектре смещения вибрации (рисунок 4) преобладающей является частота вращения (16.12 мкм), присутствует также частота режущего диска колеса насоса 349.2 Гц (4,74 мкм).
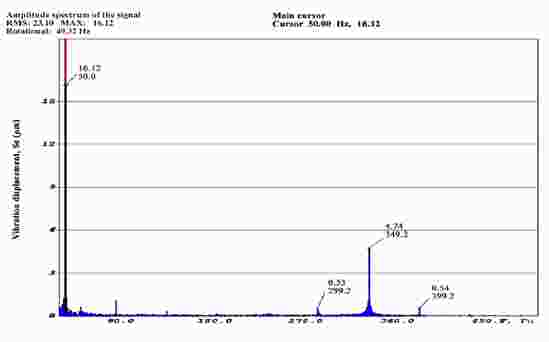
Рис. 4. Амплитудный спектр смещения вибрации от 0 Гц до 450 Гц.
То, что гармоники частоты вращения доминирует в спектре вибрации перемещения (рисунок 4), и имеет значительное влияние в спектре скорости вибрации (рисунок 3) означает наличие дисбаланса в насосе. Гармоники вращения частоты крыльчатки насоса модулируются в спектрах виброускорения, виброскорости и перемещения вибрации (рисунок 2, 3, 4). Наличие дисбаланса является результатом нарушения действующих практик и имеет гидравлическое происхождение. Длительная эксплуатация насоса с таким нарушением технологического режима неизбежно приведет к развитию дефектов в подшипниках насоса с последующей потерей работоспособности устройства.
3.2. Низкое качество ремонтных работ
При вводе - насоса в эксплуатацию, после ремонта на тепловой электростанции, было обнаружено высокое значение ускорения вибрации в хвостовой части электродвигателя. Анализ спектральных составляющих вибрации показали, что максимальная вибрация происходит на частоте прохождения пазов статора, модулированных двоичной частоты напряжения питания и частоты вращения гармоник (рисунок 5).
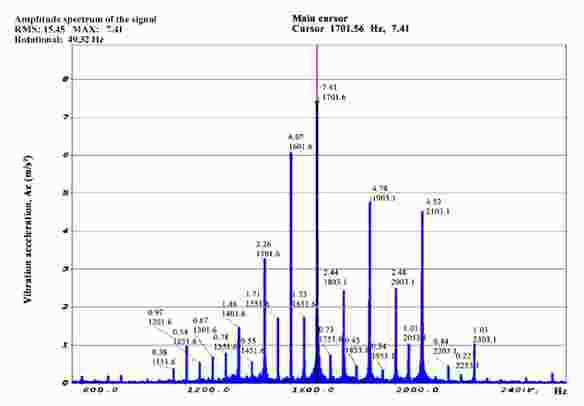
Рис. 5. Амплитудный спектр виброускорения от 800 Гц до 2500 Гц.
Это может выявить электромагнитный дефект двигателя - магнит разрыв, эксцентриситет и несоосность ротора. Повторный ремонт был необходим, чтобы привести устройство в техническую категорию "Терпимо". Эти примеры диагностики оборудования подтверждают, что виброакустическая диагностика является очень чувствительным методом для диагностики оборудования, что позволяет проследить развитие дефектов.
4. Заключение
Оборудуя машину стационарной системой технического контроля, мониторинга и автоматической диагностикой исключил несчастные случаи, и исключил так называемые отказы "Внезапный". "Внезапные" отказы происходят, где нет никакого контроля над процессом происхождения, развития дефекта, и его роста к критическому уровню, а затем к непредвиденному случаю.
Оснащение вспомогательных механизмов электростанций системами, и в связи с этим, переход к эксплуатации по фактически технической заявке, планирования и исполнения технического обслуживания и ремонта только тогда, когда указанная система обеспечивает надежную, безопасную, ресурсосберегающее обслуживание электростанций
Список источников
1. Костюков В.Н. 2002 Мониторинг безопасности производства (Москва: Машиностроение)
2. Костюков В.Н., Бойченко С.Н., Костюков А.В. 1999 Автоматизированные Контрольные Системы Безопасного ресурсосберегающего Действия Нефтяной Очистки и Оборудования Нефтехимии (АСУ SRSM COMPACS®) ( Москва: Машиностроение)
3. ГОСТ Р 53565 2010 Контроль состояния и диагностика оборудования. Состояние Мониторинг опасного Производственного оборудования. Вибрация центробежных насосных и компрессорных установок (Москва: Стандартинформ)
4. Костюков В.Н., Тарасов Е. В. Мониторинг состояния и диагностика подшипников качения электродвигателей высокого напряжения во время их эксплуатации 24 Int. Конг. на мониторинг состояния и диагностика инженерного управления (Ставангер, Норвегия, 30 мая - 1 июня 2011 г.) С. 900-904