Адаптивная оптимизация рабочих процессов проходческого комбайна как мехатронного объекта
Автор:А. К. Семенченко, О. Е. Шабаев, Е. Ю. Стипаненко, Н. В. Хиценко –
Источник: Неделя горняка семинар.
Аннотация
А. К. Семенченко, О. Е. Шабаев, Е. Ю. Стипаненко, Н. В. Хиценко – Адаптивная оптимизация рабочих процессов проходческого комбайна как мехатронного объекта.На основе анализа предпосылок и возможного эффекта от внедрения мехатронного подхода выделен ряд задач адаптивной оптимизации рабочего процесса проходческого комбайна, решение которых должно осуществляться в процессе его функционирования. Для этих задач обоснованы критерии и параметры оптимизации, выполненадекомпозиция и предложен алгоритм решения системой интеллекта комбайна. Установлено, что адаптивная оптимизация рабочих процессов проходческого позволяет получитьсущественное повышение ресурса элементов конструкции комбайна и обеспечить повышение темпов проходки.
Актуальность
Среди проблем, стоящих перед угольной промышленностью и влияющих на добычу угля в отрасли, наиболее острой остается проблема ускорения темпов проведения подготовительных выработок, обеспечивающих необходимую и своевременную подготовку фронта очистных работ. По нашим оценкам [1], традиционный способ повышения производительности проходческой техники за счет повышения массы и энерговооруженности при неизменных структурно-компоновочных схемах и способах управления для обеспечения темпов проходки на уровне 40 м/сут требует установки привода исполнительного органа мощностью не менее 1500 кВт при массе комбайна более 200 т. Это, очевидно, приведет в условиях стесненных размеров выработок к повышенной нагруженности элементов конструкции.
Предпосылки мехатронного подхода
Создание проходческих комбайнов нового технического уровня требует высокой степени интеграции механической, электрической, гидравлической, электронной и информационной составляющих, что обуславливает необходимость мехатронного подхода. Преимущества мехатронного подхода иллюстрирует рис. 1. Вусловиях нестабильности и неопределенности условий эксплуатации комбайнаприменение мехатронногоподхода позволяет обеспечить высокоекачество выработки, требуемыйресурс элементов конструкции, минимальнуюмощность и металлоемкость машиныпри высоких темпахпроходки. Проходческий комбайнкак мехатронный объект должен представлятьсякак совокупность взаимосвязанныхисполнительных механизмов ибазовых корпусных элементовконструкции, изменяющих свое положение в пространстве под действием приводовее силовых систем в результате компьютерного управления, обеспечивающегореализацию функций комбайна с максимальной эффективностью. Повышение эффективности работы машиныобеспечиваетсяпутемадаптивнойоптимизации ее рабочего процесса по критериям производительности, энергопотребления и надежности на основе текущей информации о состоянии силовыхсистем,данных опараметрах внешней средыи состоянии оборудования проходческого комплекса. Указанная информация поступает от интегрированных в элементы конструкции комбайна датчиков. При этом большое значение имеет разработка алгоритмов, заложенных в интеллектуальную систему управления проходческого комбайна.
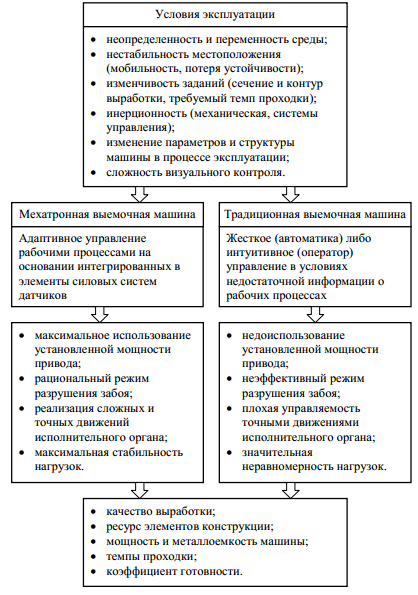
Рисунок 1 – Эффективность мехатронного подхода к проектированию выемочных машин
Задачи адаптивной оптимизации
Система интеллекта горной машины [4] программное обеспечение бортового компьютера для решения задачи многокритериальной оптимизации рабочего цикла горной машины. В соответствии с функциональным назначением система интеллектанаряду соценкой работоспособности исполнительных механизмов, прогнозированием остаточного ресурса элементов конструкции, накоплением данных об их отказах и параметрах рабочих процессоввыполняет задачиадаптивной оптимизации:
Это обуславливает необходимость разработки математической модели формирования вектора внешнего возмущения нааксиальной коронке при ее взаимодействии с разрушаемым массивом во всех воз-можных режимах работы.
Задание вектора внешнего возмущения
Для задания вектора внешнего возмущения требуется разработка математической модели определения толщины и ширины среза и изменений кинематическихзадних и боковых углов резцов аксиальной коронки, в процессе разрушения массива. При разработке этой модели былиприняты следующие исходные положения:
- режимов разрушения забоя исполнительным органом выбор рациональных значений скоростей подачи и вращения исполнительного органа для различных зон забоя;
- получения забоя заданного сечения (точность обработки) управление исполнительным органом, обеспечивающее минимальный перебор породы по контуру выработки;
- диаграммы формирования импульсов питающего напряжения для преобразователей частоты питающего напряжения выбор формы и периодичности импульсов, обеспечивающих максимальный кпд системы и отсутствие резонансных явлений в силовых системах;
- схемы обработки забоя определение рациональной траектории движения исполнительного органапри обработке забоя.
Критерии адаптивной оптимизации
Основными критериями эффективности проходческого комбайна являются эксплуатационная производительность (темп проходки) и ресурс. При эксплуатации проходческого комбайна могут возникать две типичные производственные ситуации:
- Необходимость обеспечения максимальных темпов проходки выработки, что требует от комбайна максимальной производительности при допустимом уровне нагрузок в силовых системах.
- Реализация требуемых темпов проходки, при этом необходимо обеспечить максимально возможный ресурс комбайна за счет рационального нагружения силовых систем.
Таким образом, выбор критерия определяется производственной ситуацией, а система интеллекта, в свою очередь, должна обеспечивать эффективное управление по каждому из критериев.
Оптимизируемые параметры рабочего процесса
Для проходческого комбайна избирательного действия эффективное управление процессом разрушения забоя требуетопределения рациональныхзначений следующих параметров:
- скоростиподачи и вращения резцовой коронки, определяющие соотношения толщины и ширины стружки на резцах коронки;
- глубинызарубки и шагифрезерования в отдельных режимах разрушения забоя.
Для задачи адаптивной оптимизации режимов разрушения забоя исполнительным органом:
Скорости подачи и вращения резцовой коронки определяют соотношения толщины и ширины стружки, оказывая влияние на удельные энергозатраты и формирование нагрузок на отдельных резцах коронки. Глубина зарубки и шаг фрезерования формируют сечение забоя, обрабатываемого коронкой. Величина и форма сечения определяет объемы породы, разрушаемой отдельными резцами, что влияет на удельные энергозатраты процесса разрушения и динамичность нагрузок в целом на исполнительном органе.
- последовательностьрежимов разрушения забоя (например, для аксиальной коронки фронтальная зарубка, боковой рез одной или двумя коронками, вертикальная зарубка), определяющих количество циклов низкочастотной составляющей нагрузки в силовых системах комбайна за цикл обработки забоя;
- длины резов в каждом режиме цикла разрушения забоя исполнительным органом. Эти параметры совместно со скоростями подачи определяют длительность цикла обработки забоя, а дополнительно с обрабатываемыми сечениями теоретическую производительность комбайна. Длины резов однозначно определяются последовательностью режимов обработки забоя заданного сечения с соответствующими глубинами зарубки и шагами фрезерования, поэтому их не следует рассматривать как оптимизируемые параметры;
- глубинызарубки и шагифрезерования в отдельных режимах разрушения забоя, которые определяют количество циклов обработки забоя на один метр проходки и оказывают влияние на точность воспроизведения контура выработки.
Для задачи адаптивной оптимизацииперебора породы по контуру выработки:
- моменты времени подачи команд управления перемещениями исполнительного органа при обработке забоя, которые должны определяться с учетом возможной частичной потери устойчивости комбайна, ограниченной видимости в рабочей зоне и инерционностисистемы
оператор-машина
; - глубинызарубки и шагифрезерования, которые определяют размеры неровностей на боковых стенках выработки, соответствующих форме коронки.
- опереженияпо времени подачи управляющих воздействий, что возможно ввиду повторяемости рабочих процессов комбайна от цикла к циклу. Это требует реализации адаптивных механизмов самообучения, позволяющих учесть изменчивость физико-механических свойств и структуры забоя в направлении проходки выработки;
- скоростьотработки управляющих воздействий, обеспечивающаядопустимый уровень нагрузок в переходных режимах работы комбайна при минимальной их длительности.
Таким образом,осуществляется компенсацияинерционностиэнергомеханической системы комбайна. Поступающие от оператора управляющие воздействия отрабатываются исполнительным органом с некоторым запаздыванием, обусловленным как инерционностью энергомеханической системы комбайна и его системы управления, так и скоростью отработки управляющих воздействий, обеспечивающей сглаживание переходных процессов. В результате несвоевременности выполнения управляющих воздействий возможны выходы режущего органа за требуемый контур выработки и разрушение забоя с нерациональными режимными параметрами, что оказывает существенное влияние на формирование нагрузок, особенно при переходе со слабой породы на крепкую.
Для задачи адаптивной оптимизации диаграммы формирования импульсов питающего напряжения преобразователей частоты:
- параметры диаграммыформирования импульсовпитающего напряжения;
- скорость регулирования преобразователей частоты питающего напряжения, обеспечивающаядопустимый уровень переходных нагрузок в силовых системах.
Для задачи адаптивной оптимизациисхемыобработки забоя заданного сечения (траекториидвижения исполнительного органа при обработке забоя):
Декомпозиция задач адаптивной оптимизации
В таблице 1 сгруппированы управляемые параметры рабочего процесса подсистемы «Исполнительный орган» проходческого комбайна, значения которых определяются системой интеллекта в процессе решения задач оптимизации. Все параметры представляют собой вектора, компоненты которых соответствуют последовательным режимам разрушения забоя исполнительным органом.
Как видно из таблицы, большинство параметров определяются в процессе решения различных задач оптимизации, что требует их совместного решения либо декомпозиции. Поэтому для решения задач оптимизации рабочего процесса подсистемы Исполнительный орган
требуется анализ целевых функций для каждой задачи. Целевая функция является численным выражением критерия оптимизации, определяемого сложившейся производственной ситуацией. Поэтому для каждой ситуации можно выделить соответствующую группу целевых функций для решения задач оптимизации.
Одновременное решение указанных задач затруднительно и нецелесообразно, так как среди них можно выделить первичные и вторичные, связанные и независимые. Была выполненадекомпозиция, предполагающаяследующую последовательность решения задач:
- Установление рациональных параметров режима разрушения забоя исполнительным органом для характерных зон забоя, имеющих различные физико-механические свойства. Одновременно решается задача выбора рациональной схемы обработки забоя. В качестве критериев оптимизации в зависимости от производственной ситуации принимаются темп проходки или ресурс комбайна.
Оценку ресурса можно осуществлять (в относительных единицах) по величине накопленной повреждаемости [2]. В работе [3] установлено, что при показателе степени кривой усталости m=9 низкочастотная составляющая нагрузки, вызванная переходами из режима в режим разрушения забоя, оказывает определяющее влияние на накопленную повреждаемость в большинстве элементов конструкции. Это позволяет существенно упростить расчет накопленной зацикл обработки забоя повреждаемости, то есть вести его по известным максимальным и минимальным значениям нагрузки в каждом режиме с учетом только их последовательности при заданной схеме обработки забоя. Очевидно, чем ниже и равномернее будет нагрузка в элементах конструкции, тем ниже величина накопленной повреждаемости. Нагрузки в элементах конструкции комбайна формируются под действием вектора внешнего возмущения на исполнительном органе, компонентами которого являются проекции главного вектора системы сил на резцах и момент сопротивления на оси коронки. Как известно, между проекциями главного вектора и моментом сопротивления существует корреляционная связь. Таким образом, в качестве целевой функции при оптимизации по критерию ресурса может быть принят максимальный момент сопротивления на исполнительном органе за цикл обработки забоя.
- Установление рациональных по критерию ресурса значений скорости отработки управляющих воздействий и ширин импульсов диаграммы напряжения при частотном регулировании приводного двигателя. При изменении частоты питающего напряжения в приводе возникает переходной процесс, сопровождающийся формированием динамических нагрузок.Очевидно, желательно иметь минимальное время переходного процесса при допустимом уровне нагрузок.Поэтому в качестве целевой функции следует принятьскорость отработки управляющих воздействий при ограничении коэффициента неравномерности нагрузки (момента сопротивления на валу двигателя)
- Установление рациональных по критерию перебора породы значений опережения подачи управляющих воздействий при обработке забоя вблизи заданного контура выработки[6]. Глубина зарубки и шаги фрезерования, также влияющие на величину перебора, принимаются по результатам решения предыдущей задачи. Снижение перебора дает положительный эффект при решении любой из двух рассмотренных производственных задач. Поэтому в качестве целевой функции может быть принята величина выхода исполнительного органа за заданный контур выработкив каждом резе)
- Установление рациональных по критерию ресурса значений опережения подачи управляющих воздействий при обработке забоя вблизи граничных зон между пластами забоя различной прочности[5]. При переходе с более слабой на более крепкую породу со значительными величинами скорости подачи и толщины среза на резцах возникают пиковые нагрузки, обусловленные инерционностью системы и запаздыванием изменения толщины среза относительно скорости подачи. Опережения в подаче управляющих воздействий позволяют исключить эти пиковые нагрузки. При определенных значениях выход на более крепкую породу происходит уже с требуемыми значениями параметров режима разрушения. Дальнейшее увеличение нецелесообразно, так как уже не приводит к снижению пиковой нагрузки в пределах рассматриваемого реза, в то же время увеличивается длительность цикла обработки забоя. Поэтому в качестве целевой функции следует принять опережение подачи управляющих воздействий при соответствующем ограничении по максимальной нагрузке (моменту сопротивления на оси коронки) при переходе граничной зоны.
Таблица1 – Оптимизируемые параметры рабочего процесса подсистемы «Исполнительный орган» проходческого комбайна
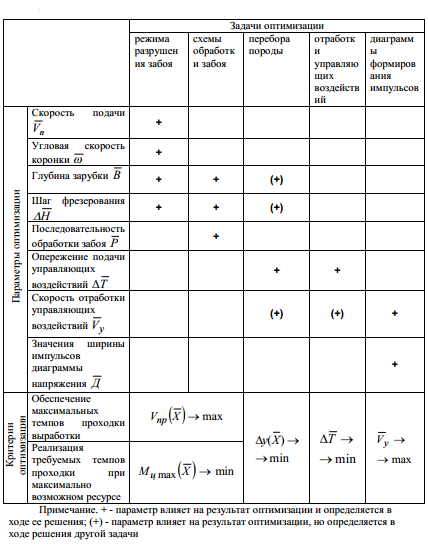
Оценка эффективности адаптивной оптимизации
С учетом выполненной декомпозиции были разработаны математическиемоделии методы решения приведенных задач адаптивной оптимизации, реализация которых для проходческого комбайна типа КПД дает следующий эффект(установлен методом имитационного моделирования):
- повышение темпов проходки в 1,4-2,5 раза за счет повышения уровня использования установленной мощности приводного двигателя и более эффективного по энергозатратам режимаразрушения забояв режимебокового реза;
- существенноеповышениересурса (по сравнению с автоматизированным регулированием нагрузки по току двигателя): для элементов металлоконструкции до 50-132 раз, для элементов трансмиссии: подшипников до 2,0 раз; зубчатых колес(контактная усталость)и коротких валов в 1,1-5,6 раза; зубчатых колес (изгибная усталость) и длинных валов в 2,6-28 раз;
- снижениес 5-15 см практически до нуля переборапородыпо контуру выработки, обусловленного сложностью визуального контроля, частичной потерей устойчивости машины и инерционностью исполнительного органа.
Заключение
Обеспечение высоких показателей производительности при приемлемых уровнях металлоемкости и энерговооруженности проходческих комбайновможет быть достигнуто путем их оснащения интеллектуальной системой управления, которая реализует адаптивную оптимизацию рабочего процесса комбайна по критериям производительности и ресурсана основе текущей информации о состоянии силовых систем машины, данных о параметрах внешней среды и состоянии оборудованияпроходческогокомплекса.
a name=ref>Список источников
- Семенченко А.К., Шабаев О.Е., Семенченко Д.А., Хиценко Н.В. Перспективы развития проходческих комбайнов. Горная техника 2006. Каталог-справочник. –С-Пб: ООО «Славутич». –С. 8-15.
- Семенченко А.К., Кравченко В.М., Шабаев О.Е. Теоретические основы анализа и синтеза горных машин и процесса их восстановления как динамических систем. –Донецк: РВА ДонНТУ, 2002. –302с.
- Семенченко А.К., Шабаев О.Е., Каплюхин А.А., Семенченко Д.А., Мизин В.А. К определению исходных данных для расчета элементов горной машины на выносливость. Наукові праці ДонНТУ. -Донецьк: ДонНТУ, 2006. -Вип. 104. -С. 176-182.
- Шабаев О.Е., Семенченко А.К., Степаненко Е.Ю., Хиценко Н.В., Мороз О.К. Интеллектуализация рабочего процесса проходческогокомбайна как мехатронного объекта. – VII Miedzynarodowa Konferencja Zastosowanie mechaniki w gornictwie”, Ustron, 25-26 czerwca2009.–с. 77-87.
- Шабаев О.Е., Семенченко А.К., Степаненко Е.Ю., Хиценко Н.В. Оценка эффективности проходческого комбайна синтеллектуальной системой «управление-подача» исполнительного органа. -Вісті Донецького гірничого інституту: Всеукраїнський науково-технічний журнал гірничого профілю, №1, 2009. –С. 207-218.
- Шабаев О.Е, Семенченко А.К., Хиценко Н.В., Степаненко Е.Ю. Мехатронная система подачи исполнительного органа проходческого комбайна с интеллектуальным модулем воспроизведения контура выработки. -Проблеми експлуатації обладнання шахтних стаціонарних установок: Збірник наукових праць. -Донецьк: ВАТ "НДІГМ імені М.М. Федорова", 2008-2009. -Вип. 102-103. -С. 404-414.