Abstract
Contents
- Introduction
- 1. Relevance
- 2. The purpose and objectives of the study
- 3. Analysis of the electric furnace
- 4. Classification of electric furnace
- 5. The list of items of equipment
- Conclusions
- Source List
Introduction
Tamman type resistance furnace is widely used in industry for a variety of research projects. On the metallurgical faculty DonNTU Tamman furnace is used as a training experimental stand for laboratory and research work of students and teachers. The furnace allows a number of technological procedures, such as steel alloying [1].
Currently relevant is the task of raising the level of automation of the laboratory stand. There is a task develop an electronic system for monitoring and control Tamman furnace based microcontroller, which will manage the installation of the furnace using a computer that will greatly enhance effectiveness of research in this installation and the reliability of the results.
1. Relevance
Increasing the level of automation of electric furnaces currently received considerable development. This is due, on the one hand, by treating them with modern materials which require difficult schedule modes with temperature change and maintain its high accuracy, continuous monitoring and adjusting the temperature during the process, on the other – to the stringent requirements of efficiency of operation of furnaces and the desire to reduce the use of labor force in the maintenance of equipment.
2. The purpose and objectives of the study
The electronic system should provide a smooth heating furnace at a predetermined temperature variation law with constant control of the power supplied to the furnace and the temperature inside it. The current values of monitored parameters should be recorded and displayed in a legible format on your computer. It is necessary to implement the control method furnace 2:- Remote control using a computer.
- Direct manual control near the kiln.
3. Analysis of the electric furnace
The principle of electric furnace installations (EPC) based on the conversion of electrical energy into heat. In accordance with the law of the Joule – Lenz, the amount of heat released in a conductor is proportional to the square of the current, the resistance of the conductor and the current travel time:
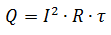
When choosing specific materials with known resistance and appropriate source of electric current can be obtained sufficient power to melt the metal.
Electric resistance furnaces fall into the furnace indirect action, in which the electric current flows through the heating elements, the heat releasing them, transmissible heated products radiation, convection (heat kind in which energy is transferred to the internal streams and flows.), Thermal conductivity, and direct effect on the furnace (electric–heating installation), in which current flows directly through the heating body, whereby heat is generated therein. In vacuum furnaces, the heat transfer is carried out only by the radiation; In most furnaces indirect heat transfer is carried out simultaneously by radiation and convection, while in the furnace with a temperature above 700 °C prevails radiation in low temperature ovens and ovens with forced circulation of the atmosphere – the convective heat transfer. In ovens with a liquid coolant, which is immersed in the heated article, the heat transferred by convection and conduction. In these furnaces, heating liquid itself may be heated due to the current flowing through it or by heating elements immersed in the liquid (internal heating bath) or beyond the crucible with liquid (with external heating bath) [2].
The direct heating furnace product, usually having a regular cross–sectional shape (rods, bars, wires), through special contacts included in the circuit. This group may include furnaces glass melting furnace (in the case where the liquid glass flowing through the current), the electrode boilers, furnaces for producing silicon carbide, electrographite. This is the principle of heat release stoves group can be attributed to electro–slag remelting furnace.
4. Classification of electric furnace
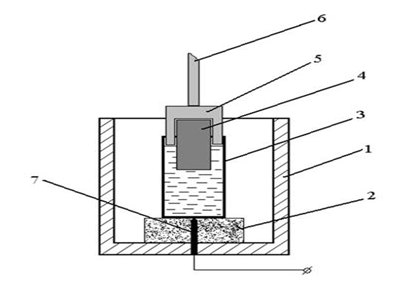
1 - Tamman furnace,
2 - Stand refractory,
3 - graphite crucible with liquid iron,
4 - pie exothermic mixture comprising magnesium oxide,
5 - mechanical seizure,
6 - an arm,
7 - thermocouple WR5/20
Figure 1 – Block diagram of the control system Tamman furnace
By appointment:
- melting;
- heating;
- thermal;
- forges;
- drying.
According to the type of electricity use:
- ovens resistance;
- induction;
- arc;
- contact;
- electronic;
- infrared.
According to the type of heating chamber:
- chamber furnaces;
- slit;
- globe;
- crucible.
By the method of temperature control:
- manual;
- the analog or digital thermostats;
- microprocessor programmers heating / cooling [3].
5. The list of items of equipment
The list of items of equipment in the system:
- block thyristor control [4];
- programmable platform Arduino;
- Interface Converter USB–UART;
- display unit;
- computer, a temperature sensor (thermocouple) [5];
- optosimistor.
In the designed system, in addition to the automatic temperature control, you need manual adjustment using the controls (during commissioning or emergency). Also, the system should present the LCD display (4 lines of 40 characters), which is a display unit. The display must show the following lines:
- the status of the furnace: on / off;
- control oven: a PC / from the stand;
- operation: heating / cooling;
- the selected heating program.
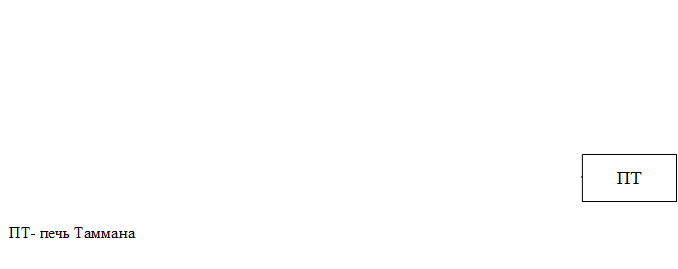
Figure 2 – Block diagram of the control system Tamman furnace
(animation: 8 frames, 18.3 KB)
Conclusions
Summary: The proposed structure of the electronic system provides a heating furnace of a given law Tamman temperature changes to the control power supplied to the furnace and temperature, with remote and manual control.
Source List
- А. А. Троянский Методические указания к лабораторным работам по курсу
Металлургия черных металлов
/ В. М. Сафонов, А. Н. Смирнов. – Донецк, ДПИ, 1993. – 30 c. - М. И. Колкер Электропечи сопротивления с широтно–импульсным управлением с применением тиристоров.–М.:Энергия, 1977.–104 с.
- Классификации промышленных электропечей по различным параметрам [Электронный ресурс]. – Режим доступа:
http://istra-vniieto.ru/ - Н. Г. Винниченко Твердотельная электроника – Донецк, Доннту, 2008. – 134 c.
- В. И. Бойко Схемотехника электронных систем. Аналоговые и импульсные устройства / А. Н. Гуржий, В. Я. Жуйков, А. А. Зори, В. М. Спивак – СПб.: БХВ–Петербург, 2004. – 496 c.
- Н. Г. Бойко Теория и практика научных исследований / Т. А. Устименко. – Донецк, ДонНТУ, 2009. – 156 c.
- А. В. Булашенко Теория электронных и магнитных цепей – Сумы, СумДУ, 2010. – 175 c.
- В. И. Бойко Методы анализа и расчета электронных схем / А. В. Вовна, А. А. Зори, В. Д. Коренев – Донецк: ГВУЗ
ДонНТУ
, 2011. – 326 с. - Д. С. Гурлев Справочник по электронным приборам / 1974. – 512 с.
- Б. В. Тарабрин Интегральные микросхемы / Л. Ф. Лунин, Ю. Н. Смирнов и др. / Радио и связь, 1983. – 528 с.
- В. П. Миловзоров Электромагнитные устройства автоматики – 1985.