Пристрій управління і діагностики температурних режимів роботи стрічкового конвеєру
Автор: Т. В. Ніженець, Б. В. Гавриленко
Источник: ХIV Міжнародна науково-технічна конференція аспірантів і студентів „Автоматизація технологічних об'єктів та процесів. Пошук молодих“: збірник наукових праць. – Донецьк: ДонНТУ, 2014. – С. 103–106.
Аннотация
Т. В. Ніженець, Б. В. Гавриленко Пристрій управління і діагностики температурних режимів роботи стрічкового конвеєру У статті аналізується важливість контролю теплових режимів стрічкового конвеєра. Виноситься пропозиція щодо розширення функціональних можливостей базової апаратури автоматизації стрічкових конвеєрів АУК - 1М впровадженням у склад системи пристрою управління тепловими режимами роботи конвеєрів.
Сучасні шахти характеризуються великими масштабами і високою концентрацією вугільного виробництва з використанням високопродуктивної вугільної техніки зі складними механічними і електричними системами. Ефективність вуглевидобутку в значній мірі залежить від чіткості і надійності роботи шахтного транспорту, тому процес транспортування вугілля вимагає великої надійності, ефективності, високого ККД.
У вугільних шахтах і рудниках для доставки вугілля з вибою, а також для транспортування його по збірним штрекам, бремсбергам, ухилам і похилим стовбурам нині широко застосовуються стрічкові конвеєри. Це складні об'єкти автоматизації як з позиції управління ними, так і забезпечення безпеки експлуатації.
Основною задачею автоматизації конвеєрних ліній є централізоване управління процесом пуску і зупинки конвеєрів з одночасним забезпеченням їх автоматичного захисту з метою зменшення енерговитрат і зниження витрати матеріалів. Крім того, все більш актуальним стає завдання автоматичного регулювання температурних режимів роботи стрічкового конвеєру.
Однією з причин, що призводять до перегріву конвеєрної стрічки є її надмірній натяг або прослизання, тому важливо запобігти и попередити аварійні теплові режими роботи конвеєрів за допомогою функції автоматичного контролю і забезпечення оптимального натягу конвеєрної стрічки у системі автоматизації.
Підвищене зношування механічних частин стрічкового конвеєра, влучення вугільного пилу в роликоопори також призводять до нагрівання стрічки і приводного барабану до неприпустимих температур.
Для оцінки нагрівання конвеєрної стрічки в залежності від рівня її сумарного натягу збігаючої та набігаючої гілок промоделюємо цей процес за допомогою пакету інженерних розрахунків MathCAD.
Вхідними параметрами для розрахунків обираємо технологічні параметри для магістрального стрічкового конвеєру 1Л800Д, а саме:
– довжина конвеєру – 800 м;
– діаметр приводного барабану – 840 мм;
– діаметр приводного барабану з футеровкою – 842 мм;
– ширина приводного барабану – 1150 мм;
– ширина стрічки – 1000 мм;
– швидкість стрічки – 2 м/с;
– кут охвату барабана стрічкою – 4π/3 рад.
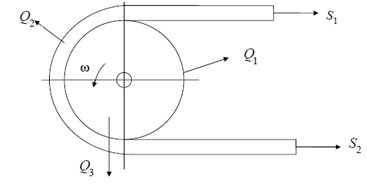
Рисунок 1 – Структурна схема пари приводний барабан – стрічка
На рис. 1 зазначено: S1 та S2 – натяг гілок стрічки; Q1 – кількість тепла, відведена випромінюванням; Q2 – кількість тепла, відведена природною конвекцією; Q3 – кількість тепла, відведена вимушеною конвекцією.
Тепло, утворене в результаті тертя барабана о стрічку, буде витрачатися на нагрів цих елементів, і відводитися випромінюванням, природною конвекцією від ділянки стрічки і вимушеної конвекцією від торцевих поверхонь барабана.
Рівняння теплового балансу [2] для нагріву приводного барабана і стрічки має вигляд, ккал:

де Qутв – кількість тепла, утворена під час роботи конвеєру, ккал / год;
Qнб – кількість тепла, що витрачається на нагрівання барабану и стрічки, ккал;
Q1 – кількість тепла, відведена випромінюванням, ккал / год;
Q2 – кількість тепла, відведена природною конвекцією, ккал / год;
Q3 – кількість тепла, відведена вимушеною конвекцією, ккал / год;
T – час роботи конвеєру.
Результат моделювання представлений на рисунку 2.
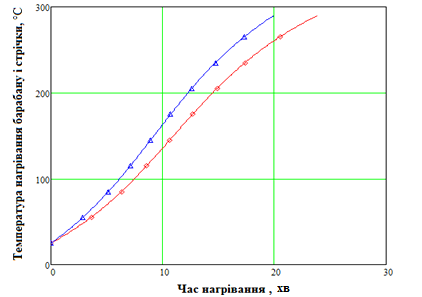
Рисунок 2 – Залежність температури нагріву стрічки і приводного барабану від часу нагрівання при різних натягах:
◊ – сумарний натяг набігаючої та збігаючої гілок стрічки 7, 4 кН,
▲ – сумарний натяг набігаючої та збігаючої гілок стрічки 10 кН.
Аналіз залежності на рис. 2 свідчить про те, що конвеєрна стрічка в однакових умовах швидше нагріється при більшому значенні сумарного натягу.
Наразі не існує систем автоматичного управління стрічковими конвеєрами, які б втілювали у собі функції автоматичного контролю теплових режимів роботи стрічкового конвеєру. Більшість систем автоматизації, які застосовуються на шахтах, виконані із застосуванням застарілої елементної бази, що обмежує функціональні можливості апаратури. Надійність і безпека роботи конвеєрів знижується також через часті відмовлення релейних і напівпровідникових елементів, викликаних нестабільністю їхньої роботи і швидким зносом контактних груп.
Базова апаратура автоматизації АУК - 1М [1] виконує функції контролю і управління роботою стаціонарних ліній (до трьох відгалужень) і напівстаціонарних нерозгалужених ліній, які складаються з стрічкових і скребкових конвеєрів з числом конвеєрів в лінії до 10.
До наступного часу апаратура АУК - 1М не використовує функцію контролю температури роликів, конвеєрної стрічки та приводного барабану, а також не контролюється натяг тягового органу, що значно зменшує безпеку підземного транспорту на шахті.
Розширимо функціональні можливості апаратури АУК - 1М впровадженням у склад системи автоматизації пристрою управління і діагностики температурних режимів роботи стрічкового конвеєру за рахунок контролю температури стрічки, приводного барабану та роликоопор, а також формування сигналу управління стрічковим конвеєром у разі виявлення аварійних значень технологічних параметрів, що контролюються.
Структура пристрою наведена на рис. 3.
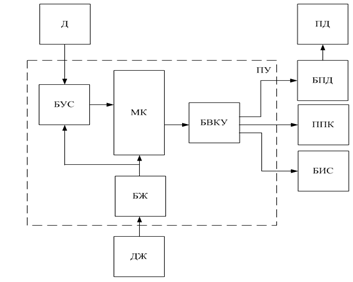
Рисунок 3 – Структурна схема пристрою управління
На структурній схемі (рис. 3) прийняті наступні скорочення: УУ – пристрій управління; Д – датчики; ДЖ – зовнішнє джерело живлення; ББ – блок живлення схеми; БУС – блок узгодження сигналів; МК – мікроконтролер; БВКУ – блок виводу команд управління; ППК – пускач приводу конвеєра; БИС – блок індикації та сигналізації; БПД – блок передачі даних; ПД – пульт диспетчеру шахти.
Наведена схема живиться від зовнішнього джерела живлення ДЖ (наприклад джерелом живлення може бути пристрій сигналізації та телефонного зв’язку УСТ) за допомогою блоку живлення БЖ, який перетворює напругу, що надходить до нього, до потрібного рівня у 5 В.
Сигнали з технологічних датчиків надходять до блоку узгодження сигналів, який перетворює сигнали для подачі до мікроконтролера.
В залежності від рівня сигналів мікроконтролер формує управляючий сигнал, який через блок виводу команд управління БВКУ надходить до пускача конвеєру ППК, блоку індикації та сигналізації БИС, та блоку передачі даних БПД, котрий в свою чергу передає сигнал на пульт диспетчеру ПД.
Як правило, пожежі відбуваються на приводних станціях і на лінійній частині конвеєра. Велика протяжність конвеєрних ліній і непередбачуваність місця спалаху ускладнює процес контролю температурних режимів.
В якості температурного датчика для контролю температури уздовж всієї довжини стрічкового конвеєру і попередження займання конвеєрної стрічки обираємо лінійний температурний сповіщувач (термокабель) PHSC, виробництва компанії Protectowire (США).
Лінійний тепловий сповіщувач PHSC являє собою кабель, який дозволяє виявити джерело перегріву в будь-якому місці на всьому його протязі. Термокабель PHSC – це єдиний датчик безперервної дії і застосовується в тих випадках, коли умови експлуатації не дозволяють установку і використання звичайних датчиків, а в умовах підвищеної вибухонебезпечності застосування термокабеля є оптимальним рішенням.
Наразі випускають декілька типів термокабелю. Обираємо термокабель типу TRI. PHSC TRI-Wire є унікальним тепловим детектором, який може генерувати окремо сигнал спрацювання («Предтревога») і сигнал пожежної тривоги в залежності від встановлених температурних порогів.
Для інтегрування термокабелю з пристроєм управління приймаємо інтерфейсні модулі типу МИП, вони призначені для контролю стану термокабеля типу PHSC (Protectowire Inc) по всій довжині і видачі дискретних сигналів про стан термокабеля в зовнішні ланцюги.
Згідно структурної схеми пристрою управління розроблена його функціональна схема, яка наведена на рисунку 4.
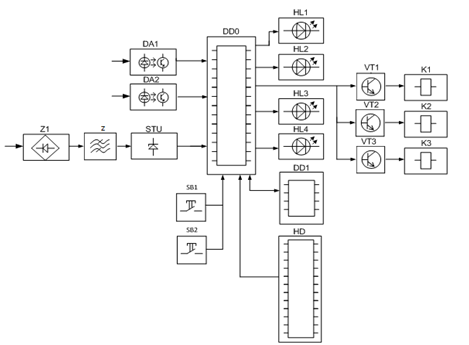
Рисунок 4 – Функціональна схема пристрою управління
На функціональній схемі зазначені: Z1, Z, STU – відповідно випрямляч, фільтр і стабілізатор напруги. Являють собою блок живлення (БЖ), який перетворює напругу, що подається від зовнішнього джерела живлення (ДЖ) для подальшої подачі на микроконтролер; DD1 – інтерфейс RS – 485, призначений для передачі керуючих впливів на відповідні технологічні ланцюжки; HL1 – HL4 – світлова індикація; HD – рідкокристалічний дисплей; DA1, DA2 – транзисторні оптопари. Виконують функцію гальванічної розв’язки і іскробезпеки при узгодженні дискретних сигналів з датчиків та мікроконтролером; DD0 – мікроконтролер ATMega16; SB1, SB2 – відповідно кнопки пуск та стоп; К1 – K3 – електромагнітні реле, що здійснюють включення аварійної звукової сигналізації, відключення приводу конвеєра та включення пускача приводу натяжної станції конвеєра відповідно.
Таким чином, використання пристрою управління тепловими режимами роботи стрічкового конвеєру у складі базової апаратури автоматизації АУК – 1М дозволяє запобігти перегріву, і як наслідок, займання конвеєрної стрічки. Це допоможе зменшити аварійність роботи стрічкового конвеєру, а також зменшити матеріальні витрати на відновлення конвеєрної стрічки, оскільки вона є найдорожчим елементом конвеєру.
Перелік посилань
1. Справочник по автоматизации шахтного конвейерного транспорта / Н. И. Стадник, В. Г. ,С. И. Егоров и др. – К.: Техника, 1992. – 438с.
2. Д. В. Хананов, А. Я. Грудачев. Аналіз процесів нагріву конвеєрної стрічки при повній пробуксовці приводного барабана шахтного конвеєра в аварійному режимі роботи.