Разработка системы контроля тепловых режимов работы шахтного ленточного конвейера
Автор: Т. В. Ниженец, Б. В. Гавриленко
Источник: XVI Международная молодежная научная конференция СеверГеоЭкоТех-2015: материалы конференции. – Ухта: УГТУ, 2015.
Технологический процесс транспортировки грузов и материалов является одним из важнейших в функционировании угольной шахты.
Современные угольные шахты характеризуются высокой концентрацией производства, использованием высокопроизводительной, угольной техники и сложных энергоемких электромеханических систем. Эффективность угледобычи в значительной степени зависит от четкости и надежности работы шахтного транспорта, поэтому процесс транспортировки угля требует большой надежности, эффективности, высокого КПД.
Ленточные конвейеры и конвейерные линии - это сложные объекты автоматизации как с позиции управления ими, так и с точки зрения обеспечения безопасности эксплуатации.
Основной задачей автоматизации конвейерных линий является централизованное управление процессом пуска и остановки, обеспечение автоматических защит с целью уменьшения энергозатрат, расхода материалов и исключения аварийных режимов работы. Кроме того, все более актуальной становится задача автоматического регулирования температурных режимов работы ленточного конвейера.
Технологический процесс транспортирования грузов представлен на рисунке 1.
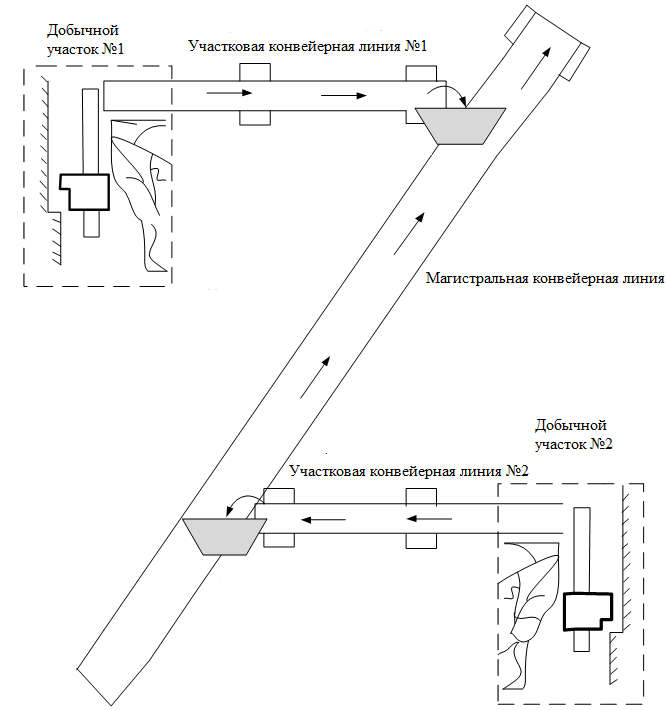
Рисунок 1 – Процесс транспортирования грузов
Процесс нагрева приводного барабана, ленты и распределенных физических элементов ленточного конвейера (роликоопор) определяется режимом его работы, натяжением набегающей и сбегающей ветвей ленты, удельной нагрузкой на ленту, техническим состоянием роликоопор (заштыбовка), а также технологическими параметрами ленточного конвейера, такими как: ширина ленты, диаметр приводного барабана и длина ленточного конвейера.
В настоящее время существующие системы автоматического управления ленточными конвейерами и конвейерными линиями (АУК-1М, АУК.3, САУКЛ и т.д.) не обеспечивают в полной мере функцию автоматического контроля тепловых режимов работы отдельных элементов и узлов ленточного конвейера [1]. Большинство средств и систем автоматизации конвейерных линий реализованы на устаревшей элементной базе, ограничивающей функциональные возможности аппаратуры. Надежность и безопасность работы конвейеров снижается также из-за частых отказов релейных и полупроводниковых элементов, нестабильности их работы и быстрого износа контактных групп.
Рассмотрим процесс нагрева для пары «приводной барабан – лента» (рис. 2).
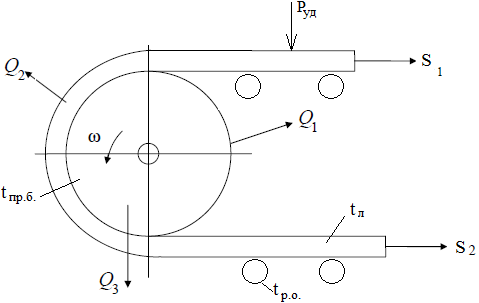
Рисунок 2 – Структурная схема пары «приводной барабан – лента»
На рис. 2 приведено: S1 и S2 – натяжение набегающей и сбегающей ветвей ленты; Q1 – количество тепла, отведенное излучением; Q2 – количество тепла, отведенное естественной конвекцией; Q3 – количество тепла, отведенное вынужденной конвекцией, tпр.б – температура приводного барабана; tр.о – температура роликоопор; tл – температура ленты; Руд – удельная нагрузка на ленту.
Тепло, образованное в результате трения ленты о барабан, затрачивается на нагрев этих элементов, и отводиться излучением и естественной конвекцией от участков ленты, а также вынужденной конвекцией от торцевых поверхностей барабана.
Уравнение теплового баланса процесса нагрева приводного барабана и ленты имеет вид [2]:

где Qобр – количество тепла, образованное во время работы конвейера, ккал/ч;
Qнб – количество тепла, затрачиваемое на нагрев барабана и ленты, ккал;
Q1 – количество тепла, отведенное излучением, ккал/ч;
Q2 – количество тепла, отведенное естественной конвекцией, ккал/ч;
Q3 – количество тепла, отведенное вынужденной конвекцией, ккал/ч;
T – время работы конвейера.
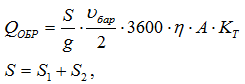
где S – суммарное натяжение ветвей ленты;
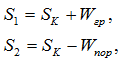
где Wгр и Wпор – сопротивления движению ленты соответственно на груженой и порожней ветвях.
Анализ уравнения теплового баланса и диаграммы натяжения показывает, что тепловой режим работы ленточного конвейера определяется удельной нагрузкой на ленту, а также усилиями натяжения груженной и порожней ветвей.
Для контроля температурных режимов работы ленточного конвейера разработана система, позволяющая выбирать рациональное соотношение удельной нагрузки на ленту и усилий натяжения ленты.
В состав разработанной системы автоматизированного контроля температурных режимов работы конвейера входит комплекс средств отбора информации по текущей температуре нагрева приводного барабана tпр.б., роликоопор tр.о, ленты tл, а также усилию натяжения ветвей ленты S1 и S2 и удельной нагрузки на ленту Руд.
Для контроля нагрева ленты и роликоопор по всей длине конвейера, предупреждения возгорания ленты применяется линейный температурный извещатель (термокабель) PHSC, производства компании Protectowire (США)[3].
Линейный тепловой извещатель PHSC представляет собой уникальный тепловой детектор в виде кабеля, который позволяет выявить источник перегрева в любом месте по всей его длине. Вариант размещения термокабеля на раме ленточного конвейера приведен на рисунке 3.
Термокабель PHSC TRI-Wire генерирует отдельные сигналы срабатывания («Предтревога») и пожарной тревоги в зависимости от установленных температурных порогов срабатывания защиты.
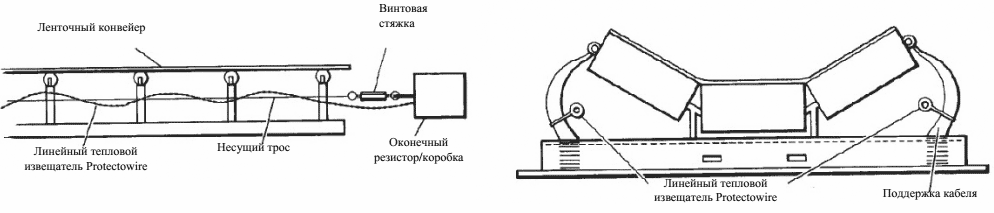
Рисунок 3 – Установка термокабеля на ленточном конвейере
Температура приводного барабана ленточного конвейера измеряется термосопротивлением, включенным в мостовую схему. Удельная нагрузка на ленту Pуд определяется конвейерными весами фирмы SBS, позволяющими автоматически тарировать ленту, осуществлять мониторинг отклонений взвешивания и отсутствие груза на ленте, обнаруживать материал остающийся на ленте, фиксировать процент времени прохождения пустой ленты за выбранный период времени. Интеллектуальный цифровой датчик удельной нагрузки SFT в конструктивном исполнении IP 65 не требует тарировки и обеспечивает очень высокое разрешение (1:1'000'000).
Натяжение груженой ветви ленты измеряется тензорезистивным преобразователем, установленным на натяжной станции.
Применение разработанной системы позволяет осуществлять эффективный и своевременный контроль тепловых режимов работы шахтного ленточного конвейера, предупреждает развитие аварийных ситуации, минимизирует затраты на ремонт и восстановление ленты.
Перечень ссылок
1. Справочник по автоматизации шахтного конвейерного транспорта / Н. И. Стадник, В. Г. Ильюшенко, С. И. Егоров и др. – К.: Техника, 1992. – 438с.
2. Д. В. Хананов, А. Я. Грудачев. Аналіз процесів нагріву конвеєрної стрічки при повній пробуксовці приводного барабана шахтного конвеєра в аварійному режимі роботи.
3. Линейный тепловой извещатель PHSC (термокабель). Режим доступа: http://www.phsc.ru/