Обоснование требований для создания средств и систем температурного контроля технологических режимов работы шахтного ленточного конвейера
Автор: Т. В. Ниженец, Б. В. Гавриленко
Источник: ХV Международная научно-техническая конференция Автоматизация технологических объектов и процессов. Поиск молодых
. – Донецк: ДонНТУ, 2015.
Аннотация
Т. В. Ниженец, Б. В. Гавриленко. Обоснование требований для создания средств и систем температурного контроля технологических режимов работы шахтного ленточного конвейера Проанализированы температурные режимы работы шахтного ленточного конвейера, рассмотрена модель нагрева и уравнения теплового баланса для фрикционной пары «приводной барабан – лента» и приводного двигателя ленточного конвейера. Предложена и обоснована система автоматизированного контроля температурных режимов работы ленточного конвейера.
Ленточные конвейеры и конвейерные линии – это сложные объекты автоматизации как с позиции управления ими, так и с точки зрения обеспечения безопасности эксплуатации.
Основной задачей автоматизации конвейерных линий является централизованное управление процессом пуска и остановки, обеспечение автоматических защит с целью уменьшения энергозатрат, расхода материалов и исключения аварийных режимов работы. Кроме того, актуальной становится задача автоматического контроля температурных режимов работы ленточного конвейера.
Базовая аппаратура автоматизации шахтных конвейерных линий АУК.3 не обеспечивает этих функций.
Проблема контроля над превышением температуры нагревания элементов шахтного ленточного конвейера по его длине является достаточно сложной, она связана со значительной протяженностью линии контроля, которая может превышать 2 километра. Кроме того, сказываются тяжелые условия эксплуатации шахтного оборудования: вибрация, угольная пыль, возможность резкого повышения температуры и др.
К аварийным тепловым режимам работы ленточного конвейера относится нагрев барабанов, ленты и роликоопор, а также перегрев двигателя конвейера.
Основными причинами появления мест локального перегрева ленточного конвейера являются: заклинивание ролика вследствие поломки подшипников ролика, чрезмерное трение ленты. Поэтому для обеспечения безопасной работы ленточного конвейера необходимо постоянно контролировать температуру роликов, ленточного полотна, других механизмов конвейера и температуру окружающего его воздуха.
Процесс нагрева приводного барабана, ленты и распределенных физических элементов ленточного конвейера (роликоопор) определяется режимом его работы, натяжением набегающей и сбегающей ветвей ленты, удельной нагрузкой на ленту, техническим состоянием роликоопор (заштыбовка), а также технологическими параметрами ленточного конвейера, такими как: ширина ленты, диаметр приводного барабана и длина ленточного конвейера.
Основной влияющий на нагрев элементов конвейера параметр – это погонная масса транспортируемого материала. Повышение загрузки конвейера и ослабленное натяжение ленты приводит к увеличению дуги рабочего проскальзывания, что повышает истирание ленты и может вызвать аварийную пробуксовку. В случае пробуксовки возрастает температура в зоне сцепления ленты и барабана, которая достигает 300-350°С за 15 мин его работы. При рабочем проскальзывании происходят потери энергии, затрачиваемые на преодоление сил трения, часть которых вызывает изменение температуры в зоне контакта барабан – лента.
Уравнение теплового баланса процесса нагрева приводного барабана и ленты имеет вид [2]:

где Qобр – количество тепла, образованное во время работы конвейера, ккал/ч;
Qнб – количество тепла, затрачиваемое на нагрев барабана и ленты, ккал;
Q1 – количество тепла, отведенное излучением, ккал/ч;
Q2 – количество тепла, отведенное естественной конвекцией, ккал/ч;
Q3 – количество тепла, отведенное вынужденной конвекцией, ккал/ч;
T – время работы конвейера.
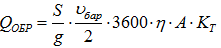
где S – суммарное натяжение ветвей ленты.
Анализ уравнения теплового баланса и диаграммы натяжения показывает, что тепловой режим работы ленточного конвейера определяется удельной нагрузкой на ленту, а также усилиями натяжения груженной и порожней ветвей.
Причиной пожара может быть также перегрев подшипников двигателя из-за недостаточной их смазки, перекосов вала и т.д.
Основной характеристикой нагрузочных режимов является тепловая характеристика электродвигателя. Работа АД всегда сопровождается его нагревом, что обусловлено происходящими в нем процессами и потерями энергии. Нормативный срок службы электродвигателя определяется, в конечном счете, допустимой температурой нагрева его изоляции. В современных двигателях применяется несколько классов изоляции, допустимая температура нагрева которых составляет для класса А – 105°С, Е – 120°С, В – 130°С, F – 155°C, H – 180°C, С свыше 180°С. Превышение допустимой температуры ведет к преждевременному разрушению изоляции и существенному сокращению срока его службы.
При эксплуатации шахтного конвейера в режимах, ненормированных ГОСТами, наиболее характерным является режим с быстроизменяющейся нагрузкой, когда двигатель периодически входит в режим перегрузки, возвращаясь затем на номинальный режим или опускаясь в режим работы с нагрузкой меньше номинальной. Если машина работает в продолжительном режиме, но с переменной нагрузкой (Р1, Р2, Р3…), имеет место неустановившийся тепловой процесс (рис. 1), т. к. в разные промежутки времени: t1, t2, t3, t4 и т. д. в ней возникают различные потери мощности, а следовательно, различные тепловые потери.
Для эффективного контроля количества тепла, накопленного приводным двигателем конвейера в процессе его работы, необходимо выяснить законы нагрева и охлаждения асинхронного электродвигателя.
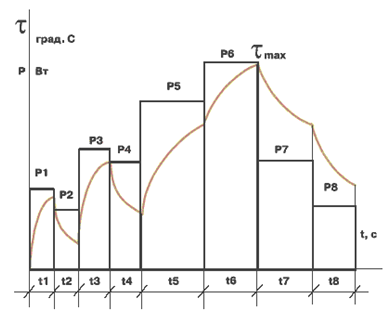
Рисунок 1 – Кривая изменения температуры двигателя при изменяющейся нагрузке
В этом случае типовая модель нагрева электродвигателя представляется в виде единого тела нагрева при следующих допущениях:
– электродвигатель имеет бесконечно большую теплопроводность и, как следствие, одинаковую температуру по всему объему;
– количество теплоты, которым электродвигатель обменивается с окружающей средой, пропорционально разности температур двигателя и окружающей среды;
– тепловые параметры электродвигателя и окружающей среды постоянны и не связаны с температурой двигателя, что обстоятельство обеспечивает линейность тепловой модели.
Нагрев приводного двигателя конвейера описывается уравнением:
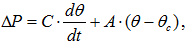
Обеспечение постоянства потерь мощности в двигателе позволяет получить решение этого уравнения с постоянным установившимся превышением температуры:

где Δθ(t) – текущее превышение температуры двигателя над температурой окружающей среды;
Δθуст – установившееся превышение температуры двигателя;
Δθо – начальное превышение температуры двигателя;
Те = С/А – постоянная времени нагрева.
Превышение допустимого нагрева для определенного класса изоляции вызывает ускоренное ее "старение", что приводит к снижению механической и электрической прочности, появлению хрупкости, разломов и трещин, пробою.
Эффективный температурный контроль режимов работы ленточного конвейера может быть обеспечен системой автоматизированного контроля с техническими средствами отбора информации, выполняющими следующие основные функции:
– обеспечение контроля фактической температуры окружающей среды в месте установки конвейера по всей его длине с возможностью сбора, обработки и хранения полученной информации;
– контроль превышения температуры в точках ее возможного повышения, например, у роликов конвейера, электродвигателя, барабана, с подачей местного светового сигнала о месте превышения температуры, сигнала по линии связи;
– контроль средней температуры и скорости ее изменения вдоль участков конвейера с передачей сигнала по линии связи о месте возможной аварии;
– обеспечение контроля усилия натяжения ленты и удельной нагрузки на ней.
В состав системы автоматизированного контроля температурных режимов работы конвейера входит комплекс средств отбора информации по текущей температуре нагрева приводного барабана tпр.б., роликоопор tр.о, ленты tл, двигателя tд, подшипников двигателя tподш, а также по усилию натяжения ветвей ленты S1 и S2 и удельной нагрузки на ленту Руд (рис. 2).

Рисунок 2 – Обобщенная структура системы автоматизированного контроля температурных режимов работы ленточного конвейера
На рис. 2 представлена структура системы контроля температурных режимов работы с блоком управления и сигнализации (БУС).
В зависимости от показателей технологических датчиков БУС формирует управляющие сигналы 1, 2, 3 и, соответственно, выдает команды на отключение конвейера при превышении контролируемых значений температуры, включение натяжной станции при недостаточном натяжении ленты и ее проскальзывании, а также обеспечивает индикацию и сигнализацию на пульте горного диспетчера.
Для контроля нагрева ленты и роликоопор по всей длине конвейера, предупреждения возгорания ленты применяется линейный температурный извещатель (термокабель) PHSC, производства компании Protectowire (США) [3].
Линейный тепловой извещатель PHSC представляет собой уникальный тепловой детектор в виде кабеля, который позволяет выявить источник перегрева в любом месте по всей его длине. Вариант размещения термокабеля на раме ленточного конвейера приведен на рисунке 3.
Термокабель PHSC TRI-Wire генерирует отдельные сигналы срабатывания («Предтревога») и пожарной тревоги в зависимости от установленных температурных порогов срабатывания защиты.
Температура приводного барабана ленточного конвейера измеряется термосопротивлением, включенным в мостовую схему.
Удельная нагрузка на ленту Pуд определяется конвейерными весами фирмы SBS, позволяющими автоматически тарировать ленту, осуществлять мониторинг отклонений взвешивания и отсутствие груза на ленте, обнаруживать материал остающийся на ленте, фиксировать процент времени прохождения пустой ленты за выбранный период времени. Интеллектуальный цифровой датчик удельной нагрузки SFT в конструктивном исполнении IP 65 не требует тарировки и обеспечивает очень высокое разрешение (1:1'000'000).
Натяжение груженой ветви ленты измеряется тензорезистивным преобразователем, установленным на натяжной станции.
Контроль температуры подшипниковых узлов двигателя осуществляется при помощи аппаратуры АКТ-2.
Алгоритм работы системы контроля температурных режимов сводится к следующему. При запуске конвейерной линии происходит инициализация и проверка состояния средств отбора информации с выполнением опроса по соответствию фактических значений температуры нагревания заданным значениям. Одновременно осуществляется проверка температуры нагревания приводного барабана, роликоопор и ленты конвейера по всей его длине. Система автоматизированного контроля работает в двух режимах. В случае если фактические значения температуры нагрева не превышают пороговых значений, осуществляется их визуализация, а работа конвейерной линии продолжается. Превышение заданных пороговых значений температуры приводит к отключению всей конвейерной линии с обеспечением аварийной сигнализации и индикации. Работа конвейерной линии и состояние технологических датчиков контроля визуализируется на мнемосхеме пульта горного диспетчера шахты.
Применение разработанной системы позволяет осуществлять эффективный и своевременный контроль тепловых режимов работы шахтного ленточного конвейера, предупреждает развитие аварийных ситуации, минимизирует затраты на ремонт и восстановление ленты.
Перечень ссылок
1. Справочник по автоматизации шахтного конвейерного транспорта / Н. И. Стадник, В. Г. Ильюшенко, С. И. Егоров и др. – К.: Техника, 1992. – 438с.
2. Д. В. Хананов, А. Я. Грудачев. Аналіз процесів нагріву конвеєрної стрічки при повній пробуксовці приводного барабана шахтного конвеєра в аварійному режимі роботи.
3. Линейный тепловой извещатель PHSC (термокабель). Режим доступа: http://www.phsc.ru/