Реферат за темою випускної роботи
Зміст
- Вступ
- 1. Характеристика і властивості високовуглецевої сталі для дроту високої міцності
- 2. Види термічної обробки дроту
- 3. Постановка завдання і цілі досліджень
- 4. Матеріали, методика, обладнання для дослідження
- 5. Результати досліджень
- Висновки
- Список джерел
Вступ
Від 8 до 10% кількості світового виробництва технічного заліза і сталі переробляється в дріт. Номенклатура виробів, що виготовляються з дроту, досить різноманітна, наприклад, канати, пружини, гвинти, цвяхи, голки, грозозахисного дріт, арматура для гуми, тканин і залізобетону. Щорічно, застосовується десятки мільйонів тонн дроту. Високоміцна дріт основне своє застосування знайшла при виготовленні канатів, пружин і арматури для попередньо напруженого залізобетону. Ці вироби є відповідальними деталями складних машин і конструкцій, тому до них пред'являються високі вимоги щодо якості [1].
За останні роки, попит на високоміцний дріт у світі збільшився вдвічі. Так, наприклад, 2010 році на внутрішньому ринку України було реалізовано 910,9 тис. Тонн високоміцного дроту. За підсумками 2013-2014 рр. попит на високоміцний дріт збільшився в середньому на 6,8% в порівнянні з 2010 роком. Спостерігався на внутрішньому ринку України зростання споживання дроту, значною мірою визначався розвитком будівельного сектора, машинобудівного комплексу, добувних галузей, де активно використовуються дана продукція [2]. У Росії в 2009 р внутрішнє споживання дроту різних видів склало 37,1 млн. Тонн (110,4% до 2008 р), у тому числі поставки вітчизняної продукції дос-тиглі 32 млн. Тонн (107% до 2006 р). Також у Росії, на думку експертів, до 2017 року потреба в високоміцного дроту складе більше 12 млн. тонн [2].
Таким чином, споживання високоміцного дроту з кожним роком збільшується, тому актуальним є питання про удосконалення технології виробництва і термічної обробки дротяної заготовки з метою отримання необхідного рівня властивостей дроту.
1.Характеристика і властивості високовуглецевої сталі для дроту високої міцності
Для виготовлення дроту високої міцності застосовують високовуглецеві сталі з вмістом вуглецю 0,6-1,0%. Для дроту високої міцності найчастіше використовують вуглецеві високолеговані сталі марок 70, 75, 80, 85 та ін. Хімічний склад визначається вимогами ГОСТ 10543. Однак у складі сталі не повинно бути домішок, які несприятливо впливають на властивості при проведенні необхідної для дроту термічної обробки - патентування.[3].
Для високоміцної сталі найбільш типова робота під дією розтягуючих сил. Міцність високоміцних сталей на розтяг характеризується тимчасовим опором розриву і межею плинності. Для встановлення властивостей міцності виготовленої високоміцної сталі її випробовують на розтяг і на вигин в холодному стані. Для цього зразок згинають під кутом 45 ... 1800, залежно від марки стали, навколо оправлення діаметром 1 ... 5 діаметрів зразка. Після вигину на зовнішній розтягнутій стороні зразка не повинно бути ніяких тріщин, відшарувань або злому. Проводять також випробування стали на удар, визначаючи тим самим її здатність чинити опір виникають в процесі роботи динамічному впливу. Випробування стали на удар дозволяє дізнатися ступінь її крихкості, якість обробки і ударну в'язкість (відношення роботи, витраченої на руйнування зразка до площі його поперечного перерізу в місці зламу). Ударна в'язкість стали вельми важливий показник, що впливає на міцність конструкцій, які схильні динамічним навантаженням при значній негативній температурі повітря [4].
Таким чином, для виготовлення високоміцного дроту застосовується високовуглецева сталь з вмістом вуглецю 0,6-1,0%. Саме структура та властивості стали надалі забезпечують необхідний комплекс властивостей готового дроту.
2. Види термічної обробки дроту
Класичний спосіб термообробки катанки - це патентування і отжиг на зернистий перліт. Патентування в цеху проводиться на протяжних агрегатах, які в своєму складі мають: піч для нагрівання; селітрову ванну; промивальну ванну - 2шт; травильну ванну; ванну для буріння; сушильний пристрій; намотувальний пристрій. [5].
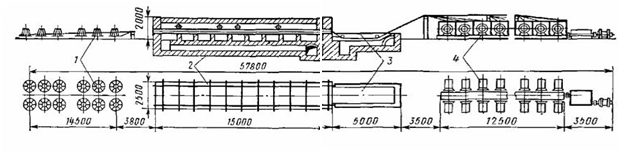
Рисунок 1 - Схема установки для патентування
Патентування полягає в нагріванні заготовки до температури 950-980°С та охолодження її в селітрової ванні при температурі 450-550°С (температури залежать від хімічного складу металу). Такі температури солі забезпечують перетворення переохолодженого аустеніту в тонкопластінчатий перліт (сорбіт) з товщиною пластинок цементиту 10-40 нм і фериту 60-200 нм [5]. Патентування стали необхідно проводити з урахуванням безперервності процесу волочіння, тому дріт по виході з фільєр пропускається через трубки, покладені в піч, нагріту до температури загартування сталі; після нагрівання дріт протягають через соляну ванну, потім витягують з неї. Охолоджують, намотують на барабани і знову простягають через наступні фільєри. Довжину печі, ванни відстань від ванни до намоточного барабана і швидкість руху дроту розраховують так, щоб дріт прогрілася до потрібних температур, завершилися відбуваються перетворення, і дріт встигла охолонути на повітрі. У мікроструктурі патентіруемой стали не повинно бути мартенситних включень і надлишкового фериту. Така структура дозволяє проводити волочіння з високими ступенями обтиску і забезпечує після волочіння зміцнення стали із збереженням підвищеної пластичності і в'язкості [6].
Існує безліч публікацій, які описують різні способи нагрівання та охолодження дротяної заготовки. Безумовний інтерес представляє нагрів дротяної заготовки в низькотемпературній плазмі та електролітах. Проте відсутня інформація про структуру і властивості, оброблених таким чином сталей. Відмовитися від використання розплавів солей можна шляхом використання низьколегованих сталей, однак це не вигідно, через зростаючого дефіциту легуючих елементів.
Останні роки великий інтерес представляють технології, в яких в якості охолоджувача при сорбітізаціі використовується вода. Com-plex Water Bath Processing - це процес, в якому температури аустенітизації при проміжному патентування складають 800-820, а при заключному - 820-850°С. Це позитивний аспект даної технології, т. К. Ці температури нижче, ніж при патентування в розплаві свинцю [7].
Ще одна технологія безсолевої сорбітізаціі - це сорбітізаціі стали на повітрі, який рухається. При вивченні сорбітізаціі потоком рухомого повітря, було з'ясовано, що підвищення температури аустенітизації і тривалості витримки зразків призводить до монотонного збільшенню мікротвердості сталі [7]. Це пов'язано з тим, що росте зерно аустеніту і його гомогенність, а це збільшує стійкість переохолодженого аустеніту, його схильність до переохолодження і отримання більш дисперсних структур при розпаді [8].
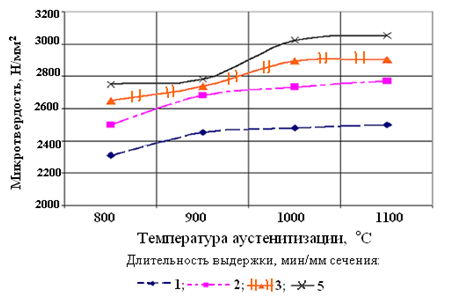
Рисунок 2 - Вплив температури аустенітизації і часу витримки на мікротвердість структури катанки зі сталі 70 при охолодженні потоком повітря, який рухається зі швидкістю 4м/с
Зі зменшенням швидкості охолодження зменшується і твердість катанки. Збільшення температури нагріву та тривалості витримки призводить до підвищення значень мікротвердості продуктів дифузійного розпаду переохолодженого аустеніту [9].
В даний час впроваджуються нові технології в процес тримаючи-ської обробки дроту. Одна з таких технологій - це сорбітізація стали в сипучому графіті. Відомо, що при охолодженні з температури аустенітизації сталей в сипучому графіті можливі мимовільні структурно-фазові перетворення, які дозволяють отримати необхідний рівень властивостей без енерговитрат на процес охолодження. Знання про фазово-структурних перетвореннях в металах базується на їх термодинаміки, механізмі і кінетиці. Кінетику фазово-структурних перетворень характеризують параметри, кінетичні криві і діаграми. Відомо, що сипучий графіт на відміну від рідких (вода, масло, розплавлені солі) і газоподібних (повітря, гази) середовищ є «псевдо твердої» податливою охолоджуючої середовищем, він забезпечує більш рівномірне передачу тепла від металу [9].
Дослідження багатьох вчених показали, що проведене в реальних неізотермічних умовах охолодження зразків дротяної заготовки в середовищі порошкоподібного графіту свідчить про те, що попередня холодна пластична деформація при подальших процесах аустенітизації і розпаду переохолодженого аустеніту сприяє прискоренню зародження центрів продуктів розпаду. В роботі [9] вивчається вплив умов формування сорбітной структури в високовуглецевої катанки шляхом аустенітизації і після-дме охолодження в порошкоподібному графіті. Для цього зразки катанки зі сталі 75 діаметром 6,5 мм, стали 70 діаметром 6,5 мм, стали 75 діаметром 5,5 мм і стали 80 діаметром 5,5 мм нагрівали до 950°С з питомою витягом з розрахунку 1,5 хв/мм перетину, після чого зразки витягували з печі і поміщали для подальшого охолодження в графітовий порошок при кімнатній температурі. Отримані значення мікротвердості підтверджують той факт, що, зі збільшенням вмісту вуглецю в сталі і зменшенням діаметра катанки і при такому способі охолодження, мікротвердість збільшується.
Структура сталі після сорбітізаціі в порошкоподібному графіті складається з сорбіту, структура якого є найбільш бажаною при проведенні даної термообробки. У ході таких досліджень вченими були отримані кінетичні криві перетворення переохолодженого аустеніту в перлітною структури. Кінетичні криві дають підстави для побудови реальних діаграм розпаду переохолодженого аустеніту в неізотерміческімі охолоджуючої середовищі графіту. Такі дослідження свідчать про можливість відмови від токсичних сольових ванн на користь порошкоподібного графіту [10].
Ще одна нетрадиційна технологія термічної обробки високоміцного дроту - це патентування дроту в киплячому шарі. З метою усунення патентування дроту в токсичних свинцевих та вибухонебезпечних селітрових ваннах Уральським політехнічним інститутом, Гіпрометізом і белорецк металургійним комбінатом розроблена технологія і дослідно-промисловий агрегат для патентування дроту в киплячому шарі.
Агрегат являє собою піч для нагрівання дроту довгою 3350 мм і ванну охолодження довжиною 4640 мм, розділені перегородкою товщиною 250 мм. Температура киплячого шару в печі 950°С, а у ванні може регулюватися від 60°С до 500°С [11].
В якості псевдоожіжаемого дрібнозернистого матеріалу в печі та ванні використовували білий корунд з частками розміром 100мкм. Для патентування дроту в киплячому шарі було відібрано понад 50 тонн дроту. Результати досліджень показали, що тимчасовий опір розриву, відносне подовження і відносне поперечне звуження дроту задовольняють вимогам ТУ 93-67 для патентіруемой дроту. Мікроструктура дроту після патентування на установці з киплячому шаром - сорбіт з наявністю невеликої кількості фериту. Також в ході досліджень, вченими Уральського політехнічного інституту було встановлено, що температуру печі з киплячому шаром можна змінювати в широких межах (від 800°С до 1000°С). Зміна температури нагріву значно впливає на структуру і властивості дроту з високовуглецевої сталі. З підвищенням температури киплячого шару збільшується стійкість аустеніту, його перетворення при охолодженні йде при більш низьких температурах, що підвищує дисперсність ферріто-карбідної суміші і зменшує кількість надлишкового фериту. Ці структурні зміни супроводжуються підвищенням міцності властивостей дроту. Найдокладніші порівняльні дослідження показали, що дріт Патентірованний в киплячому шарі, що не відрізняється від патентіруемой в свинці і селітрі не тільки за своїми механічними властивостями, але і по ряду фізичних властивостей.
Ще в 1972 р для виробництва і експлуатації печей ванн з киплячим шаром в Англії була створена фірма «Hudfire Development Limited». Вона розробила установку для патентування дроту в киплячому шарі, що складається з трьох зон [11].
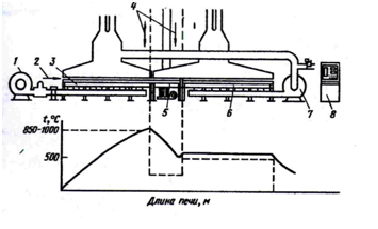
Рисунок 3 - Схема агрегату для патентування дроту в киплячому шарі і зміна температури дроту в процесі її руху через агрегат
Наголошується, що ці печі мають значні переваги перед звичайними, так як спрощується намотування дроту, в чотири рази зменшується довжина печі, знижується окислення дроту, досягається її висока температурна однорідність. У теж час заміна киплячим шаром охолоджуючої селітрової ванни дозволяє усунути відкладення солі на дроті, окислення ванни і очистити атмосферу від шкідливого впливу випаровувань солі [11].
3. Постановка завдання і цілі досліджень
В якості термічної обробки дроту з високовуглецевої сталі застосовується патентування в розплавах солей, яке забезпечує отримання структури сорбіту. Однак патентування в рідких середовищах є дуже трудомістким і енерговитратним процесом. Розплави солей також є дуже вибухонебезпечними і негативно впливають екологію навколишнього атмосфери.
Компромісним рішенням, яке забезпечує зниження Трудоем-кістки і енерговитрат на процес термообробки дроту, а також покращує умови праці на виробництві, є сорбітізація заготовки для дроту в сипучих середовищах.
Тому, мета даної магістерської роботи - це вивчення умов формування структури сорбіту в високоміцного дроту з високовуглецевих сталей шляхом аустенітизації і подальшого охолодження в сипучих середовищах типу порошкоподібного графіту.
4. Матеріали, методика, обладнання для дослідження
Матеріалом для даної роботи послужила дротяна заготівля з холоднодеформованої високовуглецевої сталі 85 з різними ступенями обтиску аж до 75% діаметром 2 мм. Хімічний склад даної сталі наведено в таблиці 1[12].
C | Si | Mn | Ni | S | P | Cr | Cu |
0.82-0.9 | 0.17-0.37 | 0.5-08 | <0.25 | <0.035 | <0.035 | <0.25 | <0.2 |
У дослідах вивчали закономірності охолодження зразків зі сталі 85 в порошкоподібному графіті. Для цього зразки O 2,0 мм і довжиною 30 мм укладали в жароміцні керамічні тиглі, засипали деревним вугіллям, який служив в якості захисного середовища від обезуглероживания і окислення поверхні, і завантажували в нагрівальні електричні печі МП-2УМ, попередньо нагріту до температури 950 ± 10°С і 1000 ± 10°С; загальний час нагрівання і витримки при цій температурі становило 10 хв для повного завершення перліто-аустенітного перетворення і формування однофазного аустенітного стану.
Після закінчення витримки зразки по одному, щоб уникнути втрат тепла швидко переносили в тигель з сріблястим порошкоподібною графітом дисперсностью 6-7 мкм; тривалість витримки в ньому 0 - 12 с; після цього зразки різко охолоджували у воді.
Шліфи виготовляли за стандартною методикою з подальшим їх травленням в 4% -ом спиртовому розчині азотної кислоти. Мікроструктуру зразків вивчали на мікроскопі МІМ - 7 з подальшим фотографуванням; вимір мікротвердості проводили на Мікротвердоміри ПМТ-3 при навантаженні 1 Н.По мікроструктури досліджуваних зразків оцінювали частку перетвореного аустеніту за методом січних (ГОСТ 5639) і будували кінетичні криві перетворення переохолодженого аустеніту в продукти розпаду.
5. Результати досліджень
На рисунку 4 і 5 представлені мікроструктури дроту після сорбітізаціі в порошкоподібному графіті при температурі 950°С і 1000°С відповідно. За мікрофотографій за допомогою методу січних вважали об'ємні частки фаз. За результатами розрахунків були отримані кінетичні криві в координатах відсоток розпаду - час розпаду.
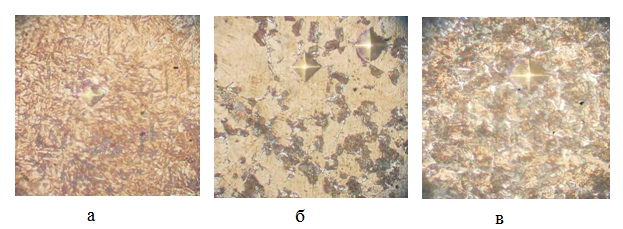
Рисунок 4 - Мікроструктура дроту зі ступенем ПХПД 27% після сорбітізаціі в сипучому графіті, с, 160: а) 1, б) 6, в) 9 при температурі 950°С
Видно, що при витримці протягом 1 с структура складається з мартенситу, отже, розпад ще не почався; при витримці 6 з структура частково складається з мартенситу і продуктів розпаду, т. е. відбувається частковий розпад аустеніту, а при 9 с - повністю із продуктів розпаду, що свідчить про повне завершення процесу розпаду переохолодженого аустеніту.
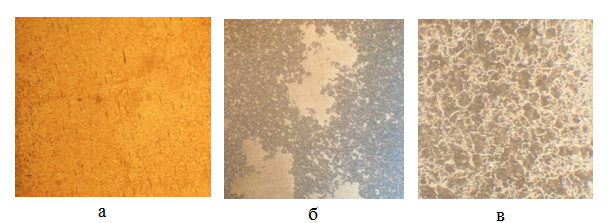
Рисунок 5 - Мікроструктура дроту зі ступенем ПХПД 27% після сорбітізаціі в сипучому графіті, с, 160: а) 1, б) 6, в) 9 при температурі 1000°С
За мікрофотографій за допомогою методу січних вважали об'ємні частки фаз. За результатами розрахунків були отримані кінетичні криві в координатах відсоток розпаду - час розпаду. Кінетичні криві представлені на рисунку 6 і 7.
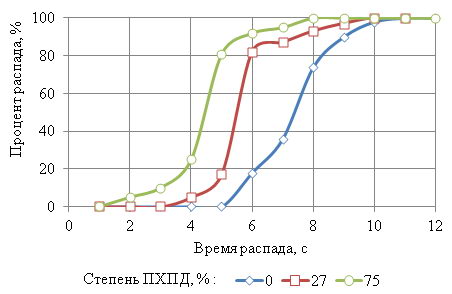
Рисунок 6 - Кінетичні криві дроту після сорбітізаціі в сипучому графіті при температурі 950 ° С
З рисунка 6 видно, що в дроті з ПХПД 0% розпад аустеніту на-чался на 6с, а завершився на 10 с. У дроті з ПХПД 27% розпад почався на 6 с і закінчився на 10 с. А в дроті з ПХПД 75% розпад аустеніту почався на 2 с, а завершився на 8с. Виходить, що розпад переохолодженого аустеніту дроту з ПХПД 0% тривав 4 с, 27% тривав 4 с, а дроту з ПХПД 75% 6 с.
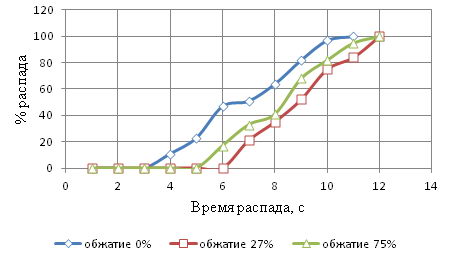
Рисунок 7 - Кінетичні криві дроту після сорбітізаціі в сипучому графіті при температурі 1000°С
З рисунка 7 видно, що в дроті з ПХПД 0% розпад аустеніту на-чался на 4с, а завершився на 11 с. У дроті з ПХПД 27% розпад почався на 7 с і закінчився на 12 с. А в дроті з ПХПД 75% розпад аустеніту почався на 6 с, а завершився на 12с. Виходить, що розпад переохолодженого аустеніту дроту з ПХПД 0% тривав 7 с, 27% тривав 5 с, а дроту з ПХПД 75% 6 с.
Порівнюючи отримані результати після сорбітізаціі при температурі 950 °С з результатами при температурі 900 °С можна зробити висновок, що розпад аустеніту в дроті з ПХПД 0% почався пізніше на 2 с. У дроті з ПХПД 27% розпад аустеніту почався пізніше на 4 с, в дроті з ПХПД 75% розпад почався раніше на 1 с.
При порівнянні результатів після сорбітізаціі при температурі 950 °С і результатів після сорбітізаціі при 1000 °С, видно, що розпад дроту з ПХПД 0% почався однаково на 4с, однак, закінчився пізніше. В дротах з ПХПД 27% і 75% розпад почався і закінчився пізніше.
Далі за допомогою Мікротвердоміри ПМТ-3 при навантаженні 50 грам вимірювали мікротвердість продуктів розпаду переохолодженого аустеніту. Після чого побудували графіки залежності мікротвердості продуктів розпаду від часу ізотермічної витримки, які представлені на малюнку 8.
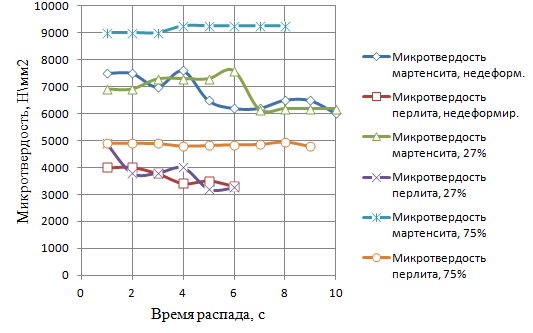
Рисунок 8 - Залежність мікротвердості структурних складових зразків від часу витримки в графіті по степені ПХПД при температурі 950°С
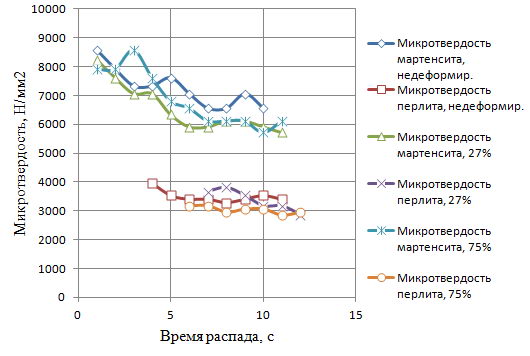
Рисунок 9 - Залежність мікротвердості структурних складових зразків від часу витримки в графіті по степені ПХПД при температурі 1000°С
Таким чином, підвищення ступеня ПХПД призводить до прискорення часу початку розпаду переохолодженого аустеніту в середовищі порошкоподібного графіту, але при цьому збільшує тривалість цього розпаду. Прискорення початку розпаду ймовірно пов'язано з введеними дефектами кристалічної будови, які збільшують кількість місць для зародження нової фази, тим самим знижуючи тривалість інкубаційного періоду.
Порівняння отриманих результатів з даними для розпаду від 900°С свідчить про те, що для недеформірованних і деформованих зразків з малими ступенями обтиску початок розпаду при температурі 950°С загальмовується, в той же час, у сільнодеформірованних зразків початок розпаду фіксується раніше. Це можна пояснити наступним чином. Відомо, що зростання температури аустенітизації сприяє зростанню розміру зерна аустеніту і прискоренню його гомогенізації, в результаті чого ускладнюється його розпад при наступному охолодженні, що і було отримано для зразків з ПХПД 0 і 27%. У разі високого ступеня ПХПД запроваджене більшу кількість дефектів не встигає достатньо знизитися за вказане (10 хв) час витримки і перешкоджає росту зерна і гомогенізації аустеніту, одночасно полегшуючи зародкоутворення при наступному охолодженні. В наслідок цього, розпад аустеніту для зразків з великою попередньої деформацією прискорився.
Висновки
Магістерська робота присвячена актуальній науковій задачі вивчення впливу параметрів аустенітизації на розпад переохолодженого аустеніту високовуглецевої сталі:
- Формування структури сорбіту в високовуглецевого дротяної заготовки шляхом аустенітизації і подальшому охолодженні в безсольових середовищах принципово можливо і потребує детального вивчення.
- На підставі аналізу літературних джерел визначено, що порошкоподібний графіт є актуальною охолоджуючої середовищем для сорбітізаціі, т. к. Дозволяє отримати необхідну структуру і рівень властивостей дротяної заготовки. Також охолодження в сипучому графіті дозволяє економити енерговитрати і поліпшити екологію навколишнього середовища.
- Проведено ряд експериментів з використання середовища порошкоподібного графіту для сорбітізаціі сталі.
- Доцільно більш глибоке вивчення даного питання для пошуку нових та удосконалення старих режимів термічної обробки дротяної заготовки, з метою підвищення і поліпшення механічних характеристик дроту, а також продовження терміну служби.
Подальші дослідження спрямовані на наступні аспекти:
- Якісне вдосконалення застосування середовища сипучого графіту для сорбітізації.
- Адаптація сорбітізаціі в графіті у виробничих умовах.
Список джерел
- Виды и применение проволоки [Электронный ресурс] / Интернет журнал – Режим доступа: http://www.sportobzor.ru/poleznye-sovety/vidy-i-primenenie-provoloki.html
- Рынок металлов: прогнозы старые и новые [Электронный ресурс] / Информационно-аналитический журнал – Режим доступа: http://www.metalbulletin.ru/analytics/color/341/
- ГОСТ 3282-74. Проволока стальная. Технические условия. – Введ. 1974-17-01. – М.: Изд-во стандартов, 1976. – 17 с.
- Циммерман Р. Металлургия и материаловедение / Р. Циммерман, К. Гюнтер; пер. с нем. – М.: Металлургия, 1982. – 480 с.
- Гуляев А.П. Металловедение. Учебник для вузов / Гуляев А.П. – [6-е изд.]. – М.: Металлургия, 1986. – 544 с.
- Жучков С.М. Новая технология и оборудование для повышения качества катанки / С.М. Жучков // Наука та Інновації. – 2007 - № 3. – С. 43 – 49.
- Алимов В.И. Бессолевая сорбитизация проволоки / В.И. Алимов // Металлургия: Сб. науч. трудов. ДВУЗ «ДонНТУ» - Донецк. – 1999. – Випуск 8 (141). – С. 129 – 133.
- Алимов В.И. Влияние режима термообработки на структуру и свойства предварительно ускоренно охлажденной с прокатного нагрева катанки / В.И. Алимов, О.В. Олейникова, Т.С. Коржова // Металлургия: Сб. науч. трудов ДонНТУ. – 2011. – Вып. 13 (194). – С. 170-179.
- Алимов, В.И. Фазовые и структурные превращения при деформационно-термической обработке проволоки / В.И. Алимов, О.В. Пушкина. – Донецк: Донбасс, 2012. – 242 с.
- Пат. на кор. Модель Укр. №65131, МПК С21Д9/52 (2006.01). Спосіб сорбітизації дротяної заготівки для музичних струн в сипучому графіті / Алімов В. І., Туков В. А., Алімова С. В., Максаков А. І., Олейнікова (Пушкіна) О. В., Пономарьова І. В. - № и 2011 06109; заявл. 16.05.2011, Бюл. № 22.
- Башнин Ю.А. Технология термической обработки стали / Башнин Ю.А., Ушаков Б.К., Сеней А.Г. – М.: Металлургия, 1986. – 424 с.
- Сорокин В.Г. Стали и сплавы: Марочник / В.Г. Сорокин, М. А. Гервасьев – М.: «Интермет Инжиниринг», 2001. – 608с.