Abstract on the topic: Improving the conditions forming tubular billets for welded pipes with diameter 1220-1420 mm in the three-roll bending machine "Haeusler" of HTZ-based computer program for calculating the parameters of molding ratsionalnyh
Contents
- Introduction
- 1. Topicality
- 2. The purpose and objectives of the study
- 3. Overview of Research and Development
- 4. Improving calibration for forming 1420x25 mm diameter pipes of steel grade X60 strength
- Findings
- References
Introduction
Production of single-seam large diameter pipes is widespread in our country and abroad, as the world's growing demand for large-diameter welded tubes.
1. Topicality
Improving the quality of the pipe is very important and therefore of HTZ ordered from the company «Haeusler AG Duggingen» Lock and modern three-roll bending machine for the construction of a new production line for gas and oil pipes 711-1422 mm in diameter with one longitudinal seam and wall thickness up to 40 mm. Improving technology forming tubular billets for oil and gas pipes of large diameter is actual scientific and technical problems.
It is also an urgent task is to improve the conditions forming tubular billets for welded pipes with diameter 1220-1420 mm in the three-roll bending machine «Haeusler» JSC HTZ ".
2. The purpose and objectives of the study
The aim is the improvement of conditions for forming tubular billets welded pipe diameter 1220-1420 mm on three-roll bending machine «Haeusler» JSC HTZ-based computer program.
Accordingly, the following objectives: to derive formulas for testing the selected diameter of the pressure shaft and the distance between the lower support shafts. They should ustnavlivatsya: Is there excess of allowable pressures and stresses that considers program. It is also necessary to determine the rational parameters of molding for the production of single-seam welded large-diameter pipes.
3. Overview of Research and Development
Pipe shells made from one sheet to the three-roll bending machine, which rolls are arranged horizontally. Fort movka billets on the bending machine «Haeusler» performed push upper and two lower supporting shafts.
Sheet feeding is carried out on the stopper. Use two stopper plate with built-in limit switches for stopping the sheet to stop. At the time of passage of the sheet under the top sheet of the shaft portions are prepared by uniformly along the length of the residual curvature. The sheet can be bent to any radius, but smaller than the radius of the upper shaft. The required diameter of the tube stock is typically achieved in 3 - 4 passes. The edges of the tube are welded using arc welding [1]
4. Improving calibration for forming 1420x25 mm diameter pipes of steel grade X60 strength
Calculations were carried out on the basis of a specialized computer program created for conditions of modern rolling production. The main window is shown in Figure 1.
The upper part of the window contains background information: diameter of the pipe; wall thickness; parameters characterizing the steel grade; length and width of the sheet.
Diameter, length and thickness of the sheet determined according to the parameters of the finished pipe. Yield point determined depending on the steel grade. The width of the sheet calculated according to the outside diameter and the thickness of the pipe. The distance between the lower rolls determined depending on the diameter of the lower supporting shafts; diameter of the upper shaft - depending on the wall thickness.
The lower part of the window contains the results of calculation. Firstly it is the magnitude of displacements of the upper shaft in each pass. Moreover, as the information given by fully elastic recovery of the sheet, and without it. Also shown are a number of pressures and stresses: in-cylinder pressure relief, the pressure in the support cylinder and the bending stress at the upper roller, which must not exceed the permissible value. In the case of software selection in red is required in accordance with the method of calculations used to take corrective action.[2]
In the process of distance calculation between lower support shafts Xuw can be identified by the machine certificate data, and if they otsutstviya- calculate using the formula:

where Duw - the lower roll diameter, mm;
The relative distance between the lower support shafts can be determined as the ratio:
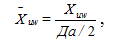
where Da - outside diameter of pipe, mm;
The outer radius of the tube is determined depending on the width of the sheet:
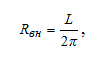
wherein L - the width of the sheet, mm.
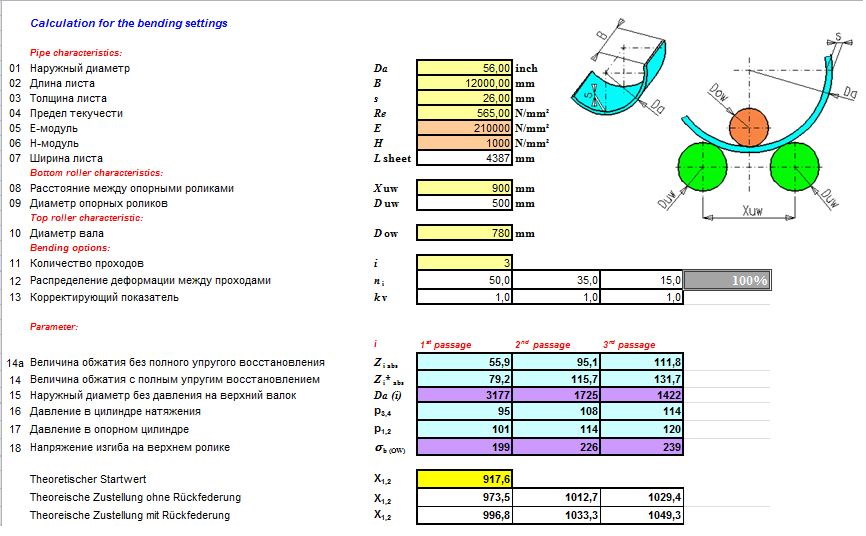
Figure 1 - General view of the working window of the operating conditions forming billets for the pipe diameter of 1420x25 mm of steel grade X60 strength
Figure 1 shows the results of calculations of rational para-meters for molding pipe 1420x25 mm diameter steel X60.
Findings
The work was development of methods of calculation modes forming tubular billets for welded pipes with diameter 1220-1420 mm on the basis of a specialized computer program for three-roll bending machine «Haeusler» JSC HTZ.
It was identified rational parameters forming sheets:
- The amount of movement of the upper shaft in each pass, taking into account the total elastic recovery of the band: the first pass - 79.2 mm; for a second - 115.7 mm; for the final passage of the third - 131.7 mm .;
- The diameter of the workpiece after the first pass of 3177 mm, after the second - 1725 mm, after the third pass of the final diameter of the finished pipe obtain - 1422 mm.
References