Abstract
Contents
- Introduction
- 1. Theme urgency
- 2. Goal and tasks of the research
- 3. Main directions of an intensification of process of thin crushing of minerals
- 4. Improvement of technology and equipment for preparation of Coal-Water Slurry Fuel for the purpose of decrease in specific power consumption of process
- Conclusions and directions of further researches
- References
Introduction
By the end of the last century the world energy crisis started gaining the menacing character as it was spent [1]:
- 87% of world reserves of oil;
- 73% of world reserves of natural gas;
- 2% of world reserves of coal.
Despite significant progress in the field of development of technologies of use of alternative energy sources (solar energy, wind power, sea inflow and so forth), for the next 30 - 40 years the main energy resource there is a coal.
Rather new type of liquid fuel – the Coal-Water Slurry Fuel (CWF) can become a basis of effective replacement of expensive environmentally friendly natural energy carriers (natural gas and oil) soon. Coal-Water Slurry Fuel is a mix of water with particles of coal and special additives. So far the main structure of CWF [2] (masses was defined. %): coal – 70…75, water 24…29, additives – to 1.
Preparation of CWF from slimes or ordinary coal is interfaced to giving of water coal suspension of the acceptable viscosity and static stability. The classical scheme of preparation of CWF developed in the USSR in the mid-sixties provides a grinding of coal and its simultaneous mixing with water in spherical or rod mills. For increase of stability various reagents which at the same time reduced viscosity were added to water-coal fuel. In total it was possible to reach the contents firm in CWF to 60…65%.
In case of transition to burning of CWF instead of coal a number of vital issues is solved [3]:
• range of regulation of productivity of coal package boilers extends;
• ecological indicators when burning coals improve;
• removal of ashes and slimes is transferred to pneumatic transport;
• oxidation (loss of caloric content) of fuel in a storage time decreases;
• there are no potential of explosion and fire danger of coal fuel feeding;
• possibility of burning on one object of different types of coals is provided.
Also such fact is represented interesting: in the USA use of CWF is chosen as part of national power policy, and in Japan and China development of heat and electricity of CWF is estimated in millions of kWh [4].
1. Theme urgency
CWF can be prepared from coals practically of any brands: from long-flame and gas to caking and even anthracites. It is considered that for preparation of CWF river water, sewer drains, water of the coal and mine enterprises and industrial wastes can be used [5].
The classical scheme of preparation of CWF didn't change from the moment of emergence technologists and consists of three stages (fig. 1): crushing (usually to fraction 10…13 mm), a wet grinding (usually to fraction <100…150 microns), classification and homogenization [6].
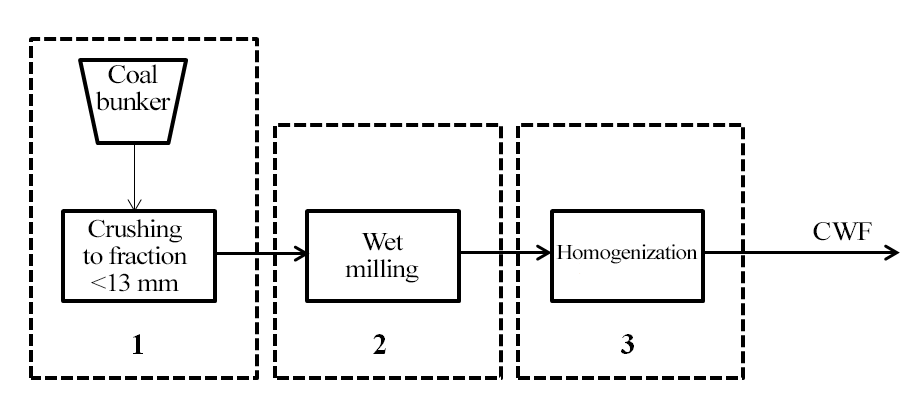
Fig. 1 – Scheme of preparation of CWF
Crushing is carried out by a wet method to fineness 100...150 microns. The stage of crushing is the basic at preparation of CWF as it defines further characteristics of CWF (particle size distribution, viscosity, stability, etc.) [2,3]. Besides, this stage is also the most energy-intensive.
The main technological machines in traditional technologies of preparation of CWF are the spherical or rod mills, vibromills, planetary, hydroshock and cavitational mills which are carrying out crushing in the dry or wet way. The wet method of crushing is more economic since for dry crushing it is necessary to dry up coal previously.
The analysis of researches of thin crushing allows to draw a conclusion that the most effective remedy for receiving a product with particle size distribution of –50 microns at initial food by fineness 2…10 mm and rather small productivity (to 10 t/h) is the vibration mill [7].
Application of vibration mills in comparison with other types of mills allows to reduce an electric power expense, to increase productivity, to reduce wear of grinding bodies and a grinding pipe, to use grinding bodies from various materials, to reach high grinding tannins, to receive purer final product, to carry out process of crushing in vacuum, the inert environment, at different temperatures [8]. Inertial one-pipe, two-pipe and multipipe horizontal vibromills with harmonic uniform oscillations are most widespread on the trajectories close to a circle or an ellipse. However the circular circulation of grinding bodies arising at the expense of a uniform field of trajectories of the movement of the case of a grinding pipe doesn't create rather intensive hashing of grinding bodies and the crushed material. There of stagnant zones (fig. 2) are formed, there is a segregation of grinding bodies and the crushed material that is an essential lack of vibration mills of the specified type [9].

Fig. 2 – The scheme of the movement of the crushed material in a drum vibration mill [9]
The water-coal suspension received at the exit from a mill is subject to control classification (for allocation of particles of coal with a size more optimum) and homogenization, giving to water-coal suspension necessary rheological properties [10]. Larger particles go for recirculation for a repeated grinding.
Industrial use of vibromills for preparation of CWF allowed to establish, what the general specific energy consumption reaches 103 kWh/t [11], and is spent for process of vibrocrushing to 55 kWh/t. And, by optimization of operating modes of the equipment of the line on preparation of CWF, specific power consumption can be reduced to 85…90 kWh/t, but also these sizes are still high.
Thus, decrease in energy consumption by preparation of CWF is an actual task.
2. Goal and tasks of the research
The purpose of this work – development of the technical and technological solutions reducing energy consumption by preparation of CWF.
Main objectives of research:
• to study and analyse the existing approaches to energy saving of process of crushing of minerals;
• to consider and study a vibration mill of new type;
• to investigate advantages of crushing in a biharmonic field of fluctuations in comparison with the harmonious.
Object of research: process of thin crushing of coals and other minerals.
Subject of research: the dynamics of technology and vibratory grinding with biharmonic oscillation mode.
3. Main directions of an intensification of process of thin crushing of minerals
The intensification of process of thin crushing can be carried out in a number of the directions, for example, by use in designs of vibromills of horizontal type of the two-dimensional and three-dimensional difficult fluctuations exciting the variable speed of the movement of the grinding bodies [12] or uses of mills with a non-conventional form of the working camera. These innovations allow "to turbulize" the loading movement, to involve a so-called inactive kernel in process and, eventually, considerably to lower energy consumption of process of crushing [13]. So, in Germany the design of a vibrating horizontal mill with a non-uniform field of fluctuations of working body due to initiation of harmonic oscillations is developed is non-central the installed unbalance vibroactivator [14]. Thanks to essential technological advantages, in comparison with the aligned systems [15], this vibromill was widely adopted when crushing various materials and served as analog for production of identical cars in many countries of the world.
In recent years by pilot studies it is established and with industrial practice it is confirmed that the polyharmonic structure of working impact on the processed technological product is significantly more effective, than idle time harmonious [16]. The spectral structure of the used vibration influences is richer, the reliability of formation in structures of the processed environment of highly effective movements and deformations, resonant and close to the resonant modes, is higher, and the grasp of active volume is wider [17].
ОHowever as a result of complexity of formations the polyfrequency of the modes of fluctuations at this stage of development of vibration equipment as rather simple, but effective decision, biharmonic operating modes can be successfully used.
Thus, the researches promoting development of new designs of the vibromills intensifying thin crushing of various materials have actual character.
4. Improvement of technology and equipment for preparation of CWF for the purpose of decrease in specific power consumption of process
Installation on production of CWF (fig. 3) represents classification crushing complex which enter: the bunker of an initial product 1, a crusher 4 and a vibromill 9 with systems of giving and dispensing of coal 2, a vibrating screen 3, 7 and a hydrocyclone 10 for the main and control classification, capacity 5 and pumps 6.
For coal fraction less than 10 ... 13mm carried raw coal crushing in a hammer mill. If used as raw material coal slurry or coal grain size > 6 mm and 6-13 mm, this step is excluded from the total cooking CWF line.
Fig. 3 – The scheme of a chain of devices of installation on preparation of CWF:
1 – bunker of initial coal; 2 – feeder; 3 – roar (d=12…13 mm);
4 – hammer crusher; 5 – capacity; 6 – pump; 7 – jet drizzling;
8 – ram (d=100 … 150 microns); 9 – vibromill; 10 – battery of hydrocyclones
As the perspective grinding equipment in the technological scheme of preparation of CWF application of essentially new design of a biharmonic vibromill with a non-uniform field of fluctuations of [18-20] (fig. 4) is offered.
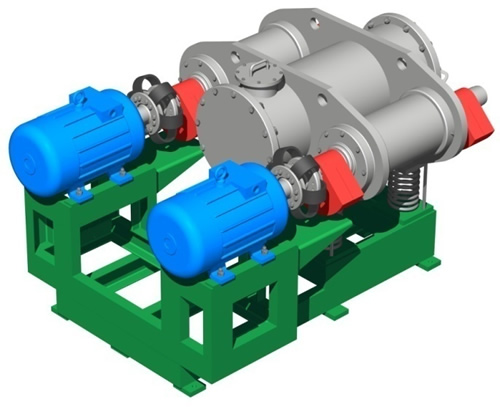
Fig. 4 – a 3D model of an experimental sample of a biharmonic vibromill of new type
The considered vibration mill of new type (fig. 5) consists of the working body including a grinding pipe 1 and grinding bodies 2 which is connected by means of basic elastic elements 3 to the motionless basis 4. The mill is supplied with two unbalance vibro drives 5, each of which includes a power shaft 6 with the individual drive of rotation 7 executed with possibility of independent change of angular speed and the direction of rotation of a power shaft and unbalance 8.
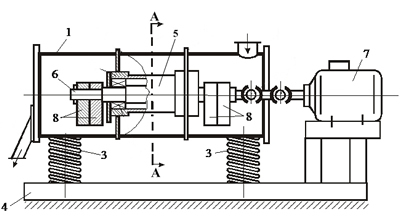
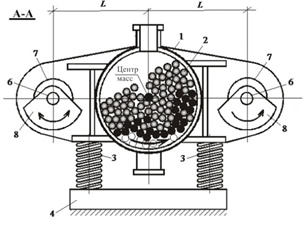
Fig. 5 – the Design of a biharmonic vibromill
By modeling of dynamic processes of a vibromill of biharmonic type it is established [21], that changing rotation frequencies, modules of exciting forces, and also changing the direction of rotation of one of electric motors of the drive of vibroactivators it is possible to operate in the wide range power impact on grinding bodies and the crushed material. It possibilities of a vibromill on creation of rational conditions of process of crushing of the concrete crushed material extend that as a result decrease in power consumption of process of processing is promoted on 20…by 30%.
Conclusions and directions of further researches
Now the increasing development is gained by new technologies of creation and application of CWF. An integral part of the technological scheme of preparation of CWF is coal crushing operation. Numerous researches on thin crushing proved that the most effective remedy for receiving the product meeting the modern requirements imposed to CWF is the vibration mill. The analysis of work of serially let out vibromills with a uniform field of fluctuations showed the increased power consumption of process of crushing of coal by preparation of CWF. It is established that the intensification of process of thin vibrocrushing can go in a number of the directions one of which is realization in designs of a vibromill of the difficult fluctuations exciting the variable speed of the movement of the grinding bodies. The mill design with a non-uniform field of biharmonic fluctuations which operating mode assumes to lower significantly energy consumption on preparation of CWF is developed. Possibly to check this hypothesis after production of an experimental sample of a mill and carrying out technological tests.
Remark
When writing this paper the master's thesis isn't finished yet. Final end - December, 2015. The full text and materials on a subject can be received at the author or his head after the specified date.
References
- Овчинников Ю.В. Искусственное композиционное жидкое топливо из угля и эффективность его использования / Ю.В. Овчинников, С.В. Луценко. Новосибирский государственный технический университет //[ Электронный ресурс].
- Круть О.А. Водовугільне паливо: Монографія [Текст] / О.А. Круть // – Київ: Наукова думка, 2002. – 169 с.
- Морозов А.Г. Гидроударные технологии для получения водоугольного топлива [Текст] / А.Г. Морозов, Н.В. Коренюгина // Новости теплоснабжения, №7, 2010. – С. 18–21.
- Жидкий уголь. Водоугольное топливо [ Электронный ресурс].
- Углепровод Белово–Новосибирск [ Электронный ресурс].
- История ВУТ в России[ Электронный ресурс].
- Vibrating mills for brown coal [Text] // “Colliery Guard.”, 1980, 228, №1. – P.32.
- Мельницы вибрационные ООО "Вибротехцентр–КТ"[ Электронный ресурс].
- Потураев В.Н. Технологические испытания вертикальной вибрационной лабораторной мельницы МВВЛ–3 [Текст] / В.Н. Потураев, В.П. Франчук, А.А. Тарасенко, П.П. Королев // Проблемы вибрационной техники: Мат. науч. семинара ИГТМ АН УССР. – Киев: Наукова думка, 1970. – С. 181–187.
- Жидкий уголь. Приготовление [ Электронный ресурс].
- Жидкий уголь. Использование вибромельниц для приготовления ВУТ [ Электронный ресурс].
- Овчинников П.Ф. Новое оборудование для измельчения [Текст] / П.Ф. Овчинников, Н.Д. Орлова // Материалы конф. «Теория и практика процессов измельчения и разделения». – Одесса. 1994. – С. 36–40.
- Арсентьев В.А. Методы динамики частиц и дискретных элементов как инструмент исследования и оптимизации процессов переработки природных и техногенных материалов [Текст] / В.А. Арсеньев, И.И. Блехман, Л.И. Блехман, Л.А. Вайсберг, К.С. Иванов, А.М. Кривцов // Обогащение руд. 2010. №1. – С. 30–35.
- Патент ФРГ на изобретение № 3224117 [Текст]. В02С 19/16. Заявл. 29.06.1982.
- Gock E. Eccentric vibratory mills – theory and practice [Text] / E. Gock, K.–E. Kurrer // Powder Technology. 105. – 1999. S. 302–310.[ Электронный ресурс].
- Букин С.Л. Интенсификация технологических процессов вибромашин путем реализации бигармонических режимов работы [Текст] / С.Л. Букин, С.Г. Маслов, А.П. Лютый, Г.Л. Резниченко // Збагачення корисних копалин: Наук.–техн. зб. – 2009. – Вип. 36 (77) – 37 (78). – С. 81–89.
- Гончаревич И.Ф. О повышении производительности и рентабельности промышленных нанотехнологий. М.: РИА. Секция «Горное дело». – 2010. [ Электронный ресурс].
- Патент України на винахід. №100756. Вібраційний млин [Текст] / С.Л. Букін, А.С. Букіна // Заявка а 2011 01521, В02С 19/16. Бюл. №15, 2012 р.
- Патент Российской Федерации на изобретение №2501608. Вибрационная мельница [Текст] / С.Л. Букин, А.С. Букина // Заявка 2012104105/13, В02С 19/00. Бюл. №35, 2013 г.
- Букін С.Л. Нова конструкція бігармонійного вібромлина для тонкого подрібнення різноманітних матеріалів [Текст] / С.Л. Букін, А.С. Букіна // Збагачення корисних копалин: Наук.–техн. зб. – 2012. – Вип. 50 (91). – С. 60–65.
- Букин С.Л. Динамические возможности инерционной бигармонической вибромельницы нового типа [Текст] / С.Л. Букин, А.С. Букина // «Прогресивні технології і системи машинобудування: Міжн. зб. наукових праць». – Донецьк: ДонНТУ, 2013. Вип. 1– 2 (44–45). – С.61–71.