- 1. Relevance of the topic
- 2. The purpose and objectives of the study
- 3. Argon and Nitrogen
- 4. The use of an inert gas
- 5. Conclusion
- List of sources
1. Relevance of the topic
The solution to this task quite priorietny because they involve two manufacturing such important factors as: the temperature control and flow rate of the inert gas.
2. The purpose and objectives of the study
The aim of the study is the analysis by the use of literary sources and existing knowledge influence blowing inert gases in the steelmaking technology, thereby to show the spectrum of use of inert gases in the present converter production.
3. Argon and Nitrogen
Method of improving the quality of metal, inert purge gases received spread industrial development as argon cheap ways to obtain large quantities as a by-product in the production of oxygen. As it is known, in air for about 1% of argon. On oxygen stations Argon is isolated by distillation of liquid air. Given the small argon expenses, if the factory purse oxygen stations simultaneously resulting volume with argon sufficient to handle large amounts of steel. In those countries where there are reserves of helium, helium is also used to purge. To purge the metal containing no nitridoobrazuyushih elements (chromium, titanium, vanadium, etc.), nitrogen is often used. In the interval 1550-1600 ° C, the process of dissolution of nitrogen in liquid iron does not receive a significant development. In the USSR, for metal and widely used blowing argon and nitrogen (typically, the term "inert gas purge" is meant use and argon and nitrogen).
4. The use of an inert gas
Modern technology steelmaking commonly used inert gas at all stages of the process. The gas used for purging the combined metal in the converter. Feed it through the bottom of the converter provides a complete implementation of the oxidation of carbon in the unit. In recent years, its use has become part of applying a protective lining on the ledge at the top of a purge. Supply of argon or nitrogen through special blowing device in the bottom of the bucket simultaneously performs two functions: gas dissolution and promotes uniform distribution of alloying elements and ferroalloys in volume of the metal bucket. Thus formed under the influence of non-metallic inclusions of bubbles successfully captured particles of slag, helps cleanse the metal. Schematically, the interaction of a gas bubble and the liquid is presented in the image (pic. 1), the left drawing according Boitchenko characterizes nucleation, bubble growth and separation. As a result of its interaction is the formation of directed metal flow, contributing to its refining.
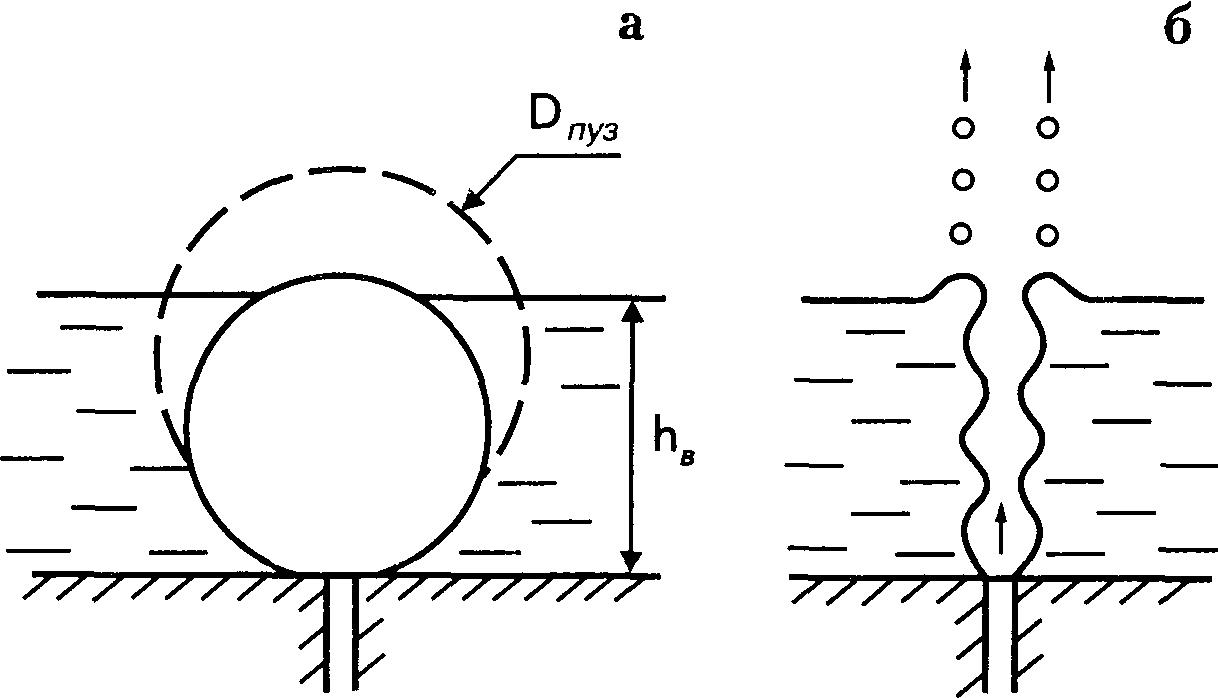
Picture 1 – Interaction of the gas bubble at the bottom purge
The right figure characterizes the least efficient from the standpoint of refining bath purge mode. The most effective bottom blowing inert gas has when achieved the largest area of ??contact between the metal and the gas bubbles. The combination of these parameters is reasonable only for a certain type of unit with inherent hydrodynamics. Apparatus for supplying different gas manifold designs. They operate as porous plugs of refractory material. This provides simultaneous output of a blower of parallel jets of gas bubbles. Additional crushing gas flow promotes the use of several concurrent purge plugs. In particular this applies to steel ladles. The intensity of the production program in the steelmaking shop compels the use of the inert gas on the "ladle-furnace". There is concentrated a number of technological methods, that run fully manage only through metal inert gas purge. The now customary use of metal blowing in tundish is a testament to the fact that at one stage of the process is not fully realized refining purge capabilities. Reserve a gas purge mode on the "ladle-furnace". A wide range of gas flow changes (100-1000 l / min) can not be fully realized because the gas is forced to flow decreases before metal casting. By this time, all operations on doping and deoxidation completed. The metal layer is formed by the slag. From the analysis of the literature shows that the metal refining process of non-metallic inclusions in time exceeds the residence time of the metal on the "ladle-furnace". In the process of metal casting transmission delay on the inert gas flow rate is reduced internally. This is primarily due to the fact that the cooling process of metal in the ladle begins. Minimize heat loss fails realizing alternately supplying gas at different purge plugs, while its consumption does not cause the formation of spots blowing, facilitating greater cooling of the metal.
5. Conclusion
Therefore, an urgent task is through physical modeling in a transparent model ladle definition of allowable management inert gas flow to preserve the functions of refining and prevent loss of heat in a ladle before casting.
List of sources
- Явойский В.И., Дорофеев Г.А., Повх И.И. Теория продувки сталеплавильной ванны. – М.: Металлургия, 1974. – 495с.
- Охотский В.Б. Физико-химическая механика сталеплавильных процессов. – М.: Металлургия, 1993. – 150 с.
- Бойченко Б. М., Охотский В. Б., Харлашин П. С. Конвертерное производство стали. – Днепропетровск: РИА «Днiпро-ВАЛ», 2006. – 454 с.