Реферат
Содержание
Введение
Современные переплавные процессы получения высококачественных слитков для авиаракетостроения, энергетики и прочих отраслей техники осуществляют плавление металла в водоохлаждаемых медных кристаллизаторах. К таким процессам можно отнести электрошлаковый (ЭШП), вакуумнодуговой, электроннолучевой, плазменный и другие переплавы. Качество получаемого слитка, в таких процессах, во многом определяется формой и размерами жидкой металлической ванны, поэтому контроль данных параметров в процессе переплава актуален. В настоящий момент существует множество универсальных программных продуктов для моделирования физических процессов, в том числе и кристаллизации слитка, которые позволяют задать условия тепловыделения и кристаллизации и оценить форму и размер металлической ванны. Многими научными коллективами разрабатываются собственные тепловые модели переплавных процессов .
Преимущества математического моделирования бесспорны, однако для получения достоверного результата необходимо иметь точные значения граничных условий теплообмена. В качестве таких, в данной работе, предлагается использовать температуру стенки кристаллизатора со стороны охлаждающей воды, для чего предлагается закрепить по её высоте некоторое количество термопар через равные расстояния между ними. Для снижения трудоёмкости и повышения наглядности исследований, отработку технологии крепления термопар на поверхности стенки кристаллизатора решено проводить вначале на физической модели ЭШП. В качестве расходуемого электрода в ней будет выступать электрод диаметром 20 мм из сплава Вуда, с температурой плавления около 80°С. В качестве шлаковой ванны, будет выступать раствор соляной кислоты, разогрев которой будет происходить под действием протекающего через неё электрического тока.
Задачей, которую предстоит решить на первом этапе исследования, является доработка существующей физической модели ЭШП, которая имеет ряд недостатков и не подходит для решения задач измерения температуры. Так, в существующей модели ЭШП, плавление электрода из сплава Вуда осуществляется в стеклянном сосуде диаметр, которого значительно превосходит диаметр расходуемого электрода, что не соответствует реальным значениям коэффициента заполнения кристаллизатора . Существенным недостатком имеющейся модели, является слабый теплоотвод от "шлаковой ванны", в результате которого имеется существенная её тепловая инерция. Для приближения условий охлаждения шлаковой ванны и слитка к реальным, необходимо организовать её водяное охлаждение.
Модель кристаллизатора
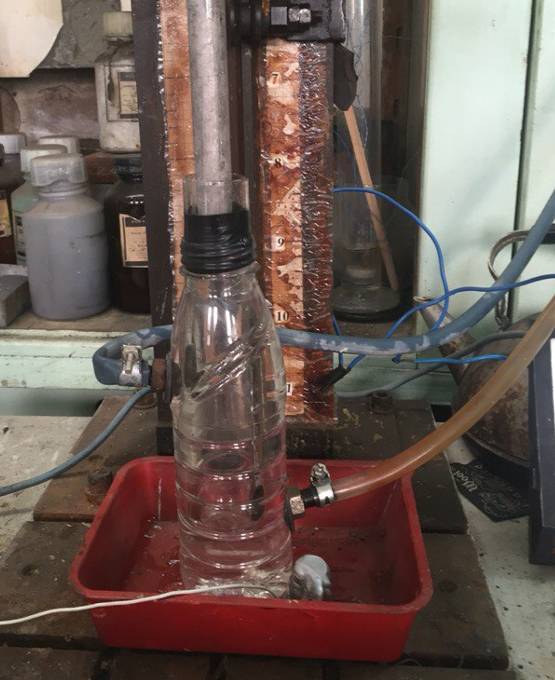
Для проверки возможности перегрева ванны электролита в условиях её охлаждения водой собрали простую конструкцию, состоящую из стеклянной колбы диаметром 20 мм, и пластиковой бутылки объемом 0,5 литра (Рис. 1). Стеклянная колба выполняет роль гильзы кристаллизатора и в ней осуществляется плавление сплава Вуда в электролите. Она герметично запрессована в пластиковую бутылку, в которой имеются патрубки для подвода и отвода охлаждающей колбу воды. На дно колбы помещена металлическая шайба диаметром немного меньше диаметра колбы, к которой с помощью изолированного провода подсоединена одна клемма источника питания. Вторая клемма подсоединена к переплавляемому электроду из сплава Вуда . Плавление электрода осуществляли на лабораторной установки ЭШП, которая имеет механизм крепления и перемещения электрода, источник питания, приборы для контроля тока и напряжения переплава. Перемещение электрода осуществляется автоматически, путем задания необходимой скорости и направления движения. Напряжение переплава можно плавно задавать в пределах от 0 до 25 В. Максимальный ток переплава составляет около 20 А. Высота электролита в колбе составляла 3 см. После заглубления электрода в электролит произошел его быстрый разогрев в течении 1-2 мин и начался процесс плавления. Тепловая инерция ванны из электролита уменьшилась, чего мы и добивались. Вместе с тем, температура охлаждающей воды практически не изменилась, что связано с низкой теплопроводностью стеклянной колбы. Таким образом, результаты практического эксперимента показали, что выделяющегося в электролите тепла достаточно для расплавления электрода из сплава Вуда в условиях охлаждения колбы проточной водой (Рис. 2). Однако теперь, требуется проверить разогрев электролита в условиях его разогрева не в стеклянной колбе, а в кристаллизаторе с металлическими стенками. В настоящий момент ведутся работы по созданию модели кристаллизатора, в которой две противоположные стенки будут выполнены из стали и будут охлаждаться водой, а две других будут выполнены из толстостенного стекла и будут в контакте с воздухом. К металлическим водоохлаждаемым стенкам кристаллизатора будут крепится термопары, а через стеклянные – вестись наблюдение за процессом плавления и кристаллизации металла.
Результат проведенного опыта
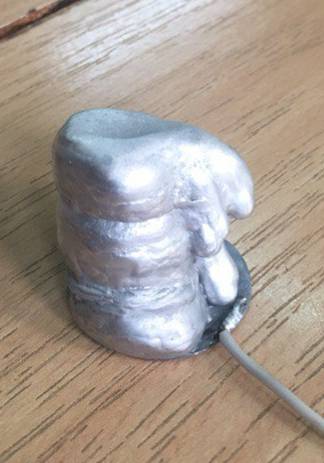
Литература
1. Multiphase modelling slag region in the ESR process / A. Kharicha, W. Schutzenhofer, A. Ludwig, R. Tanzer // International Symposium on Liquid Metal Processing and Casting, Nancy, – 2007. – P. 107-111.
2. Minisandram R., Arnold M., Williamson R. VAR pool depth measurement and simulation for a large diameter Ti-6Al-4V ingot // International Symposium on Liquid Metal Processing and Casting, Santa Fe, 2005, P. 1-6.
3. Hernandez-Morales B., Mitchell A. Review of mathematical models of fluid flow, heat transfer, and mass transfer in electroslag remelting process // Ironmaking and Steelmaking, 1999. – Vol. 26. – № 6. – P. 423-438.