Abstract
Content
- Introduction
- 1. Theme urgency
- 2. Goal and tasks of the research
- 3. Variable frequency drive description
- 3.1 Construction of a converter with direct coupling
- 3.2 The construction of a converter with a clearly expressed intermediate DC link
- 4. Vector control
- 4.1 Causes of appearance
- 4.2 Mathematical apparatus
- 4.3 Variants of modes of operation of vector control
- Conclusions
- List of sources
Introduction
At present, the state of the elevator economy. It is required to increase the security conditionsand trouble-free operation. Also an important factor. This forms the need for a revisionand modernization of existing equipment.
In elevators and freight lifts, the types of electric drives are selected depending on the speed of movement, the number of storeys and the required accuracy stop.
The use of the existing elevator park has a number of problems and shortcomings. Long service life led to a strong wear of moving parts of the elevator. In particular, the electric motor already wears out the insulation of the stator windings and the breakdown of the bearings. And the erasing of the brake pads and the grinding of the gears of the gears has long touched the winch reducer. This whole complex problems requires a reliable and economic solution.
1. Theme urgency
A modern city is not conceivable without multi-storey houses, and a modern house is without an elevator. The height of the house now directly affects the complexity of the elevator installation. Now, elevators are beginning to apply to elevators. With an increase in the number of floors, the speed of movement must increase, therefore, smooth acceleration and braking are required. The old technical means, which were used in houses of medium height, can not provide this.
Modern requirements are also advanced to the lifting capacity. The load on the motor drive must vary over a wide range. But the speed of movementlift and acceleration, for acceleration and braking, must remain constant. That is, do not react to any significant changes in the load.Much important are the issues of saving energy, repair work and extending the life of the main drive units. This master's work is dedicated tosolving these problems by introducing a frequency-controlled drive with partial or complete equipment upgrades.
2. Goal and tasks of the research
The main goal of the work is to improve operational and economic performance by introducing a frequency-controlled electric drive.
The main objectives of the study:
- Increase the overall safety level of the elevator installation.
- Reducing the likelihood of inter-turn short-circuiting by reducing the starting current.
- A significant reduction in the impact load on the bearings due to the smoothness of the acceleration and deceleration processes.
- Increase in the total service life of moving parts due to the absence of shock and vibration phenomena.
- Use a winch equipped with a single-speed, rather than a two-speed electric motor.
Object of study : frequency-controlled drive system, which includes a frequency converter and an elevator winch, equipped with a single-speed asynchronous motor.
Within the framework of the master's work, it is planned to receive actual scientific results in the following areas:
- Achieving comfortable movement of the elevator car, due to effective control of torque and speed on the output shaft of the electric motor.
- Reducing the cost of consumed electricity by leveling the transients at the time the engine starts.
3. Variable frequency drive description
Frequency-controlled drive - is a system for controlling the rotational speed of the rotor of an asynchronous (or synchronous) electric motor. It consists of the actual electric motor and the frequency converter.
A frequency converter (or frequency converter) is a device that consists of a rectifier (DC bridge) and an inverter(converter). The rectifier converts the alternating current in the industrial current.
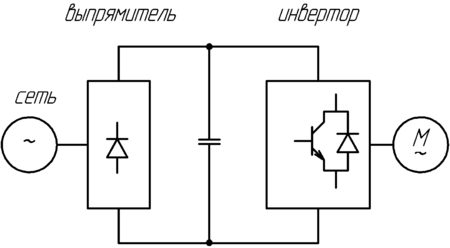
Picture 1 – Functional scheme of the frequency converter, made according to the voltage source scheme
Output thyristors (GTO) or transistors IGBT or MOSFET provide the necessary current for the motor power supply. To avoid overloadingconverter with the long feeder between the converter and the feeder.
With scalar control. Vector control is a method for controlling synchronous and asynchronous motors,not only forming harmonic currents, but also providing control of the magnetic flux of the rotor (torque on the motor shaft).
3.1 Construction of a converter with direct coupling
A frequency converter with direct coupling is a device that is a controlled rectifier. Groups of thyristors alternatelyare unlocked by the control system and the stator winds of the motor. Due to this, the converter output voltageis formed from the "cut out" sections of the sinusoid of the output voltage. The frequency of the output voltage can not be equal to or higher than the frequency of the mains.Its range is from 0 to 30 Hz. This results in a small range of engine speed control. In modern frequency-controlled drives,with a wide range of adjustment parameters.
The converter's cost increases the use of non-locked thyristors, for complex control systems. In inverters with direct couplingThe cut
sine wave at the output is a source of higher harmonics. These harmonics cause additional losses in the electric motor,overheating of the electric machine, the overpowering of the electric supply.
The use of compensating devices, to solve these problems, leads to an increase in cost, size, weight and a decrease in system efficiency.
3.2 The construction of a converter with a clearly expressed intermediate DC link
In modern frequency-controlled drives, the most used converters with a proncentdirect current. The use of electric energy. Initially, the inputthe sinusoidal voltage is rectified in the rectifier and filtered by a filter, and then converted again by an inverter into an alternating voltagevariable frequency and amplitude.
Double energy conversion. However, converters with a pronouncedDC DC link have the widest application in comparison with converters using direct communication.
4. Vector control
Vector control - is a method for controlling synchronous and asynchronous motors, not only forming harmonic currents (voltages) phases (scalar control), but also providing control of the magnetic flux of the rotor. The use of rotor position (speed) sensors is mandatoryfor the first realizations of the vector control principle and algorithms of increased accuracy.
The interaction of the control device with the space vector
, which rotates with the frequency of the field of the motor and is vector control
.
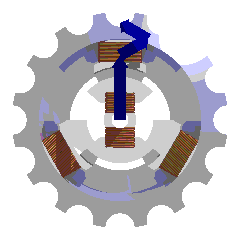
Rotating magnetic field
4.1 Causes of appearance
The reason for the appearance of vector control is that the induction of motor vehicle with a squirrel cage (ADC) is not easily controlled by speed regulation. ADCZ - is the most massive and cheap in the manufacture of an engine. He is also reliable and not demanding in operation. The construction of the ADPC allows not usingmechanical collectors and contact rings.
Initially, the asynchronous motor was used for unregulated drives, as well as for drives with mechanical adjustment. Special multichannel ADCS onlystepwise allowed to change the speed (from two to five steps). However, such a control system cost much more expensive, since a control station was required. With all this it was not possible to automatically maintain the speed of the engine.
Later, a method for scalar control of the engine speed control was developed. However, in the transient processes with scalar regulation, the flux coupling of the rotor changes,which leads to a decrease in the rate of change in the electromagnetic moment, which leads to a deterioration in the characteristics of the dynamics. This is due to changes in the stator and rotor currents.
Unlike the ADPC, the DC motor (DCT) is easy to control. Adjustment can be carried out as a change in the voltage at the anchor with a constantflow of energy, at the excitation of the wind. But DPT has a high cost, operational costs and lower reliability.
The idea of vector control was the creation of such an ADCZ control system, in which, like DPT, it is possible to separately control the moment and magnetic flux, while maintainat a constant level, the flux of the rotor, and, hence, the change in the electromagnetic moment.
4.2 Mathematical apparatus
For SD and AD, the vector control principle can be formulated as follows. Initially, the system of differential linear equations in the system of equations of the generalized two-phase machine, which has two phases (located spatially 90 ° relative to each other) on the stator and two phases on the rotor, also mutually arranged. Then all the vectors are described by this system, on the rotor axis, while the arbitrarily rotating orthogonal coordinate system the greatest simplicity of the equations, the equations of energy, and the like on the DPT equations, the projection of all vectors on the field of orientation. In fact, the second stage in the formation of quantities, two-phase generalized machine (two on a stator and two on a rotor) with one pair of mutually perpendicular windings. In addition to characteristics, close to the characteristics of the DCT, the ADCZ with field orientation has the maximum permissible speed for controlling the moment flux linking.
The alignments of the electromagnetic processes are recorded with respect to the stator currents and the rotor flux linkages in a synchronous orthogonal coordinate systemrotors have the form:
Picture 2 – Equations of electromagnetic processes
Where:
Ls, Lr, Lm — stator inductance, rotor and mutual; Rs, Rr — respectively, the active resistance of the stator and rotor; Id, Iq — projections of currents on the d and q axes; Tr — rotary chain time constant.
There may be two variants of the method:
- Orientation on the rotor field.
- Orientation along the field of the main flux linkage.
The supply of the AD and LED in the vector control mode is carried out from the an inverter that can be provided at any time the required amplitude and angular position of the vectorvoltage (or current) of the stator. Measurement of the amplitude and position of the vector of the rotor's flux-linkage is made with the help of an observernon-measurable parameters of the system).
4.3 Variants of modes of operation of vector control
Vector control determines the presence in the control link of the mathematical model (hereinafter - MM) of an adjustable electric motor. Depending on the operating conditions of the drive, control is possibleelectric motor in both modes.
In connection with the foregoing, it is possible to classify the control modes by the accuracy of the MM motor used in the control link:
- Using MM without additional specifying measurements by the motor parameter control device (only typical motor data entered by the user is used).
- The use of MM with additional refinement measurements by the motor parameter control device (i.e., active and reactive stator / rotor resistances, motor voltage and current).
Depending on the presence or absence of the speed feedback sensor (speed sensor), the vector control can be divided into:
- Motor control without speed sensor - the control unit uses the MM data of the motor and the values obtained when measuring the stator and / or rotor current.
- Motor control with a speed sensor - this device uses not only the values obtained when measuring the stator current and / or the motor rotor (as in the previous case), but also the data on the speed (position) of the rotor from the sensor, which in some control tasks allows increasing accuracy of working out by the electric drive of the task of speed (position).
Conclusions
By introducing a frequency-controlled drive, with a single-speed asynchronous motor, to an elevator installation, we obtain an efficientvehicle traffic control. This leads to increased reliability and service life, and gives the following results:
- All mechanical structures do not experience excessive electrodynamic loads, since the entire drive systemideal S-shaped mode of braking and acceleration.
- The motors accelerate and brake at currents several times smaller than with a two-speed version.
- The braking system does not actually wear out. This was facilitated by the fact that the brake pads are superimposed on the brake discat the rotational speeds of the electric motor, which are almost equal to zero.
- Moving the cockpit smooth, without sharp jerks and stops, which ensures safety and accuracy of movement.
- In a frequency-controlled drive, the motors provide the specified torque at any speed.
- Loading the cab does not affect the comfort when driving.
- The stop is not controlled by a brake, but by a change in frequency and voltage.
Modernization of the elevator installation based on the use of a frequency-controlled drive is an excellent way to increasequality of functioning.
This master's work is not completed yet. Final completion: June 2018. The full text of the work and materials on the topic can be obtained from the author or his head after this date.
List of sources:
- Требования, предъявляемые к лифтовым системам: http://drives.ru.
- Модернизация электроприводов лифтов преобразователями частоты: http://drives.ru.
- Частотно-регулируемый привод, принцип действия, структура: http://www.softstarter.ru.
- Частотный преобразователь (электропривод): https://ru.wikipedia.org.
- Частотные преобразователи: структура, принцип работы: http://www.softstarter.ru.
- Векторное управление асинхронными и синхронными двигателями: https://ru.wikipedia.org.
- Описание векторного управления: http://engineering-solutions.ru.
- Энергосбережение и энергосберегающие технологии: https://www.siemens-pro.ru.