Реферат за темою випускної роботи
Зміст
- ВСТУП
- 1. АКТУАЛЬНІСТЬ ТЕМИ
- 2. АНАЛІЗ ІСНУЮЧИХ СПОСОБІВ І ОБГРУНТУВАННЯ ПРИЙНЯТИХ РІШЕНЬ
- 2.1. Пресування, як один із способів переробки дискретних матеріалів.
- 2.2 Пресування сипучих матеріалів
- 2.3 Теплові процеси при холодному пресуванні дискретних матеріалів
- 2.4 Особливості деформування дискретних матеріалів
- 3. АНАЛІЗ пресованої ДИСКРЕТНИХ МАТЕРІАЛІВ
- 3.1 Схеми і конструктивний аналіз пресового обладнання
- СПИСОК ЛІТЕРАТУРИ
Мета магістерської роботи полягає в дослідженні пресування дискретних матеріалів для удосконалення пресового устаткування. У промисловості дисперсні системи займають надзвичайно важливе місце в зв'язку з їх поширенням і різноманітним застосуванням, винятковою роллю в природних явищах і процесах, в повсякденному техногенної діяльності людини і разом з тим в зв'язку з досить специфічними фізико-механічними властивостями.
З появою нових інноваційних ідей, прогресивних ресурсозберігаючих технологій і нової техніки важливим аспектом науково-технічного прогресу є поява нових способів отримання матеріалів і виробів із заданими або принципово новими властивостями, параметрами і якістю.
Пресування часто є основним процесом при отриманні дисперсних матеріалів, таких, як бетони, лакофарбові матеріали, високонаповнені гуми і пластики, гетерогенні тверді ракетні палива, керамічні і металокерамічні матеріали, папір та картон, штучні шкіри і безліч інших матеріалів [3]. Актуальним також є пресування вугільних шламів і дрібних класів вугілля. Отримані брикети можуть бути використані в якості палива для спалювання в побутових і промислових топках. Пресування вугільного пилу і подрібненої вугільної фракції виконується на двох-валкових пресах.
В залежності від виду вугілля і сполучного в технології буває необхідно спеціальним чином охолоджувати і витримувати готовий брикет деякий час в спеціальних бункерах, протягом якого брикет набуває міцність. Час витримування індивідуально і визначається на етапі тестування. Паливний брикет має високі споживчі властивості, підвищує економічну ефективність роботи підприємства при раціональному використанні його вторинних вугільних ресурсів. У більшості випадків процес брикетування вугілля відбувається з додаванням сполучного (вугільний пек, нафтовий бітум, смола, меляса та вапно, лігносульфонат, крохмаль, полімери.) Що робить брикет більш високої якості. В окремих випадках брикетування можливо також і без сполучного, але при цьому значно підвищуються енерговитрати. Основними перевагами є висока продуктивність, низьке питоме енергоспоживання, висока надійність, довгий горіння, сталість температури при згорянні. Розглянемо процес пресування на прикладі отримання вугільних брикетів (Рис 1.).
З зневодненого вугільного шламу і / або вугільної дрібниці з вмістом води з додаванням лігносульфонату (сухого або рідкого), в результаті чого отримують бездимний, міцне і водостійке паливо. Запропонований спосіб забезпечує зниження первинних капітальних витрат, зменшення споживаної при виробництві енергії, підвищення продуктивності, поліпшення споживчих властивостей паливного брикету за рахунок підвищення його міцності, водостійкості і повноту вигорання вугілля в брикеті.
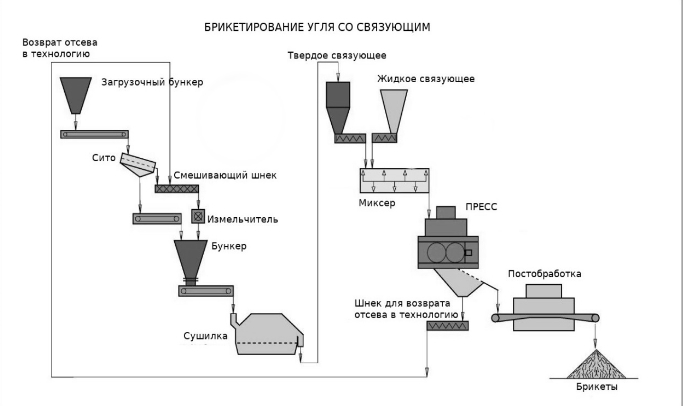
Спосіб отримання вугільних брикетів [2] включає зневоднення вугільного шламу, перемішування вугільних частинок і мінеральної складової вихідного шламу, подальше формування збезводненої зазначеної маси з гранулометричним складом; додатково вугільний шлам містить не менше 25% спікливих вугілля. При цьому отримують брикет міцний, пористий, водостійкий, з малим вмістом вологості, органічних і летючих речовин, який має раціональну формоутворювальну поверхню. Висока механічна міцність, водостійкість брикетів з вугільного шламу забезпечують його хороше збереження при транспортуванні і при несприятливих атмосферних впливах. Крім того, брикет має теплотворну здатність вище, ніж у вихідного шламу, що пов'язано зі зниженим вмістом в ньому вологості, органічних і летючих речовин при термообробці. Пористість брикетів забезпечує повне вигорання вугілля при спалюванні брикетів. При згорянні брикету забезпечує знижений вміст викидаються в атмосферу шкідливих речовин. Брикети можуть використовуватися в енергетичних цілях і в комунально-побутовому секторі, а зольний залишок у будівництві та інших галузях. Вугільний брикет містить мінімальну кількість шкідливих речовин, і забезпечує виняткову екологічну безпеку при використанні. Вугільний паливний брикет - екологічно чистий продукт і горить практично бездимний, він є хорошим паливом для використання в житлових приміщеннях. Добавки в брикети призначені для підвищення їх екологічності (пов'язуючи з'єднання сірки в зольному залишку) і поліпшення споживчих якостей (колір горіння, запах).
Пресування сипучих матеріалів - фізико-механічний процес, заснований на властивості сипучих тіл ущільнюватися під дією зовнішнього навантаження. Сипучий матеріал складається з двох фаз: твердої, що містить деяку кількість вологи; газоподібної, що заповнює простір між частками. Кількісне співвідношення цих фаз до пресування і після пов'язане з отриманням продуктів пресування (гранули, брикети) необхідної міцності. У зернопереробної промисловості пресування піддають висівки, лушпиння і комбікорми. Процес отримання великих пресованих брикетів носить назву брикетування, дрібніших-гранулювання.
Існує ряд гіпотез, що пояснюють процес пресування сипучих матеріалів (капілярна, колоїдна, молекулярна та ін.). Найбільший інтерес представляє молекулярна гіпотеза, заснована на термодинамічної теорії аутогезии, згідно з якою об'єднання частинок відбувається під дією молекулярних сил. Величина сил молекулярного тяжіння залежить від природи контактуючих поверхонь і їх геометричній характеристики. Дія сил молекулярного тяжіння при зближенні частинок проявляється практично миттєво. Тиск пресування необхідно для зближення частинок і створення достатнього числа контактів між ними.
Число контактів залежить від дисперсності пресованого матеріалу. Тому за інших рівних умов тонке подрібнення вихідних матеріалів дозволяє отримувати більш міцні гранули. На міцність гранул і питомі енерговитрати впливає довжина шляху основного етапу - пресування (циліндрична частина фільєри). Чим більше довжина фільєри, тим міцніше виходять гранули і менш проявляються їх релаксіонние властивості. На характер процесу дуже впливають вологість пресованого матеріалу і величина зазору між матрицею і роликами. Біохімічні зміни при пропарюванні і пресуванні зводяться до деякої зміни співвідношення крохмалю, білків, активності ферментів і вітамінів.
В початковий період пресування до товщини брикету [4], продукт стискається без особливих зусиль (перша стадія пресування). Потім збільшення тиску хоча і призводить до подальшого зменшення висоти брикету, але цей процес йде з повільніше (друга стадія). Нарешті, навіть значне підвищення тиску вже не призводить до скільки-небудь помітної зміни висоти брикету. Висота брикету при знятті тиску збільшується і продовжує збільшуватися з плином часу, в результаті появи пружних деформацій і розширення запресованого в продукті повітря. У процесі пресування необхідно прагнути до збільшення показника В і зниження Е. На показники В і Е впливають як умови процесу, так.Я фізико-хімічні властивості продуктів.
До числа перших відносять тиск пресування, тривалість витримування продукту під тиском, кратність навантаження, температуру робочих органів і матеріалу, конструктивні особливості і технічний стан робочих органів. Серед другої групи факторів можна виділити хімічний склад продуктів, їх дисперсність, коефіцієнти внутрішнього і зовнішнього тертя, гігроскопічні властивості, кількість і властивості речовин, що пов'язують. Зі збільшенням тиску пресування підвищується щільність і міцність пресованих продуктів, велика тривалість витримування продукту під тиском викликає релаксацію напруг в ньому, зниження коефіцієнта пружного розширення брикету. Важливим фактором, що впливає на перебіг процесу пресування, є температура продукту. Підвищення температури сприяє міграції вологи, пластичність продукт, знижуючи величину Е, хімічний склад продуктів також впливає на міцність брикетів. Продукти, що містять багато клітковини, утворюють менш міцні брикети або гранули. Більш міцні гранули утворюють матеріали з високим вмістом білка і крохмалю.
Операція формування є однією з найважливіших в технологічному циклі. Під пресуванням (формуванням) металевих порошків мається на увазі операція, в результаті якої під дією прикладених сил з аморфного сипучого порошку виходить щодо міцне тіло - пресування, яка за формою і розмірами близька до форми і розмірів готового виробу з урахуванням допусків на усадку і калібрування, а якщо необхідно, то і на механічну обробку. Розрізняють холодну (при кімнатній температурі) і гаряче (при підвищених температурах) пресування. Холодне пресування в закритих прес-формах - найбільш поширений прийом. При засипці порошку в прес-форму його частки розташовуються хаотично, утворюючи при цьому так звані містки або арки. Щільність засипаного порошку в цьому випадку не збільшується. Додаток зовнішнього тиску незначної величини до такого вільно насипному порошку призводить до різкого підвищення його щільності. Це пояснюється тим, що на початку формування частки заповнюють порожнечі і пори. У міру збільшення тиску, що додається містки і арки руйнуються і частинки проникають в дрібні пори. На подальших етапах формування відбувається якісна і кількісна зміна меж між частками: від тертя частинок при переміщенні один відносно одного видаляються окисні плівки, контакти між частками в цих місцях з неметалічних переходять в металеві. В результаті чого підвищується міцність заготівлі, потім відбувається крихке руйнування часток порошків з твердих металів і пластична деформація часток з м'яких металів.
Перспективно застосування гідростатичного пресування. Сутність такого пресування полягає в тому, що порошкова шихта, засипана в еластичні оболонки, всебічно обжимается рідиною (водою, маслом) при тиску вище 1000-2000 атм. Після холодного пресування металокерамічні заготовки мають надзвичайно низькими механічними властивостями і в деяких випадках можуть знову розсипатися в порошок при самому незначному зусиллі натискання. P>
Для підвищення механічної міцності і додання виробам необхідних фізико-хімічних властивостей спресовані заготівлі піддаються термічній обробці - спікання. При спіканні в порошковому виробі відбувається:
1) зміна форми і розмірів частинок і збільшення їх контактної поверхні; контакт між частинками з окисного перетворюється в металевий;
2) зняття залишкових напруг, що виникають при пресуванні за рахунок пружних властивостей частинок порошку;
3) об'єднання часток порошку і зміну співвідношення обсягу між порами і компактним металом частинок.
Останній процес чутливий до стану поверхні частинок порошку. Окісна плівка перешкоджає їх коагуляції. Тому спікання проводять у вакуумі або в захисній атмосфері (інертні гази, окис вуглецю, азот). Гаряче пресування - це різновид формування порошків, коли процеси пресування і спікання суміщені в часі. При порівняно малих тисках пресування є можливість отримувати майже безпористі вироби з щільністю, недосяжною при роздільному веденні процесів пресування і спікання.
температурний-швидкісні режими:
Гаряче пресування найчастіше здійснюється в закритих прес формах в області температур, що складають 0,5-0,8 від абсолютної температури плавлення основного порошку.
-Силовий умови пресування:
При виборі обладнання, розрахунку і конструюванні прес-форм необхідно враховувати вид порошку і спосіб підготовки шихти до формування. Хімічний склад, фізичні і технологічні властивості порошків впливають на процес формування, отже і на вибір обладнання.
-пресове інструмент:
Інструмент для пресування виробів повинен забезпечувати точність розмірів виробів, мати високу міцність, щоб протистояти досить великим напруженням, що виникають при пресуванні, володіти високою жорсткістю, щоб уникнути деформацій, які призводять до утворення тріщин в пресовках і підвищеного зносу інструменту, мати високу поверхневу твердість, щоб протистояти зносу, мати мінімальні допуски на формотворчих розміри, мати високу чистоту поверхні, забезпечувати високу продуктивність, бути довговічні м в роботі. До інструменту відносяться деталі прес-форм технологічного призначення: матриці, пуансони, стрижні. Розглянемо принципи конструювання цих найбільш відповідальних деталей прес-форм. Матриці в прес-формах застосовуються трьох видів: суцільні, складові і збірні. Складові і збірні матриці можуть бути як цілісні, так і розрізні. Розрізні матриці, в свою чергу, бувають роз'ємними і нероз'ємними. При конструюванні розрізних матриць необхідно правильно вибрати число розрізів і їх місця. При проектуванні калібрувальних матриць велике значення мають форма, довжина і кут заходная і вихідного конусів. Вкладиші - це деталі (або деталь) матриці, пуансона або стержня, що утворюють або формующую порожнину (вкладиші матриці або пуансона), або формуючий елемент пуансона, матриці або стержня, який створює поглиблення в пресованих виробів. Основні вимоги, що пред'являються до пресове інструменту, в повній мірі відносяться і до калібру (точність розмірів, чистота поверхні, необхідні твердість, міцність і жорсткість)
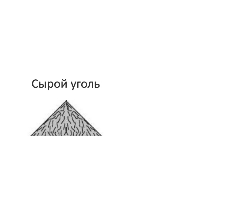
Способи пресування, що застосовуються в промисловості, відрізняються способами на-Гревьє матеріалу, його введення в форму і после¬дующего формування: пряме (компресійні-ве), литьевое (трансферне) і безперервне профільне (штранг-пресування). У процесі прямого (компресійного) пресування (ріс.1a) підготовлений до пресування матеріал 2 (прес-порошок) до¬зіруется і надходить в матрицю прес-форми З, в якій здійснюється процес формова¬нія вироби 5, після чого виріб видаляється з матриці виштовхувачем 4. Литьевое (транс¬ферное) пресування (рис. 1, 6) відрізняється від прямого тим, що розплавлений в загрузоч¬ной камері прес-матеріал 1 під дією тиску, переданого пуансоном 2, через літніковие канали 3 надходить в попередньо-тельно зімкнуту форму, де він твердіє виріб 4. Безперервне профільне пресування, або штранг-пресування, застосовується для отримання профільних погонажних виробів.
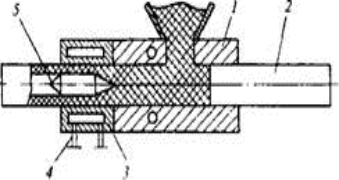
Постійного перетину видавлюванням розплаву прес-матеріалу плунжером 2 через формующий інструмент, утворений мундштуком 3 і торпедою 5 (рис 2). Привід плунжера 2 забезпечує його зворотно-поступальний рух. Прогрів матеріалу відбувається за допомогою системи обігріву 4 і за рахунок сдвіго¬вих деформацій при його видавлюванні. Пресування шаруватих пластиків, пред¬ставляющіх собою композиційні ма-ли і складаються з наповнювача і зв'язуючого, найчастіше термореактивних смол, осуществ¬ляется на багатоповерхових гідравлічних прес¬сах. В результаті отримують пластики разліч¬ние по товщині: текстоліт, склотекстоліт, асботекстоліт, гетинакс, декоративний слоі¬стий пластик, деревне шаруватий пластик. Конструкції пресового устаткування. Преси - машини статичного дії, призначені для формування виробів з прес-матеріалів шляхом застосування тиску. Різноманітні сучасні конструкції пресового обладнання можуть бути клас¬сіфіціровани по ряду ознак.
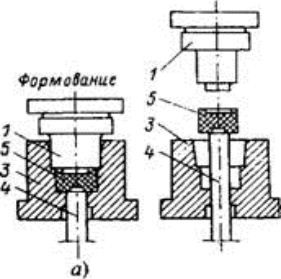
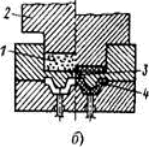
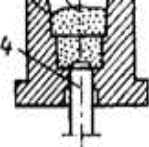
Найбільш поширеним пресовим обладнанням є преси з гідравлічним приводом, які мають значітель¬нимі перевагами перед іншими преса.
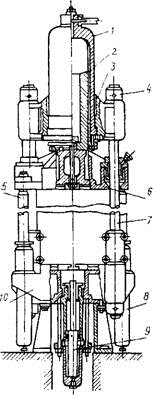
В гідравлічному колонній пресі з верхнім розташуванням робочого циліндра (рис. 4) робоча рідина (емульсія або масло) Сила пресування - один з основних параметрів преса. Гідравлічний прес, як правило, включає наступні основні механізми і деталі: станину, систему циліндрів (робочий, поворотний, що виштовхує) з плунжерами або поршнями, рухомі та нерухомі поперечки, гідроагрегат, що складається з насо¬сов, трубопроводів і розподільників потоку рідини. У напрямку діючої сили пресування гідравлічні преси подразде-ляють на вертикальні, горизонтальні та угло¬вие. Залежно від конструкції станини преси бувають колонні, рамні і щелепні. Для чеканки монет забезпечують хороший доступ до прес-формі, проте мають значі¬тельние габаритні розміри і металлоем¬кость.а також малу жорсткість. Ці недостат¬кі відсутні в пресах рамної конструкції (рис. 5). У верхній частині рами 1 жорстко закріплений робочий гідроциліндр 9 з діффе¬ренціальним поршнем 8 подвійної дії. Плита 7 рухається по напрямних 5 під дією сполученого з ним поршня 8. У нижній частині рами розташований стіл 4 і витал¬ківатель 2. Для обмеження ходу повзуна б і штока поршня 2 служать вимикачі 3. Перевагою преса з нижнім располо¬женіем робочого циліндра є його устой¬чівость (так як центр ваги розташований досить низько), невеликі габаритні раз¬мери, можливість застосування знімних форм з великою силою пресування. Пресування шаруватих пластиків проводять на поверхових пресах колоною конструкції з нижнім рас¬положеніем робочого гідроциліндра 1 (рис. 5).
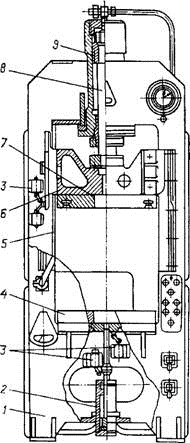
Станина преса повинна бути досить міцною і жорсткою, щоб забезпечити требуе¬мую точність взаємного розташування меха¬нізмов преса і відносного положення інструменту і оброблюваного об'єкта при динамічних навантаженнях.
Ділянка колони між нижньою і верхньою плитами в зв'язку з деформацією плит і ексцентричним їх вантаженням працює не тільки на розтягнення, а й на вигин. Крім того, на колони діють пульсуючі навантаження, тому виконується розрахунок і на їх втому. Колони зазвичай виготовляють зі сталі Ст5 або низьколегованих сталей. При цьому коефіцієнт запасу міцності приймають рівним 2,0 ... 2,2
При написанні даного реферату магістерська робота ще не завершена. Остаточне завершення: червень 2018 року. Повний текст роботи та матеріали по темі можуть бути отримані у автора або його керівника після зазначеної дати.
- Металеві порошки та порошкові матеріали: довідник /Б.Н. Бабич, Е.В.Вершініна, В.А. Глєбов і ін .; під ред. Ю.В. Левинського. -М .: Екомет, 2005. - 520с .: іл.
- Устаткування й оснащення для формування порошкових матеріалов.Клячко Л.І., Уманський А.М., Бобронов В.Н. М .: Металургія, 1986, 336 с.
- Барков, Н.А. Технологія пресування: Метод.указанія до лабораторних занять покурсу «Технологія пресування» для студентів спеціальності 110600 «Обробка металів тиском» / Упоряд. Н.А. Барков, С.Б.Сідельніков, С.В. Бєляєв и др Красноярськ: ГУЦМіЗ, 2004. - 36 с.
- Носков В.А., Ващенко С. В. Про використання принципу багатоступінчастого ущільнення при брикетуванні дрібнофракційних шихт // Фундаментальні та прикладні проблеми чорної металургії: зб. наук. тр. Випуск 4. К .: Наукова думка. - 1999. - С. 285.
- А. с. №1473246 (СРСР) / В.А. Генетів, М.Г. Скляр, Е.І. Торяник, А.А.Тараканов, В.Н.Шмадченко, Ф.С. Щелкунов Опубл. в Б. І., 1991, №22.
- А. с. №1189686 (СРСР) / Л.С. Грішних, І.І. Фетисов, В.Ф. Брикалін, В.В. Борісейко, Н.П. МарукОпубл. в Б. І., 1988, №40.
- А. с. №2190877 / 27 (СРСР) / М.Д. Петров Опубл. в Б.І., 1977, №9. .