Abstract
The content
- Introduction
- 1. Theme urgency
- 2. Goal and tasks of the research
- 3. Structural-parametric identification of the model of sterilization process in automotive periodic activities
- Conclusion
- References
Introduction
The food industry is one of the largest sectors of the economy, within the agro komple ks page Ana. The development of the canning industry in Russia, for example, is due to the construction of new plants and the modernization of existing enterprises. One of the most important technological processes in the canning industry, on which the quality and safety of the finished product largely depends, is sterilization [1].
When sterilized, the sealed jars with the product are exposed to high temperatures, as a result of which the microorganisms in the cans die, thereby ensuring the safety of food.The quality of the sterilization process, which is the most important, complex and responsible stage of the canning technology, depends on the quality of the finished product. For the sterilization of canned food, periodic apparatuses are often used - autoclaves. However, manuals and books for studying and mastering sterilization processes have hardly been published in recent years, especially on the issues of process management using automatic control and regulation devices [2]. The high quality of canning products is ensured by a clear and harmonious work of all parts of the processing process. Sterilization is one of the most important stages in the processing of agricultural products, for which batch devices are used - autoclaves [3].
1. Theme urgency
Known solutions developed in the field of automation of autoclaves, frighten off customers at their own cost, or the complexity of implementing the system of automatic control. Since the literature describing the technological process of sterilization in batch autoclaves is very small. Its relevance is subject to a lot of questions, since it was published in the late 90s, and as is known, progress has long struck forward.
The introduction of automatic regulation and control of the parameters of the sterilization process will allow to sharply reduce the amount of defective products, to shorten the time of exposure to high temperature to the product, to reduce electricity consumption, and to reduce the number of personnel and the influence of the human factor on process parameters.
2. Goal and tasks of the research
The aim of the work is to study and develop a system for automatic control of a batch autoclave.
Main tasks of the research:
- Analysis of the sterilization process in a batch autoclave. Designing an automatic control system for three autoclaves of batch operation.
- Development of a functional diagram of the automatic control system. Development of a schematic diagram of the control system.
- Development of a model of automatic autoclave control system
- Development of an algorithm for the operation of an automatic control system of three autoclaves.
Research object: a batch autoclave.
Research subject: the control and stabilization of the parameters of the sterilization process in a batch autoclave.
3. Structural-parametric identification of the model of sterilization process in automotive periodic activities
The developed mathematical model of the process includes parameters that can be conditionally divided into two groups. The first group includes the thermophysical parameters of air, water, the space of the autoclave, which can be determined using reference literature. The second group includes parameters characterizing the heat exchange at the boundaries of various media, the theoretical calculation of which is approximate or difficult.
In the case of a particular control object, these parameters should be determined as a result of solving the identification problem from the measured values of the controllable and control signals of the object in the modes of industrial operation. This parameter is the coefficient of heat transfer between the inner wall and the environment of the autoclave - k t .
We solve the problem of parametric identification of the heat transfer coefficient. Parametric identification allows you to immediately find the values of the coefficients of the model of the object from the measured values of the controlled and control signals of the object. This advantage has determined the wide use of parametric identification methods in control and automation tasks. These methods include: recurrently s second method of least squares (RLSM), the method of auxiliary variables, the maximum likelihood method.
To sterilize the cooling process in the autoclave are known quantities: G in the flow of water in the autoclave; T into the water temperature ; with the heat capacity of the water;T env ambient air temperature. It is necessary to determine the value of the heat transfer coefficient Kt.
In Fig. 1.1 is a graph of the adjustment of the heat transfer coefficient in the identification process.
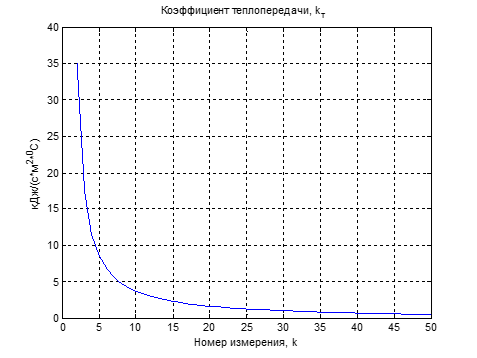
Figure 1 – Graph of the change in the estimation of the heat transfer coefficient in the process of obtaining new measurements
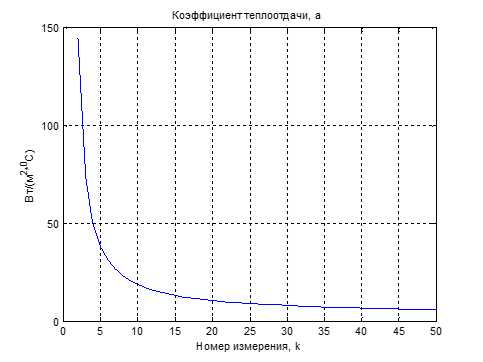
Figure 2 – Graph of change in the estimation of the heat of recoil in the process of obtaining new measurements
The heat transfer graph asymptotically tends to 0.058 kJ / (s * m 2 * 0 C), i.e. this value is an estimate of the coefficient of thermal conductivity of the walls of the autoclave.
Conclusion
The obtained results using RLSM theoretically have important properties from the point of view of practical application, namely: unbiasedness of the obtained parameter estimates, minimum dispersion of the error, convergence to the true value of the parameters as the error tends to zero.
Thus, in the model of sterilization in an aqueous medium through a hot- flow channel water - temperature of the heating medium parameters of the model can be determined by the method of least squares from the observations of the object depending on the control action , which makes it possible to use it to determine the most effective impact on the object when the dynamic characteristics of the sterilized product change, the parameters of the heating steam and the degree of loading of the autoclave.
This model is intended for realization in the microprocessor control system of the process of sterilization of canning products in vertical autoclaves of periodic action.
References
- Vlasov A.V. Improving the efficiency of steam canning sterilization in autoclaves. Author's abstract . dis . Cand. tech . sciences. Murmansk, MSTU , 20 p., 2010.
- Verboloz E.I. C Improvements heat - mass exchange processes in devices for canning sterilization // Bulletin of the International Academy of Refrigeration. 2005. № 1. P. 42-43.
- Shchagin A.V. and others. The fundamentals of the automation of technical processes. - M .: Higher Education, 2009. - 163 p.