ЭФФЕКТИВНОЕ ИСПОЛЬЗОВАНИЕ ТЕПЛОВОЙ ЭНЕРГИИ В ЭЛЕКТРОДУГОВОЙ ПЕЧИ, ИНТЕГРАЦИОННЫЙ ПОДХОД
Авторы: Umesh Kuma, A. K. Prasadbr, Sourabh Kumar Soni
Автор перевода: Дмитриенко Д. Г.
Источник: International journal of engineering sciences research technology [Ссылка]
Аннотация
На основе принципов интеграции тепла в настоящей работе исследуются конструктивные и эксплуатационные изменения, которые могут привести к эффективной интеграции энергии в электродуговой печи, эксплуатируемой в процессе прямого восстановления. Этот процесс-один из самых старых и наиболее широко применяемых процессов среди коммерческих используемых процессов в Индии. С целью энергетической интеграции данные о потоке извлекаются из фактического технологического листа установки, который состоит из температуры подачи и заданной температуры, расхода и удельной теплоемкости всех технологических потоков. В настоящей работе для утилизации тепла отходящих газов предлагается использовать предварительный подогрев входных потоков. На основе явного тепла требования для подогрева воздуха и подачи материала. Тепло теряется через стены печи, осуществляется нагрев лома, железо прямого восстановления и подачи материала, и тепла, которое необходимое для испарения влаги из сырья, потребление энергии вычисляется [11]. Для модифицированного процесса интеграции тепла представлены анализы работоспособности, которые включают потребление угля, потребность в воде и потребление энергии. Еще одним преимуществом этой системы является то, что она дает более простой модифицированный метод по сравнению с другими сценариями и, таким образом, делает процесс и его контроль легким. Это минимизирует отходы газов в атмосферу, что делает процесс экологически чистом.
Введение
Электродуговая печь (ЭДП) - это печь, которая нагревает загруженный материал с помощью электрической дуги. Электродуговая печь нагревается до 1600 градусов C электричеством, вырабатываемым через электроды [7]. Как правило,существует два типа печи (а) непрямая дуговая печь - в непрямой дуговой печи дуга ударяется между двумя угольными электродами, и тепло передается в шихту излучением. Косвенные дуговые печи имеют достаточно небольшой мощности и не могут развивать температуру выплавки стали, (б) дуговая печь прямого действия - ток прямой дуговой печи течет от электрода к шихте, а тепло, передаваемое от дуги к шихте, главным образом, излучением, но тепло также генерируется в самой шихте [6]. Около 438 млн. т/год жидкой стали (31% от общего объема в мире) производятся с помощью электродуговой печи. В Турции, приблизительно 70% из полной стали произведены в ЭДП. Это свидетельствует о том, что методом ЭДП производится около 20 млн. тонн стали [8]. В основных печах для получения шлака, для рафинирования металла, используются шлаки, такие как известняк, плавиковый шпат, песок и кварцит [13]. Основная концепция прямого восстановления железа приближается к 3000 лет существования, но первый коммерческий завод начал функционировать в 1952 году в Швеции. В Индии новаторскую работу выполнили Национальная металлургическая Лаборатория Джамшедпур и Tata steel Ltd Джамшедпур. Первый завод коммерчески с демонстрации был установлен использующ угл-основанную технологию во время 1980. В 1989 году ESSAR steel начала производство губчатого железа по газовой технологии [12].
Материалы и методы
На рис. 1 показано что в потоке входа и выхода материалов. Во входном потоке основными компонентами являются стальные обрезки, Кокс, природный газ и электрод. В выходных потоках сталь, шлак, пыль и отходящие газы.
На рис. 2 показаны входные и выходные потоки материалов. На поставку электрической энергии приходится 65% от общего объема энергии, которую также обеспечивают другие материалы. В выходных потоках сталь (57%), шлак (10%) и отходящие газы (21%). Наша цель-утилизация отходящих газов.
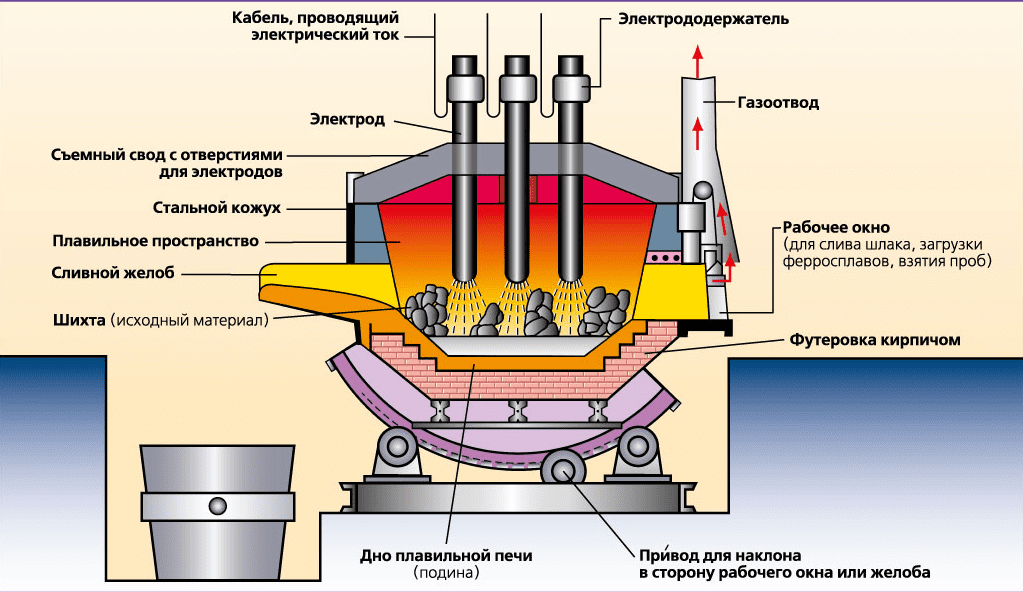
Рис 1
Результаты и обсуждение
Анализ баланса массы был проведен для ЭДП грузоподъемностью 70 тонн. Количество материалов поданных в ДСП. После определения количества каждой згрузки материала собирают химический состав всех материалов, измеренный на заводе или взятый из соответствующей литературы [7].
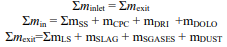
В внизу таблице количество входа и выхода материала в дуговую электропечь (ДСП) было обсужено. Как мы видим, выход жидкой стали 68125 кг, что составляет 77,3% от общего впускной металл. Шлак и отходящие газы тепла составляют 21,6% от общего объема металла. Эта диаграмма очень полезна для расчета эффективности процесса [8].
Таблица: 1 Массовый баланс полученный после деятельности
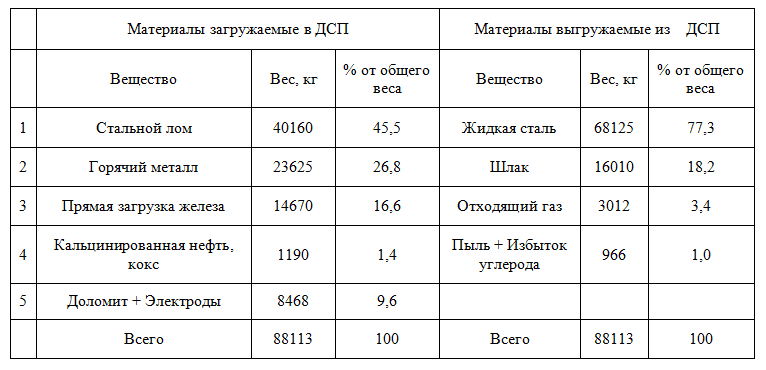
Энергетические (тепловые) балансы дают общее представление об электродуговой печи как об энергоблоке. Эти остатки выводятся из закона сохранения энергии, согласно которому общий объем энергии должен быть равен выходной энергии.

Это формула баланса энергии. Мы вынуждены потреблять электроэнергию 240 кВт ч/т, что составляет 48,84% от общего объема металла [8].
Таблица: 2 Тепловой баланс электродуговой печи 70 тонн
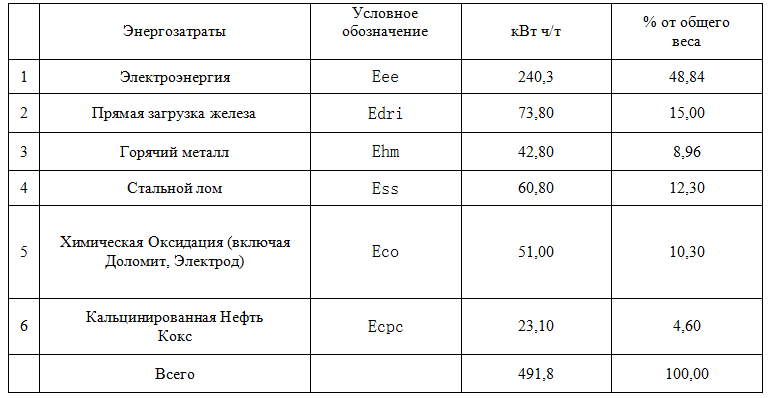
Для того чтобы сделать баланс массы и энергии, во первых все материалы которые входя в систему, высчитаны на компонентном основании. Необходая информация о чугуне и производства стали. Во-вторых, элементарно сравнивались массовые значения жидкой стали, выходящей из печи с учетом ее легирующих элементов, с входными материалами. Это сравнение позволяет определить массовые значения веществ, вступающих в химические реакции. Таким образом, были найдены соединения, образующие шлак, дымовые газы и пыль. Эти соединения соответствовали измерениям, проведенным на заводе. В связи с тем, что компания не располагает данными о соотношении материалов, присутствующих в пыли и шлаке, необходимая информация получена из аналогичного исследования. Сталеплавильное производство электродуговых печей приобретает все большую роль в производстве стали с использованием большего количества заменителей лома и лома различного уровня качества. Таким образом, цель заключается в улучшении экономических и технических характеристик печей, несмотря на трудности и ограничения, связанные с использованием этого нового типа шихты. Необходимо улучшать, получая,и модернезировать оборудование печи, некоторые основные требования необходимо соблюдать:
- Использования энергии с максимальным коэфициентом полезного действия (КПД) (электрической и внутренней), при высокой температуре окружающей среды;
- Использование электроэнергии и углерода в печи, должно быть оптимизировано;
- Время отключения дуги из-за холодной загрузки, должно быть как можно короче;
- Процесс производства стали должен быть безопасным и экологически чистым.
Вывод
На основе результатов, полученных от разработки энергосбережения для интеграции тепла в электродуговой печи, возможности его реализации, а также сравнение модифицированной системы с существующим процессом на основе энергопотребления. Основные выводы перечислены ниже:
Метод внедрения можно эффектно приложить к дуговой электропечи для того чтобы выполнить сбережение энергии который может привести к рациональному использованию энергии.
- Образующийся в результате этой работы отходящий газ на 14,2% меньше по сравнению с другой электродуговой печью.
- Среднее количество энергии, которое может быть сэкономлено в настоящем исследовании в пересчете на кокс, составляет 72,4 кВтч/тонну.
Огромное количество энергии расточительствованной в индустрии дуговой электропечи, которая может быть повторно использована применением правильной схемы. Подогрев материалов входа одна из возможных схем которую возможно применить, для того чтобы уменьшить энергопотребление и увеличить производительность. В этой схеме, энергия газообразного отхода возвращена к нейтральному газу через теплообменный аппарат, и после этого, горячий газ используется для того чтобы подогреть материалы входа. Моделирование процесса предварительного нагрева с помощью этого метода, даёт возможность сэкономить электроэнергию до 14,2% и увеличить производительность печи до 13%. Хороший потенциал к дальнейшему увеличению в сбережениях, путем увеличение температуры газа входа. При этом подогрев исходного материала осуществляется с использованием отходящих газов. В модифицированной системе электродуговой печи общее потребление энергии составляет 419,4 кВт * ч/т вместо 491,8 кВт * ч/т, что на 14,2% меньше, чем у другой электродуговой печи.
Список использованной литературы
- UnalCamdali, Murat Tunc, FeridunDikec,”A thermodynamic analysis of a steel production step carried out in the ladle furnace”,Applied Thermal Engineering 21 (2001) pg-643-655(Elsevier).
- W. Burgmann, W. Lur'e, and G.-L.Rot"charging technology for modern Electric Arc Furnace”, Metallurgist, Vol. 43, Nos. 3-4, 1999.
- I. Ekmekci,Y. Yetisken, and U. Camdali, “Mass balance modeling for Electric Arc Furnace and ladle furnace system in steelmaking facility in Turkey,” Iron Steel Res., Int., 14, No. 5,(2007)Pg 1–6, 55.
- L. Hocine et al. ,“ Improvement of electrical arc furnace operation with an appropriate model,” Energy, 34, (2009)1207–1214.
- U. Camdali and M. Tunc, “Computer-aided mass balance analysis for AC electric arc Furnace steelmaking,” J. Iron Steel Res. Int., 12, No. 3,(2005) 11–13 .
- Yuri N. ToulouevskiIlyaz Y. Zinurov, “Innovation in Electric Arc Furnaces”, springer press(2010).
- M. Tunc,1 U. Camdali,2 and G. Arasil1,”Mass analysis of an electric arc furnace (EAF) at a steel company in turkey” Metallurgist, Vol. 56, Nos. 3–4, July, 2012 (Russian Original Nos. 3–4, March–April, 2012).
- YasarYetiskena, UnalCamdalib, and Ismail Ekmekcic,”optimum charging materials for electric arc furnace (EAF) and ladle furnace (lf) system: a sample case", International Iron & Steel Symposium, 02-04 April 2012, Karabuk, Turkiye.
- U. Camdali and M. Tunc, “Exergy analysis and efficiency in an industrial AC electric arc furnace,” Appl. Therm. Eng.,21, 2255–2267 (2001).
- A. K. Prasad, R. K. Prasad, S. Khanam,”Design Modifications for Energy Conservation of Sponge Iron Plants”, Journal of Thermal Science and Engineering Applications march 2011, Vol. 3 / 015001-11.
- M. E. Ertem , S. Sen& G. Akar , “Energy Balance Analysis and Energy Saving Opportunities for Electric Arc Furnace”,( Taylor & Francis group) PP.-979-994,(2010).
- U. Camdali , Y. Yetisken&I.Ekmekci, ”Determination of the Optimum Cost Function for an Electric Arc Furnace and Ladle Furnace System by Using Energy Balance", (Taylor & Francis group),PP.-200212,(2011).
- H. Pfeifer, M. Kirschen, “Thermodynamic Analysis of EAF Energy Efficiency and Comparison With a Statistic Model of Electric Energy Demand”. (Institute of Industrial Furnaces and Heat Engineering in Metallurgy), (2010).
- Bernd Kleimt,Siegfried Kohle& Robert Kuhn, ”Application Of Models For Electrical Energy Consumption To Improve EAF Operation And Dynamic Control”,(2007).
- H.S. Shey& A Ghosh, “Principal of Extraction Metallurgy”,(1998).
- Jeremy Jones,”Utilization of Pig iron in the Electric Arc Furnace”, (prepared for the International pig iron association).PP.-1-18.(2007).
- Chirattananon and Gao,’’A model for the performance evaluation of the operation of electric arc furnace”, (Energy Conversion Management), PP.161 -166,(1996).
- Czapla, Karbowniczek and Michaliszyn, “ The optimization of electric energy consumption in the electric arc furnace”,(2008),PP.559–565.
- V. D. Smolyarenko, A. N. Popov,”Next-Generation Electric Arc Furnaces as a Steelmaking Modernization Factor”, (Journal of Russian Metallurgical) Vol.7,(2007).
- Jian-ping Duan, Yong-liang Zhang, ” EAF steelmaking process with increasing hot metal charging ratio and improving slagging regime”,(International Journal of Minerals, Metallurgy and Materials) Volume 16, Number 4,(2009), PP.375-382.
- E. H. Mclntyre, J.E. Goodwill and D.E. Klesser, “The challenge of improving electric arc furnace efficiency”,(Journal of IronSteel Eng.),vol.71,(1994), PP.28.
- V. Logar, D. Dovzan, and I. Skarjanc, “Mathematical modeling and experimental validation of an electric arc furnace,” ISIJ Int., 51, No. 3,(2011) 382–391.