Content
- Introduction
- 1. Relevance of the topic
- 2. The purpose and objectives of the study
- 3. Analysis of previous studies
- 4. Material and research results
- Conclusion
- References
Introduction
Among the devices that convert electrical energy into mechanical energy, the undoubted leaders are three-phase asynchronous motors. Their share is about 85% of all electric cars. They are very simple and reliable, which makes them a good choice for driving the mechanisms of industrial enterprises and the system's own needs of power plants. Despite the fact that their design is simple and reliable, the damageability of electric motors reaches 25% of the total number of operating engines per year, which, in turn, leads to major repair work. Currently, an increasing number of enterprises pay great attention to the development, production and installation of relay protection and automation, made on a microprocessor base.
It is believed that the normal service life of an asynchronous electric motor is 15– 20 years under normal operation, however, there are a number of factors that significantly reduce this indicator: poor quality of the supply voltage, elevated temperature, humidity. As a result of adverse effects, about 10% of electric motors fail.
Accidents caused by electric motor breakdown usually lead to large material damage due to the downtime of the entire process. All abnormal operating conditions lead to an increase in the heating temperature of the AED windings, and, consequently, to a reduction in the service life of the machine. Exceeding the heating temperature above the allowable values ??causes aging of the motor winding insulation, and, therefore, contributes to the emergence of severe emergency conditions such as multiphase short circuits, coils, single-phase earth circuits in the stator winding (for AED operating in networks with insulated neutral). Emergency modes lead, in turn, to the steel melting of the stator magnetic core and the winding melting. Standard AED protection, implemented in most modern microprocessor-based relay protection devices, does not provide the required sensitivity for most types of damage. One of the ways to increase the service life of an AED is to improve the existing and develop new algorithms for protection against thermal overload of induction motors. For this reason, there is a need for protection devices and monitoring of the status of asynchronous electric motors. Modern standards of most countries of the world are placing increasing demands on the technical operation of electrical installations. The need for continuous monitoring of expensive equipment reinforces the need to use high-quality, reliable and comprehensive protection of electric motors.
1. Relevance of the topic
The key electric motors of alternating current, massively used as the electric drive of the mechanisms of the system of own needs of power plants and industrial enterprises, are asynchronous electric motors (BP) with a squirrel-cage rotor (KZR). These machines are characterized by simplicity of design, relative reliability and ease of maintenance. However, in spite of the above advantages, as fairly shown in [ 1 , 2 ], ADRs with a sufficiently high percentage of damage (about 25-30% per annum of the total number of machines operated), associated with work in emergency and abnormal modes, as well as with incorrect operation of relay protection and automation devices (RPAA). It is possible to reduce the damage to blood pressure in the CDR due to the further improvement of the systems RZAA. Therefore, the task of improving the thermal protection of asynchronous electric motors is relevant.
2. The purpose and objectives of the study
The work is devoted to the improvement of thermal protection of low-voltage asynchronous machines with a short-circuited rotor, based on the control of the equivalent heating temperature according to the definition of the input active resistance of the direct sequence in cold and hot states. The calculation of the input resistance is based on the measurement of phase currents and voltages, as well as the magnitude of the slip. The performance of the proposed thermal protection is tested on a PC using mathematical modeling methods for a 5.5 kW asynchronous motor with a stator voltage of 0.4 kV
3. Analysis of previous studies
A large number of scientific papers [ 1 – 6], in which the focus is on thermal protection (TZ). [ 1 – 3 ] shows upgraded thermal overload protection, which is characterized by the use of pseudo-thermal models that are unsatisfactory operation in a number of abnormal and emergency modes of operation, such as mixed mode, breakage of rozor cores, etc. In [ 4 & ndash; 6 ], the most promising TZ algorithms are presented, based on monitoring the parameters of the current mode, but requiring further modernization to be used as protection of low-voltage AM with Sp.
4.Material and research results
As a platform for improving the TZ of low-voltage AM with KZR, we will use an algorithm for controlling the equivalent heating temperature of an asynchronous machine based on the measurement of the parameters of the current mode described in [ 5 ]. Unlike the TK algorithm presented in [ 5 ], we will use to determine the equivalent heating temperature of an asynchronous machine based on the measurement of instantaneous values ??of phase currents and voltages, as well as the slip value. With a view to correct operation in asymmetric modes, we will use the calculation at each step of the microcontroller's operation of input active resistances of a direct sequence (PP), similar to the algorithm presented in [ 6 ].
In this paper, we will use the single-circuit equivalent replacement circuit (ESA) AM with the loss contour in the stator steel and taking into account the direct-sequence skin effect shown in Fig.1 in the basis of the TZ algorithm. All calculations will be performed in the system of relative units (ru). The parameters of the selected ESZ AM with KZR will be determined using the method described in [ 7 ]. The skin effect in this replacement scheme is taken into account in a simplified way using linear dependencies (1), which is acceptable for low-voltage machines.

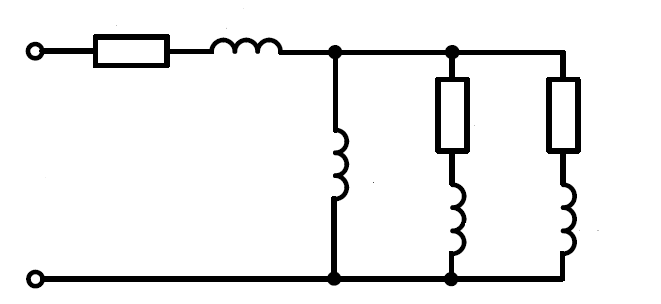
Picture 1 – Single-circuit equivalent replacement circuit for an asynchronous machine with a direct sequence with a loss loop in the stator steel taking into account the skin effect (animation of 6 frames, 6 cycles)
The idea of TK, as in [ 5 ], is to determine in real time the equivalent heating temperature of an asynchronous machine by comparing the current calculated value of the input active resistance in a hot state with a known cold state value. At each step of the operation of the microprocessor terminal of the RZAA, the following computational operations should be performed to determine the equivalent heating temperature of AM with KZR:
• Measurement of instantaneous currents (ia, ib, ic) and voltages (ua, ub, uc) of phases a, b, and c;
• If there is a temperature sensor embedded in the stator winding, we adjust the current value of the active resistances of the stator and the loss circuit in the steel of the stator magnetic circuit, similarly to [ 6 ];
• Measurement of the slip value (s) by one of the known methods, for example, a rotor angle sensor mounted on an AM shaft [3–6];
• Calculation of the modules of the generalized vector of the current and voltage of the stator PP asynchronous machine:

• Calculation of power PP AM with KZR:

• Determination of the input active resistance of the direct sequence in the hot state:

• Determination of the input active resistance of the PP machine in the cold (source) RВХисх.1 (s) state for the current value of slip s:

• Determination of the current value of the equivalent temperature of heating AED with KZR based on a comparison of the input active resistance PP, measured in the hot state and the known resistance in the cold (initial) state for the current slip value:

The efficiency of the proposed thermal protection of the asynchronous machine was tested on a modern PC using mathematical modeling methods for AED with KZR type AIR-112-M4, the catalog data of which are presented in Table 1. The paper used a mathematical model of AED with KZR based on full differential equations, given in [ 5 ]. The parameters of SPS AM for temperature 750С were determined on the basis of catalog data, according to [ 7 ], and are presented in table 2.
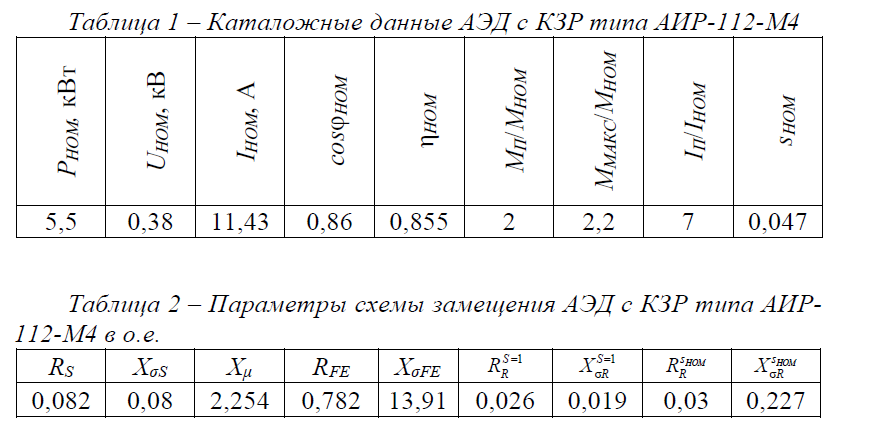
The results of calculations of the mode of increasing the load on the shaft (load build-up) confirming the correctness of the algorithm are shown in Fig. 2 as a function of time, the equivalent heating temperature of the AED with KZR determined from the algorithm (VR) proposed in the work and the temperature calculated according to a certain law (VR *) as in [ 5 ]. The coincidence of practically VAED confirms the correctness of the work of TZ AM with KZR. Also, similarly to [ 6 ], the correct operation of the TOR with different asymmetry coefficients was checked, which confirms the leveling effect of asymmetric operating modes on the accuracy of determining the temperature of the machine.
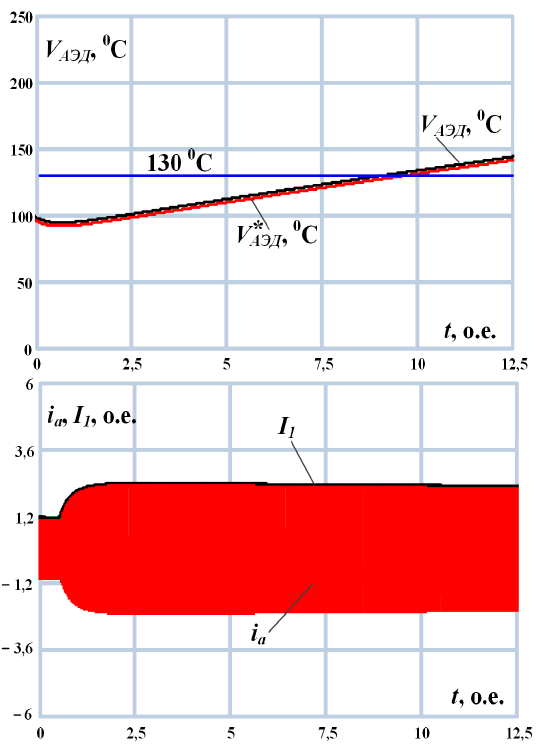
Picture 2 – The dependence of the equivalent temperature of heating AED with KZR type AIR-112-M4 from time
Conclusion
The paper proposes an improved algorithm for thermal protection of low-voltage asynchronous machines with a short-circuited rotor based on monitoring the parameters of the current mode. It was proposed to indirectly determine the equivalent heating temperature of the machine on the basis of determining the direct sequence, based on the measurement data of the parameters of the current mode of input resistances, which positively affects the operation of thermal protection in various asymmetric modes. The efficiency of the proposed thermal protection was tested on a PC using mathematical modeling methods for a 5.5 kW asynchronous motor with a stator voltage of 0.4 kV.
The above material was presented at the international scientific and technical conference "Innovative Perspectives of Donbass", and also published in the relevant collection of scientific papers of the conference, which was included in the RISC database [ 8 ].
When writing this essay master's work is not yet completed. Final Completion: June 2018. The full text of the work and materials on the topic can be obtained from the author or his manager after the specified date.
References
- Корогодский В.И. Релейная защита электродвигателей напряжением выше 1кВ/С.Л. Кужеков, Л.Б. Паперно – М.: Энергоатомиздат, 1987. – 248 с.
- Гусаров А.А. Определение температуры элементов тепловой схемы замещения асинхронного двигателя для разработки теплового реле и диагностики / А.А. Гусаров, Е.Б. Ковалёв // Сборник научных трудов УкрВНИИВЭ. Серия «Взрывозащищённое оборудование». –2009. – С. 155 – 161.
- Zocholl S.E. On the protection of thermal processes power delivery / S.E. Zocholl, G. Benmouyal // IEEE Transactions on Vol.20, Issue 2 – 2005. – P.: 1240 – 1246;
- Ткаченко С.Н. Цифровая релейная защита низковольтных асинхронных электродвигателей с короткозамкнутым ротором системы собственных нужд электростанций / Збірник наукових праць ДВНЗ «Донецький національний технічний університет». Серія «Електротехніка і енергетика». – випуск 2 (15). – Донецьк, 2013. – С. 217 – 222.
- Ткаченко С.Н. Прогнозирование срока службы асинхронного электродвигателя с короткозамкнутым ротором на основе контроля параметров текущего режима / С.Н. Ткаченко – Завалишинские чтения'16, ГУАП, г. СПб, №4.– 2016. – С.246-249.
- Сивокобыленко В.Ф. Моделирование алгоритма тепловой защиты короткозамкнутого ротора асинхронного электродвигателя / В.Ф. Сивокобыленко, С.Н. Ткаченко // Вісник національного університету «Львівська політехніка». «Електроенергетичні та електромеханічні системи». – № 654. – Львів,2009. – С.203–209.
- Ткаченко С.Н. Метод идентификации параметров эквивалентных схем замещения асинхронных электродвигателей с короткозамкнутым ротором / Ткаченко С.Н. // Збірник наукових праць ДВНЗ «Донецький національний тех-нічний університет». Серія «Електротехніка і енергетика». – випуск 1 (16). – Донецьк, 2014. – С. 210 – 215.
- Ткаченко С.Н.,Коваленко А.В., Киселёв В.А. Совершенствование тепловой защиты низковольтных асинхронных машин с короткозамкнутым ротором / Иновационные перспективы Донбасса, 4-й международной научно-практической конференции 2018.