Abstract
Content
- Introduction
- 1. Theme urgency
- 2. Goal and tasks of the research
- 3. A review of research
- 3.1 The requirements placed on to the gears
- 3.2 Signs of declining health gears
- 3.3 Treatment of gears
- Summary
- References
Introduction
In today's world, most machines and mechanisms are difficult to imagine without gears. Although the name of the inventor of the gear is unknown, certainly it can be called one of the great inventors. Its use gears found in ancient times. Their application due to the need to convert and transfer mechanical energy from a natural source to the consumer. They were originally distinguished its shape is from modern and made of wood. Since the XVIII century, with the development of such Sciences as geometry, kinematics and mechanics, the profile of teeth was improved, getting more rational form and outlines.
Now gears are one of the most important elements of various devices, machines and mechanisms. Their quality depends on the operational properties and reliability of these machines. They are used to convert rotational motion into translational motion, as well as to transmit rotational motion. movement between the axes of the shafts. The use of gears is due to a number of advantages over other types of transmission.
Gears are classified depending on the design: cylindrical, worm, conical.
1. Theme urgency
Gears are the most common type of power transmission. The quality of their work depends on the accuracy and quality surfaces of gear teeth, which are achieved mainly at the stages of finishing and hardening treatment. Ring gear it is an element with a complex periodic profile and is obtained by machining. This requires high labor input machining and appointment of additional allowances associated with the achievement of the required accuracy and quality of the teeth. Finishing and finishing of teeth, due to the large surface area of the toothed crown, requires no less labor input, which increases significantly with increasing demands on the accuracy of the gears. Therefore, it is currently relevant the task of improving the performance and quality of finishing gear teeth.
On the basis of the above, this work is relevant, and is devoted to improving the performance and quality of finishing gears prior to application of coatings.
2. Goal and tasks of the research
The aim of the work: improving the productivity and quality of machining teeth of gear wheels by means of improving technology finishing of teeth and application of special coatings.
The main objectives of the study:
- Perform an analysis of the working conditions of the gears, to determine the basic requirements for the gears to ensure reliable and trouble-free operation;
- On the basis of morphological analysis, to determine the most rational methods of finishing and hardening treatment of teeth;
- To develop a General structure of the technological process of finishing and hardening treatment of teeth, providing an increase in the performance of gears;
- To offer a rational method of finishing teeth, which provides an increase in the productivity of polishing the side surfaces of the teeth;
- To study the influence of input parameters on the finishing quality of the surface of the teeth;
- To develop recommendations for improving the productivity of the final processing of teeth and the quality of the treated surfaces.
3. A review of research
3.1 The requirements placed on to the gears
The following requirements apply to the teeth of gears:
- high wear resistance of working surfaces;
- high efficiency;
- quiet and smooth running;
- high kinematic transmission accuracy;
- high fatigue strength of teeth.
These requirements can be realized with the help of thermal, chemical-thermal, finishing, finishing, hardening by PPD.
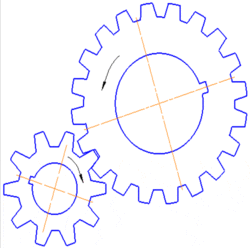
Figure 1 – Gear drive (animation: 8 frames, 65 KB)
3.2 Signs of declining health gears
The main signs of reduction of operational properties of gears [3]:
- Noise in work. It occurs as a result of impacts and friction of conjugate pairs of teeth. The reasons can be: increased side clearances, pulsating sig-variable loads, the mutual sliding of the profiles of the edge contact.;
- Mechanical. It occurs due to the friction of the working profiles in the absence or insufficient amount of lubricant in the contact spot of the teeth. The presence of solid particles of wear products in the lubricant.;
- Dyeing. The cause may be contact stresses, hydrodynamic phenomena in the lubricant.;
- Fatigue wear. Accompanied by the appearance of cracks in the working profile of the teeth. Causes: contact stresses, dynamic loads are different in magnitude and direction.;
- Oxidative wear. The reason: the work of gears in aggressive environments and in conditions of high humidity.;
- Deformation wear. It is manifested in the form of plastic deformation of the surface layer of the teeth. Reasons: mismatch of mating teeth shape to the theoretical profile. Edge contact. Uneven load distribution along the tooth length.;
- Jamming. Limitation of free running–in of mating teeth.;
Among the features considered, noise in operation, breakage and jamming are caused mainly by violations of the normal working conditions of the gear drive, and wear is a gradual loss of the original shape, size and properties of the LC, and can cause other signs of operational violations characteristics'. Thus, the main task of modern technologies is to reduce the rate of spread of wear of various elements of gears [3].
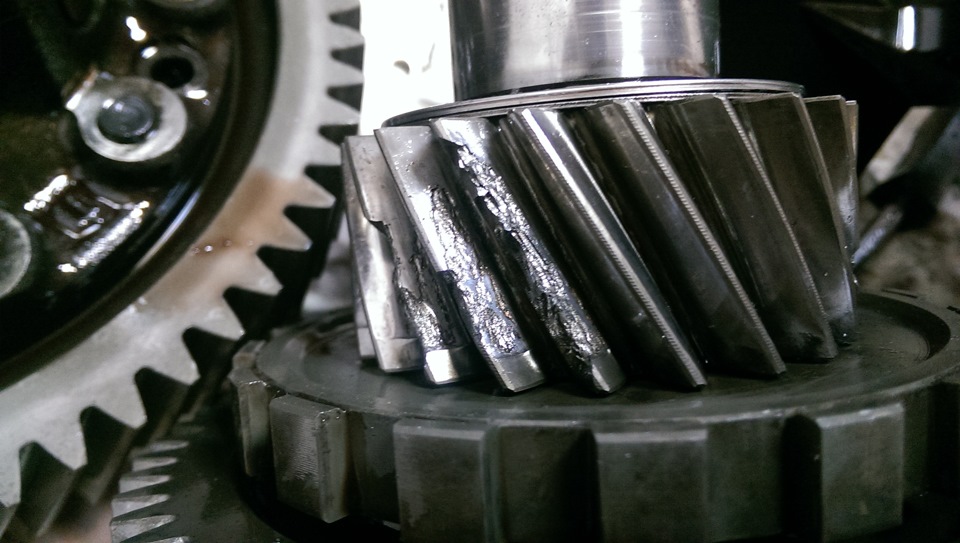
Figure 2 – Effects of gear jamming
3.3 Treatment of gears
The main requirement for the substrate is its low surface roughness (up to Ra=0,08...to 0.16 µm) and a sufficient surface finish, excluding the presence of inorganic inclusions and oil films in the surface layer. The latter is achieved by ultrasonic cleaning and degreasing immediately before placing the products in the coating chamber. Achieving the required surface roughness teeth introduces an additional finishing stages of machining. After achieving the accuracy of the ring gear expressed by the complex parameters corresponding to the specified accuracy class, further finishing of the teeth is performed. Roughness after dimensional tooth treatment should not exceed Ra = 1.6 µm, which can be achieved by gear grinding, stirring or gear honing. Further the treatment should be aimed mainly at smoothing the surface micro-roughness in order to achieve a lower roughness. Polishing is used for this purpose [4]. And to achieve this roughness under the coating requires 3 stages. At the first stage – pre-polishing, an instrument used a cotton or felt a round, knurled abrasive powder of electrocorundum of white granularity 6-3. As a result, the roughness Ra=0.63-0.32 µm is achieved. Circle speed 25-30 m/ s, speed serves 4-6 m/min, the polishing pressure of 0.2 MPa. Final polishing to a roughness Ra=0,32-0,16 microns is made soft cotton circles pismami based on chromium oxide or iron oxide, or thumb microlaparoscopy grain size M28-M14. Speed circle 30-35 m/s, flow 6 m / min, pressure 0.1-0.15 MPa. The third step is polishing to a roughness Ra=0,08-0,04 µm is soft felt circle pasta based on chromium oxide with a grain size microclimatology M10-M7. The speed range 30-35 m/s, the feed speed is 6-8 m/min, tool pressure on the part 0.05-0.1 MPa [4].
4. Summary
The paper considers: requirements for gears, causes of failure and reduction of the operational properties of gears, features of finishing treatment of gear teeth, subjected to the application of wear-resistant coatings. The analysis of the considered features is carried out reducing the properties of gears, and ways to eliminate them. The goals and objectives of future research are set.
References
- Александров Л. И., Артеменко Л. П., Костюк Д. И. Зубчатые передачи. Харьков: Издательство харьковского университета, 1964. 276 с.
- Бароне, Тордьон Точное распределение напряжений в стандартных зубьях и геометрические коэффициенты.//Труды американского общества инженеров – механиков, Серия В, 1973. № 4. С. 271–176.
- Аттиа Шум эвольвентных косозубых колес//Труды американского общества инженеров –механиков, Серия В, 1969. № 1. С. 179–186.
- Адам Я. И., Антонов О. И., Жарков В. В., Копф И. А., Овумян Г. Г. Чистовая обработка зубьев крупных закаленных колес // Вестник машиностроения, 1980. № 9
- Айрапетов Э. Л., Апархов В. И., Мельникова Т. Н., Филимонова Н. И. Неравномерность распределения статической нагрузки в косозубых и шевронных зубчатых передачах // Вестник машиностроения, 1997. № 10.
- Айрапетов Э. Л., Афонский Б Д., Генкин Б. Д., Луценко В. И., Мдинарадзе Н. И. Об анализе кинематической погрешности зубчатых передач с использованием фильтрации// Вестник машиностроения, 1985. № 3.
- Байков А. Н., Шрайбман С. М. Нарезание колес с малым числом зубьев на зубодолбежном станке // Вестник машиностроения, 1973. № 7.