Сравнение методов финишной обработки зубьев зубчатых колес
Авторы: Лебеденко Ю. А., Лахин А. М.
Источник: Студенческий научно-технический журнал ИНЖЕНЕР(№ 1(25)–2(26)'2018)–2018 / Матерiали студентiв, аспiрантiв та молодих вчених – Донецьк, ДонНТУ – 2018, Том 1, с. 53–55.
Аннотация
Лахин А. М., Лебеденко Ю. А. Сравнение методов финишной обработки зубьев зубчатых колес.В данной статье выполнен анализ существующих методов окончательной обработки зубьев зубчатых колес. Произведено сравнение и выбор наиболее рационального метода финишной обработки зубьев ЗК с точки зрения производительности и улучшения качества поверхности зубьев.
1. Введение
В современном мире большинство машин и механизмов трудно представить беззубчатых колес. Хотя имя изобретателя зубчатого колеса неизвестно, определенно его можно назвать одним из великих изобретателей. Свое применение зубчатые колеса нашли еще в глубокой древности. Их применение обуславливалось необходимостью преобразования и передачи механической энергии от природного источника к потребителю. Изначально они отличались своей формой от современных и изготавливались из дерева. Начиная сXVIII в., с развитием таких наук как геометрия, кинематика и механика, профиль зубьев совершенствовался, приобретая более рациональную форму и очертания.
Сейчас зубчатые передачи являются одним из важнейших элементов различных приборов, машин и механизмов. От их качества зависят эксплуатационные свойства и надежность этих машин. Они применяются для преобразования вращательного движения в поступательное, а также для передачи вращательного движения между осями валов.
Применение зубчатых передач обусловлено рядом преимуществ по сравнению с остальными видами передач. Этими преимуществами являются:
- надежность в работе;
- постоянство передаточного числа;
- долговечность;
- высокий КПД;
- простота эксплуатации;
- компактность.
Зубчатые колеса классифицируются в зависимости от конструктивного исполнения:
- цилиндрические;
- червячные;
- конические.
В зависимости от условий эксплуатации к зубчатым колесам предъявляют следующие требования [1]:
- высокий КПД;
- высокая износоустойчивость;
- бесшумность и плавность хода;
- высокая усталостная прочность;
- высокая кинематическая точность передачи.
2. Общее содержание
С развитием машиностроения повысились требования к деталям машин. Возросли требования к долговечности и точности зубчатых передач, что повлекло за собой необходимость создания методов финишной обработки зубчатых колес
Рассмотрим существующие методы финишной обработки зубьев цилиндрических зубчатых колес: шевингование, зубошлифование, зубохонингование, обкатка, притирка.
Шевингование – это процесс отделки зубьев ЗК с помощью специального инструмента (шевера), срезающего с боковых поверхностей зуба стружку (5–15 мм) при скрещивающихся осях шевера и заготовки. Шевингование применяется для чистовой обработки колес с твердостью не более 320...360 НВ с целью уменьшения шероховатости поверхности на профилях зубьев, снижения уровня шума и повышения точности зубчатого зацепления путем исправления шага, направления зуба, профиля. Шевингованием можно повысить точность на одну–две степени. Достигаемая шероховатость – Ra0,8–2,5мкм., 5-6 степень точности. Схема шевингования дисковымшевером приведена на рис.1.
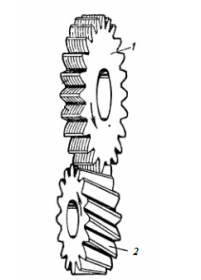
Рисунок 1 – Схема шевингования зубьев ЗК: 1 - шевер, 2 - зубчатое колесо.
Зубошлифование производится в основном при изготовлении колес повышенной точности, термически обработанных до твердости свыше 40 HRCэ. При этом устраняют все виды отклонений и деформаций зубьев, полученных после термической обработки. Различают два метола шлифования: копирования и обкатки. При шлифовании по первому методу шлифовальный круг повторяет профиль впадины обрабатываемого зубчатого колеса, а по второму – боковые поверхности круга воспроизводят зуб рейки в зацеплении с обрабатываемым колесом.Недостатки зубошлифования: низкая производительность, сложность и дороговизна оборудования, возможность появления прижогов и трещин на шлифуемых зубьях. Достигается 4–6 степени точности, шероховатость Ra0,4–1,25 мкм.
Зубохонингование применяют для чистовой обработки зубьев закаленных колес. Обработка выполняется абразивными алмазными зернами из кубического нитрида бора, хаотически расположенными в инструменте. Зубохонингование позволяет устранить небольшие заусенцы и забоины, повысить качество пятна контакта и плавность передачи, уменьшить шероховатость рабочих поверхностей зуба и уровень шума передачи. Недостатком является то, что ввиду малого съёма металла погрешности профиля и другие погрешности практически не устраняются. При зубохонинговании достигается шероховатость Ra 0,1–0,05 мкм.
Обкатка представляет собой процесс совместного вращения обрабатываемого колеса и одного или нескольких рабочих колес под распорной или окружной нагрузкой. Рабочие колеса обычно имеют высокую твердость, так как нагрузка при обкатке достигает 5.. .10 МПа. Время ее, как правило, составляет 1...2 мин. В результате на рабочих поверхностях зубьев образуется наклепанный слой, снижается шероховатость, устраняются заусенцы и забоины. Обкатка способствует увеличению твердости в 1,5–2 раза, уменьшению шероховатости до Ra 0,2–0,6 мкм.
Процесс притирки заключается в том, что обрабатываемое зубчатое колесо вращается в зацеплении с чугунными шестернями-притирами, приводимьши во вращение и смазываемыми пастой, состоящей из смеси мелкого абразивного порошка с маслом. Помимо этого обрабатываемое зубчатое колесо и притиры имеют в осевом направлении возвратно-поступательное движение друг относительно друга: такое движение ускоряет процесс обработки и повышает ее точность. Большей частью движение в осевом направлении придается притираемому зубчатому колесу. Притирочные станки изготовляются с параллельными (рис. 2, а) и со скрещивающимися (рис. 2, б) осями притиров. Притирка применяется для ответственных передач с целью уменьшения шума, повышения их плавности и улучшения пятна контакта. Она дает лучшую по качеству поверхность зубьев, чем шлифование, но при условии правильного изготовления зубчатого колеса, так как притиркой можно исправить лишь незначительные погрешности; при наличии же значительных погрешностей зубчатые колеса необходимо сначала шлифовать, а затем притирать. Притирка дает поверхности высокого качества, она сглаживает микронеровности и придает зеркальный блеск поверхности, значительно уменьшая шум и увеличивая плавность работы зубчатых колес. Шероховатость поверхности после притирки составляет Ra 0,16–0,05 мкм.
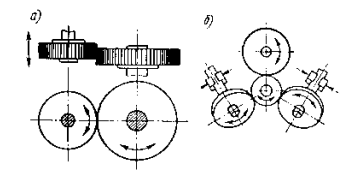
Рисунок 2 – Схемы притирки зубьев цилиндрических зубчатых колес: а - с параллельными осями притиров; б - со скрещивающимися осями притиров.
3. Выводы
В данной статье были рассмотрены такие методы финишной обработки зубьев,как: шевингование, зубошлифование, зубохонингование, обкатка, притирка.
Из вышеизложенного можно сделать вывод, что наиболее производительным и рациональным способом получения точных зубьев является шевингование, применяемое после нарезания зуба, но до термической обработки. После него для исправления небольших искажений в профиле и шаге и получения чистовой поверхности зубьев целесообразно применить притирку и только в случае значительной деформации прибегать к шлифованию зубьев.
Список использованной литературы
1. Овумян Г. Г., Адам Я. И. Справочник зубореза – 2-е изд., перераб. и доп. – М.: Машиностроение, 1983–223с.
2. Калашников А. С. Технология изготовления зубчатых колес. – М.: Машиностроение, 2004–480с.