Особенности отделочной обработки зубьев зубчатых колес перед нанесением покрытий
Авторы: Лахин А. М., Панченко О. Н.
Источник: Студенческий научно-технический журнал ИНЖЕНЕР(№ 1(25)–2(26)'2018)–2018 / Матерiали студентiв, аспiрантiв та молодих вчених – Донецьк, ДонНТУ – 2018, Том 1, с. 23–25.
Аннотация
Лахин А. М., Панченко О. Н. Особенности отделочной обработки зубьев зубчатых колес перед нанесением покрытий. Отделочная обработка зубьев зубчатых колес перед нанесением покрытий.
1. Введение
Зубчатые передачи являются наиболее распространенным видом силовых передач. Качество их работы зависит от точности и качества поверхностей зубьев зубчатых колес, которые достигаются главным образом на этапах отделочной и упрочняющей обработки. Между тем зубчатый венец является элементом со сложным периодическим профилем и получается главным образом путем механической обработки лезвийным инструментом. Это требует высоких затрат трудоемкости механической обработки и назначения дополнительных припусков, связанных с достижением требуемой точности и качества зубьев. Финишная и отделочная обработка зубьев, ввиду большой площадь поверхности зубчатого венца, требует не меньших затрат трудоемкости, которая значительно увеличивается при повышении требований к точности зубчатых колес. Поэтому в настоящее время актуальной является задача повышения производительности и качества отделочной обработки зубьев зубчатых колес.
Для облегчения понимания общих закономерностей колебательных процессов целесообразно начинать их изучение с простых и наглядных систем, например, замкнутая цепь, содержащая конденсатор и катушку индуктивности. Изменение во времени физических величин, характеризующих разные колебательные системы, описывается одинаковыми дифференциальными уравнениями.
Исследование компьютерных программ при моделировании разных способов возбуждения колебаний позволяет определить точностные и частотные характеристики программ.
2. Основное содержание и результаты работы
Как известно, обработка зубчатого венца сводится к следующим этапам:
1. Формообразование зубьев. Осуществляется методом копирования или обкатки на зубо-фрезерных, зубодолбежных, зубострогальных или зубо-протяжных станках. В редких случаях первоначальная форма зуба может быть получена на этапе получения заготовки (накатка зубьев), однако такие зубья нуждаются в последующей механической обработке.
2. Чистовая обработка зубьев. Заключается в снятии тонких припусков лезвийным инструментом с целью достижения заданных параметров точности зубьев. На данном этапе применяются методы чистового зубонарезания, зубодолбления а также зубошевингование.
3. Упрочняющая обработка для обеспечения требуемых физико-механических свойств зубьев. На этом этапе чаше всего применяется закалка рабочих поверхностей зубчатого венца, либо цементация с последующей закалкой. В последнее время в качестве упрочняющей обработки. применяют методы нанесения износостойких покрытий, которые не нарушая размерной точности зубьев, позволяют достичь высокие физикомеханические свойства в соответствии с условиями эксплуатации зубчатых колес.
4. Отделочная или финишная обработка зубьев. На этом этапе осуществляется абразивная обработка зубьев с целью обеспечения точности и качества поверхности, нарушенных при выполнении упрочняющей обработки, и дальнейшего достижения точности для приведения зубчатого колеса к соответствию требованиям чертежа. Используется зубошлифование (методом копирования или обкатки), зубохонингование и притирка зубьев
Следует отметить что зубчатые колеса, подвергаемые нанесению износостойких покрытий, хоть и не требуют дорогостоящей термической обработки, однако имеют некоторые особенности обработки рабочих поверхностей зубьев, поскольку в дальнейшем они являются подложкой под покрытие. При этом важной задачей является достижение достаточной прочности адгезионной связи наносимого покрытия и подложки (рабочих поверхностей зубьев). Основным требованием к поверхности подложки является ее низкая шероховатость (до Ra=0,16…0,08 мкм) и достаточная чистота поверхности, исключающая присутствие в поверхностном слое неорганических включений и масляных пленок. Последнее достигается ультразвуковой мойкой и обезжириванием непосредственно перед помещением изделий в камеру для нанесения покрытий. Достижение требуемой шероховатости поверхностей зубьев вводит дополнительные этапы отделочной механической обработки.
После достижения точности зубчатого венца, выражаемой комплексом параметров соответствующих заданному классу точности, производится дальнейшая отделочная обработка зубьев. Шероховатость после размерной обработки зубьев не должна быть более Ra=1,6 мкм, что может быть достигнуто зубошлифованием, шевингованием или зубохонингованием. Дальнейшая обработка должна быть направленна главным образом на сглаживание микронеровностей поверхности с целью достижения более низкой шероховатости. Для этого используется полирование [2]. Причем для достижения указанной шероховатости под нанесение покрытия требуется 3 этапа. На первом этапе – предварительное полирование, в качестве инструмента используется хлопчатобумажный или фетровый круг, накатанный абразивным порошком электрокорунда белого зернистостью 6-3. В результате достигается шероховатость Ra=0,63-0,32 мкм. Скорость круга 25-30 м/с, скорость подачи 4-6 м/мин, давление полировального круга 0,2 МПа. Окончательное полирование до шероховатости Ra=0,32-0,16 мкм производится мягкими хлопчатобумажными кругами пасмами на основе окиси хрома или окиси железа, или накатанные микрошлифпорошком зернистостью М28-М14. Скорость круга 30-35 м/с, подача 6 м/мин, давление 0,1-0,15 Мпа. Третий этап – глянцевание до шероховатости Ra=0,08-0,04 мкм производится мягким войлочным кругом пастой на основе окиси хрома с зернистостью микрошлифопорошка М10-М7. Скорость круга 30-35 м/с, скорость подачи – 6-8 м/мин, давление инструмента на деталь 0,05-0,1 Мпа.
При обработке зубчатых колес наиболее эффективно применять полирование методом копирования, заключающееся в последовательной обработке каждой впадины зубьев и двух противоположных сторон зубьев. Для автоматизации процесса обработки целесообразно использовать устройство [1], представленное на рис. 1.
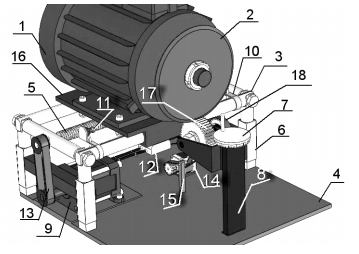
Рисунок 1 – Общий вид устройства для полирования зубьев
Обработка осуществляется быстросменным полировальным кругом 2 на войлочной основе. Вращение круга осуществляется от электродвигателя 1, установленного на суппорте 16. Привод главного движения, вместе с суппортом образуют полировальную бабку. Перемещение полировальной бабки происходит по двум направляющим 3, посредством линейных подшипников. Ходовой винт 5, осуществляющий реверсивное вращательное движение, входит в зацепление с гайкой, жестко связанной с суппортом. При этом вращательное движение винта преобразуется в возвратно-поступательное движение суппорта полировальной бабки. Вращение ходового винта 5 передается от ременной передачи 13 и двигателя 9.
Команды пуск, остановка, смена направления вращения двигателя 9, поворот на требуемый угол вала шагового двигателя 14, выдают контактные импульсные датчики 11, установленные в конечных положениях движения полировальной бабки, и установленные на регулируемых упорах 10. Количество двойных ходов полировальной бабки, требуемых для обработки одной впадины зуба, а также величина угла поворота шагового двигателя, обеспечивающего поворот колеса на один зуб, задается с помощью блока управления 12, основанного на программируемом микроконтроллере. Сигнал о смене направления вращения двигателя ходового винта поступают от блока управления 12 на двигатель 9, а после совершения требуемого количества двойных ходов полировальной бабки на шаговый двигатель 14 поступает импульс, величина которого определяет угол поворота вала шагового двигателя. Преобразование этого угла передаточным числом зубчато-ременной передачи 18 обеспечит требуемый угол поворота зубчатого колеса для обработки следующей впадины. Натяжным роликом 15 осуществляется натяжение зубчатого ремня 18, что позволяет, за счет варьирования расстояния между осями заготовки и шагового двигателя, устанавливать зубчатые колеса различных габаритов без смены зубчатого ремня. Заготовка 17, закрепленная на оправке жестко связанной с ведомым роликом привода шагового двигателя, устанавливается на вертикальном суппорте 8, который перемещается по направляющей с помощью передачи винт-гайка. На маховике винта 7 имеется лимб, с помощью которого производится точная регулировка положения заготовки 17 относительно войлочного круга 2 и задается требуемое усилие прижатия круга к обрабатываемой поверхности. При этом должно обеспечиваться плотное прилегание рабочей части круга к боковым поверхностям зубьев образующих впадину. Все выше перечисленные механизмы смонтированы на плите-основании 4.
После нанесения покрытий стоит задача очистки рабочих поверхностей зубьев от остатков покрытия, осевших, однако не имеющих прочной адгезионной связи с подложкой. Эти частицы покрытия, при их отрывании от поверхности зубьев и попадании в масляную ванну зубчатой передачи, образуют абразивную смесь, которая при попадании в зону зацеплении приведут к интенсивному износу зубьев. Поэтому непосредственно после нанесения покрытий, рабочие поверхности зубьев подвергаются дополнительной обработке – высотно-сглаживающему полировании, в результате которого производится отрыв остатков покрытия и сглаживание рабочих поверхностей. Обработка осуществляется на режимах соответствующих глянцеванию (скорость инструмента 30-35 м/с, скорость подачи – 6-8 м/мин, давление инструмента на деталь 0,05-0,1 МПа). В результате обработки обеспечивается шероховатость поверхности Ra=0,16-0,32 мкм и достигается монолитный слой покрытия без несплошностей. Для предотвращения истирания покрытия при его обработке, используются полировальные пасты с мягким абразивным материалом (пасты на основе окиси железа или хрома).
3. Заключение
Таким образом, в работе рассмотрены особенности отделочной обработки зубьев зубчатых колес, подвергаемых нанесению износостойких покрытий. Предложен эффективный способ полирования зубьев перед и после нанесения покрытий, позволяющий вести высокопроизводительную обработку в автоматическом цикле.
Список использованной литературы
1. Лахин А. М. Особенности нанесения функциональноориентированных покрытий на рабочие поверхности зубчатых колес / А. М. Лахин / Прогрессивные технологии и системы машиностроения: – Донецк: ДонНТУ, 2017. – Вып. 2 (57). – С.1723.
2. Масловский В. В. Полирование металлов и сплавов / Дудко П. Д. // М.: Высшая школа, 1974.–255 с.