Реферат за темою випускної роботи
Зміст
- Вступ
- Теоретична модель траєкторії руху інструмент
- Етапи підвищення ефективності процесу фрезерування
- Висновки
- Список джерел
Вступ
На сьогоднішній момент фрезерування є одним з найбільш часто використовуваних методів отримання поверхні різанням, так як дозволяє отримати деталь практично будь-якої складності. Основним перевагами цього методу обробки є висока продуктивність, точність і якість оброблених поверхонь.
Фрезерування характеризується складною кінематикою і динамікою різання, пов'язаних з переменностью зрізаного шару ударні процесу різання. Питання про підвищення якості обробленої поверхні фрезерної обробки в непростих сучасних економічних умовах стоїть особливо гостро.
Постійне підвищення вимог до точності і якості обробленої поверхні, а також до ресурсу виготовленої деталі призводять до необхідності проведення досліджень за всіма параметрами якості поверхні і розробки на їх основі нових технологічних рекомендацій, що дозволяє отримувати оптимальний комплекс властивостей обробленої поверхні на даному етапі виготовлення деталі.
Теоретична модель траєкторії руху інструменту
Існують чотири принципи генерації траєкторії руху ріжучого інструменту, яким підпорядковані всі підходи до створення УП для високошвидкісної обробки [1]:
- Слід надавати перевагу довгі траєкторії інструменту для різання з невеликою глибиною в осьовому і радіальному напрямках.
- Різання утворює замість торцевого фрезерування. Окружна швидкість прямо пропорційна радіусу інструменту, і навіть при високій швидкості обертання шпинделя вона дорівнює нулю в центрі інструменту (на осі). Сили різання при високошвидкісній обробці істотно зменшуються в напрямку осей X і Y, а в напрямку осі Z практично не змінюються. До того ж при торцевому фрезеруванні видалення стружки утруднено, що негативно позначається на процесі різання.
- Плавна зміна умов різання: умови відводу стружки, зусилля різання в осьовому і радіальному напрямках і так далі. Для інструменту з твердого сплаву більш сприятлива постійна (нехай навіть і висока) температура в зоні різання, ніж її коливання.
Різка зміна умов різання при врізання інструменту в матеріал призводить до збільшення кількості виділеної теплоти та механічної напруги, що негативно позначається на стійкості інструменту. Якщо траєкторія інструменту розрахована за умови плавного зміни умов різання, то це дозволить значно збільшити стійкість інструмента, отримати кращу точність і шорсткість обробленої поверхні.
- Плавні траєкторії інструменту. Застосування функції попереднього аналізу траєкторії з відповідним регулюванням робочої подачі дозволяє запобігти різким врізання в матеріал, так як робоча подача буде відповідати запрограмованому значенню тільки на плавних (особливо на прямолінійних) ділянках траєкторії, а перед різкою зміною напрямку руху інструменту робоча подача буде поступово зменшуватися до деякого значення. При плавній зміні навантаження на інструмент на механічні вузли верстата діятимуть найменші сили. Практика показує, що деталь неможливо виготовити без використання траєкторії, яка передбачає різку зміну напрямку руху інструменту (рис. 1а), але такі випадки необхідно мінімізувати.
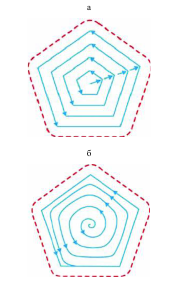
Малюнок 1. Схеми траєкторій руху інструменту:
а – з різкою зміною напрямку;
б – плавний рух
Плавне траєкторія (рис. 1б) більш підходить для високошвидкісної обробки. Трохоідальная обробка – фреза рухається по колу (рис. 2).
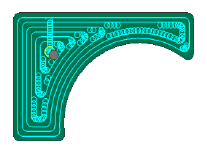
Малюнок 2. Схема трохоідальной траєкторії руху інструменту
Сила різання в напрямку осі Z не зменшується при збільшенні швидкості обертання шпинделя. Врізання в твердий матеріал з високою робочою подачею створить напругу в інструментальному патроні і шпинделі і призведе до пошкодження інструменту. Необхідно уникати вертикального врізання інструменту (за винятком графіту, алюмінію і деяких інших м'яких матеріалів). Переміщення ріжучого інструменту на величину проходу по осі Z рекомендується проводити в повітрі, а врізання в горизонтальному напрямку – по дугоподібної траєкторії. Бажано і вихід інструменту здійснювати по дузі. Чим твердіше матеріал, тим менше повинно бути значення кута врізання. Наприклад, при обробці стали твердістю 62-65 HRC рекомендується ставити кут врізання не більше 0,5 градуса.
Різання паралельними шарами (фреза рухається послідовно шарами по горизонтальних площинах) – найбільш поширений метод формування траєкторії для попередньої обробки (рис. 3). Перевага цього підходу полягає в простоті програмування при збереженні глибини фрезерування. При обробці паралельними шарами генеруються проходи для остаточної обробки бічних стінок кишень або островів. Однак для обробки плоских поверхонь (низ кишені або верх острова) така техніка не зовсім підходить, і тут краще застосовувати інші методи. Деякі CAM-системи дозволяють програмувати траектории для обробки комбінованіх поверхонь [2].

Малюнок 3. Модель обробки сложнопрофільних поверхні паралельними шарами
Одна з проблем обробки паралельними шарами – зміна кроку по осі Z. Тільки частина САМ-систем автоматично визначають різні значення приросту по осі Z в залежності від кута нахилу стінок, більшість же - не може. Технолог-програміст змушений вручну розділяти поверхню на області і вказувати різні значення кроку по осі Z, щоб отримати оптимальну шорсткість поверхні похилих і вертикальних стінок.
Етапи підвищення ефективності процесу фрезерування
Фрезерування бічними лезами кінцевих фрез широко поширене в загальному машинобудуванні і авіабудуванні. Наведемо приклад деталі, що виготовляється на ПАТ Роствертол
(рис. 4). Це вилка, за допомогою якої кріпиться лонжерон до несучого гвинта вертольота. До внутрішньої поверхні вилки пред'являються високі вимоги до якості поверхні, так як параметри точності і якості поверхні впливають на довговічність вузла кріплення, і, отже, на ресурс вертольота. Дані по втомним випробувань вузла кріплення лонжерона з несучою системою вертольота за допомогою вилки, виконані в умовах ПАТ Роствертол
показують, що зниження висоти хвиль з 12 до 6 мкм дозволяє в 2 і більше разів підвищити втомну довговічність. Це визначає вимоги до якості поверхні аналогічних виробів. На усталостную довговічність впливає і шорсткість.
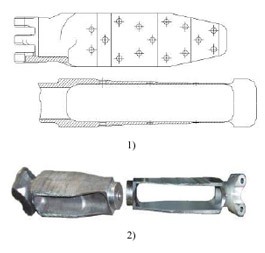
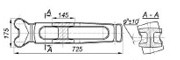
Малюнок 4. Приклад деталі:
1 – ескіз;
2 – фото заготовки;
3 – операційні ескізи обробки наконечника лопаті несучого гвинта.(анімація 4 кадрів, 3 повторення,25,3 кб)
Виконані дослідження дозволили сформулювати ефективний алгоритм вибору і настройки процесу контурного фрезерування кінцевими фрезами при обробці деталей, ширина оброблюваної поверхні яких перевищує діаметр фрези. Цей випадок відноситься до обробки великої номенклатури деталей на підприємствах авіаційної промисловості. Приклад ескізу такої деталі наведено на рис. 5, ескіз технологічної наладки. Значення жорсткості дані по середній лінії деталі. На рис. 5 представлені тільки діагональні елементи матриці. Забезпечення якості деталей, що мають тонкі і маложестких стінки, є багатофакторна проблема. Її рішення включає кілька етапів [3, 4].
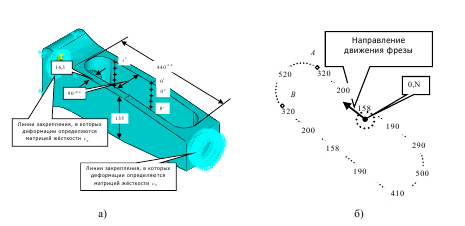
Малюнок 5. Ескіз заготовки при обробці внутрішньої поверхні (а) і приклад розподілу коефіцієнта жорсткості (кг / мм) в напрямку, нормальному до котра утворює (б) (наконечник лопаті 8АТ-270-25)
Перший етап – вибір стратегії обробки. Тут можливі два варіанти. Перший варіант пов'язаний з послідовними проходами для обробки верхньої частини заготовки, потім наступній частині, як показано на рис. 5. Це області 1, 2 і 3.
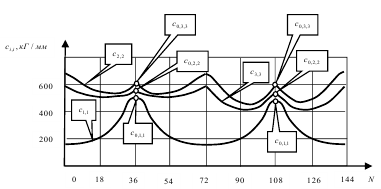
Малюнок 6. Зміни діагональних елементів матриці жорсткості заготовки, матеріал 40ХН2МА
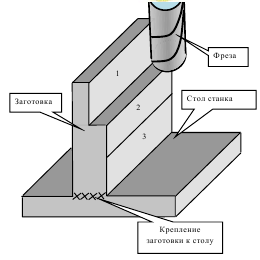
Малюнок 7. Схема першої стратегії обробки тонкостінної заготовки
В даному випадку нижня частина за рахунок підвищеної твердості заготовки зменшує жорсткість оброблюваної частини деталі. Однак на лінії сполучення послідовних проходів (кордони областей 1, 2, 3) завжди утворюється нерівність, яка призводить до похибки форми. Крім цього ефективність застосування такої стратегії істотно знижується. Другий варіант пов'язаний з обробкою відразу всієї поверхні. Він більш продуктивний, але призводить до вищевказаних похибок. З цієї причини необхідно залишати припуск для додаткових чистових проходів. Розглянемо другу стратегію, як більш продуктивну, але складну в аналізі і синтезі [5].
Другий етап – вибір верстата. Для фрезерування поверхні, ширина якої більше діаметру фрези, бажано вибрати верстат з п'ятикоординатне контурним управлінням. Це обумовлено необхідністю компенсації похибки вигинистих деформацій фрези. Крім цього, для компенсації залежно жорсткості деталі уздовж траєкторії руху по котра утворює формованої поверхні необхідно забезпечувати постійне відношення сили до сумарної приведеної жорсткості в напрямку, нормальному до котра утворює. Для цього, як можлива стратегія обробки, розглядається програмне керування швидкістю руху столу у напрямку формованої утворює.
Третій етап – діагностування кінематичних збурень верстата в єдності оцінювання амплітуди радіальних биття шпинделя і варіацій швидкостей подачі руху столу. Для оцінювання кінематичних збурень можна скористатися методикою, викладеної в роботах [1, 2]. Вона заснована на обробці інформації від датчиків зворотного зв'язку по положенню столу, якими забезпечені практично всі верстати з ЧПУ з контурним управлінням. Характеристики кінематичних збурень, представлені, наприклад, автокореляційна функція, характеризують гранично досяжну точність обробки на конкретному верстаті.
Четвертий етап – вибір інструменту. При виборі інструмента необхідно брати до уваги такі особливості.
- Число зубів (крок між зубами фрези), з урахуванням кута нахилу ріжучих лез, має забезпечувати безперервність процесу без перекриття контактів. Діаметр фрези вибирається на основі компромісу між бажанням його збільшити для забезпечення підвищеної жорсткості та необхідністю формування поверхні на ділянках її викривлення (на ділянці «А-В» на рис. 2 б).
- Необхідно забезпечити геометричну точність ріжучих лез фрези. В описуваному випадку точність радіусу ріжучих лез повинна бути в два-три рази вище необхідної точності поверхні. Необхідно враховувати, що при фрезеруванні, на відміну від точіння, формована поверхня безпосередньо визначається всієї геометрією кожного зуба по осі обертання інструменту.
- При заточуванні зубів фрези необхідно вибирати, по можливості, передній кут ріжучого клина не менше 12 ° -15 °. В цьому випадку при русі інструмента орієнтація сили має проекцію, практично збігається з напрямком руху фрези. Тоді на ділянках формоутворення буде мінімальне відхилення інструменту від ідеальної траєкторії.
- Кут нахилу зубів фрези необхідно вибирати таким, щоб осьова складова сили, як зазначено раніше, мала напрям в сторону столу, на якому закріплена оброблювана заготовка. В описаному випадку – це фреза з правого орієнтацією нахилу зубів.
- Рекомендовані значення геометричних параметрів фрези при обробці матеріалу.
П'ятий етап – вибір технологічних режимів і управління.
При обробці деталі, у якій параметри жорсткості залишаються незмінними, величина подачі на зуб при обробці стали 40ХН2МА залежить від вимог до якості формованої поверхні. Вище показано, що показник шорсткості поверхні враховує кінематичну характеристику, зростаючу при збільшенні подачі; траєкторію, що залежить від сформованих притягують множин і самостійні процеси в зоні різання. У міру розвитку зносу інструменту співвідношення між ними змінюється. На початковому етапі основний внесок має кінематична складова. Потім істотно зростає вплив самостійних процесів в хоні різання. Утворює траєкторія залежить від параметрів динамічної системи і еволюційно змінюються параметрів динамічної зв'язку. Крім цього, необхідно враховувати, що при подачі на зуб меншою, ніж 0,01-0,02мм, може спостерігатися збільшення шорсткості за рахунок можливого перескоку траєкторії руху інструменту. При цьому хвилястість може збільшуватися ще більше. Тому, строго кажучи, для забезпечення незмінних значень висоти мікронерівностей необхідно змінювати величину подачі при обробці одного типорозміру деталей.
При обробці деталі, у якій змінюються параметри жорсткості уздовж траєкторії руху інструменту, бажано при побудові програми встановити проміжні вузлові точки для інтерполяції траєкторії, що забезпечує малі варіації відносини сили до значення жорсткості в напрямках, нормальних до оброблюваної поверхні.
При обробці ділянок поверхні, на яких змінюється напрямок руху стола (рис. 2б участок А-В
), додатково необхідно враховувати зміну кута контакту фрези з заготівлею, який впливає на сили різання, і, отже, на пружні деформації і всю динаміку системи.
Швидкість різання вибирається з умов забезпечення стійкості траєкторій. Як відомо [1], з одного боку при збільшенні швидкості зростає запас стійкості, з іншого – при збільшенні частоти обертання інструменту, можливо параметричне самозбудження системи. Теоретичні та експериментальні дослідження [3, 5] показують, що для втрати стійкості в системі досить незначного збільшення частоти обертання шпинделя і швидкості різання. Так як динамічна характеристика процесу різання залежить від зносу інструменту і точності геометрії інструменту, значить, існує оптимальне значення швидкості, при якій одночасно відсутні параметричні самозбудження і система стійка.
На швидкість різання накладаються обмеження, обумовлені відсутністю биття в деформаційних зсувах інструменту на ділянках формоутворення інструмента.
З огляду на вищезазначене, можна стверджувати, що динаміка процесу фрезерування визначається параметрами динамічних підсистем, що взаємодіють з процесом обробки, технологічними режимами і геометрією інструменту. Принципово можливо змінювати всі ці характеристики для забезпечення необхідних показників якості формованої поверхні.
Наведемо приклад ефективності управління процесом на прикладі обробки внутрішньої поверхні вилки кріплення лонжерона до несучої системі вертольота. Вихідні технологічні параметри, покладені в основу побудови програми ЧПУ на чистових проходах, такі: подача на зуб – 0,02 мм; швидкість різання – 0,8 м / с; величина технологічного припуску – 2, 5 мм. Використовувалася четирехзубие фреза з Р6М5 діаметром 60,0 мм з кутом нахилу зуба 35 °. Після динамічного аналізу та експериментальної перевірки встановлено, що частота обертання
Висновки
Запропонований алгоритм (етапи) забезпечує підвищення якості поверхні при фрезеруванні кінцевими фрезами. Він включає вимоги до інструменту, вибору його геометрії, технологічним режимами параметрам точності верстата. У загальному випадку проблема поліпшення мікрорельєфу формується поверхні вирішується за допомогою методу, заснованого на використанні відомостей про акустичний шум, виміряний мікрофоном, з подальшою обробкою інформації. Запропонований метод дозволяє в процесі різання оцінювати граничні стани процесу для отримання інформації про заміну інструменту і його переналагодження.
Розроблені рекомендації щодо вибору параметрів інструменту і технологічних режимів обробки, а також метод для контролю критичного стану процесу можуть бути прийняті до впровадження в реальних умовах на підприємствах авіаційної промисловості.
Список джерел
- Zelinski, P. Five sides and one zero: Shopfloor programming for five-side parts. Mod. Mach./P. Zelins-ki // Shop. – 2003. – 76. – № 7. – С. 54–55.
- Hans, B. Kief. CNC for Industry / Hans B. Kief. – 2000. – Р. 198.
- Заковоротный, В. Л. Определение оптимальных траекторий при обработке с учётом эволюции процесса резания / В. Л. Заковоротный, В. П. Лапшин, А. А. Губанова // Вестник Дон. гос. техн. ун-та. – 2014. – № 3 (78). – С.5–12.
- Заковоротный, В. Л. Синергетическая концепция при построении систем управления точностью изготовления деталей сложной геометрической формы/ В. Л. Заковоротный, А. А. Губанова // Инновационные технологии в машиностроении и металлургии : сб. трудов VI междунар. науч.-практ. конф. – 2014. – С.51–70.
- Заковоротный, В. Л. Определение оптимальных координат переключения циклов обработки в эволюционной динамической системе резания/ В. Л. Заковоротный, В. П. Лапшин, А. А. Губанова // Изв. вузов. Сев.-Кавк. регион. Техн. науки. – 2014. – № 4 (179). – С.59–63.
- Заковоротный, В. Л. Особенности формирования притягивающих многоообразий в окрестности стационарных траекторий попутного фрезерования концевыми фрезами/В. Л. Заковоротный, А. А. Губанова, А. Д. Лукьянов // Вестник Дон. гос. техн. ун-та. – 2016. – № 3 (86). – С.23–38.
- Губанова, А. А. Виброакустическая диагностика фрезерования концевыми фрезами / А. А. Губанова, Н. Н. Черненко// Юбилейная конференция студентов и молодых ученых, посвященная 85-летию ДГТУ [Электронный ресурс] : сб. трудов. науч.-техн. конф. – Ростов-на-Дону, 2015. – С.5089–5091.