Реферат по теме выпускной работы
Содержание
- Введение
- 1. Актуальность темы
- 2. Цель и задачи исследования
- 3. Моделирование процесса штамповки колёсных заготовок на прессах силой 20 МН, 50МН, 100МН
- Выводы
- Список источников
Введение
Актуальным для современной теории колесопрокатного производства является создание методов проектирования технологии деформирования точных по массе (отличие заготовок по массе до 1%) заготовок колес, которые бы обеспечивали высокую точность прогноза формоизменения металла и силовых параметров процессов штамповки и прокатки заготовок. Решение данной проблемы требует изменения постановки соответствующих краевых задач и способов их реализации в соответствии с техниче-скими и технологическими особенностями производства колес на конкретной прессопрокатной линии.
Постановка задачи моделирования. В настоящей работе выполнена постановка задачи моделирования многопереходного процесса деформи-рования заготовок колес с последующей ее реализацией в системе DEFORM 3D.
1. Актуальность темы
Актуальным направлением совершенствования технологии деформирования заготовок колес на прессопрокатной линии является создание технологических схем и режимов деформации металла, позволяющих уменьшить асимметрию штампуемых колесных заготовок и, как следствие, - снизить эксцентричность прокатываемых колес. .
Оборудование прессопрокатной линии, введенное в эксплуатацию более 40 лет назад с одной стороны позволяет обеспечивать высокую производительность технологического процесса, а, с другой, - морально устарело, следствием чего является нестабильность размеров штампованно-катаных колес и повышенная ремонтная обточка.
2. Цель и задачи исследования, планируемые результаты
Данная работа посвящена моделированию процесса штамповки заготовки по новому способу штамповки с частично сформированными ободом и ступицей на заготовочном прессе.
Недостатком существующей технологии является неудовлетворительная центровка заготовки перед ее формовкой в штампах пресса 100 МН. Существующий на прессе центрователь требует постоянной подстройки в процессе работы, что выполняют далеко не всегда, так как для этого необходимо останавливать прокат. В результате этого при высоком темпе прокатки получается большое количество прокатанных колес с нестабильными размерами обода и, как следствие, - повышенная ремонтная обточка.
Преимущество новой технологии: полученная заготовка будет самоцентроваться в нижнем штампе пресса 100МН еще до начала деформации по сформированной посадочной поверхности в зоне ступицы.
Применение предлагаемой технологии позволит стабилизировать размеры колесных заготовок и, соответственно, прокатываемых из них колес.
Для изучения особенностей рассмотренной технологии необходимо выполнить в системе DEFORM 3D конечно-элементное моделирование процесса осадки-разгонки заготовок.
3. Моделирование процесса штамповки колёсных заготовок на прессах силой 20 МН, 50МН, 100МН
Предварительная осадка на прессе силой 20 МН производится с целью уменьшения высоты и увеличения площади поперечного сечения заготовок. Осадку применяют для улучшения структуры и механических свойств металла заготовок, а также для уменьшения неравномерности свойств в осевом и радиальном направлениях.
В процессе осадки удаляется окалина с боковых поверхностей заготовок, а также оставшаяся после гидросбива окалина с торцевых поверхностей. Пресс силой 20 МН – гидравлический вертикальный четырехколонный с архитравом и установленной на фундаменте станиной. Между станиной и архитравом расположена траверса, которая перемещается по колоннам пресса. На станину пресса и опору установлена плита, по направляющим которой перемещается стол пресса. Плита с одной стороны упирается в зуб станины, а с другой подпирается двумя гидроцилиндрами, находящимися под постоянным давлением.
Опускание траверсы осуществляется плунжером рабочего цилиндра, подъем траверсы – двумя подъемными цилиндрами, размещенными в приливах архитрава. К траверсе и столу крепятся осадочные плиты.
Рабочий цикл пресса состоит из опускания траверсы до соприкосновения с заготовкой, рабочего хода – осадки заготовки и подъема траверсы в исходное положение. Опускание траверсы начинается после подачи манипулятором заготовки на стол пресса во время его возврата в исходное положение. Установленная величина осадки обеспечивается системой автоматического управления траверсой. Для контроля высоты осаженной заготовки пресс оборудован указателем хода траверсы в виде дискового циферблата с вращающейся стрелкой. Разнотолщинность осаженных заготовок не должна превышать 2 мм.[1]
Перед подачей заготовки на стол пресса посредством дозаторов осуществляется нанесение технологической подсыпки на середину нижней обжимной плиты с целью предупреждения запрессовки окалины, не отделившейся после гидросбива. Она подается также и на верхнюю торцевую поверхность заготовки.
После осадки заготовка убирается манипулятором из рабочей зоны пресса силой 20 МН. Для предупреждения разогрева и уменьшения износа обжимные плиты после удаления заготовки охлаждаются водой. Окалина с нижней плиты также удаляется водой.
По рольгангу заготовка подается к кантователю, установленному перед прессом силой 50 МН, и кантуется на 180°. Для более полного удаления вторичной окалины торцевые поверхности заготовки перед кантователем и после него подвергаются очистке металлическими щетками, после чего заготовка по рольгангу подается к прессу силой 50 МН. Заготовка на прессе 50МН перед разгонкой - центрируется (путем поднятия кольца).Операции деформации на прессе силой 50 МН производятся с целью регламентированного распределения металла между периферийной и центральной частями заготовки.[2]
Пресс силой 50 МН – гидравлический вертикальный четырехколонный состоит из неподвижных поперечин – станины и архитрава, соединенных между собой колоннами. С пресса силой 50 МН заготовка убирающим перекладывателем перемещается на отводящий рольганг и транспортируется к формовочному прессу силой 100 МН. При этом она подвергается очистки от окалины металлическими щётками.
Деформация заготовки на прессе силой 100 МН производится с целью получения отформованной заготовки с окончательными размерами ступицы и прилегающей к ней части диска, а также подготовки обода и прилегающей к нему части диска для последующей прокатки на колесо-прокатном стане.
Пресс силой 100 МН – гидравлический вертикальный четырёхколонный имеет две неподвижные поперечины – станину и архитрав, соединённые между собой четырьмя колоннами. В архитраве установлен рабочий цилиндр пресса, а также два подъёмных дифференциальных и два уравновешивающих цилиндра. Плунжеры этих цилиндров закреплены на подвижной траверсе. К траверсе крепится подштамповая плита, в которой установлен верхний выталкиватель заготовки. Цилиндр выталкивателя работает совместно с подъёмными цилиндрами траверсы.[2]
Технологический цикл работы пресса силой 100 МН включает следующие операции: укладку заготовки на нижний формовочный штамп; центровку заготовку на штампе; опускание траверсы до соприкосновения верхнего штампа с заготовкой; рабочий ход – формовку заготовку; подъём траверсы в исходное положение; удаление отформованной заготовки с помощью выталкивателей из верхнего и нижнего штампа и выдачу её на рольганг.
Результаты моделирования. На первом этапе исследований было выполнено моделирование процесса остывания заготовки на воздухе при ее транспортировке (время транспортировки – 25с) по рольгангу от печи к осадочному прессу силой 20 МН. Распределение температур в заготовке после ее транспортировки и выдержки (время выдержки –5с) на нижней плите пресса 20МН представлено на рис. 3.1. Средняя температура металла на поверхности заготовки перед осадкой составляет 1260 – 1270°С. Свободную осадку заготовки производят до высоты 117–120 мм. Результаты моделирования процесса осадки заготовки, представлены на рис. 3.2. Полученное значение силы осадки (24,9МН) является для данного пресса максимально возможным. Его достигают при давлении рабочей жидкости 31,4МН/м2.[3][4][5]
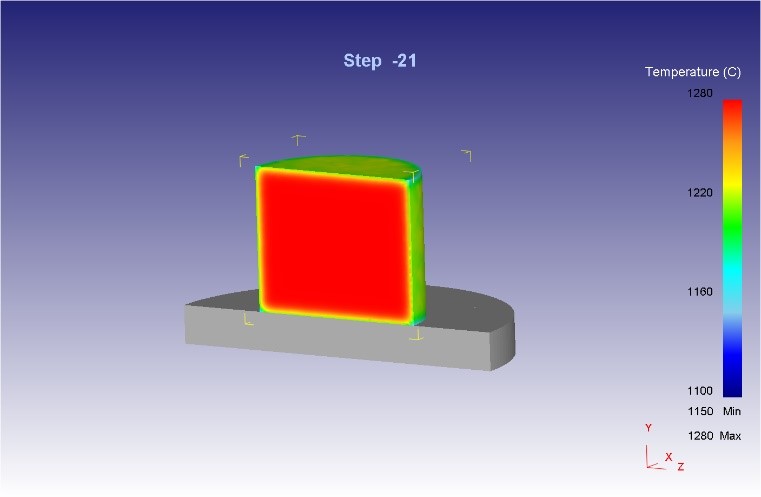
Рисунок 3.1 – Заготовка после ее транспортировки и выдержки на нижней плите
После этого заготовка подается на пресс силой 50 МН (время транспортировки – 10 с) для осадки-разгонки в технологическом кольце. Перед прессом 50 МН заготовку кантуют на 180° для выравнивания температуры с её верхней и нижней сторон. На рис. 3.3 а, б представлено распределение температуры в заготовке до и после её транспортировки к прессу 50 МН, а также после выдержки заготовки (время выдержки – 5 с) на нижней обжимной плите пресса. Средняя температура металла на поверхности заготовки перед разгонкой составляет 1250 – 1260°С.
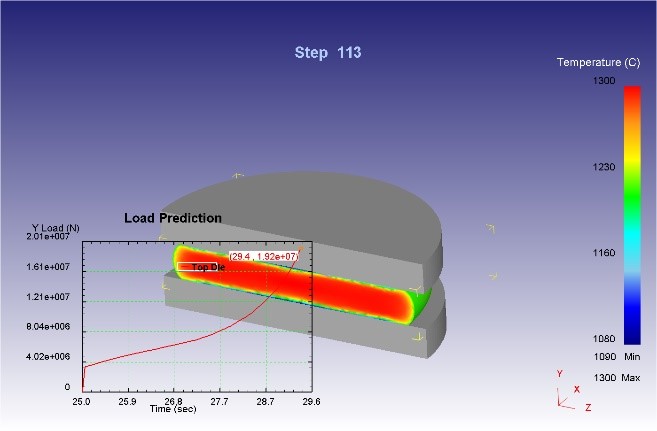
Рисунок 3.2 – Заготовка после ее осадки на прессе силой 20 МН
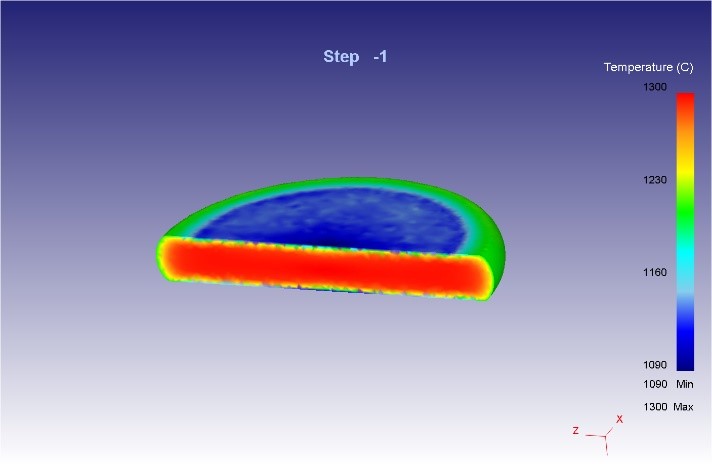
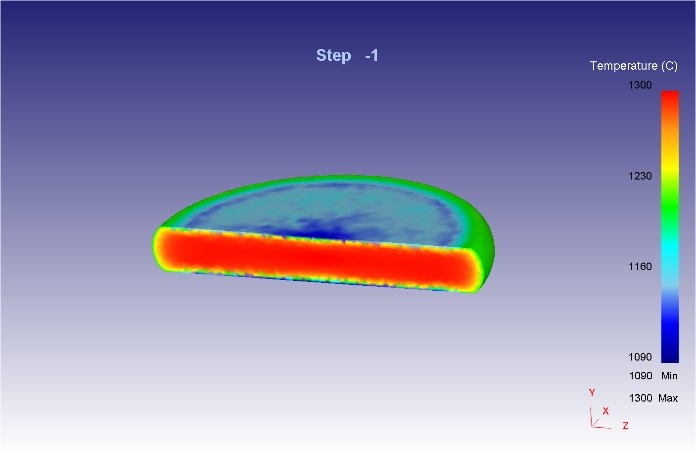
Рисунок 3.3 – Заготовка (а) до и (б) после ее транспортировки и выдержки на нижней плите
На следующем этапе выполняют опускание траверсы пресса до возникновения контакта верхнего штампа с заготовкой. Результаты моделирования процесса до и после разгонки заготовки на прессе силой 50 МН представлены на рис. 3.4 а, б.
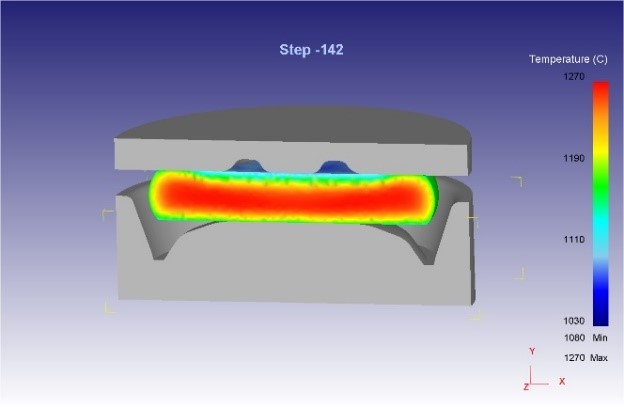
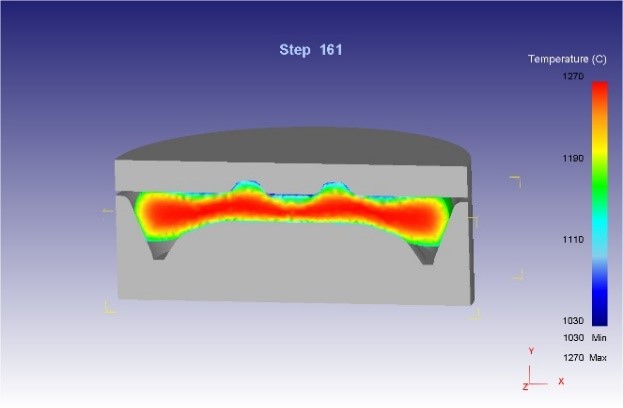
Рисунок 3.4 – Заготовка (а) до и (б) после ее разгонки на прессе силой 50 МН
После разгонки на прессе 50МН, заготовка передается на пресс силой 100МН, где осуществляется формовка. Такая заготовка самоцентруется в нижнем штампе, что обеспечивает стабильность процесса. На рис. 3.5 а, б, представлены результаты до и после формовки.
Выводы
Разработана схема штамповки колесных заготовок, обеспечивающая повышение точности и стабильности размеров получаемых заготовок под прокатку.
За счет сформированного калибра на заготовочном прессе 50МН, заготовка будет самоцентроваться в нижнем штампе формовочного пресса 100МН что обеспечит стабильность процесса.
Выполненный анализ формоизменения и силовых параметров процессов деформации заготовок на прессах 20МН, 50МН и 100МН показал рациональность разработанных режимов деформации.
Полученные при моделировании значения сил штамповки, температур заготовок и параметров их формоизменения хорошо согласуются с экспериментальными данными, полученными в условиях промышленного производства колес диаметром 957 мм.
Список источников
- Яковченко, А.В. Проектирование профилей и калибровок железнодорожных колес : монография / А.В. Яковченко, Н.И. Ивлева, Р.А. Голышков. - Донецк: ДонНТУ, 2008. – 491с.
- Яковченко А.В., Снитко С.А., Ивлева Н.И. Пути совершенствования компьютерных программ проектирования калибровок инструмента деформации для производства штампованнокатаных железнодорожных колес // Металл и литье Украины. - 2003. - № 6. - С. 30-35.
- Гун Г.Я. Теоретические основы обработки металлов давленим / Г.Я. Гун. – М.: Металлургия, 1980. – 456 с.: ил.
- Снитко С.А. Анализ силовых и скоростных параметров прокатки колес / С.А. Снитко // Наукові праці ДонНТУ. Металургія: Зб. наук. пр. – Донецьк, 2008. – Вип. 10 (141). – С. 163 – 172.
- Прогнозирование и способ устранения образования зажимов при формовке колесных заготовок / Б.Г. Каплунов, В.Н. Крашевич, М.И. Староселецкий, А.В. Белущенко // Изв. вузов Черная металлургия. – 1991. – № 1. – С. 55–56.
- Шифрин М.Ю. Резервы производительности и выхода годного при прокатке колес / М.Ю. Шифрин. – М.: Металлургия, 1989. – 144 с.: ил.
- Шифрин М.Ю. Рациональный режим осадки обода колесной заготовки / М.Ю. Шифрин // Сталь. – 1993. – № 5. – С. 52–54.