Abstract
Content
- Introduction
- 1. Theme urgency
- 2. Goal and tasks of the research
- 3. An approach to the unification of synthesis of Moore FSM on FPGA
- Conclusion
- References
Introduction
The need to develop gasification technologies for solid fuels is usually associated with a reduction in the reserves of cheap oil and gas resources. Stocks of solid fuel (coal, biomass, peat) are large enough, and the cost is much lower than for hydrocarbons. In addition, the reserves of solid fuels are distributed more evenly than oil and gas. It is precisely these causes that caused bursts in the intensity of work on this subject in the pre-war years and after the 1973 energy crisis.
Gasification makes it possible to solve the problem of processing waste from forestry, pulp and paper, agricultural, coal-dressing industry, solid household waste, low-grade coals. Despite the large reserves of such energy resources, their use in power engineering by traditional combustion is difficult, since such fuels have a low calorific value due to low carbon content in the fuel part, high humidity, high proportion of noncombustible ballast, and toxicity of combustion products. However, these features do not prevent the processing of fuels by pyrolysis and gasification.
1. Theme urgency
The problem facing the developers of equipment for gasification is the lack of reliable engineering methods for calculating gas-generating equipment. For this reason, in the development of gas generators, an empirical approach is unreasonably important, and the preliminary feasibility studies of such facilities do not allow an adequate assessment of their potential. For complete combustion, such techniques are well known, as the composition of products is easy to assess. In the case of gasification, the composition of products is determined by the physico-chemistry of the processes that proceed. Therefore, the development of mathematical models based on the analysis of the physicochemical features of the gasification process and the search for new approaches to their description is an urgent scientific task, the solution of which can significantly accelerate the design stages of such installations. The problems of the development of engineering methods for calculating the layer combustion of carbon are devoted to the work of Z.F. Chukhanova, H.I. Kolodtseva, B.V. Kantorovich, V.V. Pomerantseva.
2. Goal and tasks of the research
From the urgency of the methods for calculating the processes of gasification, it follows the urgency of creating mathematical models of such processes, which must be sufficiently universal. By universality in this case is understood that when the parameters of the process (such as the technical characteristics of fuels, the dimensions of the apparatus, the costs of blasting and fuel) change within the range of the values ??of interest to the designer, the structure of the model would not change.
Detailed diffusion-kinetic models, which provide the basis for heterogeneous combustion calculations, can not always be used in such wide ranges of parameters. This is due, as already indicated, to the difficulties in the detailed description of phenomena occurring during the gasification of solid fuels, many of which have been studied only to a small extent. Therefore, for calculations using kinetic models, it is necessary to introduce a large number of assumptions and simplifications, the applicability of which can not always be estimated. In this regard, the kinetic model is saturated with uncertain information. You can "tune" the kinetic model in such a way that you can explain the behavior of the system in a certain narrow range of conditions, but the model often loses its universality.
Traditional equilibrium thermodynamic models allow us to calculate processes, the detailed mechanism of which is unknown. However, unlike the processes of complete combustion, with gasification, complete equilibrium is practically not achieved. In addition, at the same time, there is no binding to a particular type of apparatus and the technology used. Therefore, some of the effects can not be investigated using classical thermodynamic models.
3. An approach to the unification of synthesis of Moore FSM on FPGA
The processes of converting fuels into gaseous products are usually described using approximate kinetic schemes, for which the bulkiness of the phenomena is cumbersome and sometimes inconsistent. This is due to the insufficiently developed theory of heterogeneous phenomena in the combustion and gasification of solid fuels. Simpler models - thermodynamic models - can be applied with appropriate consideration of macrokinetic features.
Gasification of solid fuels is used when the target product is a combustible gas. To this end, the fuel is oxidized in such a way as to most fully transfer its chemical energy into the chemical energy of the gas (i.e., its heat of combustion, which is mainly determined by the presence of CO and H2)
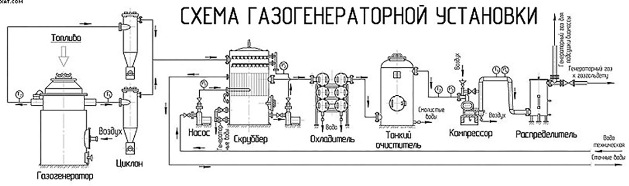
Generator gas can be used for various energy needs - for example, for burning in heating purposes or for generating electricity in gas turbine plants. For low-grade fuels, which can often not be used for direct combustion because of their inherent characteristics (increased ash content, humidity, toxicity), gasification can be most expedient by thermochemical conversion.
There are various options for organizing the gasification of solid fuels. This technology is a dense layer, fluidized bed technology, streaming technology. Separately, the underground gasification of coal, which occurs in the channel, punched in the coal seam.
According to the chemical composition of the blast (ie gas supplied to the gasifier), gasification can be air, steam-air, oxygen, steam-oxygen, steam, and carbon dioxide. Gasification processes can be autothermal (that is, capable of sustainably flowing at the expense of their own heat) and allothermic (that is, requiring external heat).
Technologies of a dense layer are the simplest from a technical point of view. In a dense layer of fuel, different versions of the flow of blasting in relation to the flow of fuel are possible. This is the direct flow of the blast (against the direction of the flow of fuel), the inverted feed (in the direction of the flow of fuel), combined (in both directions) and crosswise (in the perpendicular direction). In the forward process, blown from below, and at the point of its supply a combustion zone is formed, which are mainly exothermic reactions. Further, the heated gas enters the reduction zone, where the combustion products are partially reduced to combustible gases. After that, the gases enter the fuel preparation zone. In this zone, the temperature and concentration of the oxidizer are not sufficient for combustion, but drying and pyrolysis of the initial fuel takes place. In this case, the outgoing gas contains caloric products of thermal decomposition, however, when gasifying low-grade fuels also contains a large amount of resin. To create high temperatures in the combustion zone, a mining method of gasification is used - for this purpose, fuel dust is supplied to the layer with blowing. The combustion of dust creates high temperatures sufficient for liquid slag removal. Due to this, reactions in the reducing zone are intensively proceeding. Thus, it is possible to achieve a high rate of fuel activation.
Reversed blowing is carried out with the flow of fuel. In this case, the combustion zone is located below the preparation zone, therefore the resulting resins are partially decomposed under the influence of high temperature. Below the combustion zone is a recovery zone where the combustion products of fuel and volatiles are reduced to combustible gases. Thus, it is possible to produce a generator gas with a small tar content. However, in this case, fuel preparation is less effective than in the direct process. Therefore, the reversed method of blowing is limited in terms of humidity and ash content of the fuel.
The combined method assumes simultaneous supply of blast from above and from below to the fuel layer. At the same time, a straight process is realized in the lower part of the layer, and in the upper part it is reversed. Generator gas is discharged at the boundary of the reduction zones. Obviously, managing such a process is not easy. Cross-gasification is carried out by blowing through the bed from the side. The zones are in this case analogous to the direct process, however, the zoning occurs over the section of the layer. Due to the complexity of management and the lack of clear advantages over direct and reversed processes, combined and cross-blown methods are rarely used.
The most developed on an industrial scale is the technology of a dense Lurgi layer. Such gas generators were widely used earlier both for power purposes and for the needs of the chemical industry. To date, around 100 such gas generators are used on an industrial scale in the world. Most of them are located in South Africa.
In this paper we consider a dense layer with reversed blowing.
One of the reasons for the high unit cost of gas generating units is the cost of their development. Since reliable engineering methods for calculating the gasification process have not yet been proposed, the development of technologies is basically empirical, using the method of sequential scaling. This is due to the fact that the elementary processes of solid fuel conversion have been studied insufficiently to create a general theory of phenomena in a layer. The main tools therefore are balanced and equilibrium methods of calculation, which do not always justify the expectations of developers of gas-generating equipment.
Conclusion
Thus, it is more expedient to develop hybrid models that, on the one hand, allow describing (even approximate) the macrokinetic behavior of the system, on the other hand, do not overload the model with undefined incoming data and use as simple as possible simple approximations for stages with an unknown mechanism.
References
- Kravtsov V.V. Economic use of coal in heat power engineering / V.V. Kravtsov, A.G. Makhmudov, A.V. Kharchenko - Donetsk: DonSTU, 1999.-320s.Mano M. Digital design / M. Mano. – Prentice Hall, 2003. – 516 pp.
- Shilling G.-D. Gasification of coal / D.-D. Shilling, B. Bonn, W. Kraus. -M .: Nedra, 1968. - 175 p.Barkalov A.A. Synthesis of operational and control automata / A.A. Barkalov, L.A. Titarenko. – Donetsk: DonNTU, TechPark DonNTU UNITECH, 2009. – 256 pp.
- Parakhin M.F. Specialty pittannya spalennya ta term³chnoi perebokki paliva / M.F. Parakhin, V.I. Sheludchenko, V.V. Kravtsov .- Donetsk: RIA DonTU, 1999.- 252p.Avedillo M.J. SMAS: a program for the concurrent state reduction and state assignment of finite state machines / M.J. Avedillo, J.M. Quintana, J.L. Huertas // Proceedings of IEEE International Symposium on Circuits and Systems. – 1991. – vol. 3. – pp. 1781-1784.
- Kravtsov V.V. Development of a technique for determining the temperature in the zone of active burning of solid fuel with additives to air blasting of water or steam. Kravtsov, G.G. Makhov, V.I. Sheludchenko, A.B. Biryukov // Collected scientific works of the Donbass Mining and Metallurgical Institute. Issue 15.Alchevsk: DGMI, 2002.-P.29-30Goren S. CHESMIN: a heuristic for state reduction in incompletely specified finite state machines / S. Goren, F. Ferguson // Proceedings of the Conference on Design, Automation and Test in Europe. – 2002. – pp. 248-254.
- Kravtsov V.V. Heat engineering of thermal processing of solid fuels: a tutorial / V.V. Kravtsov, A.B. Biryukov, I.P. Drobyshevskaya. - Donetsk: Publishing house "Nouvelage", 2011. - 170 p.
- Biryukov A.B. Method of calculation and investigation of the gasification of solid fuel under a mixed scheme / A.B. Biryukov // Metallurgical and mining industry: Scientific and technical and industrial journal. - 2014/1. - No. 3. - P. 115-119p.
- Safianz C.M. Development and analysis of steam generation methods for steam-air blast generation in mixed gas generator production systems / C.M. Safyants, A.B. Biryukov, A.S. Safianz // Metallurgical Heat Engineering: Sat. sci. tr. - Âûï. 6 (21). - Dnepropetrovsk: A new ideology, 2014. - P. 58-65.