Реферат
Зміст
- Вступ
- 1. Кінцево-елементне моделювання схем штампування колісних заготівок
- 2. Результати дослідження
- Висновки
- Перелік літератури
Вступ
Багато задач, з якими доводиться в даний час стикатися дослідникам і інженерам, не піддаються аналітичному рішенням або вимагають величезних витрат на експериментальну реалізацію. Найчастіше єдиною можливістю експрес-аналізу інженерної проблеми є комп'ютерне математичне моделювання. Прогрес в розробці чисельних методів дозволив істотно розширити коло завдань, доступних аналізу. Отримані на основі цих методів результати використовуються практично у всіх областях науки і техніки.
Сучасний технологічний процес, в тому числі металургійний, не може обійтися без активного використання, як комп'ютерної техніки, так і відповідного програмного забезпечення, необхідного для розробки та освоєння нових технологій і, звичайно, для задоволення потреб поточного виробництва (розробка креслень, конструкторської документації, виконання перевірочних розрахунків і т.п.).
1.Кінцево-елементне моделювання схем штампування колісних заготівок
На сьогоднішній день актуальною науково-технічною задачею в сфері виробництва залізничних коліс є вдосконалення схем штампування в частині застосування раціональних силових режимів роботи пресів і високої стійкості інструменту деформації.
У даній роботі буде розглянуто 3 схеми штампування залізничних коліс: розроблена фахівцями SMS Eumuco, фахівцями ВАТ «Євраз НТМК» і працівниками АТ «Виксунський металургійний завод» (далі АТ «ВМЗ»), які реалізовані на підприємствах ВАТ «Євраз НТМК» і АТ « ВМЗ ».
Поряд з отриманням необхідних параметрів по геометрії, макро- і мікроструктурі, а також механічних властивостей виробів, одним з важливих критеріїв оцінки ефективності застосованих схем деформування заготовки є їх вплив на силовий режим пресопрокатного обладнання і стійкість деформуючих штампів.
У колесопрокатному виробництві підвищення стійкості інструменту деформації є актуальним завданням, так як саме цей параметр впливає на витрати, пов'язані з вибором марки стали для штампів, схемою їх виробництва і застосовуванням технологічної мастилом.
Метою даної роботи є вивчення впливу вищезгаданих схем штампування на силові параметри формованого преса R9000 і преса силою 100 МН і величину зносу інструменту деформації (штампів даних пресів).
Аналіз формозміни металу, температурних і силових параметрів, а також знос штампів на формувальних пресах R9000 і 100 МН був виконаний на основі результатів кінцево-елементного моделювання процесу штампування в середовищі DEFORM-3D.
Для колісної заготовки була обрана пластична модель матеріалу, криві течії металу були розраховані для стали марки Т (ГОСТ 10791-2011) для технологій SMS Eumuco, ВАТ «Євраз НТМК» і АТ «ВМЗ».
Заготівля мала нерівномірний температурне поле в діапазоні 1100-1280°С, отримане шляхом кінцево-елементного моделювання процесів транспортування заготовки до пресу R5000, деформації заготовки на даному пресі і транспортування до пресу R9000 для технологій SMS Eumuco і ВАТ «Євраз НТМК». Для технології АТ «ВМЗ» температура заготовки становила 1080-1260°С, яка була досягнута шляхом моделювання процесів транспортування заготовки до осадового пресу 20 МН, деформації на пресі 20 МН, транспортування до пресу 50 МН, деформація на даному пресі і транспортування до пресу 100 МН.
Отримати реальні значення величини зносу інструменту деформації не має можливості через брак інформації для розрахунку даного параметра за допомогою закладених в програму DEFORM-3D інструментів, то можливий лише порівняльний аналіз величини зносу штампів щодо кількох технологій.
При порівняльній оцінці різних схем штампування колісних заготовок враховували тільки абразивний знос. Для розрахунку величини зносу використовували модель Арчарда.
Напруга контактного тертя визначили, як частку від величини напруги течії металу на зрушення.
2. Результати дослідження
Виконано аналіз трьох схем штампування колісної заготовки (малюнок 1-3) для коліс діаметром 957 мм з плоскоконічним диском по ГОСТ 10791-2011:
- Схема штампування з попередньою осадкою гладкими плитами колісної заготовки в верхньому плаваючому калібрувальному кільці (дана технологія в даний час застосовується на пресопрокатной лінії ВАТ «Євраз НТМК»;
- Схема штампування з попереднім формуванням заготовки на пресі R5000 (дана технологія була розроблена фірмою SMS Eumuco і впроваджена на підприємстві ВАТ «Євраз НТМК»);
- Схема штампування з попередньою осадкою заготовки на гладких плитах преса силою 20 МН і «розгінкою» в нижньому технологічному кільці на наступному пресі силою 50 МН (технологія використовується на підприємстві АТ «Виксунський металургійний завод»).
Результати моделювання показали, що при штампуванні колісних заготовок за всіма трьома схемами температура штампів в останній момент штампування не перевищує 300°С.
В результаті аналізу було встановлено, що при штампуванні колісної заготовки по схемі 1, штампи в зоні ступеці заповнюються задовго до закінчення процесу формування (малюнок 1б), що передбачає роботу преса в екстремальних умовах при максимально допустимій силі формування. В результаті цього, в ряді випадків, має місце недоштамповка колісної заготовки в зв'язку з тим, що необхідна для продовження деформування металу сила, навіть з урахуванням роботи преса в режимі витримки під навантаженням, перевищує допустиму величину (90 МН). Крім цього, доштамповка колісної заготовки в режимі витримки, що розвивається максимально пресом сили протягом 2 - 4 с, призводить до збільшення тривалості контакту деформованого металу з інструментом і, отже, до його додаткового розігріву, що зменшує термін служби деформуючих штампів.
При штампуванні колісних заготовок за схемами 2 і 3 силовий режим роботи преса є більш раціональним, тому що величина середньої сили для умов формування в цьому випадку менше більш ніж на 25% від величини відповідної середньої сили при штампуванні за схемою 1 і характеризується поступовим наростанням необхідної для реалізації процесу формування сили, що видно на графіках (малюнок 2б; 3б). Її максимальна величина потрібна лише в останній, короткочасний момент штампування (малюнок 2в; 3в). При цьому робота преса R9000 і преса силою 100 МН в режимі витримки під навантаженням, як при штампуванні за схемою 1, не потрібна.
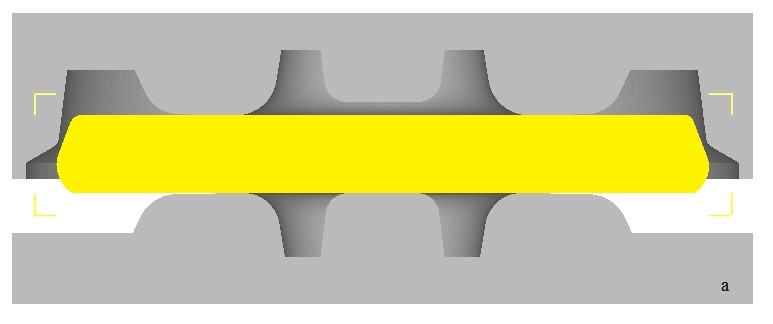
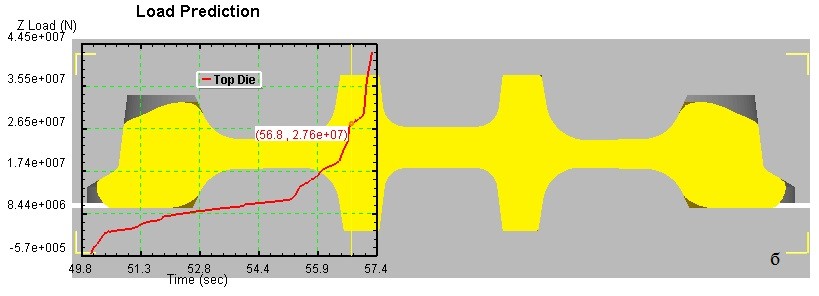
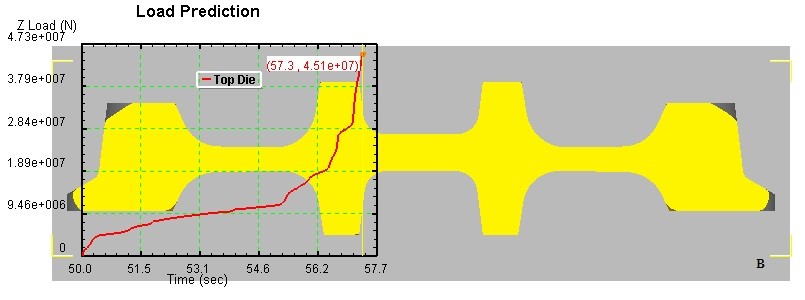
Малюнок 1 – Штамповка колісної заготовки за схемою 1: а – перший момент часу; б – проміжний момент штамповки; в – останній момент штамповки.
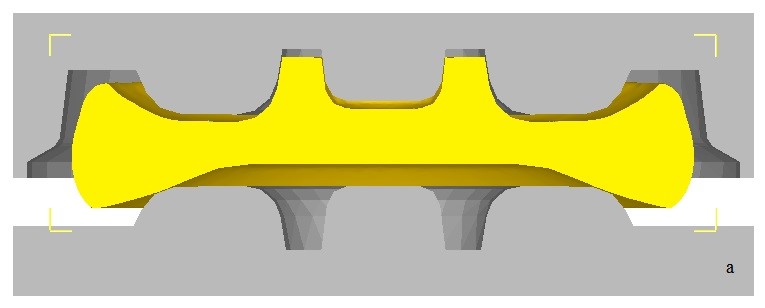
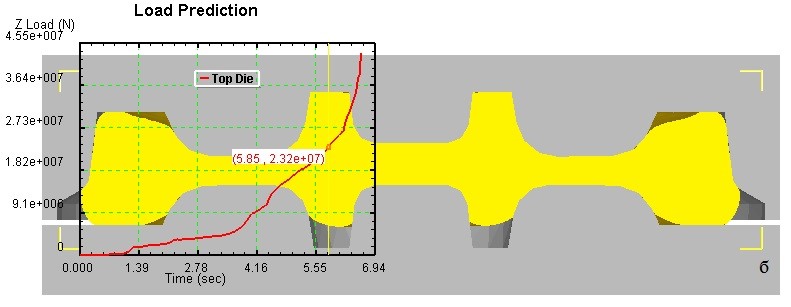
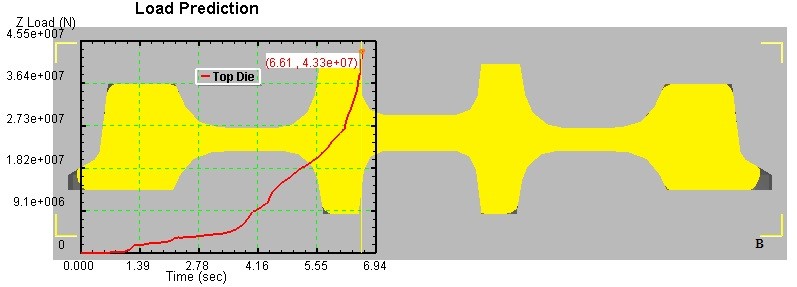
Малюнок 2 – Штамповка колісної заготовки за схемою 2: а – перший момент часу; б – проміжний момент штамповки; в – останній момент штамповки.
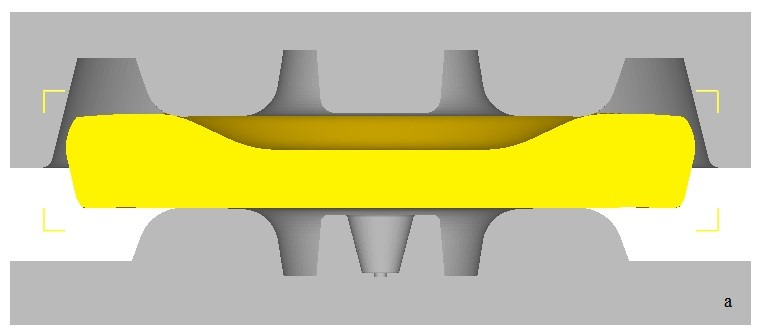
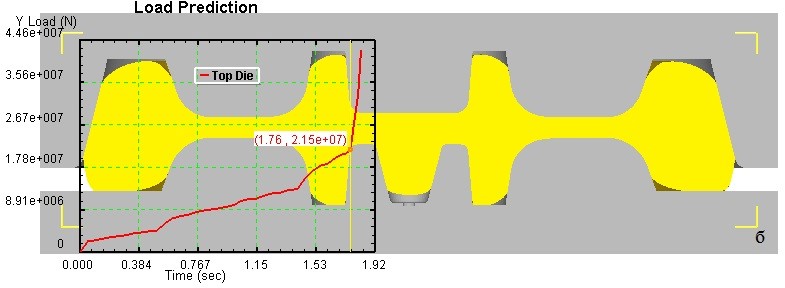
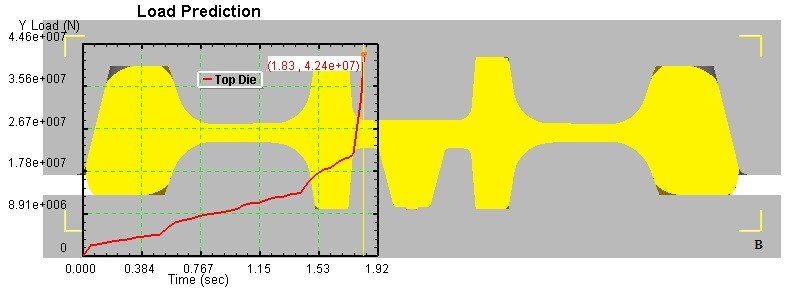
Малюнок 3 – Штамповка колісної заготовки за схемою 3: а – перший момент часу; б – проміжний момент штамповки; в – останній момент штамповки.
На основі результатів моделювання процесу зноса інструменту деформації (малюнок 4-6) можна сформулювати наступні висновки: передчасне заповнення ступеці (схема 1) і реалізація схеми односторонньої течії металу на заключній стадії формування призводить до підвищення величини зносу формувальних штампів більш ніж на 30% (порівняно з іншими схемами) на ділянці формування диска колісної заготовки, тому що саме в цій частині і відбувається основна деформація металу; реалізація схеми формування заготовки з попередньою «розгонкою» (схема 3), крім зменшення величини зносу (щодо схеми 1) призводить до локалізації зносу штампів з ділянки формування диска в ділянку переходу від диска до ступеці і ділянку переходу від диска до обода, причому в другому випадку дана величина в 2 рази більше, ніж в першому; реалізація схеми формування заготовки з попереднім формуванням верхньої частини заготовки (схема 2) в ще більшій мірі зменшує величину зносу інструменту деформації, щодо двох попередніх схем, і при цьому основний знос припадає на ділянку переходу від диска в обід. Знос деформуючих штампів внаслідок передчасного контакту країв заготовки з формувальних кільцем хоч і присутній і практично рівний для всіх трьох схем, проте є незначним у порівнянні з основною величиною зносу.
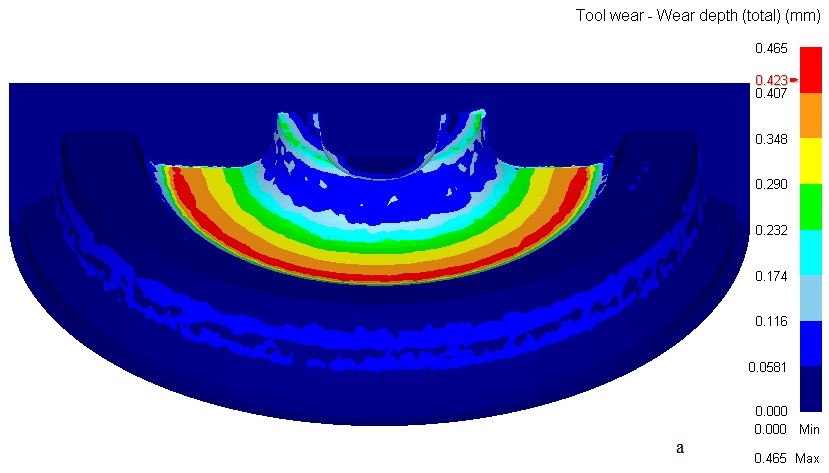
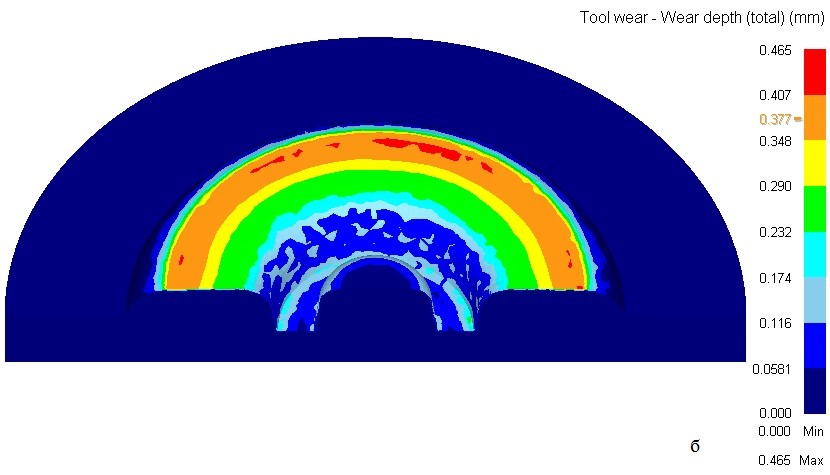
Малюнок 4 – Результати моделювання зноса штампів при штампуванні колісної заготовки за схемою 1: а – верхній штамп; б – нижній штамп
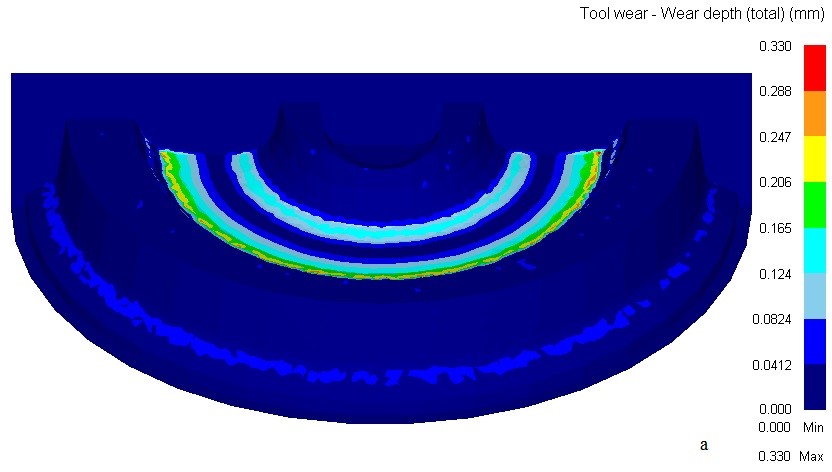
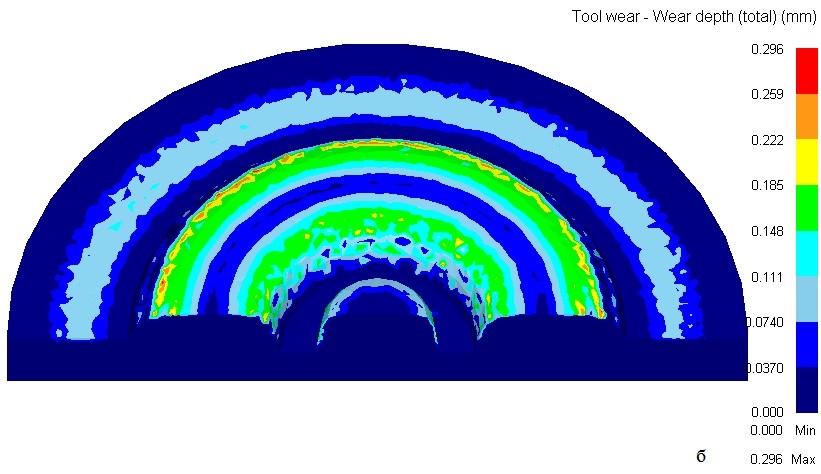
Малюнок 5 – Результати моделювання зноса штампів при штампуванні колісної заготовки за схемою 2: а – верхній штамп; б – нижній штамп
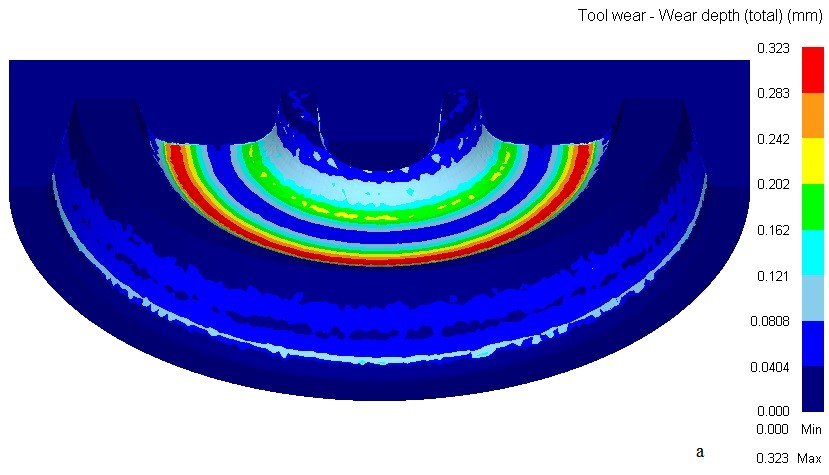
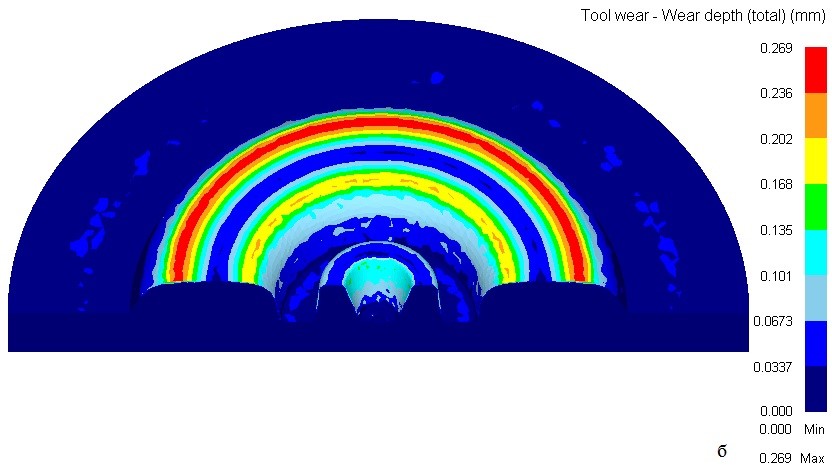
Малюнок 6 – Результати моделювання зноса штампів при штампуванні колісної заготовки за схемою 3: а – верхній штамп; б – нижній штамп
Висновки
Таким чином, на основі результатів кінцево-елементного моделювання виконано аналіз впливу схем штампування колісних заготовок на силові режими роботи формувального преса і знос інструменту деформації.
Показано, що використання схем штампування, які передбачають регламентований розподіл металу між її центральної та периферійної частинами, характеризується раціональним силовим режимом. По-перше, величина середньої сили в цьому випадку знижується на 25% від величини середньої сили при штампуванні за схемою 1. По-друге, в цьому випадку має місце поступове наростання необхідної для реалізації процесу формування сили, причому її максимальна величина необхідна лише в останній , короткочасний момент штампування.
Виняток передчасного заповнення ступеці і, відповідно, односторонньої течії металу на заключній стадії штампування сприяє зменшенню середньої величини зносу формувальних штампів більш ніж на 30%. Встановлено, що в процесі обтиску металу в області диска, чим раніше утворюється підпір течією металу з боку формувального кільця, тим менше величина проковзування деформованого металу відносно поверхні формувальних штампів в зонах їх найбільш інтенсивного зносу (переходу від диска до обода) і, як наслідок, менше величина зносу.
Перелік літератури
- Снитко С.А., Дужуржи А.А. Влияние параметров конечно-элементных моделей на точность расчета формоизменения металла и сил при штамповке и прокатке заготовок железнодорожных колес / С.А. Снитко С.А. [Электронный ресурс] // Обработка материалов давлением: сб. науч. тр., Краматорск: ДГМА, 2010. - Вып.1(22) - С. 44 – 48.
- Снитко С.А., Конечно-элементное моделирование многопереходного процесса деформирования заготовок при производстве железнодорожных колес / С.А. Снитко, В.Л. Калюжный [Электронный ресурс] // Вісник Національного технічного університету України “Київський політехнічний інститут”. Серія: Машинобудування / Київ: КПІ, 2010. – Вип. 62. – С. 53 – 62.
- Снитко С.А., Яковченко А.В., Ивлева Н.И. Компьютерное проектирование прессового инструмента деформации для штамповки колесных заготовок [Электронный ресурс] // Вестник ДонНТУ. – 2016. – №5(5)’2016. – С. 22 – 30.