ТЕХНОЛОГИЧЕСКИЕ РЕШЕНИЯ ДЛЯ ПОВЫШЕНИЯ КАЧЕСТВА ПОВЕРХНОСТИ ТОНКОСТЕННЫХ СИТАЛЛОВЫХ ОБОЛОЧЕК
Олейник С. Ю.
В статье представлен анализ технологических решений и способов, которые обеспечивают повышение качества и точности поверхности сложнопрофильных оболочек. Рассматривается технология обработки крупногабаритной оболочки сложной формы из ситалла. Результатом этой работы является обобщение информации о составе и взаимодействии входных факторов. Для повышения качества поверхности определены направления дальнейших исследований. Актуальными направлениями является разработка рациональных схем обработки, которые будут положены в основу компоновки нового специального станка; разработка математической модели формирования геометрии поверхности с учетом схемы резания, режимов обработки, сложного профиля изделия, вибраций в технологической системе, напряженно–деформированного состояния в зоне резания для их использования при разработке управляющих программ для станков с CNC.
Снижение трудоемкости обработки тонкостенных изделий сложной формы, в том числе крупногабаритных оболочек из труднообрабатываемых хрупких неметаллических материалов, является актуальной задачей на сегодняшний день.
Наиболее широко подобные изделия представлены среди элементов аэрокосмической и ракетной техники, что определяет их эксплуатационные характеристики. К таким характеристикам относятся: конструкция изделия (высокоточная тонкостенная сложнопрофильная оболочка), обеспечивающая требуемые аэродинамические характеристики; определенные радиотехнические свойства (например, радиопрозрачность), для обеспечения которых должны быть выдержаны высокая точность толщины стенки детали (отклонение толщины не более ±0,02 мм [1] и требуемый уровень микро– и макро– геометрии наружного профиля; высокие прочностные характеристики с учетом работы в высокотемпературном режиме, обеспечение которых предполагает отсутствие дефектного слоя в обработанных поверхностях изделия. В качестве материала используется неорганические стекла, техническая керамика, ситаллы, обладающие определенным комплексом физико–механических свойств, позволяющих выполнить все перечисленные выше требования при относительно небольшой массе изделия.
В данной работе рассматривается технология на примере обработки крупногабаритной ситалловой оболочки сложной формы (профиль содержит цилиндрическую, параболическую и коническую части) длиной до 1 м, диаметром цилиндрической части 350 мм, толщиной стенки на этапе алмазного шлифования 7 мм. Из–за несовершенства технологии заготовительных операций обеспечение требуемого качества изделий предполагает многоэтапную механическую обработку. Заданная высокая точность профиля изделия обеспечивается на операциях механической обработки, которые включают черновые и чистовые операции шлифования внутреннего и наружного контуров, на которых удаляется основной припуск (до 8–9 мм на сторону). При этом алмазно–абразивная обработка ведется способом глубинного шлифования (глубина резания от 0,5 до 2 мм), которое сопровождается хрупким разрушением обрабатываемого материала и формированием нарушенного обработкой дефектного слоя.
Алмазное шлифование тонкостенных оболочек вращения происходит в условиях динамической нестабильности процесса резания, которая обусловлена неравномерной жесткостью подсистемы шпиндель–оправка–заготовка
по длине оболочки; неравномерностью сил
резания в процессе шлифования при перемещении круга по формируемой поверхности изделия; быстрым и неравномерным износом шлифовальных кругов; биением и огранкой алмазного инструмента [2, 3]. В результате формируется профиль изделия, который характеризуется волнистостью с переменными шагом и высотой для различных участков заготовки
вдоль её оси. Окончательная механическая обработка поверхности осуществляется доводкой
алмазными брусками, которая в виду сложности профиля изделия производится вручную,
что увеличивает трудоемкость получения готовой детали.
Для обеспечения заданных прочностных свойств изделия после его механической обработки в зависимости от наличия, глубины и структуры нарушенного обработкой поверхностного слоя проводится операция химического травления, на которой полностью удаляется дефектный слой, с последующим ионным упрочнением сформированной поверхности.
Целью статьи является анализ технологических решений и формирование задач для совершенствования технологии получения тонкостенных ситалловых оболочек в условиях современного производства.
Проведенные ранее исследования [4, 5, 6] позволили определить основные факторы, влияющее на эффективность технологии получения качественного изделия (рис. 1). Под эффективностью, в данном случае, понимается достижение заданной точности изделия и качества поверхности при снижении трудоемкости, что возможно при исключении операции ручной доводки и достижении точности по толщине стенки на этапе алмазного шлифования, а также снижения глубины дефектного слоя, что уменьшит затраты на операции комбинированного упрочнения поверхности. Важный фактор, влияющий на указанные проблемы – это вибрации во время алмазного шлифования.
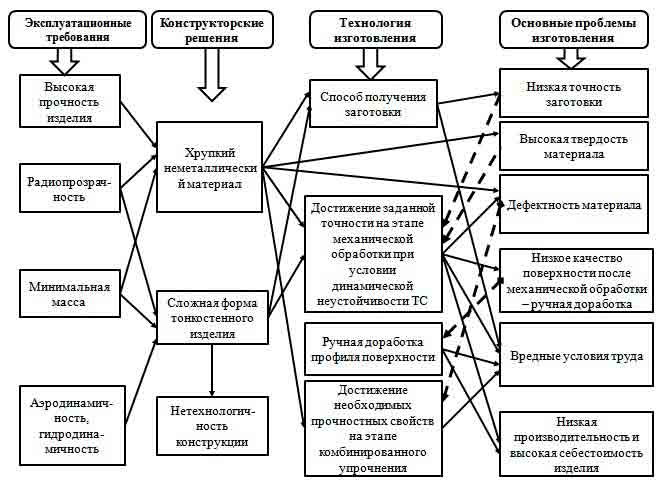
Рисунок 1 – Схема влияния эксплуатационных требований и конструкторско–технологических факторов на качество поверхности оболочек из ситаллов
Параметры качества изделия определяются эксплуатационными требованиями, которые выполняются как за счет конструкторских решений, так и за счет технологии их изготовления. Основные причины снижения качества поверхности и точности изделия представлены на схеме рис. 2.
Проблеме повышения качества подобных изделий уделяется внимание несколько десятилетий, и на отдельных этапах были достигнуты важные результаты. Среди них можно отметить теоретическое и экспериментальное исследование механизма разрушения припуска при силовом резании материала [7]; разработку научного обоснования зависимости дефектности поверхностного слоя изделия от входных технологических параметров; экспериментальное и теоретическое обоснование влияние состава применяемых технологических сред на формирование дефектности поверхности [8].
Перечисленные теоретические разработки стали основой прикладных исследований и разработки технологических способов, которые повышают эффективность производства изделий из хрупких неметаллических материалов.
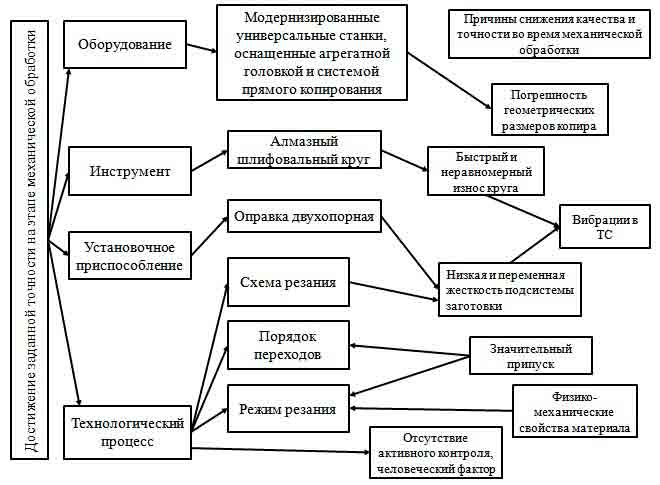
Рисунок 2 – Схема влияния элементов ТС на причины снижения качества поверхности и точности обработки оболочек из ситаллов на этапе алмазного шлифования
К ним относятся исследования, касающиеся оптимальных режимов обработки с учетом получаемых характеристик дефектного слоя [9] и шероховатости поверхности [10], а также рациональных режимов резания с учетом вибраций в ТС (технологической системе) [5]. Исследовано динамическое поведение заготовки–оболочки, толщина стенки которой на окончательных этапах алмазного шлифования достигает 6–7 мм, что при диметре оболочки 350 мм и определенных сочетаниях технологических параметров вызывает её неустойчивое состояние относительно параметрических колебаний.
Предложена схема шлифования, исходя из обеспечения минимального силового воздействия на формируемую поверхность в сочетании с высокой производительностью процесса формообразования (для внутреннего шлифования) [4]. Предложена схема шлифования с перекрещивающимися осями для наружного шлифования. Разработаны варианты приспособлений как для шлифования внутренней, так и наружной поверхности, учитывающие жесткость и вибрации в ТС. Предложены приспособления для активного контроля профиля во время обработки [11]. Разработаны мероприятия, направленные на уменьшение износа шлифовального круга путем применения системы автоматической правки и замены шлифовального круга. Разработана методика разбиения общего припуска, исходя из данных о дефектности, образованной на предыдущей операции [8].
Все предложенные рекомендации апробированы на производстве, некоторые из них внедрены, что позволило повысить качество поверхности и снизить вибрации в ТС, однако это не исключило операции доводки. Требования к современному производству определяют, что для повышения эффективности технологического процесса требуется комплексное применение полученных решений, которые будут реализованы на специальном станке, оснащенном системой CNC.
На предприятиях, производящих подобные изделия, определены основные требования к специальному станку, которые отражают ранее рассмотренные решения проблем механической обработки [12]. К основным требованиям относятся наличие системы CNC, которая обеспечивает сканирование внутреннего и наружного профиля заготовки перед обработкой, учитывая разрабрковку
на операции отжига для автоматического расчета припуска на обработку и расчета режимов резания в зависимости от программы, которую задает оператор; оснащение станка автоматической системой копирования и системой обратной связи, системой автоматической правки и замены кругов, непрерывной подачи СОЖ с возможностью осуществления быстрой и доступной её профилактики и очистки; обеспечение станка самоцентрирующимися приспособлениями для внутренней и наружной обработки; создание условий динамической устойчивости технологической системы во время алмазного шлифования.
Исследование природы колебательных явлений ТС алмазного шлифования тонкостенных ситалловых оболочек [6] показало, что уровень вибраций во время обработки зависит от сочетания параметров режима резания, параметров шлифовального круга. Динамическая устойчивость ТС (отсутствие незатухающих колебаний, при которых возможны значительные динамические нагрузки) зависит от постоянства параметров жесткости её элементов и наличия демпфирования в системе, что определяется схемой резания и приспособлением. На рис. 3 приведена традиционная схема шлифования оболочки в производственных условиях со схематичным указанием изменения величины и направления нормальной составляющей силы резания Pn при перемещении шлифовального круга.
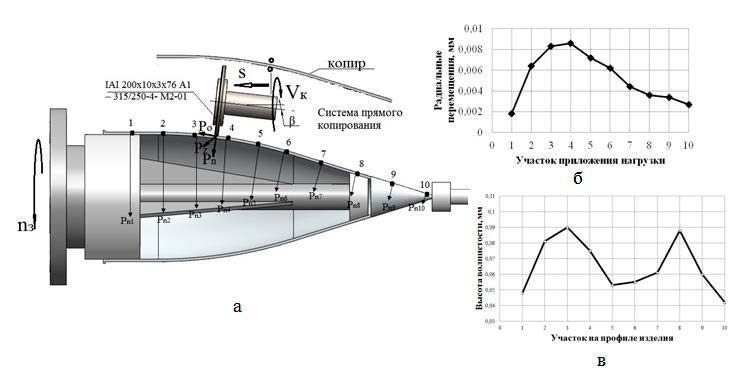
Рисунок 3 – Влияние переменных параметров технологической системы: а – схема шлифования оболочки в производственных условиях с указанием изменения Pn; б – отжатия подсистемы оправка–заготовка
под действием Pn; в – высота волнистости поверхности на соответствующих участках обрабатываемой заготовки
На рис. 3, а показано, что при перемещении шлифовального круга по профилю изделия от участка 10 к участку 1 изменяется величина и направление силы резания. При сочетании с переменной жесткостью ТС алмазного шлифования, износом шлифовального круга, колебаниям толщины стенки оболочки это приводит к вибрациям элементов ТС, появлению переменной точности по толщине стенки (рис. 3, б) и качества поверхности (по параметру волнистости) в направлении продольной подачи (рис. 3, в). Таким образом, влияя через схему резания и параметры процесса резания на нормальную составляющую силы резания, возможно достижение постоянства параметров качества и точности поверхности.
Проведя анализ параметров ТС алмазного шлифования по данным современных исследований, обобщили исходную информацию о составе и взаимодействии исходных факторов. Переменные свойства ТС во время обработки затрудняют получение постоянства заданного качества и точности поверхности. Решение задачи повышения качества на этапе алмазного шлифования может быть получено как с применением системы автоматического регулирования, так и путем разработки математических моделей формирования параметров качества и точности поверхности, с использованием известных экспериментальных и аналитических данных, важной составляющей которых является сила резания, связывающая все параметры рассматриваемой ТС.
Выводы
На основании проведенного анализа существующих технологических решений для повышения качества поверхности тонкостенных ситалловых оболочек определены направления дальнейших исследований в этой области. К ним относятся разработка и исследование рациональных схем обработки, которые будут положены в основу компоновки нового специального станка. При этом предполагается, что конструкция нового станка может иметь отличную от традиционной схемы обработки. Разработка математических моделей формирования параметров качества и точности поверхности с учетом схемы резания, режимов обработки, сложного профиля изделия, отжатий и вибраций в ТС, напряженнодеформированного состояния в зоне резания с целью их использования для создания управляющих программ на станок с CNC. Разработка технологической оснастки с учетом изменения схемы резания.
Литература
- Каплун В. А. Обтекатели антенн СВЧ. Радиотехнический расчет и проектирование / В. А. Каплун. – М. : Сов. Радио, 1974. – 240 с.
- Гусев В. В. Влияние динамики процесса алмазного шлифования на формирование поверхностного слоя изделий из ситаллов / В. В. Гусев, Л. П. Калафатова, Д. В. Поколенко // Новые материалы и технологии в металлургии и машиностроении. – 2007. – № 2. – С. 14–17.
- Исследование динамических характеристик элементов системы СПИД при шлифовании деталей сложной пространственной формы из ситаллов / В. В. Гусев, Л. П. Калафатова, И. С. Каракуц, Д. В. Поколенко // Надежность инструмента и оптимизация технологических систем. – 2007. – №21. – С. 148–155.
- Калафатова Л. П. Влияние схемы шлифования как динамического фактора процесса резания на дефектность и прочность изделий из ситаллов / Л. П. Калафатова // Резание и инструмент в технологических системах. – 2005. – № 68. – 385 с.
- Гусев В. В. Теоретическое исследование влияния режимов обработки на уровень вибраций при алмазном шлифовании тонкостенных оболочек из хрупких неметаллических материалов / В. В. Гусев, Л. П. Калафатова, С. Ю. Олейник // Вестник СевНТУ. Серія : Машиноприладобудування та транспорт : зб. наук. пр. – Севастополь : Изд–во СевНТУ, 2013. – Вип. 139/2013. – С. 57–62.
- Гусев В. В. Повышение виброустойчивости технологической системы во время алмазного шлифования тонкостенных оболочек вращения из ситаллов / В. В. Гусев, Л. П. Калафатова, С. Ю. Олейник // Резание и инструмент в технологических системах : межд. научн.–техн. сб. – Харьков : НТУ
ХПИ
, 2013. – Вип. 83. – С. 86–92. - Ардамацкий А. Л. Алмазная обработка оптических деталей / А. Л. Ардамацкий. – Л. : Машиностроение, Ленингр. отд–е, 1978. – 232 с.
- Калафатова Л. П. Технологічні основи підвищення ефективності обробки та забезпечення якості виробів із технічних стекол і ситалів : автореф. дис. на здобуття наук. ступеня д–ра техн. наук: спец. 05.02.08
Технологія машинобудування
/ Калафатова Людмила Павлівна; НТУХарківський політехнічний інститут
– Харків, 2001. – 26 с. - Гусев В. В. Назначение режимов резания при алмазном шлифовании конструкционной керамики / В. В. Гусев // Наукові праці ДонНТУ. – 2006. – № 110. – С. 6–5.
- Шкарупа М. И. Повышение эффективности механической и физико–технической обработки деталей типа оболочек вращения из конструкционной керамики: автореф. дис. на соиск. уч. степ. канд. техн. наук: 05.02.07
Технология и оборудование механической и физико–технической обработки
/ Шкарупа Михаил Игоревич; РУДН – М., 2011. – 23 с. - Королёв Д. А. Автоматизация технологического процесса механической обработки и контроля оболочек двойной кривизны из керамических материалов: автореф. дис. на соискание уч. степени канд. техн. наук: спец. 05.02.07
Автоматизация в машиностроении
/ Королёв Дмитрий Александрович; УДН. – М., 2010. – 23 с. - Поколенко Д. В. Підвищення ефективності обробки антенних обтічників із ситалів за рахунок удосконалення технології алмазного шліфування: автореф. дис. на здобуття наук. ступеня канд. техн. наук: спец. 05.02.08
Технологія машинобудування
/ Поколенко Дмитро Валерійович; . ДонНТУ – Донецьк, 2014. – 20 с.