ВЛИЯНИЕ СОСТАВА СМАЗОЧНО–ОХЛАЖДАЮЩИХ ТЕХНОЛОГИЧЕСКИХ СРЕД НА ТЕПЛОВЫЕ И СИЛОВЫЕ ХАРАКТЕРИСТИКИ ПРОЦЕССА ШЛИФОВАНИЯ СИТАЛЛОВ
Калафатова Л. П., Поезд С. А.
Одним из факторов, которые существенным образом изменяют ситуацию в зоне шлифования, являются смазочно–охлаждающие технологические среды (СОТС), применение которых обязательно при абразивной обработке хрупких неметаллических материалов (ХНМ) [1]. Даже при оптимизации всех других параметров, которые определяют состояние технологической системы при обработке, использование СОТС с направленными свойствами дополнительно повышает эффективность процессов резания за счет изменения условий протекания процессов диспергирования обрабатываемых материалов (ОМ) в зоне резания.
При силовом воздействии инструмента и под влиянием СОТС изменяются прочность, теплофизические характеристики, химические и физико-механические свойства ОМ [2]. Кроме того, и свойства самого инструмента претерпевают изменения в процессе резания, что зависит от состава и характеристик сред. Влияние СОТС на процесс алмазного шлифования (в особенности тонкого) связан как с изменением характера разрушение поверхностного слоя обрабатываемого материала, так и с созданием условий, которые изменяют скорость износа алмазных зерен и связки инструмента. Среда, активно взаимодействуя со связкой инструмента, провоцирует образование вторичных структур и тем самым активирует или замедляет износ алмазного инструмента, влияет на адгезию частиц диспергированного материала к поверхности связки.
Известно [3], что при шлифовании основными функциями СОТС являются следующие: обеспечение эффективного отвода тепла из зоны резания (охлаждающая способность); обладание смазывающей способностью, проявляющейся в создании смазочных пленок в зоне контакта инструмента и ОМ, и снижения за счет этого трения между ними; наличие диспергирующего действия, позволяющего за счет эффекта П. А. Ребиндера [4] разупрочнить приповерхностные слои ОМ и тем самым облегчить процесс шлифования. Наличие этого эффекта при шлифовании сопровождается снижением обеих составляющих силы резания: как тангенциальной составляющей Pz, ответственной за интенсивность удаления материала припуска, так и радиальной составляющей Py, влияющей на уровень силового воздействия на обрабатываемую поверхность и приводящей к развитию дефектного слоя.
Смазывающее действие и теплоотвод из зоны резания важны не только с точки зрения уменьшения скорости износа инструмента, но и как средство уменьшения термических напряжений в поверхностном слое хрупких материалов, которые могут приводить к появлению дополнительных дефектов в обработанной поверхности. Реализовать эти требования в сочетании с диспергирующим действием возможно за счет использования поверхностно–активных технологических сред. Механизм разрушающего действия среды связан с проникновением тончайших ее пленок на уровне слоев молекул в деформируемый материал, и разупрочнении его поверхностного слоя. При этом мельчайшими каналами, по которым проходит жидкость, являются микротрещины, присущие как исходной структуре самого обрабатываемого материала, так и возникающие при обработке. Поверхностно–активные вещества стимулируют этот процесс. Соответственно представлениям о химической специфичности влияния адсорбционноактивных сред на прочность твердых тел [4] наибольшее облегчение процессов диспергирования ОМ вызовут поверхностно-активные вещества, близкие к нему по молекулярной природе. Исходя из положений теории П.А. Ребиндера, можно сформулировать требования к физико-механическим свойствам сред, применяемых с целью интенсификации процессов механической обработки большинства ХНМ, особенно материалов на основе стекла. СОТС должны быть полярными; обладать высокой скоростью растекания, соизмеримой со скоростью образования микросколов при резании, для чего они должны иметь низкое поверхностное натяжение, высокое значение движущей силы растекания и малую вязкость [5]. Для большинства хрупких неметаллических материалов такими средами есть вода и водные растворы ПАВ.
Как известно, алмаз является уникальным абразивным материалом, превосходящим во много раз по своей твердости другие абразивы. Тем не менее, при высокой твердости и абразивной способности алмаза он отличается сравнительно низкой теплостойкостью, графитизируясь при температуре 10000°С и окисляясь на воздухе при температуре 7000°С. Его износ в инструменте обычно связывают с поверхностным окислением и графитизацией в результате реакции между моноокисью углерода и сложной поверхностной окисью с образованием углекислого газа и углерода. Показано [3], что температура, обеспечивающая протекание этой реакции (800°C), может возникать в точках соприкосновения стекло—алмаз при шлифовании стекла. Отсюда вытекает ряд важных требований к СОТС, связанных с обеспечением эффективного отвода тепла из зоны резания и обладания повышенной смазочной способностью. Последнее свойство достигается за счет образования на контактирующих поверхностях граничных пленок с малым сопротивлением на сдвиг, что снижает трение между связкой, алмазными зернами и обрабатываемой поверхностью, облегчая работу абразивных зерен. Смазка и повышенный теплоотвод важны не только с точки зрения уменьшения скорости износа алмаза, но и как средства снижения термических напряжений в поверхностном слое обрабатываемого материала, которые могут приводить к появлению в нем дополнительных дефектов.
Снижение сил резания, происходящее за счет облегчения диспергирования обрабатываемого материала в присутствии поверхностно–активных СОТС, сопровождается уменьшением тепловыделения в зоне контакта алмазных зерен с обрабатываемой деталью, что является крайне важным с точки зрения уменьшения скорости их износа. Однако, в настоящее время практически отсутствуют исследования, устанавливающие связь охлаждающих свойств СОТС, используемых при абразивной обработке ХНМ, с уровнем их поверхностной активности по отношению к ОМ.
Исходя из сказанного, целью представляемой статьи является исследование влияния СОТС различных составов и различной степени активности по отношению к обрабатываемому материалу на процесс шлифования ситаллов, в частности, на температуру в зоне обработки и силовые характеристики процесса резания.
Основное содержание работы
Проведенные ранее исследования [6] позволяют заключить, что СОТС для обработки изделий из ХНМ на основе стекла должна представлять собой полярную жидкость, содержащую в своем составе поверхностно-активные добавки, повышающие диспергирующее действие среды и улучшающие ее доставку в зону обработки за счет возрастающей способности к смачиванию и растеканию по поверхности обрабатываемого материала, а также улучшающие смазочную способность среды при создании экранирующих пленок между поверхностями контакта изделия и инструмента. СОТС должна обладать высокими моющими свойствами, обеспечивая за счет этого своевременное удаление продуктов диспергирования материала и изнашивания инструмента из зоны обработки, и пониженной вязкостью. Среда должна быть безвредной для здоровья рабочих, экономичной и простой в приготовлении. В качестве одного из вариантов при разработке таких сред может выступать использование синтетических моющих средств (СМС), предназначенных для бытовых целей, в качестве ПАВ в составе технологических сред для механической обработки ХНМ [6], например, ситаллов. В проведенных исследованиях в качестве ПАВ использовалось бытовое моющее средство ТУ 6–00209651,242–2000 отечественного производства, имеющее следующий состав: вода, анионные ПАВ, лауретсульфат натрия, натр едкий, кокодиэтаноламид, ЭДТА, консервант, минеральные соли. Однопроцентный водный раствор этого средства использовался в качестве основы при приготовлении СОТС для абразивной обработки ситаллов. О поверхностной активности водного раствора этого ПАВ косвенно свидетельствует его практически вдвое меньшее значение поверхностного натяжения по сравнению с водой (0,034 Н/м против 0,072 Н/м). В таблице 1 приведены составы СОТС, которые при проведении исследований использовались при алмазном шлифовании ситалла.
Таблица 1. Состав и свойства испытуемых СОТС
Маркировка СОТС | Состав СОТС | Поверхностное натяжение СОТС σ, Н/м |
СОТС №1 | Вода + 1% кальцинированной соды +10% индустриального масла | 0,041 |
СОТС №2 | Вода + 1% СМС +1% индустриального масла | 0,028 |
СОТС №3 | Вода + 0,8% СМС | 0,034 |
СОТС №1 и №2 содержат в своем составе добавки индустриального масла и представляют собой масляные эмульсолы низкой степени концентрации, что, по данным ряда исследователей [6], тем не менее, должно способствовать повышению смазывающей способности сред. В СОТС №1 присутствует включение технической соды, которую в производственных условиях добавляют к составу водных сред для снижения возможной коррозии станка.
Предполагаемую эффективность используемых жидкостей при шлифовании ситаллов оценивали по величине их поверхностного натяжения σ, Н/м, которое определялось по стандартной методике счета капель (сталагмометрический метод [5]). Как следует из данных, приведенных в таблице, добавление индустриального масла в количестве 10% при практически одинаковом количестве СМС в качестве ПАВ в исследуемых составах жидкостей несколько повышает уровень σ, то есть предположительно снижает диспергирующую способность среды. Рассматриваемые среды обладают практически одинаковой вязкостью и охлаждающей способностью, реально не отличающейся от охлаждающей способности воды.
Была проведена серия экспериментов с целью выяснения влияния СОТС приведенных составов на температуру и силовые характеристики процесса шлифования ситалла АС–418. Эксперименты проводились на плоско-шлифовальном станке 3672 алмазным кругом 1А1 200х10х3х76 А 315/250–4–М2–01. Обработке подвергались образцы из ситалла АС–418 с размером обрабатываемой поверхности 10×20 мм.
В процессе экспериментальных исследований использовались следующие приборы и оборудование: для регистрации сил, возникающих при шлифовании, применялся специальный динамометрический стол, позволяющий измерять радиальную и тангенциальную составляющие силы резания в диапазоне (5–2000) Н с точностью 2,5 Н. Регистрация температуры (до 1000 °С) осуществлялась при помощи искусственной термопары хромель-капель (хромель–константан) (NiCr–NiCu) диаметром 0,2 мм. Термопары прокладывались в специальных пазах, вырезанных в образце, изолировались, после чего образец склеивался эпоксидной смолой, дабы в процессе шлифования СОТС не попадала на спай. Глубина залегания головки термопары – 2 мм.
Запись электросигналов, соответствующих значениям сил резания, осуществлялась на самописце Н338–6П с помощью усилителя АНЧ–8. Запись электросигналов, соответствующих значениям температуры в зоне шлифования, осуществлялась на том же самописце с помощью усилителя постоянного тока. С целью возможности последующей расшифровки записей температуры и сил резания была проведена статистическая тарировка динамометрического стола вместе с усилителем и термопары. Эксперимент проводился при использовании составов СОТС, приведенных в таблице. Для каждого вида СОТС обработка производилась в одинаковых условиях кругом, обладающим определенной режущей способности, по плану полуреплики 23-1, при варьировании режимов обработки в пределах: скорость круга v = (23–41) м/с; подача s = (1,1–4,47) м/мин; глубина резания t = (0,1–0,4) мм.
Были получены следующие результаты экспериментов. Влияние состава СОТС на температуру в зоне обработки при вариации режимов резания можно проследить по графикам, представленным на рис. 1. При шлифовании ситалла при максимальных, наиболее напряженных режимах обработки (t = 0,4 мм, s = 4,47 м/мин, v = 41 м/с) в среде СОТС №1 температура достигала θ = 240°С, при использовании СОТС №2 θ = 146°С, при использовании СОТС №3 θ = 88°С. Это свидетельствует о том, что наличие масла в составе жидкостей в указанном незначительном количестве, не влияя практически на их охлаждающую способность, тем не менее, приводит к практически трехкратному снижению температуры в зоне обработки (СОТС №3 в сравнении с СОТС №1). По нашему мнению, причина этого явления связана со степенью поверхностной активности среды по отношению к ОМ и, как следствие, с уровнем ее проникающей способности в зону резания. СОТС №3 (наличие в составе ПАВ при отсутствии масла), обладая такой способностью, оказывает, при прочих равных условиях, максимальное воздействие на снижение температуры при шлифовании ситалла практически при всех рассмотренных сочетаниях режимов резания.
Из всех параметров режима шлифования скорость резания в наибольшей степени влияет на температуру в зоне обработки (см. рис.1, в). В условиях осложненного резания, когда t больше величины выступания зерен из связки, с увеличением скорости резания все большее количество зерен в единицу времени не режет, а вместе со связкой скользит по обрабатываемой поверхности, при этом все большее количество тепла не успевает уноситься вместе с СОТС, а переходит в деталь. Наличие масляных включений в составе среды усугубляет это явление.
Диспергирующая способность СОТС позволяет жидкости проникать в малейшие трещинки обрабатываемого материала и одновременно с процессом разупрочнения ОМ уносить тепло из зоны резания. Как видно из представленных результатов, способность СОТС снижать температуру в зоне резания зависит от наличия и концентрации масляных включений. По-видимому, масло, снижая поверхностную активность среды, тормозит ее проникновение в микротрещины на поверхности ОМ, что отрицательно сказывается на температуре.
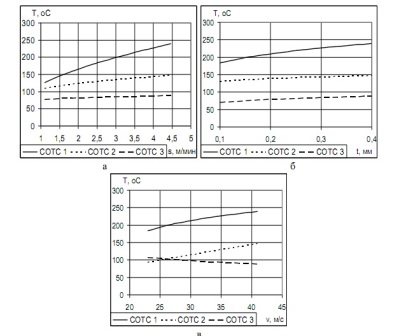
Рисунок 1 – Влияние составов применяемых СОТС на температуру в зоне обработки при вариации режимов обработки: а – v = 41 м/с, t = 0,4 мм; б – v = 41 м/с, s = 4,47 м/мин; в – s = 4,47 м/мин, t = 0,4 мм
При обработке хрупких неметаллических материалов, в частности, ситаллов, нормальная составляющая силы резания в 4–10 раз превышает тангенциальную составляющую, то есть Py ⁄ Pz = 4–10. Сила Py направлена в формируемую поверхность, и ее увеличение оказывает существенное отрицательное влияние на формирование и развитие вызванного обработкой дефектного слоя в изделии [2,7]) и, как следствие, снижает его эксплуатационные характеристики.
На рис. 2 представлены данные эксперимента по определению Py при шлифовании ситалла в условиях использования сред различной степени активности при вариации режимов обработки.
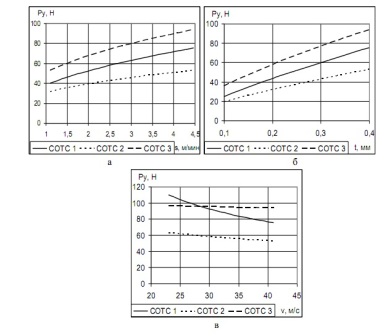
Рисунок 2 – Влияние составов применяемых СОТС на нормальную составляющую силы резания Py при вариации режимов обработки: а – v = 41 м/с, t = 0,4 мм; б – v = 41 м/с, s = 4,47 м/мин; в – s = 4,47 м/мин, t = 0,4 мм
Как следует из представленных графиков, максимальное влияние на уровень Py оказывают подача и глубина резания вне зависимости от состава применяемой СОТС. Сила Py возрастает с увеличением s и t. Увеличение скорости резания практически не сказывается на уровне Py при шлифовании ситалла с использованием сред, имеющих в своем составе одинаковое количество ПАВ и минимум масла – СОТС №2 или вообще не содержащих масла – СОТС №3. При использовании среды, имеющей в своем составе дополнительно к ПАВ большее количество масла (до 10%) – СОТС №1, увеличение скорости резания оказывает положительное влияние на изменение величины Py (см. рис.2, в).
Как было сказано выше, при глубинном шлифовании связка круга в полной мере участвует в формообразовании поверхности и наличие масляных включений в составе СОТС благоприятно сказывается на величине нормальной составляющей силы резания. При использовании СОТС №3 значения Py наиболее высоки и при максимальных режимах из диапазона варьирования составили 95 Н, что вызвано отсутствием масла в составе СОТС, снижающего трение связки по обрабатываемой поверхности.
В состав СОТС №2 кроме ПАВ, которые при обработке ситаллов повышают диспергирующие свойства сред, входит также и масло. Несмотря на то, что в этой среде уровень масла значительно ниже, чем в СОТС №1, при максимальных режимах резания из диапазона варьирования (s = 4,47 м/мин, t = 0,4 мм, v = 41 м/с) нормальная составляющая силы резания достигает лишь 50 Н против 75 Н, полученной при обработке с использованием СОТС №1. Это позволяет сделать вывод о благоприятном влиянии на силовые характеристики процесса шлифования СОТС, объединяющих в себе смазочные свойства масла, представленного в незначительном количестве (не более 1%), и диспергирующие действия ПАВ.
Влияние режимов обработки на тангенциальную составляющую силы резания, направленную в удаляемый припуск, однозначно вне зависимости от состава использованных технологических сред: Pz увеличивается с ростом s и t и снижается с увеличением скорости резания v. Об этом свидетельствуют графики, представленные на рис. 3. Тангенциальная составляющая изменяется эквивалентно изменению температуры при резании, что, согласно [8]), соответствует зависимости Θ = Pz⋅v.
При шлифовании образцов ситалла при максимальных параметрах режима наименьшее значение тангенциальной составляющей силы резания соответствовало обработке с СОТС №3, и составило 6 Н. При обработке с СОТС №2 – 8 Н, и 13 Н при обработке с СОТС №1. Отсюда можно заключить, что тангенциальная составляющая силы резания Pz, в отличие от радиальной силы Py, в наибольшей степени определяется диспергирующими свойствами применяемой СОТС. Физически это можно обосновать следующим образом. Учитывая, что в процессе эксперимента реализовывалась схема плоского встречного шлифования, то в этом случае влияние трения на процесс диспергирования материала припуска минимально. Поэтому среды, имеющие в своем составе масло (СОТС №1 и СОТС №2) в меньшей степени способствуют снижению величины , чем наиболее поверхностно – активная среда СОТС №3.
Выводы
Исходя из полученных данных, можно заключить, что эффективность технологических сред различных составов определяется условиями обработки ХНМ. На разных стадиях обработки «полезными» могут быть различные составляющие СОТС.
Масляные включения в технологических средах благоприятно сказываются на величине радиальных составляющих сил резания, что позволяет снизить остаточную дефектность обработанной поверхности. Однако наличие масла ухудшает охлаждаемость обрабатываемой поверхности технологической средой, что способствует повышению температуры в зоне обработки, что так же может негативно влияеть на качество обработанной поверхности. Диспергирующие свойства СОТС за счет разупрочнения поверхностного слоя обрабатываемого материала облегчают условия резания и благо- приятно сказываются как на уровне сил так и на температуре в зоне обработки.
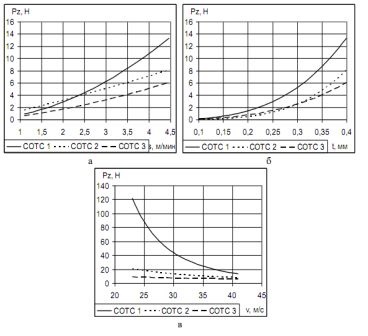
Рисунок 3 – Влияние составов применяемых СОТС на тангенциальную составляющую силы резания при вариации режимов обработки: а – v = 41 м/с, t = 0,4 мм; б – v = 41 м/с, s = 4,47 м/мин; в – s = 4,47 м/мин, t = 0,4 мм
Среды, обладающие повышенной диспергирующей способностью, целесообразно применять на операциях чернового и получистового шлифования ситаллов. Здесь важно обеспечить высокую производительность обработки в сочетании с благоприятной структурой дефектного поверхностного слоя (развитой трещиноватости в поверхностном слое в сочетании с мелкодефектной структурой более глубоких слоев). Этого можно добиться за счет возможности интенсификации съема ослабленного активной средой поверхностного слоя обрабатываемой детали при минимальном силовом воздействии на нее.
На чистовых операциях обработки ХНМ можно рекомендовать к использованию поверхностно-активные СОТС с минимальными добавками масел, обеспечивающих снижение радиальной составляющей силы резания, отрицательно влияющей на развитие дефектности формируемой поверхности, за счет уменьшения трения связки по поверхности детали при большей смазочной способности среды.
Знание механизмов влияния структурных составляющих сложной системы СОТС на процесс резания позволяет им управлять, обеспечивая за счет проектирования рационального технологического процесса обработки, требуемое качество детали при минимальной технологической себестоимости.
Список литературы
- Калафатова Л. П. Технологические среды как способ интенсификации процессов механической обработки стекломатериалов // Прогрессивные технологии и системы машиностроения: Междунар. сб. научн. трудов. – Донецк: ДонГТУ. – 1996. – Вып. 3. – С. 25–37.
- Калафатова Л. П. Влияние технологической наслед-ственности на эффективность процессов механической обработки стекломатериалов // Справочник. Инженерный журнал. – М.: Машиностроение. – 1997. – № 9. – С. 7–11.
- Исследование процессов финишной алмазной обработки корундовых керамических материалов / Г. А. Смирнов, В. П. Бахарев, М. О. Куликов, Т. П. Антюфеева // Вестник машиностроения. – 2001. – №9. С. 56–60.
- Калафатова Л. П. Особливості механічної обробки виробів із крихких неметалевих матеріалів // Процеси механічної обробки в машинобудуванні. Зб. наук. праць. – Житомир: ЖДТУ, 2007. – Вип. 5: В 2–х ч. – Ч. 1. – С. 72–87.
- Круглицкий Н. Н. Основы физико-химической механики. – К.: Вища школа. – 1975. – 268 с.
- Технологические свойства новых СОЖ для обработки резанием/ Под ред. М. И. Клушина. – М.: Машиностроение. – 1979. – 192 с.
- Калафатова Л. П. Технологические основы повышения эффективности обработки и обеспечения качества изделий из технических стекол и ситаллов: Диc. докт. техн. наук:05.02.08. – Донецк, 2002. – 356 c.
- Хрульков В. А., Головань А. Я., Федотов А. И. Алмазные инструменты в прецизионном машиностроении. – М: Машиностроение, 1977. – 223 с.