Повышение эффективности деятельности предприятия
Авторы:Самойлов П. И.
Источник:http://www.sworld.com.ua/
Экономическая эффективность работы предприятия является одним из важнейших показателей, которые подтверждают работоспособность предприятия.
В соответствии с международным стандартом ISO 9000:2008 под эффективностью (efficiency) понимается связь между достигнутым результатом и использованными ресурсами. Отдельно рассматривается категория результативность, определяемая, как: ... степень реализации запланированной деятельности и достижения запланированных результатов
.
Интерес к экономической эффективности работы предприятия возникает по нескольким причинам: при выделении кредитов необходимо обладать данными об экономической эффективности предприятия и динамике ее изменения, при обороте ценных бумаг предприятия (для акций–вопрос об их стоимости, для облигаций и векселей–вопрос надежности и гарантий погашения).
Повышение эффективности деятельности предприятия можно добиться современными методами менеджмента. Достаточно повысить удовлетворенность потребителя, следовательно, повысится и спрос на выпускаемую продукцию, а как итог увеличится рентабельность производства. Удовлетворение потребителя в первую очередь происходит за счет качества продукции. Достичь его можно и с минимальными затратами, за счет применения современных методов повышения эффективности, таких как: Total productive maintenance (Всеобщее обслуживание оборудования
), реинжениринг бизнес процессов, 5S (Упорядочение
), Шесть сигм
и др.
Можно отметить, что среди исследователей нет однозначного ответа на вопрос о том, как определить экономическую эффективность деятельности предприятия. Конечно, было бы желательно, чтобы экономическую эффективность функционирования предприятия можно было определить с помощью единого показателя. Это позволит производить сравнения между деятельностью различных предприятий.
Для анализа факторов, влияющих на результат работы производственного предприятия, воспользуемся причинно–следственной диаграммой Исикавы (рис. 1).
Метод Исикавы с построением соответствующей диаграммы является сугубо инженерным, использующимся в Японии для управления качеством продукции при низких затратах и высокой производительности труда. Указанный метод позволяет уяснить связь контролируемых параметров (качество, стоимость, производительность) с неограниченным количеством причинных факторов, а, следовательно, обеспечивает возможность управлять этими параметрами.
Исходя из рис.1 эффективность работы производственного предприятия зависит от эффективности использования 5-ти основных факторов (5М): оборудования (machine), персонала (man), методов (methods), материалов (materials), среды (medium).
Где
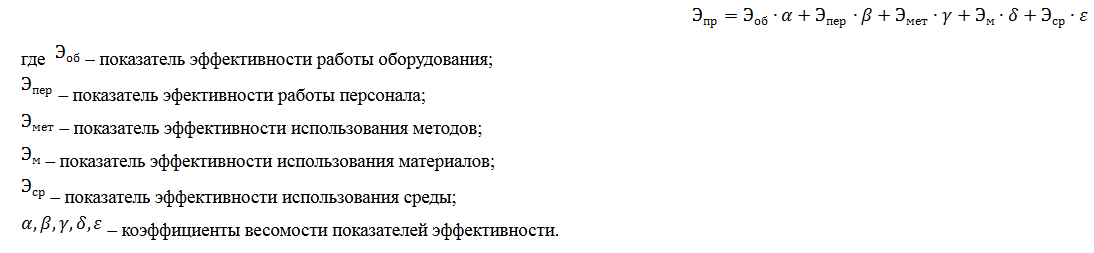
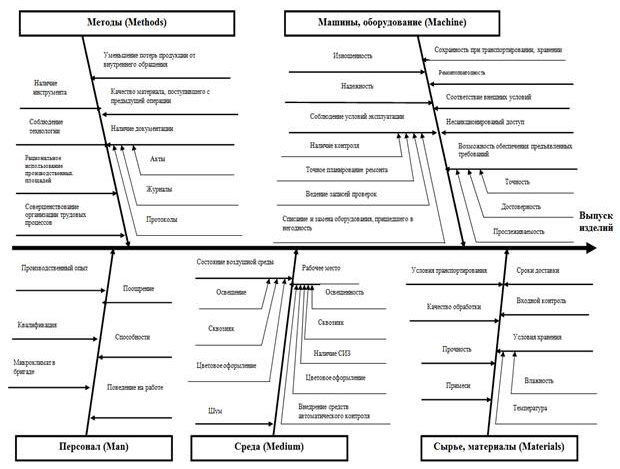
Рисунок 1–Причинно–следственная диаграмма Исикавы для производственного предприятия
Особое внимание в момент непроходящего украинского кризиса заслуживают орудия труда, так как большинство из них отработали свой срок службы и подошли к черте, когда каждый день работы оборудования может стать последним. Значительный процент работающего сейчас оборудования выпущен еще в 70х–90х годах XX столетия. Конечно, имеется возможность приобретения нового оборудования, нодля этого необходимы значительные, а также возможно повреждение оборудования вследствие обслуживания его по старым системам и методам. При этом большинство собственников хотят получать наибольшие доходы с минимальными затратами.
Одним из методов оптимальной организации управления жизненным циклом работы оборудования является система Total productive maintenance (TPM). Система TPM родилась в 60-е годы в Японии. Этот термин можно перевести как обслуживание оборудования, позволяющее обеспечить его наивысшую эффективность на протяжении жизненного цикла с участием всего персонала. На рубеже 40-х – 50-х годов прошлого столетия в японских компаниях широко применялась американская система профилактики оборудования, подразумевавшая четкое разделение труда между операторами, использующими оборудование, и специалистами, осуществляющими его техническое обслуживание.
ТРМ получила распространение в отраслях, где состояние оборудования оказывает решающее влияние на уровень производительности, качества, травматизма, загрязнения окружающей среды. Сегодня среди тех, кто уже внедрил или внедряет ТРМ, помимо японских компаний, есть и американские, немецкие, и многие другие компании Европы, Южной Америки и Азии, а также Китая. Это Истмен Кодак
, Форд
, Проктэр энд Гэмбл
; несколько заводов Пирелли
, группа Дюпон
и др. Что касается стран СНГ, здесь система ТРМ еще не получила массового признания, хотя уже начинает внедряться на некоторых предприятиях. TPM–система общего технического обслуживания оборудования. Система TPM позволяет обеспечить наивысшую эффективность работы оборудования. Задачей TPM является сведение к минимуму непредусмотренного и экстренного обслуживания оборудования, исключение или значительное уменьшение вероятности срыва работ вследствие незапланированного простоя оборудования. Как и все новые технологии, система TPM базируется на использовании человеческого фактора. Именно от персонала, его заинтересованности и мотивации будет зависеть эффективность внедрения.
ТРМ–система постоянного действия, предназначенная для измерения качества работы и принятия мер по совершенствованию процессов. Она направлена на обеспечение непрерывного улучшения качества продукции, состояния оборудования и развитие персонала. Основной акцент в развертывании проекта следует делать на усиление вовлеченности персонала, работу в команде и повышение ответственности. Анализ существующих производственных процессов позволяет выявить 6 групп факторов, влияющих на работоспособность оборудования (рис. 2). Совокупность этих групп и составляет зону максимального риска выхода оборудования из строя. Как показывает статистика работы предприятий Донецкой области (рис. 3), 67% простоев оборудования в цехах происходили по вине обслуживающего персонала. Это происходило вследствие нарушения персоналом своих должностных обязанностей и технологических инструкций. Простои, связанные с износом основного и вспомогательного оборудования, встречались в 25% случаев. 5% простоев оборудования связано с невозможностью определения скрытых дефектов оборудования, а оставшиеся 3% происходили из-за факторов, которые нельзя спрогнозировать.
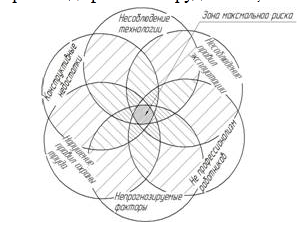
Рисунок 2–Сочетание факторов выхода оборудования из строя
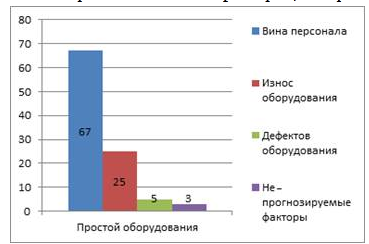
Рисунок 3–Вероятностное распределение количества простоев
Большее количество простоев оборудования вызвано человеческим фактором. Человеческий фактор включает в себя следующие группы причин выхода из строя оборудования: непрофессионализм работников, нарушение правил охраны труда, несоблюдение правил эксплуатации, несоблюдение технологий. Т.е. в главную очередь, как и любая современная технология, TPM сталкивается с барьером в виде собственного персонала.
Выводы: Определение экономической эффективности функционирования предприятия является важной задачей как для отдельных субъектов хозяйственной деятельности, так и для экономики. Согласно предложенному методу полная эффективность находится как комплексный критерий состояющий из пяти основных факторов: методов, среды, материалов, персонала, оборудования. Следовательно, достичь повышения полной эффективности можно увеличением эффективности использования одного из представленных факторов. Одним из способов повышения эффективности деятельности предприятия является система TPM, которая позволяет добиться увеличения производительности, уменьшения поломок и аварий, уменьшения числа брака, снижения себестоимости, отсутствия производственного травматизма, увеличения рационализаторских предложений.