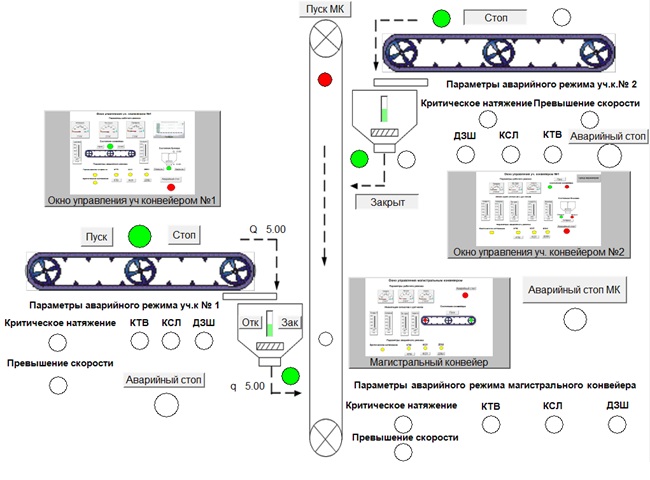
Рисунок 1 – Общий вид мнемосхемы системы диагностики на АРМ диспетчера
Автор: Горячев Н. В., Ткаченко А. Е.
Источник: Автоматизация технологических объектов и процессов. Поиск молодых ХIХ Международная научно–техническая конференция аспирантов и студентов (в рамках 5-го Международного научного форума Инновационные перспективы Донбасса
) 21–23 мая 2019 года.
Ленточные конвейеры способны осуществлять непрерывное транспортирование грузов на большие расстояния, что по технологическим причинам обуславливает их незаменимость на шахтах и рудниках. Именно поэтому, особое значение приобретает вопросы надежной и безопасной эксплуатации конвейерных линий.
Контролировать технологические параметры ленточных конвейеров необходимо как для обеспечения непрерывной и безаварийной работы конвейера, так и требуемой производительности конвейера, а также стабилизации натяжения ленты. Для решения данных задач необходимо осуществлять оперативный контроль и управление или, как это ещё называется – диагностику работы конвейерной линии. Диагностирование – процесс оперативного контроля состояния объекта в режиме реального времени или же анализ системы по результату её работы постфактум.
Система диагностики конвейерной лини должна обеспечивать непрерывный контроль технологических параметров рабочего и аварийного режимов.
Рабочий режим ленточного конвейера характеризуется такими параметрами, как скорость движения ленты [v], м/с, вес насыпаемого груза [G], кН/м, натяжение ленты [S], кН, производительность конвейерной линии либо производительность очистного забоя [Q ], т/час, уровень груза в бункере, массовый расход груза из бункера [q], т/час.
Для нормальной работы конвейерной установки должны выполняться следующие технологические требования: скорость движения ленты должна изменяться в диапазоне от минимально допустимого значения (25% от максимальной) и до максимально допустимого значения, устанавливаемого оператором; должен осуществляться оперативный контроль веса насыпаемого груза для последующей стабилизации нагрузки на ленту и регулирования натяжения; натяжение ленты конвейера не должно достигать минимально допустимого значения на провисание и не превышать максимально допустимое значение для предотвращения порыва ленты; должен контролироваться массовый расход груза из бункера для дальнейшего регулирования нагрузки на ленту и стабилизации натяжения.
При работе ленточной конвейерной линии возможны следующие аварийные ситуации:
Рассмотрим алгоритм работы разрабатываемой системы диагностики ленточной конвейерной линии.
На первом этапе система производит инициализацию линий связей, устанавливает уставки по скорости и натяжению, проводит предварительный опрос технологических датчиков, таких как, двухпозиционные датчики верхнего и нижнего уровня в погружном бункере, тахо-генераторные датчики скорости приводных двигателей, датчик натяжения, основные датчики аварийных ситуаций (КТВ, КСЛ, ДЗШ) для проверки их работоспособности.
На втором этапе начинается непрерывный технологический опрос всех датчиков, и система ждёт команды оператора на пуск конвейерной линии, далее система диагностики подаёт сигнал на блок управления конвейером в составе системы автоматизированного управления конвейерной линии САУКЛ, и будет запущен магистральный конвейер в направлении обратном грузопотоку, затем могут быть запущены участковые конвейеры.
В режиме реального времени система осуществляет непрерывный контроль параметров рабочего и аварийного режима конвейерной линии. Так же, при необходимости, может осуществляться стабилизация нагрузки на ленту конвейера и регулирование натяжения или скорости движения ленты, а именно, в режиме PID-регулирования система может управлять заслонками всех погрузочных бункеров и всеми приводными электродвигателями конвейерной линии, тем самым регулируя нагрузку на ленту, натяжение и скорость движения каждого ленточного конвейера линии.
В случае возникновения любой из описанных выше аварийных ситуаций, разрабатываемая система должна проинициализировать место аварии, если авария произошла на участковом конвейере, он будет остановлен, и данная участковая ветвь будет изолирована, однако, в случае возникновения аварии на магистральном конвейере, будет остановлена вся конвейерная линия. Далее система должна проинициализировать непосредственно аварийную ситуацию и выдать сообщение с информацией об аварии на пульт диспетчера, сопровождая всё соответствующим звуковым и световым сигналом. После устранения неполадки система снимает запрет на пуск конвейера и погрузочного бункера.
В конце рабочей смены значения основных параметров рабочего режима и записи об авариях архивируются, так же могут быть выданы рекомендации для ремонтной смены, например, осуществить ручное регулирование натяжения ленты 1-ого участкового конвейера перед началом следующей смены, проверить работу датчиков уровня в погрузочных бункерах, так как были зафиксированы недостоверные сведения.
Исходя из того, что задачей системы диагностики работы конвейерной линии является не только оперативный контроль, но и индикация, архивация параметров рабочего и аварийного режимов, актуальным техническим решением будет считаться создание Scada-системы, основанной на работе программируемого логического контроллера и мнемосхемы на АРМ диспетчера.
Вышеописанный алгоритм работы системы диагностики реализован на базе PLC 150 в среде программирования Codesys, а мнемосхема для АРМ диспетчера разработана в программе Master Scada. Общий вид мнемосхемы системы представлен на рисунке 1.
Рисунок 1 – Общий вид мнемосхемы системы диагностики на АРМ диспетчера
Таким образом, разработанная система диагностики на базе Scada-системы выполняет поставленные ей задачи оперативного контроля и регулирования основных параметров работы ленточной конвейерной линии, что существенно повышает безопасность и эффективность транспортирования грузов. При этом система диагностики, благодаря современной элементной базе может входить в состав АСУ ТП конвейерного транспорта.
1. Стадник, Н. И. Справочник по автоматизации шахтного конвейерного транспорта / Н. И. Стадник, В. Г. Ильюшенко, С. И. Егоров и др.– Киев: Техника, 1992. – 436 с.
2. Батицкий, И. А. Автоматизация производственных процессов и АСУ ТП в горной промышленности/ И. А. Батицкий, В. И. Куроедов, А. А. Рыжков. – Москва: Недра, 1991. – 303 с.
3. Пейсаховича, Г. Я. Подземный транспорт шахт и рудников/ Под общей ред. Г. Я. Пейсаховича, И. П. Ремизова. – М.: Недра, 1985. – 565 с.