Cтруктурные превращения в зоне термического влияния при восстановлении деталей наплавкой из закаливающихся сталей
Автор: М. Л. ВОЛОВОДЮК, Л. П. КРАВЧЕНКО
Источник: ISSN 1727-7337. АВИАЦИОННО-КОСМИЧЕСКАЯ ТЕХНИКА И 30 ТЕХНОЛОГИЯ, 2011, № 2
Общая постановка проблемы
В настоящее время одним из основных вопросов ремонтного производства является восстановление изношенных деталей. Наряду с узкой номенклатурой основных и массовых деталей на поточных линиях особое место отводится широкой номенклатуре изделий, восстановление которых целесообразно на большинстве авиаремонтных предприятий. При этом важным условием является их восстановление до уровня новых при относительно невысокой стоимости.
Одним из наиболее экономичных, надежных и широко применяемых методов восстановления изношенных деталей является наплавка. Восстановление деталей летательных аппаратов наплавкой позволяет изменить свойства наплавленного металла.
Однако широкое применение этого метода тормозится тем, что большинство деталей летательных аппаратов изготавливаются из сталей, которые под влиянием наплавочного термодеформационного цикла в зоне термического влияния (ЗТВ) закаливаются на мартенсит, что приводит к образованию недопустимого дефекта – холодных трещин.
1. Формулирование проблемы
Особонагруженными деталями летательных аппаратов являются шестерни редукторов.
Условия работы шестерен в редукторе зависят от многих факторов: скорости движения летательного аппарата, его нагрузки, смазки редуктора и т.д. В местах входа в зацепление зубья как бы бьют своими боковыми поверхностями друг по другу. Это и приводит к износу торцевых поверхностей зубьев шестерни за время ее эксплуатации.
Кроме того, шестерни испытывают статические нагрузки при работе, трение, действие крутящих моментов. Такие сложные условия работы шестерен приводят к небольшой длительности срока их службы.
Поэтому важной задачей является увеличение долговечности их работы, чего возможно достичь как повышением качества вновь изготавливаемой шестерни, так и ее ремонтом. В последнем случае изношенные объемы металла наносятся путем наплавки, а последующая механическая и термическая обработка позволяет получить изделие по качеству не уступающему вновь изготавливаемому.
Преимущественно из цементуемой стали 25ХГТ и нецементуемой 40Х. Для обеспечения их долговечности поверхность зуба должна иметь высокую твердость 50-60HRC, а глублежащий металл высокую прочность и вязкость. Поэтому для качественного восстановления изношенных зубьев наплавкой необходимо применение специальных наплавочных материалов, дающих химический состав металла наплавки, близкий к основному. Наиболее приемлемой для этих целей является наплавочная проволока Нп-30ХГСА. Кроме достаточного количества углерода и хрома она содержит около 1% Mn и 1% Si. Последние участвуют в раскислении металла наплавочной ванны, что обеспечивает высокое качество наплавленного металла. Наличие элементов раскислителей в проволоке Нп-30ХГСА позволяет применять ее как при наплавке под флюсом, так и при наплавке в защитных газах – СО2 и аргоне.
С использованием этой проволоки была разработана технология восстановления наплавкой шес- терен непостоянного зацепления. Технология предусматривает наплавку в среде СО2 изношенных торцов зубьев на специальной установке. Для предупреждения образования холодных трещин в зоне термического влияния перед наплавкой производится предварительный подогрев шестерни в печи. Температура подогрева шестерни из стали 25ХГТ составляет 200…250оС, а для шестерни из стали 40Х – 350…400оС. Промышленное опробование этой технологии показало хорошее качество наплавленного металла, удовлетворительную его обрабатываемость. Применение последующей термической обработки позволяет получить восстановленные шестерни по свойствам близким к вновь изготовленным.
Однако, для широкого внедрения восстановления шестерен наплавкой необходимо располагать сведениями о структурных и фазовых превращениях в зоне термического влияния сталей 25ХГТ и 40Х, что позволит правильно выбрать режимы наплавки, термической обработки деталей и обеспечить высокую стойкость зоны термического влияния против образования холодных трещин.
2. Решение проблемы
Для получения таких данных удобно пользоваться термокинетическими диаграммами превращения аустенита сталей, полученными в условиях воздействия термодеформационных циклов. Они позволяют прогнозировать структурное состояние металла зоны термического влияния при различных условиях наплавки и по структуре оценить свойства ЗТВ и склонность к образованию холодных трещин.
По методике исследовалась кинетика превращения аустенита сталей при воздействии термодеформационных циклов.
Жестко закрепленные образцы трубчатого сечения нагревались проходящим током до температуры 1250°С и затем охлаждались с различными скоростями. Нагрев осуществлялся со скоростью около 150°С/с, а регулирование охлаждения производилось продувкой через внутренне отверстие образцов аргона под различным давлением, охлаждением на воздухе, а также пропусканием на стадии охлаждения подогревающего тока.
В процессе нагрева и охлаждения с помощью осциллографа Н-700 регистрировалось изменение температуры образца, магнитной проницаемости средней его части и усилий, возникающих в образцах за счет стесненности его перемещения при тепловом расширении или сокращении. Путем обработки осциллограмм построены диаграммы термокинетического превращения.
Исследование кинетики превращения аустенита применительно к высоко-температурным участкам ЗТВ для стали 25ХГТ изучали при скоростях охлаждения от 4,2°С/с до 85°С/с. Подсчитывалась средняя скорость охлаждения в интервале 600…500оС. Диаграмма термокинетического превращения аустенита стали 25ХГТ приведена на рис. 1.
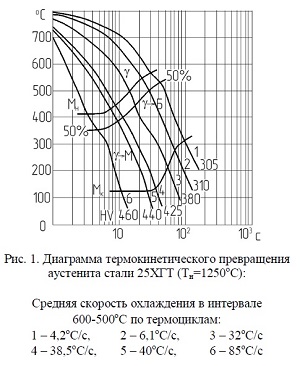
Она характеризуется достаточной устойчивостью переохлажденного аустенита. При охлаждении в исследуемом диапазоне скоростей перлитное превращение отсутствует.
Охлаждение по темоциклам 1 и 2 (рис.1) со скоростями 4,2 и 6,1оС/с приводит только к бейнитному превращению. При этом образуется смешанная структура верхнего и нижнего бейнита. Твердость образцов после такого охлаждения составляет 305…310HV.
При охлаждении по термоциклу 3 со скоростью 32°С/с аустенит претерпевает бейнитно-мартенситное превращение, а твердость образца повышается до 385HV.
При охлаждении по термоциклу 3 со скоростью 32°С/с аустенит претерпевает бейнитно-мартенситное превращение, а твердость образца повышается до 385HV. Последующее увеличение скорости охлаждения до 40°С/с и выше приводит к полному превращению аустенита в мартенсит (термоциклы 5 и 6). Температура начала мартенситного превращения Мн равна 410°С, а заканчивается оно при Мк=125°С. Твердость мартенсита составляет 440…460HV.
Исследование кинетики превращения аустенита стали 40Х после высокотемпературного нагрева изучалось при скоростях охлаждения от 1,2°С/с до 300°С/с. Диаграмма термокинетического превращения приведена на рис. 2.
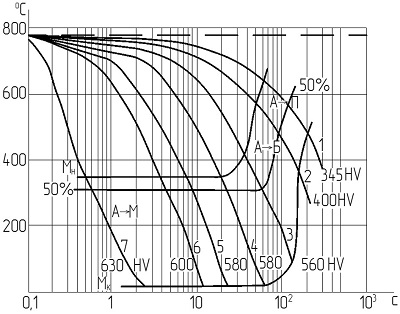
а)
При медленном охлаждении со скоростью 1,2°С/с (термоцикл 1) фазовое превращение аустенита происходит в температурном интервале 670…490°С.
В этом случае происходит диффузионный распад переохлажденного аустенита на ферритноцементитную смесь преимущественно по перлитному механизму.
При охлаждении со скоростью 23°С/с (термоцикл 2) происходит преимущественно бейнитное превращение аустенита в области температур 580…380°С. Увеличение скорости охлаждения приводит к превращению аустенита в мартенсит (термоциклы 3-7). После охлаждения в исследуемом интервале скоростей твердость стали 40Х изменяется от 345HV до 630HV.
Диаграммы термокинетического превращения сталей 25ХГТ и 40Х, полученные в условиях имитации наплавки, позволяют определить оптимальные параметры наплавки, используя теорию распространения тепла.
Использование кратковременного нагрева при закалке токами высокой частоты незначительно влияет на строение нитроцементованного слоя зубьев основного металла шестерни стали 25ХГТ и позволяет исключить применение дорогостоящей химико-термической обработки. Для шестерен из стали 40Х из-за высокой температуры предварительного подогрева 350…400оС твердость металла на поверхности шлицевых отверстий может снижаться до 400HV. Ее можно повысить, применяя дополнительную закалку с нагревом токами высокой частоты до 900°С и последующим низким отпуском.
Выводы
Разработанный технологический процесс позволяет производить многократное восстановление изношенных шестерен редукторов и является экономически целесообразным с точки зрения ресурсосберегающей технологии.
Список использованной литературы
- Лебедев Ю.М. Установка для исследования
структурных превращений в условиях жестко закрепленного образца / Ю.М. Лебедев, Л.П. Кравченко // Труды НКИ. – Николаев: НКИ, 1973. – Вып. 66. – С. 12-16.
- Кравченко Л.П. Исследование структурных превращений в условиях сварки титанового сплава ВТЗ-1 / Л.П. Кравченко, Ю.М. Лебедев // Тез.док. II Всесоюз. конф. по сварке цветных металлов. – Ташкент: Госиздат, 1982. – С. 28-32.
- Воловодюк М.Л. Побудова аналітичної моделі термоциклування з фазовими перетвореннями в вуглецевих сталях / М.Л. Воловодюк // Техногенна безпека: Наукові праці. – Миколаїв: Вид-во ЧДУ ім. Петра Могили. – 2010. – Т. 137, вип. 124. – С. 16-22.
- Шершоров М.Х. Фазовые превращения и изменения свойств стали при сварке / М.Х. Шершоров, В.В. Белов. – М.: Наука, 1972. – 219 с.
Грабин В.Ф. Металловедение сварки наплавлением / В.Ф. Грабин. – К.: Наук. думка, 1982. – 416 с. http://www.irbis-nbuv.gov.ua/cgi-bin/irbis_nbuv/cgiirbis_64.exe?Z21ID=&I21DBN=UJRN&P21DBN=UJRN&S21STN=1&S21REF=10&S21FMT=JUU_all&C21COM=S&S21CNR=20&S21P01=0&S21P02=0&S21P03=IJ=&S21COLORTERMS=1&S21STR=%D0%9624839