Реферат за темою випускної роботи
Зміст
- Вступ
- 1. Актуальність теми
- 2. Мета і задачі дослідження та заплановані результати
- 3.Аналіз високопродуктивних способів шліфування зразків, які складаються з різних матеріалів.
- 3.1 Огляд конструкцій виробів, які складаються із матеріалів з різними фізико-механічними властивостями.
- 3.2 Сучасні способи шліфування (заточка) комбінованих зразків. Інструмент, що використовується.
- 3.3 Аналіз сучасних конструкцій пристроїв для плоского шліфування за пружною схемою.
- 3.4 Аналіз способів пошуку режимів оброблення.
- Висновки
- Перелік посилань
Вступ
Сучасне виробництво характеризується використанням матеріалів з високою твердістю та зносостійкістю. Внаслідок цього їх оброблення різанням викликає певні труднощі. Для фінішної обробки таких матеріалів, як правило, використовують шліфування кругами із надтвердих матеріалів (НТМ), до яких відносяться алмаз та ельбор. При цьому круги використовуються на металевій зв’язці, що потребує використання електроерозійної правки та електроерозійних дій на робочу поверхню круга (РПК).
На кафедрі «Мехатронні системи машинобудівного обладнання» ДонНТУ запропонований новий метод пошуку оптимальних режимів оброблення за допомогою такого показника, як миттєва поточна лімітована різальна здатність круга, математичний опис якої може бути знайдений за допомогою пружної схеми шліфування. Метод широко використовується при пошуку режимів плоского шліфування ванадійових інструментальних сталей, твердих сплавів, заточці інструментів, потребує значно менших витрат часу порівняно з класичним методом знаходження оптимальних режимів шліфування, але потребує модернізації верстату з метою реалізації шліфування за пружною схемою.
1. Актуальність теми
Використання з метою формування параметрів РПК електричної ерозії, електро-фізикохімічних дій і механічної дії на зв’язку вільним абразивом поклали початок розробці оперативних способів підвищення різальної здатності шліфувальних кругів.
Під час шліфування зразків, які складаються із матеріалів з різними фізико – механічними властивостями оптимізація режимів оброблення виконується шляхом аналітично – експериментального методу або експериментально. Недоліком цих методів є висока трудомісткість пошуку, а також обмежена область використання рекомендацій, які знайдені експериментально. Цих недоліків можливо позбутися якщо пошук режимів оброблення виконувати з використанням поточної лімітованої різальної здатності круга (ПЛРЗК), яка описується кількістю зішліфованого матеріалу за одиницю часу при шліфуванні за пружною схемою з постійним підтиском зразка до РПК.
2. Мета і задачі дослідження та заплановані результати
Метою дослідження є є визначення оптимальних режимів різання при плоскому шліфуванні комбінованих зразків. Пошук режимів оброблення виконувати з використанням поточної лімітованої різальної здатності круга (ПЛРЗК).
Для пошуку закономірностей зміни ПЛРЗК необхідно вирішити наступні завдання:
- Розробити конструкцію пристрою для плоского шліфування за пружною схемою.
- Знайти значення технологічних обмежень, які накладені на режим різання верстатом, шліфувальним кругом та виробом.
- Дослідити вплив часу оброблення на зміну ПЛРЗК при шліфуванні за пружною схемою.
- Розробити рекомендації з режимів оброблення, які забезпечують повне використання різальної здатності круга.
Об'єкт дослідження: алмазний круг.
Предмет дослідження: режими оброблення з використанням ПЛРЗК, значення технологічних обмежень.
3. Аналіз високопродуктивних способів шліфування зразків, які складаються з різних матеріалів.
3.1 Огляд конструкцій виробів, які складаються із матеріалів з різними фізико-механічними властивостями.
До виробів, які складаються із матеріалів з різними фізико-механічними властивостями відносяться: токарні різці, фрези, зенкери, розвертки. Для виконання алмазного заточування перерахованих інструментів в їх конструкцію введена ціла низка змін геометричних параметрів і конструктивних елементів, які наведені на цих рисунках. Для виключення можливості шліфування алмазними кругами стальної державки у різців твердосплавна пластина виступає над поверхнями державки [1] . На передній поверхні виконано завищення пластинки твердого сплаву над державкою (див. рис 1.1а та 1.1б). Величина завищення дорівнює a= 0,10 – 0,15 мм. Також був створений вільний простір за гніздом під пластину твердого сплаву (див. рис 1.1в). Також змінений кут нахилу гнізда під пластинку твердого сплаву( див. рис. 1.1г). По головній і допоміжної задній поверхні виконано завищення (нависання) задніх поверхонь пластинки твердого сплаву над державкою на величину а. Проведена підточка задніх поверхонь державки на глибину t = 2 – 5 мм (див. рис1.1 б). Робочу частину інструменту конструюють таким чином, щоб державка і твердосплавна пластина заточувались по трьом різним за величиною задніми кутами. По допоміжній задній поверхні передбачають два різних за розміром кута. При конструюванні різців залежно від конкретних умов можливі різні комбінації зазначених змін конструктивних елементів і геометричних параметрів різців [1] .
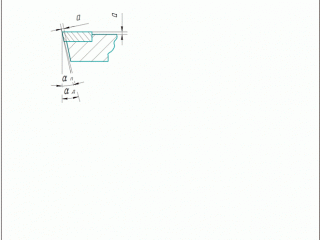
Рисунок 1 – Конструктивні елементи та геометричні параметри твердосплавних різців, що оброблюються алмазними кругами.
Окрім різального інструменту з матеріалів із різними фізико – механічними властивостями виготовляються ножі для різання паперу. В якості робочої частини використовуються леговані сталі, тверді сплави. В якості матеріалу конструктивної частини використовують залізо [2] . Як видно із наведених прикладів використання алмазного заточування потребує змін конструктивних параметрів, чого можливо позбутися при виконанні заточування алмазними кругами з електро–фізико–хімічними діями на робочу поверхню круга.
3.2 Сучасні способи шліфування (заточка) комбінованих зразків. Інструмент, що використовується.
Використання різальних властивостей алмазів при шліфуванні кругом значною мірою залежить від виду зв’язки, на якій виготовлений алмазовмісний шар. Так, за даними Т.Н.Лоладзе і Т.В.Бокучави, при шліфуванні алмазними кругами на бакелітовій зв’язці АС 40-Б1-100 зразків із молібдену МВ1 використовується тільки 9% різальних властивостей алмаза, жароміцного сплаву ХН7ОВМТЮ – 6%, титанового сплаву ВТ-1 – 3%, сталі 40 – 2%, сірого чавуна СЧ 18-28 – 0,07% [3]. Для ефективного використання різальних властивостей алмазу в інструменті він повинний бути надійно закріплений у матриці алмазовмісного шару. Властивість міцного утримання зерен у матриці алмазовмісного шару мають металеві зв’язки, [9] що являють собою композиції на основі міді, олова, заліза, алюмінію, нікелю та інших металів. Однак, підвищення міцності закріплення зерен за допомогою металевих зв’язок призвело до втрати кругами властивості самозаточування, у результаті чого різальна здатність РПК із збільшенням часу обробки постійно знижується. Зниження різальної здатності РПК збільшує потужність різання і сприяє підвищенню температури в зоні шліфування, величина якої може перевищити поріг фазово-структурних перетворень у поверхневому шарі деталі. Підвищити різальну здатність РПК можна введенням до складу металевих зв’язок твердих неметалевих наповнювачів: абразивних порошків, антифрикційних добавок, твердих мастил. Тверді мастила типу графіту або дисульфіду молібдену крім перерахованих вище ефектів забезпечують зниження сил тертя на поверхні зв’язки [5] . Менше схильні до засалювання і забезпечують зниження температури в зоні різання при шліфуванні твердих сплавів круги на зв’язках МО13, МО4, МВ1, ТМ2, які мають властивість самозагострення. Однак, перераховані прийоми не усувають проблеми зниження працездатності кругів при шліфуванні широкої номенклатури виробів із різних матеріалів. Використання з метою формування параметрів РПК електричної ерозії, електро-фізикохімічних дій і механічної дії на зв’язку вільним абразивом поклали початок розробці оперативних способів підвищення різальної здатності шліфувальних кругів. Оскільки при здійсненні дій на РПК одночасно з обробкою виробів інтенсивність цих дій узгоджується із задачами стабілізації вихідних показників обробки і зберігання певних параметрів РПК постійними, то такі дії на РПК можуть бути внесені до керуючих, а процес підтримки різальної здатності круга – до керування різальною здатністю круга в процесі обробки [6] . Виникнення керування різальною здатністю кругів на металевій зв’язці пов’язане з розробкою в Харківському державному політехнічному університеті колективом учених під керівництвом М.К. Беззубенко та А.І. Грабченко алмазно-іскрового шліфування (АІШ) та способу заточування різальних інструментів із синтетичних надтвердих матеріалів. Сутність АІШ полягає в поєднанні процесу різання алмазними зернами оброблюваної деталі з одночасним електрофізичною дією на інструмент і деталь за рахунок введення в зону різання імпульсивного технологічного струму в середовищі звичайних шліфувальних мастильно-охолоджувальних рідин (МОР). При обробці надтвердих неструмопровідних полікристалів у процесі їх шліфування здійснюється безперервна електро-фізикохімічна дія на зв’язку круга в автономній зоні з метою її електролітичного розчинення і електроерозійної руйнації, що забезпечує постійну величину виступання зерен із зв’язки. Процес дій на робочу поверхню круга в автономній зоні був поширений на обробку струмопровідних виробів, а потім був запропонований спосіб шліфування з подачею технологічної енергії одночасно в зону обробки та в автономну зону.
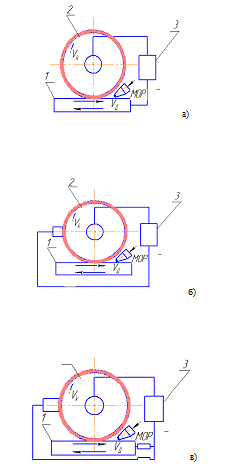
Рисунок 2 – Способи шліфування з керуванням різальною здатністю круга за допомогою електроерозійних дій.
3.3 Аналіз сучасних конструкцій пристроїв для плоского шліфування за пружною схемою.
Пристрій для плоского шліфування за пружною схемою розташовується на магнітній плиті верстата 3Г71 [7] . Оброблюваний зразок 2 закріпляли в струбцині 3, розміщеній на повзуні 4, яка має можливість переміщатися в корпусі 5 по роликовим напрямним 6. Для виключення можливості намагнічування рухомих частин пристрою в нижній частині корпусу встановлена мідна прокладка 7. Повзун спирається на підшипник 8, який закріплений на малому плечі важеля 9 на більшому плечі важеля встановлені вантажі 10 для врівноваження рухомої частини пристрою та вантажі 11, які забезпечують необхідну силу притискання зразка до робочої поверхні круга. Для того, щоб відвести зразок від поверхні шліфувального круга при виході його з зони різання служать копіри 12, з якими в цей момент починає контактувати підшипник 13. Це забезпечується за рахунок того, що корпус пристрою закріплений на магнітній плиті верстата, а копір за допомогою планки 14, стійок 15 та планки 16 на хрестовому супорті 17. При поздовжньому переміщенні столу підшипник 13 набігає на похилу поверхню копіра і опускає підшипник 8, який притискає повзун до поверхні шліфувального круга. Як наслідок, оброблюваний зразок від РПК опускається вниз. Положення копірів можна регулювати як в горизонтальній площині шляхом їх переміщення вздовж планки 14, так і в вертикальній, опускаючи чи піднімаючи планку 14 за допомогою гайок 18 [10] . Внаслідок зі шліфування зразка по висоті положення підшипника 13 відносно поверхні копірів змінюється, що призводить до зміни моменту врізання шліфувального круга в зразок. Щоб виключити вплив відносного положення вантажів 11 на силу притискання зразка до РПК, на стійці 15 встановлений кронштейн 19, а на важелі 9 – лінійка 20. В процесі оброблення постійне відносне положення лінійки і кронштейна підтримується з допомогою механізму вертикальної подачі шліфувального круга. Для підвищення точності виміру зішліфованого матеріалу на струбцині 3 встановлений штифт 21, який служить базою при вимірюванні зразка до та після шліфування. Вимірювання зразка відбувається в фіксованому нижньому положенні повзуна. Для захисту роликових напрямних від попадання мастильно-охолоджуючої рідини корпус пристрою закритий плівкою, яка не пропускає воду [8] .
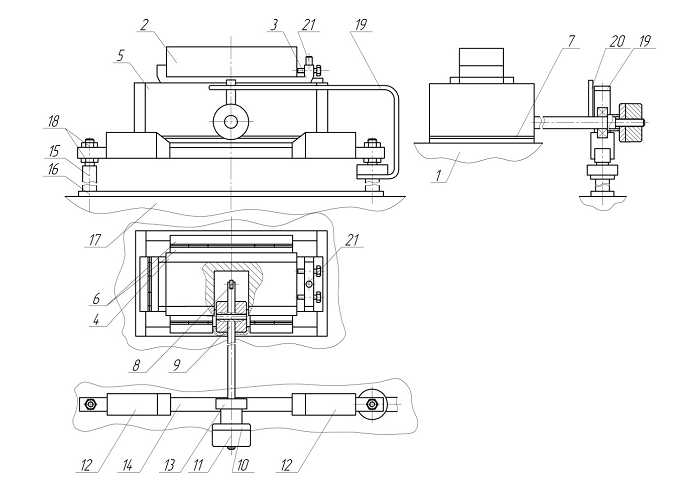
Рисунок 3 – Пристрій для плоского шліфування за пружною схемою.
3.4 Аналіз способів пошуку режимів оброблення.
Вихідними даними для визначення режиму різання при шліфуванні є: а) відомості про матеріал, який оброблюється та розміри оброблюваної поверхні; б) припуск на обробку; в) вимоги до точності, шорсткості оброблених поверхонь і іншими показниками якості; г) відомості про верстат; д ) жорсткість системи верстат-деталь-пристосування-круг і е) характеристика круга, яким проводять обробку на даній операції.
Режими різання при шліфуванні можуть бути визначені розрахунковим шляхом або призначені на основі практичних рекомендацій. Розрахунок режиму шліфування доцільно проводити для умов масового виробництва, коли незначні відхилення від оптимальних умов обробки можуть призвести до суттєвих втрат. Розрахунок режимів доцільно також проводити при розробці різних нормативів і рекомендацій, що відносяться до використання шліфувальних інструментів [4] . Задача визначення оптимального режиму шліфування виконується в три етапи : 1) складання системи рівнянь, що описують технічні обмеження, що накладаються на режим різання вимогами до деталі, верстатом, інструментом і умовами виробництва; 2) математичний опис цільової функції, тобто функції, яка виражає мету оптимізації; 3) спільний розгляд технічних обмежень і цільової функції і визначення на цій основі оптимального режиму шліфування.
Висновки
Зниження різальної здатності робочої поверхні відбувається, в основному, через відсутність пор на поверхні металевої зв’язки, у зв’язку з чим згодом стає неможливим розміщення стружки в міжзеренному просторі, об’єм якого, сформований під час правки, зменшується в процесі шліфування в результаті зносу зерен, а також схильністю металевої зв’язки до схоплювання з оброблюваними металами і сплавами. Зниження різальної здатності РПК збільшує потужність різання і сприяє підвищенню температури в зоні шліфування, величина якої може перевищити поріг фазово-структурних перетворень у поверхневому шарі деталі. Підвищити різальну здатність РПК можна введенням до складу металевих зв’язок твердих неметалевих наповнювачів: абразивних порошків, антифрикційних добавок, твердих мастил. Використання з метою формування параметрів РПК електричної ерозії, електро-фізикохімічних дій і механічної дії на зв’язку вільним абразивом поклали початок розробці оперативних способів підвищення різальної здатності шліфувальних кругів
При написанні даного реферату магістерська робота ще не завершена. Остаточне завершення: грудень 2014 року. Повний текст роботи та матеріали по темі можуть бути отримані у автора або його керівника після вказаної дати.
Перелік посилань
- Справочник по алмазной обработке металлорежущего инструмента./ Бакуль В.Н., Захаренко И.П., Кункин Я.А., Мильштейн М.З. Под общей редакцией Бакуль В.Н. – Киев: Техніка, 1971. – 208с
- Типы бумагорезальных ножей. Рекомендации по заточке. Сохранность и уход. Описание классов ножей. [Электронный ресурс].: // Типы бумагорезальных ножей. – Режим доступа (http://www.drukar.org/article10529.html.). – Дата доступа: март 2013г. – Название с экрана.
- Матюха П.Г. Високопродуктивне шліфування ванадієвих штампових та інструментальних сталей / Матюха П.Г. – Донецьк: ДВНЗ «ДонНТУ», 2008. – 222с.
- Абразивная и алмазная обработка материалов. Справочник.; под ред. д-ра техн. наук проф. А. Н. Резникова. – М.: Машиностроение, 1977. – 391 с.
- Узунян М.Д. Алмазно – искровое шлифование твердых сплавов / Узунян М.Д. – Харьков: НТУ «ХПУ», 2003. – 359с.
- Справочник метал листа: в 5 т. / перераб. под ред. С.А. Чернавского и В.Ф. Рещикова. – М. : «Машиностроение», 1976 Т.1. Изд. 3-е – 1976. – 768 с.
- Матюха П.Г. Полтавець В.В. Алмазне шліфування з електроерозійними керуючими діями на робочу поверхню круга. – Донецьк: ДонНТУ, 2006 – 164 с.
- Металлорежущие станки: Учебник для машиностроительных втузов/ Под ред. В.Э. Пуша. – М.: Машиностроение, 1985. – 256 с.
- Матюха П.Г., Габитов В.В. Влияние вида шлифования на шероховатость обработанной поверхности. // Наукові праці Донецького національного технічного університету. Серія: Машинобудування і машинознавство. Випуск 8 (190). – Донецьк: ДВНЗ „ДонНТУ”, 2011. – 214 с.
- Универсальный плоскошлифовальный станок высокой точности с горизонтальным шпинделем и прямоугольным столом. Модель 3Г71. Руководство к станку.