УДК 622.693-52
АВТОМАТИЗИРОВАННЫЙ КОМПЛЕКС ПОГРУЗКИ УГЛЯ В ЖЕЛЕЗНОДОРОЖНЫЕ ВАГОНЫ
Синегуб П.С., студент; Гавриленко Б.В., доцент, к.т.н.
Донецкий национальный технический университет
Автоматизация технологических объектов и процессов. Поиск молодых Сборник научных статей VI Международной начно-технической конференции аспирантов и студентов в г. Донецке 24-27 апреля 2006р. – Донецьк: ДонНТУ, 2006.
Погрузка угля в железнодорожные вагоны является завершающим звеном в технологической схеме угольного комплекса поверхности шахт. Различают два вида технологии погрузки:
- с предварительным накоплением добытого угля и последующей периодической погрузкой его в вагоны (погрузка из бункеров и со склада);
- поточная с непрерывной погрузкой угля непосредственно в вагоны без предварительного аккумулирования в емкостях (безбункерная погрузка).
При бункерной и безбункерной погрузках контроль загрузки вагона может осуществляться по объему или весу.
Следует отметить, что количество отгружаемого угля является одним из основных показателей деятельности угольного предприятия, поэтому задача точного учёта отгружаемого угля имеет первостепенное значение. [1]
На рисунке 1 показана технологическая схема автоматизированного углепогрузочного комплекса с применением электронных вагонных весов.
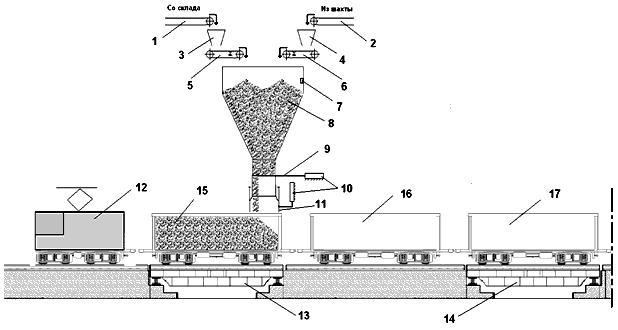
Рисунок 1 - Технологическая схема автоматизированного углепогрузочного комплекса с применением электронных вагонных весов и весов конвейерных.
где: 1,2 - конвейерные системы; 3,4 - направляющий бункер; 5,6 - конвейерные весы; 7 - датчик уровня; 8 - накопительный бункер; 9 - затвор накопительного бункера; 10 - гидроприводы; 11 - выдвижной телескопический желоб; 12 - электротягач; 13,14 - электронные весы; 15,16,17 - железнодорожные вагоны.
Структурная схема имеет следующий вид, показанный на рисунке 2.
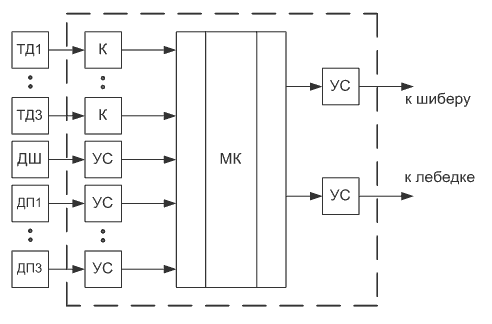
Рисунок 2 - Структурная схема устройства автоматической загрузки железнодорожных вагонов
где: ТД - тензодатчик, 3 пары датчиков, соединенных попарно;
ДШ - датчик положения шибера;
ДП - датчик положения вагона на весах, 3 шт.;
УС - устройство согласования;
К - компаратор, 3 шт.;
МК - микроконтроллер.
Функциональная схема устройства имеет следующий вид, показанный на рисунке 3.
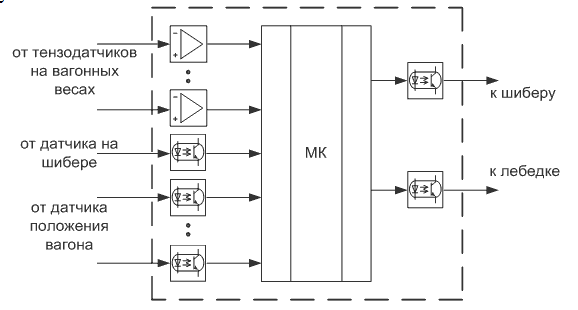
Имея структурную и функциональную схемы устройства, составим алгоритм его работы : после формирования микроконтроллера (МК) команды на включение лебедки (вагон приходит в движение и начинает заезжать на весы) происходит ожидание срабатывания первого датчика положения. Его срабатывание означает, что вагон на треть заехал на весы и можно начинать его загрузку. После этого формируется команда на открытие шибера, начинает засыпаться уголь в вагон. Срабатывание датчика положения шибера означает, что он достиг крайнего положения, тогда МК дает команду на остановку движения шибера. Происходит ожидание заполнения этой части вагона, о котором сообщит сигнал с первой пары тензодатчиков, после чего опять включится лебедка и вагон сместится на одну треть по направлению движения. Дальнейшие действия выполняются в аналогичной последовательности. Такое плавное управление загрузкой вагона позволяет эффективнее заполнить его углем. Об окончании загрузки будет свидетельствовать положительный сигнал со всех трех пар тензодатчиков, что будет означать, что вагон загружен полностью. При этом МК дает команду на закрытие шибера, проверяя этот процесс датчиком положения шибера (аналогично, как и при его открытии). После полного закрытия шибера (прекращен доступ угля в железнодорожный вагон), лебедка опять приходит в движение, вагон съезжает с весов, освобождая место следующему, загрузка которого происходит аналогично. Таким образом, загрузка железнодорожных вагонов происходит непрерывно и эффективно.
Ускорение процесса погрузки достигается тем, что взвешивание тары и брутто двух разных вагонов в одном составе происходит одновременно и автоматически, так как комплекс включает в себя двое вагонных весов в статике. Точность достигается тем, что во первых, вес тары железнодорожных вагонов берётся не по документам, а автоматически с вагонных весов, что позволяет отдозировать точно заданную массу угля. А во вторых, весы, применяемые для взвешивания отгружаемого угля являются статическими и имеют гораздо большую точность по сравнению с конвейерными весами или весами вагонными в движении.
А при помощи конвейерных весов имеется возможность проконтролировать остаток угля на складе, знать сколько отгрузилось угля прямо из шахты и сколько угля находится в накопительном бункере. Это достаточно важная информация для учёта движения угля в технологическом процессе на шахте.
Принцип работы данного автоматизированного углепогрузочного комплекса с применением статических электронных вагонных весов (с тензометрическими датчиками и весоконтроллером с дозирующими функциями) и весов конвейерных заключается в том, что появляется возможность свести к минимуму человеческое влияние на погрузочные работы, ускорить процесс погрузки, увеличить точность показаний веса отгружаемого угля и облегчить его подсчёт на складе и в составе.
Перечень ссылок:
1. Левин М. А., Ленский И. А., Весо-дозировочные системы для отгрузки угля потребителям-М.: Недра,1984, 192стр.