УДК 669.02/02
К обоснованию параметров системы привода подачи и загрузки в конвертер сыпучих материалов
Мустаев Н. Н., Моргунов В. М. (кафедра ЭМС, ДонНТУ, г. Донецк)
Аннотация. В статье приведены рекомендации по улучшению эффективности работы предприятия с учетом реально существующих задач развития отрасли и отдельных предприятий, а также предложен вариант модернизации привода затворов подачи и загрузки в конвертер сыпучих материалов.
Ключевые слова:шиберный затвор, пневматический привод, система приводов, конвертер, пневмолиния
Введение
Техническое перевооружение металлургии в ближайшие годы будет осуществляться в условиях стабилизации, а в дальнейшем и снижении объемов производства основных видов металлопродукции и определяться главной задачей – удовлетворения потребности народного хозяйства в черных металлах требуемого качества и сортамента при значительном повышении эффективности производства и использования металла в потребляющих отраслях.
К числу важнейших стратегических задач, стоящих перед черной металлургией можно отнести:
–снижение металлоемкости производства примерно в 2 раза;
–повышение производительности труда в отрасли вдвое;
–коренное обновление основных производственных фондов и повышение экономической эффективности работы отрасли в условиях рыночной экономики и самофинансирования;
–комплексное решение вопросов социального развития, охраны окружающей среды, рационального использования природных ресурсов и отходов производства.
Указанные задачи должны решаться в процессе технического перевооружения, реконструкции и обновления каждого металлургического предприятия и, в частности, каждого конкретного цеха.
При этом в подавляющем большинстве случаев не стоит задача наращивания объемов производства продукции на отдельных предприятиях, хотя мощность и производительность реконструируемых и новых агрегатов и даже цехов могут увеличиваться. В каждом конкретном случае главными задачами являются повышение качества и расширение сортамента металлопродукции, улучшение условий и рост производительности труда, решение проблем охраны окружающей среды и повышения эффективности производства.
В связи с этим особенно актуальными становятся выбор и экономическое обоснование вариантов реконструкции объектов металлургического производства в частности конвертерного цеха.
Важнейшими мероприятиями по повышению эффективности системы подачи и загрузки сыпучих материалов являются:
–повышение доли производства готовой продукции, получаемой в один передел из непрерывно литой заготовки, с соответствующим снижением удельного расхода металла и энергии;
–применение автоматического неразрушающего контроля исходной заготовки с последующей зачисткой заготовок и автоматическим контролем поверхности готовой продукции;
–внедрение средств автоматизации с применением программируемых контроллеров и промышленных ЭВМ.
Сыпучие материалы в конвертере подаются системой ленточных конвейеров и питателей, расположенных в изолированном участке конвертерного пролета. Для сохранения текущего запаса сыпучих материалов в районе каждого конвертера есть по четыре расходных бункера. Два бункера общей емкостью 200 м3 заполнены известью, бункер полезной емкостью 70 м3 заполнен железной рудой и бункер емкостью 32 м3 заполнен плавиковый шпат.
С конвейера, подающего сыпучие материалы в конвертерный прогон, сыпучие материалы сбрасывают на передвижной реверсивный конвейер, расположенный над бункерами и распределяет по ним материалы. Материалы из бункеров выдаются с помощью питателей [1].
В бункерах установлены питатели производительностью по 220 м3 / час, а под бункерами руды и плавикового шпата - питатели производительностью по 720 м3 / час. Питатели подают материалы на весы дозаторы 3–5 т. Кроме общих для всех конвейеров перегрузочных бункеров, в районе каждого конвейера установлено по два промежуточных бункера 4, содержащих запас ферросплавов на одну плавку. Материалы из бункеров подаются в ковш с помощью поворотной течки.
Модель кислородного конвертера приведена на рис. 1.
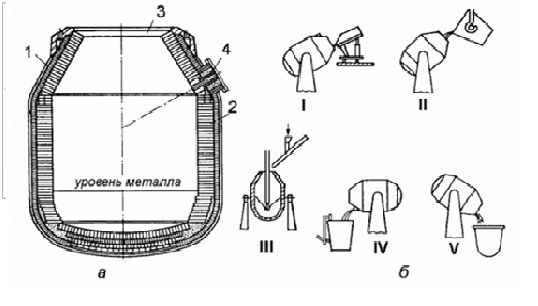
Рисунок 1 – Схема конвертера (а) основные периоды плавки (б): I – загрузка лома; II – заливка чугуна; III – загрузка шлакообразующих добавок и продувка кислородом; IV – слив стали; V – слив шлака; 1 – кожух; 2 – футеровка; 3 – горловина; 4 – боковое отверстие выпуска стали (летка)
Система загрузки материалов в конвертер (рис. 2) должна обеспечивать хранение оперативного запаса материалов:
– набор, дозирование и загрузку порций материалов в определенное время и в определенной последовательности без остановки продувки;
–возможность быстрого варьирования программы загрузки;
–автоматизацию всех выполняемых процессов;
–малое выделение пыли в атмосферу цеха и в газоотводящий тракт.
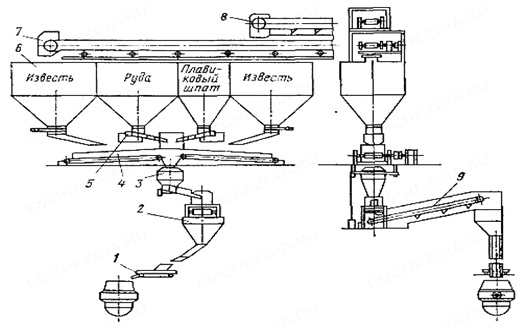
Рисунок 2 – Система загрузки сипучих материалов в цехе с 100–130 т конвертерами
Системы загрузки различаются устройством, числом и компоновкой отдельных элементов, бывают одно- и двусторонние, с индивидуальными и общими для двух конвертеров расходными бункерами, с промежуточными бункерами и без[2].
Технологическая схема конвертерного цеха представлена на рис. 3.
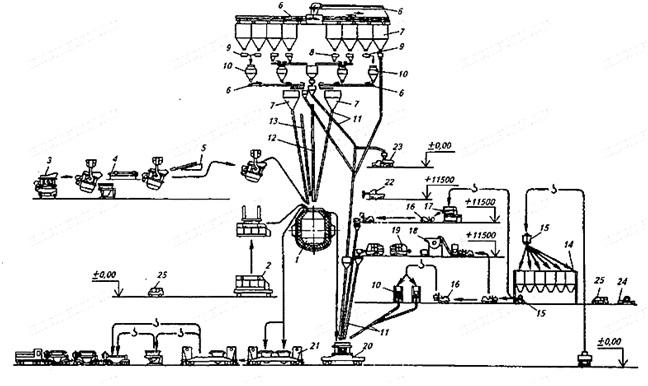
Рисунок 3 – Технологическая система работы конвертерного цеха: 1 – конвертер; 2 – совок с ломом; 3 – чугуновозный ковш; 4 – машина для скачивания шлака; 5 – устройство для измерения температуры чугуна; 6 – конвейер для подачи сыпучих материалов: 7 – бункер для сыпучих материалов; 8 – шибер с виброгохотом; 9 – шибер; 10 – весы; 11 – устройство для подачи сыпучих материалов в конвертер;12,13 – кислородная и измерительная фурмы; 14 – бункер для ферросплавов; 15 – контейнер для загрузки бункеров ферросплавами; 16 – погрузчик; 17 – печь для нагрева ферросплавов; 18 – электропечь для расплавления для расплавления алюминия; 19 – машина для транспортировки ферросплавов; 20 – сталевоз; 21 – шлаковоз; 22 – машина для отсечки шлака; 23 – цементовоз для известковой пыли; 24 – промышленный пылесос; 25 – уборочная машина
Большинство промышленных предприятий стран СНГ работают на морально устаревшем оборудовании произведенном 10 и более лет назад. Основными недостатками являются низкая ремонтопригодность в связи с отсутствием запчастей, относительно малый уровень производительности и самого качества выпускаемой продукции, простои из-за выхода из строя каких либо отдельных узлов оборудования, большие количество времени на поиск неисправности.
Для решения этой проблемы лучшим способом является установка более современного оборудования взамен устаревшего. Именно поэтому, взяв в пример систему подачи и загрузки в конвертер сыпучих материалов металлургического завода можно заменить устаревшие узлыконвертерного цеха, а именно питатели которые установлены после бункеров с известью, плавиковым шпатом и рудой.
Питатели представляют собой механические устройства, которые обеспечивают стабильность регулируемого грузопотока из бункера на конвейеры. В настоящее время они работают с электроприводом, двигатели которого работают в запыленной среде, слой пыли может достигать до 3 см. Следствием этого возникает локальный перегрев лобовых частей обмоток и преждевременный выход из строя электродвигателя. Именно это снижает надежность и показатели качества работы всей системы подачи и загрузки сыпучих материалов в конвертер и, как результат качество стали на выходе из конвертера.
Поэтому предполагается заменить существующие затворы с электроприводом которые стоят на выходе с бункеров, на шиберные затворы с пневматическими приводами, их можно подключить к общей пневмолинииконвертерного цеха, в которой давление 6 бар достаточное для питания пневмопривода. При этом необходимо будет исследовать процессы истечения сыпучих материалов из бункеров, определить характер воздействия слоя материала на затвор и обосновать параметры системы привода затворов с учетом автоматизации процесса дозирования
Предполагается управление шиберами по следующей пневматической схеме привода (рис.4) [3]. В автоматизированной системе управления будут использованы электропневматические элементы и контроллер [4].
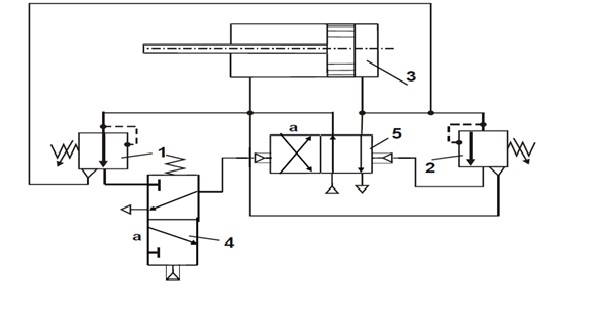
Рисунок 4 – Схема управления пневмоприводом затвора с контролем по давлению в рабочей полости пневмоцилиндра: 1,2 – клапаны последовательности; 3 – пневмоцилиндр; 4 – пневмотумблер; 5 – главный пневмораспределитель.
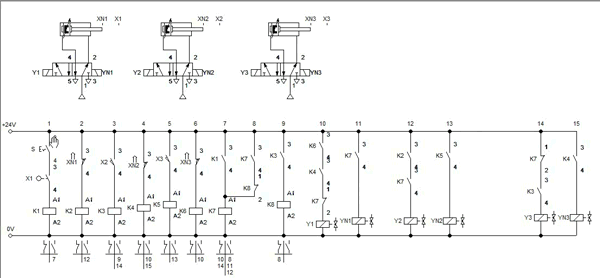
Рисунок 5 – Демострация работы пневмоэлектричесой схемы для дозирования сыпучих материалов
(анимация: 5 повторов, 19 кадров, 199 килобайт);
Задача дальнейшей работы состоит в обосновании параметров системы автоматического управления приводами затворов подачи и загрузки в конвертер сыпучих материалов на базе электропневматических элементов приводаи свободно программируемого контроллера
Список литературы
- Целиков А. И. Машины и агрегаты металлургических заводов. В 3–х томах. Т2. Машины и агрегаты сталеплавильных цехов. Учебник для вузов / А.И. Целиков // &ndash М.; Металлургия 1988. – 432с.
- Михайловский В. Н. Основы проектирования металлургических заводов. Определение объёмно–планировочных решений, состава и количества основного технологического и подъёмно–транспортного оборудования сталеплавильных цехов: учеб.пособие./В. Н Михайловский// Спб.: Изд–во Политехн. ун–та, 2013.–215с.
- Лаптева Н. Е. Пневмопривод и средства автоматики 2009.
- Шахматов Е. В. Пневмопривод и средства аввтоматики: учеб. пособие – Самара: Издательство СГАУ, 2006 – 112с.