Использование новых технологий для повышения качества производства на станке с ЧПУ
Авторы: Rafal Golebski, Pitor Sikora, Adam Gnatowski
Источник: Компания Sciendo
Rafal Golebski, Pitor Sikora, Adam Gnatowski Использование новых технологий для повышения качества производства на станке с ЧПУ В статье представлен анализ модификации производственного процесса на станке с ЧПУ. Процесс был изменен за счет использования новой процедуры сверления глубоких отверстий.
Введение
- большая эффективность за счет более быстрой обработки, а также из-за более короткого времени основного, вспомогательного, подготовительного и чистового времени,
- равномерная точность и качество заготовок,
- снижение количества производственного брака,
- сокращенные производственные циклы,
- повышенная гибкость производства - серийное производство механической обработки выгодно, а детали, изготовленные на ЧПУ, идеально соответствуют требованиям заказчика.
- использование этой технологии более подвержено изменениям в рисовании благодаря простоте внесения корректировок в программу.
Общее содержание
В настоящее время числовое управление станков очень интенсивно развивается, в основном из-за потребности отрасли в постоянном снижении затрат, увеличивая производительность станков и постоянное развитие микромеханики, которое демонстрирует потребность в небольших элементах с очень узкими полями допусков, часто сделанных из труднообрабатываемых материалов (Golebski, 2017; Petru et al., 2017). Постоянное развитие систем управления и микрокомпьютеров для компенсации мельчайших ошибок и неточностей станка с помощью более точных карт ошибок станка помогает удовлетворить такие требования. Сами машины также подвергаются эволюции, в которой устанавливаются все более совершенные приводы и измерительные системы, которые предназначены для компенсации, например, температурной деформации каркаса машины (Boral et al, 2017). Одна из самых интересных тенденций в машиностроении - постепенное добавление возможности подготовки всей технологии вместе с выбором державок, считыванием смещения и указанием точных размеров инструмента, установленного на держателе инструмента, что позволяет только оператор должен прикрепить соответствующий инструмент, указанный в программном обеспечении, в выбранных местах и станке, измерив количество поправок, которые необходимо внести в программу (Sadilek, 2015). На данный момент большая часть производства металлических элементов отягощена допусками по форме или ошибками размеров порядка 0,1–0,05 мм, однако чаще проектировщик сталкивается с необходимостью уменьшения элементов, что также меняет допуски на размеры. как ошибки формы и положения (Djurovic, 2015). Допуски для мелких элементов часто на порядок меньше или от 0,02 мм до 0,01 мм. Такие изменения допусков требуют использования других более точных станков и более технологичных обрабатывающих инструментов, таких как специальные твердосплавные сверла, спеченные твердосплавные пластины или охлаждаемые центром метчиков. Здесь возникает проблема эффективности производства и сроков внедрения элемента в серийное производство (Borkowski, Ulewicz, 2009). Время внедрения состоит из микроинструментов, проверки их прочности, выбора подходящих рабочих ходов инструмента и определения параметров обработки, что позволит получить максимально возможную производительность с минимально возможной заменой инструмента во время производства полной производственной серии. . Процесс полной реализации детали для серийного производства может длиться от 2 недель до 2 лет (Borkowski, Ulewicz, 2014).
2. ХАРАКТЕРИСТИКИ ТЕХНОЛОГИИ ОБРАБОТКИ В СЕРИЙНОМ ПРОИЗВОДСТВЕ
В этой статье будет показана модификация процесса производства медного соединителя, где модификация потребовала процесса сверления из-за небольшого диаметра 1,4 мм и очень длинного отверстия длиной 8 мм, то есть около шести диаметров. Также был изменен процесс прокатки: диаметр 10 мм должен был достичь 2,9 мм, что дало глубину резания 3,55 мм. При этом необходимо было получить узкое поле допуска 0,02 и 0,02 соответственно. На рис. 1 представлен элемент с его размерами и допусками. Общий допуск для волочения вынуждает изготовить поверхность в пределах допуска Ra = 2. Процесс изготовления до сих пор заключался в сверлении отверстия 1,4 мм глубиной 2 мм (первые зеленые линии), затем выполнялась фаза изготовлен с зенковкой с углом при вершине 60 (синяя линия), после чего для обработки использовалось сверло O 1,4 мм, которое выполнялось до заданной глубины с шестью отводами, чтобы избавиться от стружки с зеленых линий. Отверстие после обработки находилось в пределах предполагаемого допуска поверхности, а шероховатость поверхности варьировалась в пределах 1,7> Ra <1,1.
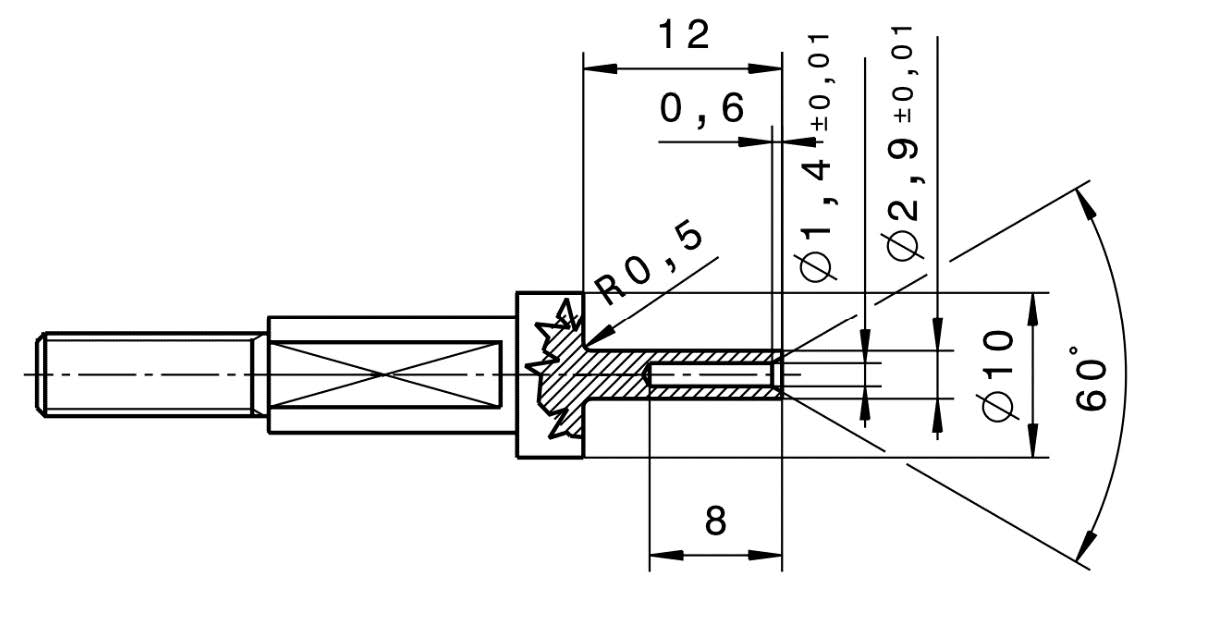
Рисунок – Деталь с допусками
Затем деталь прокатывалась от диаметра O 10 мм до диаметра 2,9 мм, эта процедура показана на рис. 3. Процесс проходил в трех проходах ножа типа DCMT. Глубина первых двух проходов резца была равной и составила ap = 1,5 мм, в то время как последний чистовой проход резца собрал ap = 0,55 мм, поэтому небольшой припуск был для уменьшения сил, действующих на инструмент, и улучшения шероховатость поверхности и поддержание хорошей округлости заданного диаметра.
Изготовление элемента с такой технологией заняло 104 секунды, из которых сверление заняло 8 секунд, тогда как обработка 2,9 мм длилась: первый проход 4,8 секунды, второй 5,3 секунды, третий проход 6,1 секунды, плюс время вылета станка между последующими. Обработка слоев 3 секунды, общее время поворота 19,2 секунды.
3. ИДЕЯ МОДИФИКАЦИИ ТЕХНОЛОГИИ
Такой процесс как сверление, так и точения неизменно в зависимости от параметров этой технологии давал вихревую стружку, которую нельзя было направить на рис. Стружка при окончательной токарной обработке имела очень маленькое поперечное сечение и была такой же, как и стружка при сверлении. Эти стружки требовали от оператора остановки станка для удаления стружки из держателя каждые 2 штуки. Удаление стружки длилось от 30 секунд до 42 секунд в зависимости от оператора, время обработки увеличивалось с 15 до 21 секунды. Вот почему деталь изделия, на которой основано изделие, так важна для выполнения всего процесса. Для нужд этого производства были выбраны 2 технологии и специальные инструменты, чтобы уменьшить количество остановок станка для удаления стружки и ускорить сам процесс массового производства.
При модификации технологического процесса, направленной на ограничение длины стружки и машинного времени единичного цикла, использовалась технология LFV и технология высокого давления смазочной жидкости под высоким давлением 140 бар, наносимой на режущую кромку. Технологии были изменены, чтобы обеспечить удовлетворительное время производства и чип, позволяющий работать в производственном цикле без необходимости останавливать станок для удаления стружки с инструментов, как в случае предыдущего производства.
4. ПРИМЕНЕНИЕ МОДИФИКАЦИЙ ПРОЦЕССА И ЕЕ ВЛИЯНИЕ НА КАЧЕСТВО И ЭФФЕКТИВНОСТЬ
Использование нового процесса стало возможным благодаря использованию твердосплавного сверла 1,4 мм из карбида вольфрама с охлаждением через сверло и фазы, выполненной на сверле (линия Брауна). Этот процесс состоял из одного входа сверла в материал рис.6 (Фиолетовая линия). Благодаря технологии LFV, которая основана на микро движениях по оси Z станка, были получены очень мелкие стружки , благодаря использованию охлаждающей жидкости с давлением 140 бар, удаление стружки из острия сверла вне элемента стало возможным. Кроме того, было обнаружено, что поверхность после такой обработки продольного отверстия сохраняет шероховатость поверхности Ra <0,8.
Следующей модифицированной операцией была токарная обработка с диаметра O 10 до диаметра ? 2,9 мм, из-за использования LFV оказалось, что лист, который использовался для обработки по старой технологии, теперь мог увеличить ap до 3,55 мм. Это позволило сделать только один ножевой переход (серая линия), чтобы он имел ту же форму, что и в старой технологии, за 3 прохода. Допуски на размер и поверхность не изменились по сравнению со старой обработкой. Стружка менялась диаметрально, из длинной или отслаивающейся удалось получить мелкую короткую стружку . Это полностью избавило от необходимости останавливать станок для удаления стружки из держателя.
Время, которое было достигнуто в процессе, значительно короче, время простоя станка имеет особое значение для очистки держателей инструмента. На прохождение скважины по новой технологии требуется 1,6 секунды вместо 8, время поворота уменьшилось с 19,2 секунды до 9,4 секунды. Общее сэкономленное время составляет 16 секунд плюс среднее время простоя машины из-за стружки 18 секунд. Общее время массового производства по сравнению со старым процессом сократилось на 34 секунды. Старое время производства составляло 105 секунд плюс 18 секунд простоя для удаления стружки, или 123 секунды, в то время как новое время производства составляет 89 секунд. В этом производстве доля затрат на производство в стоимости элемента составила 91%. После сокращения сроков производства эта доля составила 82%, при этом цена продукции снизилась на 21%. Время производства вместе с боковым запасом для 10 000 деталей этой детали составило бы 427 часов при старой технологии, в то время как для новой технологии можно было сократить это время до 309 часов, что дает 27% всего производства.
Выводы
Объектом проекта согласно предположениям, указанным в статье, было внедрение инновационной технологии, разработанной в рамках собственных экспериментальных и опытно-конструкторских работ. В рамках проекта было запланировано и реализовано приобретение инструмента, такого как: специальные твердосплавные сверла и режущие пластины DCMT, которые представляют собой интегрированную технологическую систему и полностью внедренную технологию. В технологическую систему входят следующие обрабатывающие устройства: токарный автомат BNA-42GTY с ЧПУ, оснащенный двумя шпинделями, основным с проходом 42 мм и шпинделем с вылетом 34 мм. Эти шпиндели позволяют обрабатывать детали длиной до 100 мм при скорости вращения шпинделя 6000 об / мин и на захватном шпинделе 5000 об / мин. Этот станок имеет агрегат высокого давления и технологии LFV, позволяющие выполнять технологические задачи в соответствии с инновационной технологией, восемь инструментов на поворотной головке, устройство подачи прутка и инструменты на планке у главного шпинделя.
Технологическая система позволила получить очень высокий уровень точности (отвечающий ожиданиям получателей в этой сфере) в предполагаемом допуске на размер в отношении: внутреннего диаметра отверстий, внешнего диаметра, шероховатости поверхности, геометрической связи с основанием детали. . Очень важным аргументом является тот факт, что процессы обработки были реализованы с учетом высоких параметров производительности, гарантирующих экономическую эффективность оказываемых услуг, в то же время с дополнительными предположениями, связанными с высокой энергоэффективностью, эргономикой машин и устройств, используемых в процесс. Указанная Компанией новая технология разработана для нужд комплексной обработки указанной серии изделий прецизионных деталей машин и устройств. Развитие обрабатывающей промышленности для прецизионных деталей машин с очень маленькими габаритными размерами очень динамично как с точки зрения модификации материала, способа производства, формы, так и с точки зрения эффективности обработки, что, следовательно, влечет за собой развитие в области технологии изготовления отдельных компонентов. . Важным аспектом изменений является как повышение показателей качества (точность изготовления, меньшее количество бракованной продукции), так и снижение производственных затрат.
Таким образом, в связи со значительными темпами изменений возникает необходимость в улучшении и повышении уровня технологической подготовки производителей, необходимость совершенствования процессов обработки, приводящих к более широкому применению решений в области автоматизации процессов, использованию более интегрированных технологические системы, выполняющие воспроизводимое производство в крупных масштабах, с повышением параметров качества в диапазоне точности. Принимая во внимание вышесказанное, следует четко указать, что допущения, упомянутые в статье, касающейся технологии и ее реализации, были выполнены в полной мере. Инновационная технология, реализованная компанией для многоосной токарной обработки внешних и внутренних поверхностей, с применением инновационной технологии, предполагающей использование охлаждения. Жидкая смазка с очень высоким рабочим давлением и системой LFV, характеризуется высокой технологической эффективностью, в частности, благодаря применяемым техническим решениям и автоматизации процессов.
Список использованной литературы
1.Boral, P., Antun, S., Kliajin., M, 2018. Machining of Spur Gears Using a Special Milling Cutter. Technical Gazette 25(3), 701-705, DOI: 10.17559/TV-20171120121636
2.Boral, P., Nieszporek, T., Golebski, R., 2017. The Welded CNC Machine Tool Frame. MATEC Web Conf. 157, DOI: 10.1051/matecconf/201815701003
3.Borkowski, S., Ulewicz, R., 2009. Instruments of Production Processes Improvement. PTM, Warszawa.